“The Greenfield factory by the name PIPL (Prathisthan Industries Pvt. Ltd.) which is being constructed is located in the Paithan MIDC, Dist. Aurangabad (Maharashtra)… With the support of Zume’s manufacturing technology, PIPL will pave the way for the future of the plant fiber-based products.”
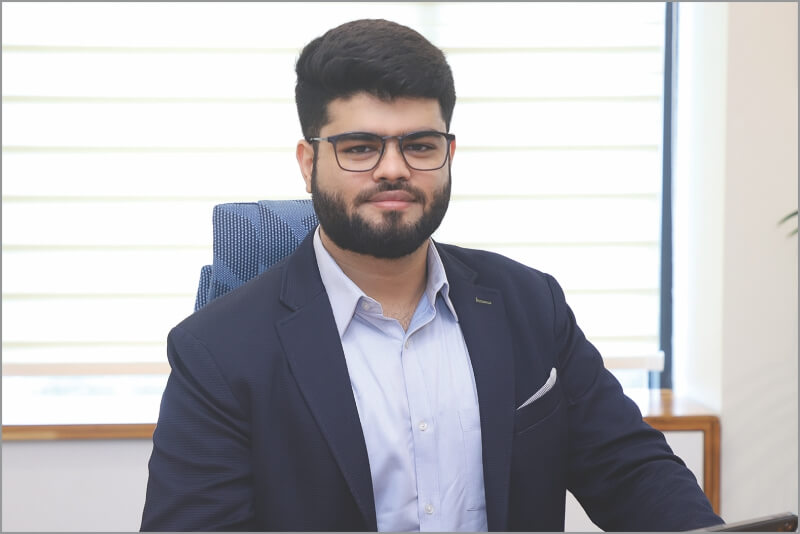
Mr. Madhure Desarda, Director of Operations, PIPL enlightens us on the recent partnership of PIPL which is a subsidiary of Parason Machinery with Zume Inc., the details on the Greenfield factory where the manufacturing technology will be used, and the USP of PIPL’s molded fiber product line, in an exclusive conversation with Paper Mart.
Paper Mart: PIPL has announced the company’s new manufacturing and professional-services partnership with Zume Inc. – please elaborate on this unique collaboration.
Madhure Desarda: As per the statistics cited in a feature report by the UN, by the year 2050, there may be more plastic in the ocean than fish by weight. To fight the battle against plastic pollution, we’ve been replacing single-use plastics with 100% compostable, and plant fiber-based products. PIPL’s partnership with Zume Inc. is a step towards reducing the use of single-use plastics from the day-to-day lives of people.
“Amid the pandemic, the food delivery business has grown rapidly and PIPL-Zume will be providing these businesses a compostable alternative that was not available earlier.”
PIPL and Zume share the same vision to save planet earth from the harmful effects of plastic. Furthermore, using Zume’s technology in the PIPL venture, we can produce patented anti-leak products that can be used in the food delivery sector in this time of the pandemic.
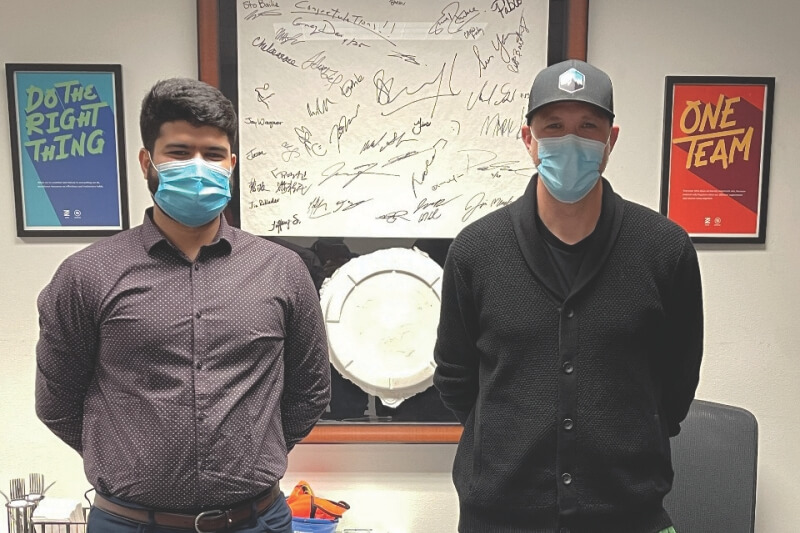
PM: PIPL is the Greenfield factory wherein Zume’s manufacturing technology will be deployed; tell us more about the factory – investment, total area, technical infrastructure, commercial startup, and future expansion plans etc.
MD: The Greenfield factory PIPL which is being constructed is located in the Paithan MIDC, Dist. Aurangabad (Maharashtra). In this factory, with the support of Zume’s manufacturing technology and Parason’s Pulping technology, PIPL will pave the way for the future of the molded fiber products. A huge amount of capital has been invested for this project, comprising a huge area with a plan of expanding more units in the same area. The factory will use the latest technical equipment in addition to having world-class infrastructure, and having pertinent global standard certifications.
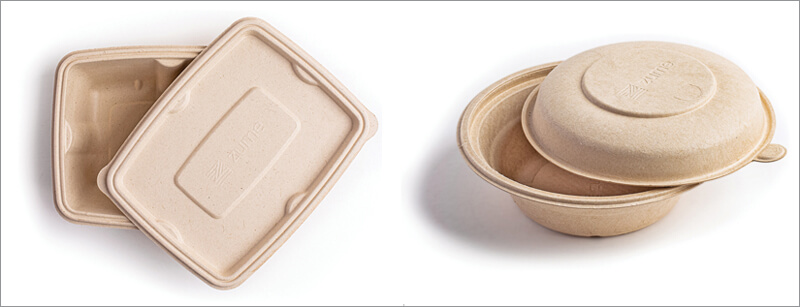
PM: Please elaborate on Parason’s technologies and equipment that would be delivered and complement Zume’s core molded fiber manufacturing technology for PIPL?
MD: Parason is a global leader in stock preparation systems. The technologies and equipment that will be delivered for the project will be an entire turnkey project. Being the best-in-class, the technology and the components of the equipment will be on a par with Zume’s core molded fiber technology and it will complement the latter quite smoothly. Parason is proud to assert that it is officially the wet-end partner of Zume Inc.
PM: The collaboration is said to put Parason in a network of Zume manufacturing partners to produce sustainable goods that replace plastics and Styrofoam — how do you see your business expanding in other regions/ markets with this partnership?
MD: The product is made of moldable fibers such as bagasse (sugarcane fiber), bamboo, wheat, straw, and blends of various grass fibers. The tableware manufactured is elegant, oil–proof and designed with superior strength, and won’t break or crack under moderate pressure. It is perfect for storing hot as well as cold food products. The product has Snap lids, is compostable and can be easily stacked. This is a market that is growing at a rapid pace and PIPL will focus on the expansion of the business in India and abroad. Partnering with Zume, PIPL looks forward to entering this business segment with a bang. Parason has a pre-established presence in India, Brazil and the USA and with the association with Zume, we look forward to setting up world-class molded fiber facilities starting with PIPL.
PM: Talking about molded fiber products — could you please brief us up about PIPL’s molded fiber product line market share, new developments or any technology upgradation? What are the USPs of PIPL’s molded fiber product line?
MD: PIPL is specialized in offering complete project engineering and solutions to produce biodegradable and compostable molded fiber-based products that are used in hospitals, corporate cafeterias, quick serving restaurants, universities, restaurants, schools, homes, etc. There have been continuous developments, research, and technology upgradation in this segment.
One of our USPs is that the molded fiber products that are manufactured using our equipment are the best eco-friendly solutions for an environmentally-conscious consumer. These products are manufactured under high-quality standards with the least greenhouse effects along with zero-waste production, using electric heating for hot presses. No thermo fluid heater, coal, or any other solid fuel is being used which implies that clean energy is being used and this is another of our USP.
The raw materials used are biodegradable and compostable, made from natural plant fibers such as sugarcane bagasse, wheat fiber, or bamboo fiber, all of which are renewable resources. Placing hot foods in plastic or Styrofoam containers generates a lot of cryogenic gases which further leads to life-threatening diseases such as cancer and other diseases. The products are also listed on Amazon and are performing great. Amid the pandemic, the food delivery business has grown rapidly and PIPL-Zume will be providing these businesses a compostable alternative that was not available earlier. The timing is just perfect.
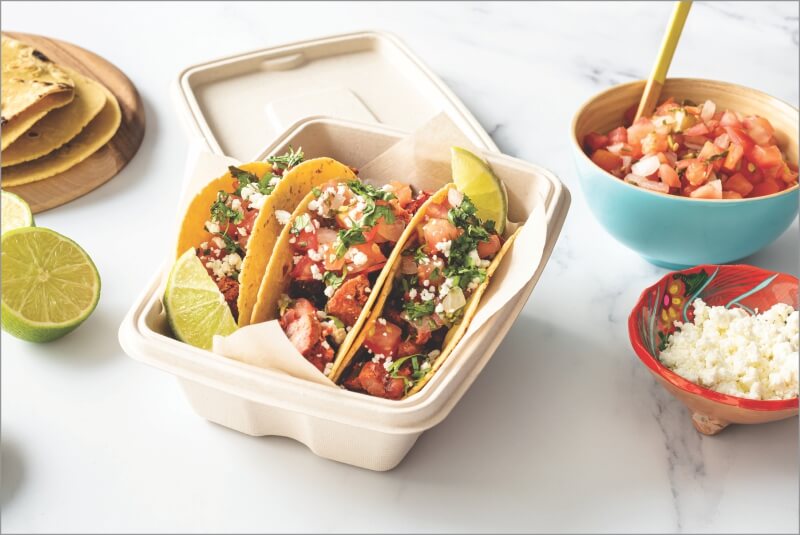