ABB and Raumaster Paper will jointly explore integrated winder solutions in the US, helping paper mills enhance operational efficiency and extend the lifecycle of existing equipment.
May 2, 2025
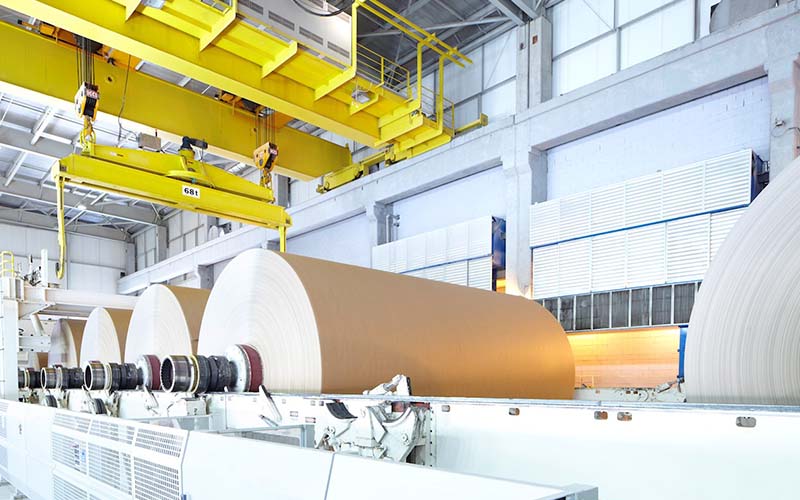
ABB has signed a Memorandum of Understanding (MoU) agreement with Raumaster Paper to jointly explore integrated winder solutions in the US, helping paper mills enhance operational efficiency and extend the lifecycle of existing equipment. ABB will bring its expertise in automation, system drives and digitalization to the partnership, combining its industry-leading control technologies with Raumaster Paper’s deep specialization in paper mill finishing equipment.
Watch: In Pursuit of Lesser Water Footprint
Many paper mills face increasing pressure to improve efficiency while working within tight investment constraints. Rather than requiring full system replacements, this partnership offers a practical path to modernization by enabling targeted upgrades to both control and mechanical systems. By aligning Raumaster Paper’s winder designs with ABB’s automation expertise, mills can benefit from reduced commissioning times, streamlined operation, and enhanced safety – delivering tangible improvements for operators managing aging assets.
Raumaster has been designing and manufacturing diverse machinery including paper mill finishing house equipment for over 40 years. In this time, it has delivered more than 110 high-capacity winder and rewinder machines globally. With a strong presence in Europe and Asia and a growing footprint in North America, the company has established itself as a trusted supplier, providing reliable and adaptable solutions that support performance improvements in the pulp and paper industry.
With more than 400 successful global installations, ABB’s drive control solutions for winders are well-established in the industry. This collaboration will enable access to an optimized winder control package that seamlessly integrates with ABB’s broader automation ecosystem, including ABB Ability™ System 800xA®, motors and drives. This end-to-end approach ensures smoother operation, easier maintenance, and better visibility in machine performance, helping operators manage their finishing processes more efficiently.