Following an ANDRITZ rebuild in 2023, Huatai Paper’s mill in Dongying, Shandong Province, China, has the world’s largest mechanical pulping line for writing & printing paper production. The BCTMP line rebuild increased the 20 year-old line’s capacity from 100,000 TPA to 300,000 TPA, while at the same time reduced the line’s energy consumption per ton of pulp by a substantial 20 percent.
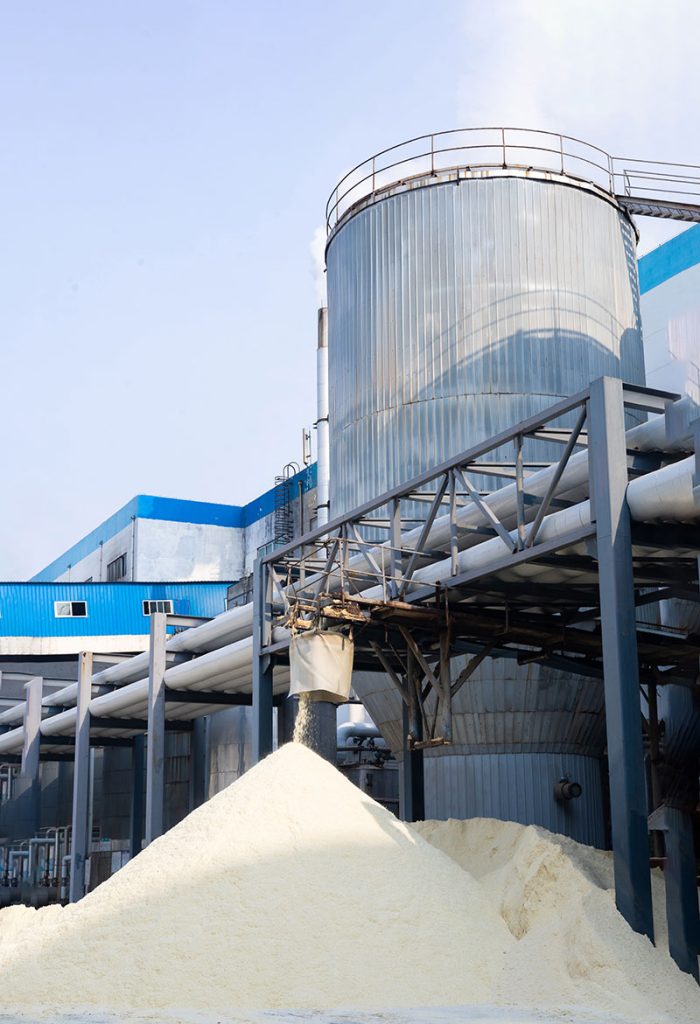
ANDRITZ worked in partnership with Shandong Huatai to achieve several goals through a number of unique solutions on this landmark project. The BCTMP line rebuild increased the 20 year-old line’s capacity from 100,000 TPA to 300,000 TPA while at the same time reducing the line’s energy consumption per ton of pulp by a substantial 20 percent. Pulp yield and quality also increased significantly, with shive content down from 0.3% before the upgrading to below 0.03%, with the lowest recorded being 0.01%, and brightness up from around 73% to more than 78%. Freeness, bulk and tensile index have all been beyond expectations.
The rebuild is part of Huatai Group’s 14-year plan to develop ecological forestry alongside profitable, environmentally friendly pulp- and papermaking. This includes raising pulp production by one million tons per year within a new pulp and paper industrial park, to which the Shandong Huatai rebuild is a strong contributor. The rebuild project has been synchronized with the upgrade of the original newsprint line and supporting wastewater treatment plant.
“Since the startup of the rebuilt BCTMP line, the quality of the pulp has been quite outstanding, which has significantly reduced the proportion of imported chemi-mechanical pulp (CMP). This, in turn, has contributed strongly to reducing raw material costs and improving paper quality,” said Mr Li Jianqiang, General Manager, Dongying mill, Shandong Huatai Paper.
Watch: In Pursuit of Lesser Water Footprint
Understanding the Customer’s Needs
Vice Project Manager, Huatai Holding Limited, Mr Zheng Xingshan, adds: “The ANDRITZ on-site team understood our actual production needs very well, by having the newly configured systems and equipment installed and commissioned before the shutdown, and then concentrating on the renovating and updating of equipment and systems after the shutdown.”
Mr Zheng elaborates on the project execution itself: “During the scheduled shutdown for upgrading, initially planned to last for three months, the actual project duration was only 69 days, from the shutdown of the old line to the startup of the upgraded line, including the dismantling of old equipment, reconstruction of foundations, installation, and commissioning of new equipment. ANDRITZ’s on-site supervision and commissioning experts worked proactively alongside our Huatai staff day and night, showing full commitment to the project. All were united in a shared goal of ensuring safety and quality, and achieving production efficiency as soon as possible. The celebration of completion was loud!”
The scope of supply included the rebuild of two high-consistency (HC) refiners, plus screw presses, disc filters and screens, along with new equipment for other process stages.
Key new equipment and benefits comprise:
PrimeMSD Impressafiner
- Optimal removal of moisture – better subsequent absorption of chemicals
- Maximized impregnation for energy savings in the high-consistency grinding stage
- Removal of extractives
- Maceration, partial delamination and homogenization
- Shive reduction after refining
TwinFlo LC refiner
- High operational reliability due to simple and robust mechanical design
- Low maintenance costs
- Easy and quick replacement of refiner discs
PrimeScreen X
- Top-feed stock inlet to minimize wear on rotor and basket
PrimeRotor and foils for increased efficiency and lower power consumption
- Easier maintenance thanks to streamlined design
- Optimized screen basket height-to-diameter ratios
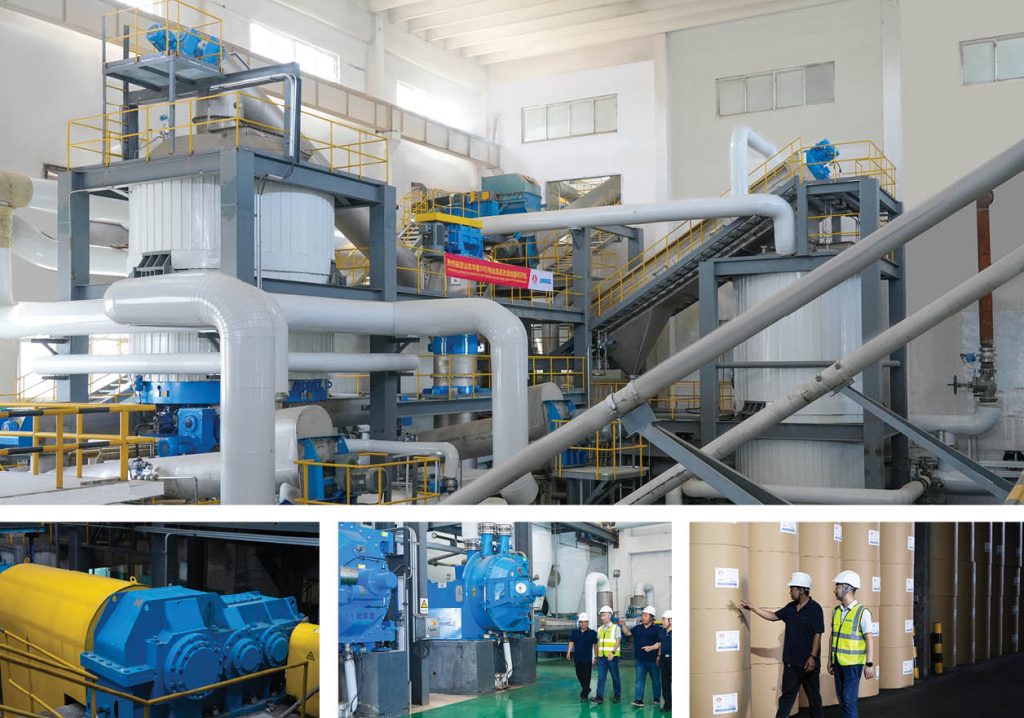
“One of the highlights of this entire line’s upgrading is the refurbishment of the existing HC refiner, which is at the heart of the line, and the upgrading of the control system for the HC refining system,” according to Mr. Wang Yuwei, ANDRITZ Paper Service Division Manager.
The latest QUANTUM refiner plates have ensured a more even distribution of pulp in the refining zone, improving the refining efficiency. QUANTUM refiner plates feature a patented graduated geometry that perfectly models the changes to the fiber as refining energy is applied – coarse at the inlet and fine at the periphery. This pattern results in stable and consistent refining without pinch points, lower energy consumption for a desired fiber strength, and reduced shives.
The renewal of the HC refiner control system Hydraulic Commander, ANDRITZ’s state-of-the-art control system, has also allowed the mill to have a more flexible and diversified selection of refining plates without limitations. The upgrade has reduced the need for special gap sensors, thereby lowering the cost of using refining plates. Moreover, the operation is simpler and more flexible, which minimizes downtime.
Also Read: Valmet: At the Heart of TNPL’s Hardwood Kraft Pulp Line
More than 60 Projects
ANDRITZ has the experience of more than 60 chemical/mechanical pulp projects, which has included previous collaborations with Huatai. “What impressed me deeply was the ANDRITZ team’s customer-first service and fearless and exploratory spirit. They put the customer first, maximize use of resources, and have saved us a significant amount of commissioning time,” says Mr Wei Lijun, General Manager, Huatai Holding Ltd..
So what is next for Shandong Huatai? Mr Wei hints at the future: “Under our integrated strategy of forest, pulp, and paper, I believe that there will be more and more opportunities for cooperation with ANDRTIZ. For instance, the 700,000-ton chemical pulp project we are currently promoting includes ANDRITZ technology. ANDRITZ’s continuous innovation in energy saving, consumption reduction and digital technology will undoubtedly create more opportunities for cooperation between us.”
Accumulated Expertise
A final word from ANDRITZ Project Manager Ji Haihong: “ANDRITZ is honored to contribute its globally accumulated expertise in CMP technology to this project. We have provided Huatai with the optimal upgrade solution, encompassing a state-of-the-art process from chip washing to final pulp production, including significant new equipment for profitable production.
“When they faced problems, Huatai always proceeded with the principle of ‘results first’ to drive the project forward. This spirit greatly inspired the ANDRITZ team members, who, as always, followed the principle of ‘customer first’, and by timely increases in personnel allocation, adding shifts for commissioning staff, working overtime, optimizing the commissioning process management, actively engaging in feedback and communication, and quickly resolving unexpected issues. We significantly shortened the project timeline and secured precious time for Huatai.”