JMC Paper Tech is known for its energy-efficient machine design, advanced technology, and customization capabilities. With an emphasis on sustainability, energy efficiency, and the integration of modern technologies, such as IoT-enabled systems, the machinery is designed to deliver long-term value and operational efficiency, setting the company apart from traditional offerings in the market. In an exclusive interview with Paper Mart, Dr. Yesha Patel, CEO, JMC Paper Tech, discusses the company’s journey in the paper industry emphasizing its technological innovations and sustainable practices that position them as an energy-efficient and sustainable company in the country.
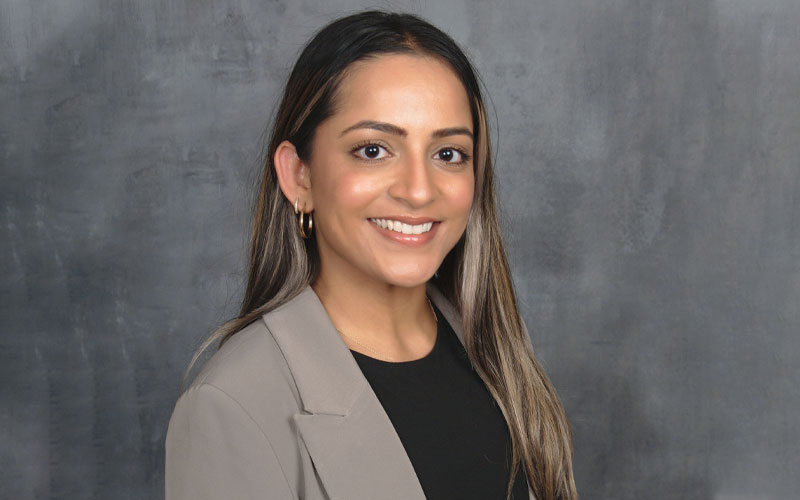
Paper Mart: Can you elaborate on your journey as a pulp and paper equipment manufacturer?
Yesha Patel: Our journey in the pulp and paper industry began in 1972 when my grandfather and his family founded the business, focusing initially on the local market. Over time, we gained a strong reputation for quality and craftsmanship, supplying machinery for paper production.
In 2002, my father, Mr. Rajni Patel, took over the business and expanded its reach by founding JMC Paper Tech. With the advanced technological solutions, we began competing with global manufacturers and exporters, establishing ourselves on the world stage. Today, as a third-generation business, we continue to build on our legacy, blending innovation with tradition to meet the industry’s evolving needs.
With presence in over 25 countries, more than 200 clients, and over 225 completed projects, JMC Paper Tech remains customer-focused. Our business philosophy centers on delivering value to clients through comprehensive system solutions.
PM: What are the key challenges you faced in the pulp and paper industry during the initial phase of your business?
YP: One of the key challenges we initially faced was competing with low-cost suppliers, as many customers opted for cheaper machinery that compromised quality for price. However, through persistent effort and by educating our clients on the long-term advantages of investing in durable, high-quality equipment, we successfully overcome this hurdle.
As the market matured, the demand for reliable and technologically advanced products increased, allowing us to earn the trust of key industry players. Today, we continue to focus on our quality, innovation, and customer service to meet our customers’ needs and maintain our position in the market.
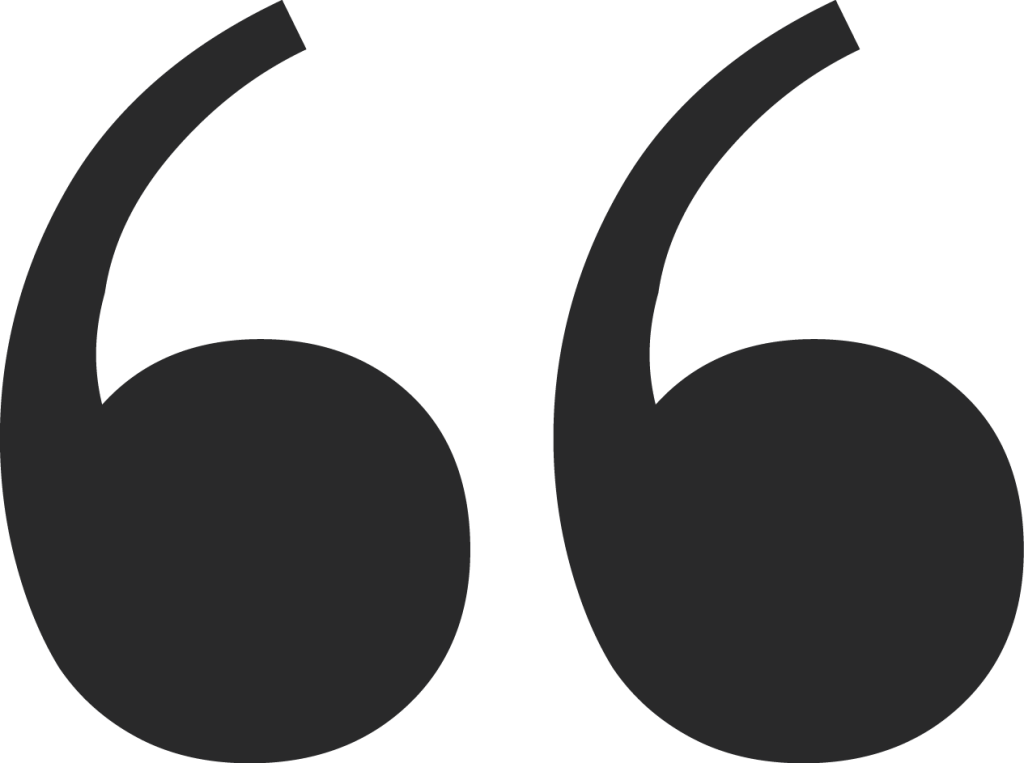
We are committed to advancing digitization by integrating Industry 4.0 technologies into our equipment. This includes IoT-enabled systems, predictive maintenance tools, and smart diagnostics to offer clients real-time monitoring and enhanced efficiency.
PM: What types of paper grades and pulp types can your machines process?
YP: We provide machinery designed to handle a diverse range of paper grades and pulp types. Our specialized equipment is capable of producing high-strength kraft paper, testliner, fluting medium, duplex board, writing and printing paper, and sack kraft paper. These grades serve various industries, including packaging, printing, and heavy-duty sacks. Some of the key machines include the kraft paper machine and duplex board machine for industrial paper production. For writing and printing paper, we offer a range of equipment such as the headbox section, forming section, pressing section, drying section, surface sizing, calendering, top dewatering former, and various accessories.
PM: What are the new innovations you have introduced at JMC Paper Tech?
YP: With a strong emphasis on sustainability, our machines are designed to process recycled pulp, bagasse pulp, and both softwood and hardwood pulps. This versatility enables our customers to incorporate eco-friendly alternative fibers alongside traditional wood and virgin pulps in their paper production.
Our technological advancements ensure that each grade and pulp type is processed efficiently, meeting both market demands and environmental standards, while maintaining high performance and precision.
Watch: In Pursuit of Lesser Water Footprint
PM: What are the key features that make your equipment unique compared to similar machinery available in the market?
YP: Our machinery is distinguished by its energy-efficient design, advanced technology, and customization capabilities. A standout feature of the machinery is the carbon steel drying cylinders, which provide superior energy efficiency, durability, and corrosion resistance compared to the traditional cast iron cylinders used by many competitors. These cylinders not only reduce operational costs but extend the lifespan of the equipment. With a strong focus on sustainability, energy efficiency, and integration of modern technology like IoT-enabled systems, our machinery provides long-term value and operational efficiency.
PM: What is the expected lifespan of your equipment, and what kind of maintenance and after-sale support do you provide to your customers?
YP: Our equipment has a lifespan of 20 to 30 years, depending on operating conditions and regulatory maintenance. Our machinery is built with high-quality materials, including carbon steel cylinders, precision-engineered components, and advanced technology integration. These features ensure extended durability, optimal performance, maximizing efficiency and longevity.
In addition, our after-sales support includes 24/7 technical assistance, on-site support, and remote diagnostics for early issue detection. We offer annual maintenance contracts (AMC) for routine inspections and preventive care, along with rapid spare parts supply to minimize downtime. To keep pace with the evolving technology, we provide upgrades and retrofitting services, ensuring that our clients’ machinery remains efficient and up-to-date over its operational lifespan.
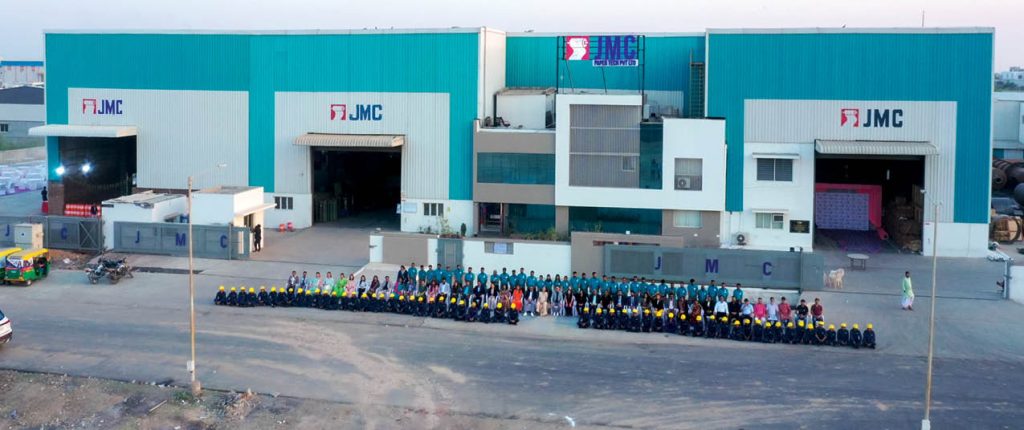
PM: What kind of training support do you offer for the operators and maintenance personnel?
YP: To ensure smooth operations, we offer customized training programs for both operators and maintenance teams.
The operator training covers machine operation, safety protocols, and troubleshooting. Operators have necessary knowledge to handle various paper grades and optimize machine settings for maximum efficiency while maintaining high safety standards. For maintenance personnel, we offer specialized training focused on preventive maintenance, component-specific care, troubleshooting mechanical and electrical issues. Our goal is to ensure that our team can handle routine maintenance and resolve their issues promptly to reduce downtime.
The key areas include managing critical components, spare parts management and maintaining the machine’s mechanical and electrical systems. In addition to it, we also provide remote support for troubleshooting.
PM: What are the lead times for production & delivery?
YP: Our standard lead time for production and delivery of machinery is 8-12 months, which accounts for design, manufacturing, testing, and logistical coordination. For customized machinery, lead times may extend to 12-14 months, depending on the complexity of the modifications.
PM: What is your annual production capacity?
YP: Our production facility in Sanand, Gujarat, spans 15,000 square meters, and have the capacity to manufacture 5-6 paper machines annually. Our facility is designed to scale up, allowing us to accommodate larger or more complex projects, ensuring we meet both domestic and international demand.
Also Read: Line O Matic: Paving the Way for Self-Reliance in Paper Machinery Innovation
PM: Can you share a case study or a client references from the pulp and paper industry?
YP: One notable case study is our work with Modern Laminates in Jinja, Uganda.This partnership commenced with a significant project: the installation of a 120-ton per day (TPD) kraft paper machine on an EPC (Engineering, Procurement, and Construction) basis. The project encompassed the design and delivery of a complete kraft paper production line, successfully navigating the environmental and logistical challenges unique to Uganda. The machine not only met but surpassed production goals and performance expectations. Building on this success, Modern Laminates extended its operations by commissioning a 15-ton tissue paper machine. This project required a compact yet efficient production line, tailored to produce high-quality tissue paper with energy-efficient components. The tissue machine not only diversified Modern Laminates’ product range but also maintained high profitability and quality standards.
Currently, we are working on a large-scale expansion for Modern Laminates, which includes a 200 TPD wood pulping line, a 100 TPD bagasse pulping line, and a 150 TPD virgin kraft paper machine to enhance the company’s production capacity and integrate eco-friendly practices.
PM: Discuss some of the major challenges you experience and how you overcome them?
YP: Managing client expectations and customization requests is a common hurdle. Another challenge is sourcing high-quality components impacted by global supply chain disruptions. To mitigate this, we maintain a diverse supplier network and keep a substantial inventory of critical parts, ensuring that our projects remain on schedule.
Additionally, staying abreast of technological advancements is essential. We invest significantly in R&D to incorporate the latest innovations into our machinery to provide cutting-edge solutions to our clients.
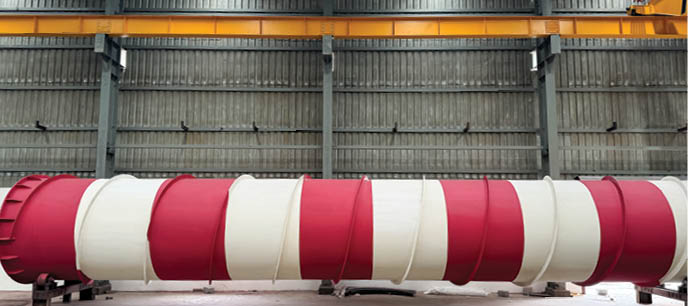
PM: How do you incorporate sustainability into your manufacturing processes?
YP: We focus on creating energy-efficient machinery, such as our carbon steel drying cylinders, which reduce energy consumption and operating costs. Additionally, use of energy-efficient motors and drives further minimizes electricity usage, contributing to a lower carbon footprint for our clients. Apart from that, our machinery is equipped with advanced water recycling and treatment systems that allow for multiple water reuse cycles within the paper mill, ensuring that the discharged wastewater complies with stringent environmental regulations.
In addition to it, we also promote the use of sustainable raw materials, such as bagasse, and agro-based pulping technologies that reduce reliance on virgin wood fibers and support a circular economy.
PM: What policy interventions would boost India’s pulp and paper equipment manufacturing?
YP: I envision India emerging as a global leader in pulp and paper equipment manufacturing. To accelerate this growth, several key policy interventions could play a crucial role.
Providing targeted R&D incentives such as tax breaks or grants can significantly boost innovation in energy efficiency and automation within the manufacturing sector. Public-private partnerships are crucial in pooling resources and making advanced technologies more accessible, especially for smaller manufacturers.
Additionally, establishing specialized industrial clusters, such as industrial parks or Special Economic Zones (SEZs) with subsidized land and tax benefits, can support smaller companies by providing shared facilities like advanced machining centers and training institutes, streamlining production processes.
To ensure a steady pipeline of skilled workers, the government could implement skill development programs and integrate relevant modules in technical institutes. Apart from that, financial support through low-interest loans or credit guarantee schemes would enable SMEs to scale up and invest in new technologies.
Lastly, encouraging sustainable manufacturing practices by introducing green certifications and energy efficiency labels would position Indian manufacturers as leaders in eco-friendly technology, aligning with global standards and customer expectations.
PM: What are your future plans? Where do you see yourself in five years?
YP: Our primary focus is on launching two innovative product lines: the elite pro series for paper machines and the fiber pro series for stock preparation. The elite pro series has advanced automation, IoT-enabled diagnostics, and energy-efficient design. These machines could enhance productivity while minimizing operational costs and environmental impact. Similarly, the fiber pro series will offer fiber processing capabilities, improving the quality and performance of paper production through advanced screening systems and high-efficiency refiners.
We are also introducing a new R&D lab dedicated to advancing screening and refining technologies, The lab will serve as a testing and simulation center for clients, enabling us to provide customized solutions that align with their specific production needs and keep pace with evolving industry trends. Looking ahead, our vision also involves significant global expansion, particularly into emerging markets in Asia, Africa, North and South America.
Additionally, we are committed to advancing digitization by integrating Industry 4.0 technologies into our equipment. This includes IoT-enabled systems, predictive maintenance tools, and smart diagnostics to offer clients real-time monitoring and enhanced efficiency.