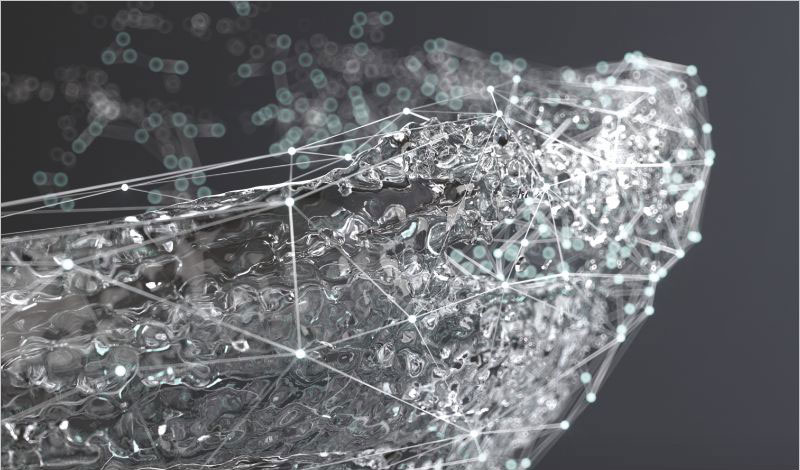
By: Göran Bäckman, Senior Manager, Global Business Development, Pulp & Paper, Kemira & Sari Krapu, Senior Research Scientist, R&D, Kemira
Amidst a global water crisis, the pulp and paper industry grapples with the challenge of securing sufficient water supply for its operations. Increasing limitations on freshwater use and the imperative need to conserve scarce water resources call for a critical examination of water management practices. This article discusses an innovative solution for the industry: effective recycling of effluent to raw water as a sustainable approach to minimize freshwater consumption.
Navigating the Water Crisis
The pulp and paper industry heavily relies on water, a vital resource, for its operations. With the rising concern over water scarcity and increasing limitations on freshwater use, the industry faces a critical challenge: how to overcome the shortage of available water sources without compromising production.
Water consumption in the manufacturing of pulp and paper has already decreased dramatically over the last decades. Today, the water systems in the mills are closed to a high degree, with a significant part of the process water being recycled. A modern Kraft mill can still consume around 20–80 cubic meters of freshwater for each ton of bleached pulp produced.
The reduction of water use and recycling of water have also considerably reduced the discharge of wastewater from pulp and paper production. Due to increasing environmental regulations and the imperative to conserve scarce water resources, the industry needs to focus on finding ways to further reduce and carefully manage its wastewater, to minimize environmental impact.
Watch: Top Paper Companies 2023
Challenges with Current Water Management
Freshwater for modern pulp and paper mills is typically sourced from nearby rivers and undergoes efficient coagulation treatment before being utilized in mill operations as process water. After use, the water used in the production process is discharged back into natural waterways. The industry faces a challenge in managing water quality during both the intake and discharge processes.
The quality of water taken in often varies; for example, over seasons, it may contain high loads of organic compounds. These dissolved compounds can cause issues with the runnability of the papermaking process, increasing the risk of deposits and adding operational costs. At the other end of the process, the discharged wastewater raises concerns due to its potentially higher level of contaminants compared to the originally drawn water.
Currently, biological treatment is the dominant method for treating effluent, successfully removing over 90% of the biological organic material from the wastewater. However, a persistent challenge remains; most of the detrimental hard COD, in addition to color and bacteria, are still present in the water after treatment. An additional treatment step with chemically aided coagulation and flocculation is effective in removing these impurities.
To meet tightening environmental regulations, mills are now exploring new tertiary treatment technologies for their wastewater treatment plants, aiming to complement biological treatment and address these resilient contaminants. However, investing in tertiary treatment can be a costly endeavor for the mills, as it requires the implementation and adoption of new processes and, for example, handling of resulting sludge.
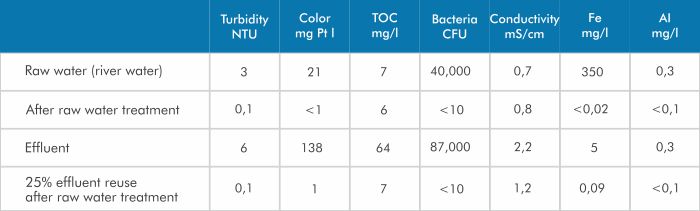
Innovative Solution: Transforming Effluent Into Raw Water
Kemira’s Water Quality and Quantity Management (WQQM) team is exploring an innovative concept for wastewater treatment. The idea is simple: recycling a portion of the effluent after the biological treatment back into the raw water treatment plant, thus replacing part of the incoming raw water. This method helps reduce both the dependency on freshwater sources and the amount of discharged effluent water, making it particularly well-suited for regions facing freshwater scarcity or stringent effluent discharge limits.
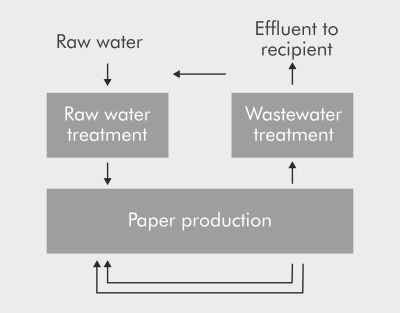
High Recycling Ratio
Our studies show that achieving a high recycling ratio is feasible. Laboratory tests on samples from various mills demonstrate that mixing a certain amount of effluent with the incoming raw water and treating them together through the existing coagulation treatment process does not significantly compromise the quality of the final process water, as shown on Figure 1. These tests indicate that incorporating 25% of biologically treated effluent into the raw water is possible. Depending on the process and the grade produced, it might even be feasible to replace up to 50% of the raw water with effluent.
Leveraging Existing Treatment Process
This straightforward strategy is outlined in the flowchart. Here, effluent from the outlet of the secondary sedimentation basin, post-biological treatment, is partly recycled back to the intake of the raw water treatment instead of being discharged into the receiving natural water bodies like rivers or lakes. The highly effective raw water treatment process already in place at mills includes coagulation, flocculation, and biocidal methods to remove most impurities through sedimentation and filtration.
After biological treatment, part of the effluent is recycled back to the intake of the raw water treatment instead of being discharged.
It is not uncommon that, due to changing process conditions, treatment chemicals are either underdosed or unnecessarily overdosed, leading to occasional poor water quality and, on the other hand, to chemical wastage and unnecessary costs.
By leveraging the existing treatment process, the suggested method of recycling effluent back into the raw water treatment process emerges as an effortless yet effective step toward more optimized and sustainable water management. The only investment required to enable effluent reuse is the installation of a pipe connecting the wastewater and the raw water treatment processes.
Benefits of Effluent-to-Raw Water Recycling
The innovative way to recycle and reuse effluent in the pulp and paper industry comes with multiple benefits. The method helps preserve water resources and aligns with the broader goal of sustainable industry practices.
Reduce Water Intake
By recycling effluent, mills can cut down on the need for fresh influent water, aligning with the efforts to reduce water use and reducing costs.
Reduce Effluent Discharge
This method lowers the volume of wastewater discharged into the natural water bodies, helping to mitigate the impact on nearby rivers and lakes.
Avoid Investing into New Tertiary Treatment
Utilizing the existing raw water treatment process with the efficient coagulation-flocculation process for removing residual organics, including hard COD, bacteria, color, and nutrients.
Generate Savings with Recovered Heat
This approach also presents an opportunity to utilize the warm effluent water to heat the colder incoming raw water, generating significant cost savings. Raw water treatment capacity can also be increased as the warmer water improves removal efficiency. In some cases, the increased volumes of secondary warm water and recovered heat can make it possible to provide extra effect for district heating to nearby cities.
Also Read: Xylem: Helping Solve Water Challenges with Innovation & Expertise
Leveraging Digital Tools for Optimized Water Management
In all water treatment processes, the fluctuating nature of water poses constant challenges. The key to enhanced operational control and performance in water treatment lies in the up-to-date visibility and transparency provided by real-time monitoring, control, and optimization. Kemira’s suite of digital solutions, KemConnect™ services, enables online monitoring of critical quality parameters across the mill’s processes, facilitating optimized water management for raw, process, and wastewater treatment alike. Real-time visibility also supports optimized dosing of treatment chemicals.
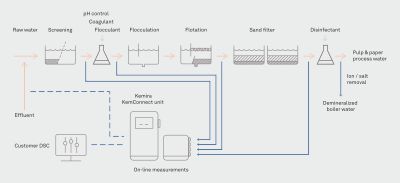
In the context of effluent recycling, these digital tools enable the continuous control of the effluent recycling process for optimal results. Kemira’s concept is based on real-time monitoring of all the necessary parameters, such as conductivity, turbidity, and color, to ensure stable, high-quality process water for the papermaking process. The raw water treatment chemical dosages, disinfection, and pH control are adjusted based on the real-time data.
Kemira’s online monitoring and control units can be integrated with the operator control system at the mill, improving and stabilizing the quality of incoming process water and providing more security and reliability for the process, as described in Figure 3.
By leveraging digital services, mills can achieve a more precise and responsive approach to water treatment, adapting in real time to changes in water quality and process demands.
Conclusion
Water scarcity highlights the pulp and paper industry’s urgent need to further reduce water consumption and wastewater discharge. The key is in recycling and reusing water. The effluent-to-raw-water recycling introduced in this article emerges as an innovative solution. By leveraging existing treatment processes and technologies and advanced digital tools, the approach helps address environmental concerns but also brings forth a range of operational and economic benefits for the mills.