Started in the year 1989 by Mr. Rakesh Kumar with a small capacity of 30 TPD to produce kraft paper, Bindal Group has notched up great heights with group production of over 1200 TPD. With the investment of over Rs. 300 crores Bindal Paper has ventured into a new orbit of high quality writing & printing paper with pretty decent technology. To get the sequence of their voyage, present project, technology, raw material along with their strengths & weakness team Paper Mart visited Bindal Papers Ltd.
The Voyage
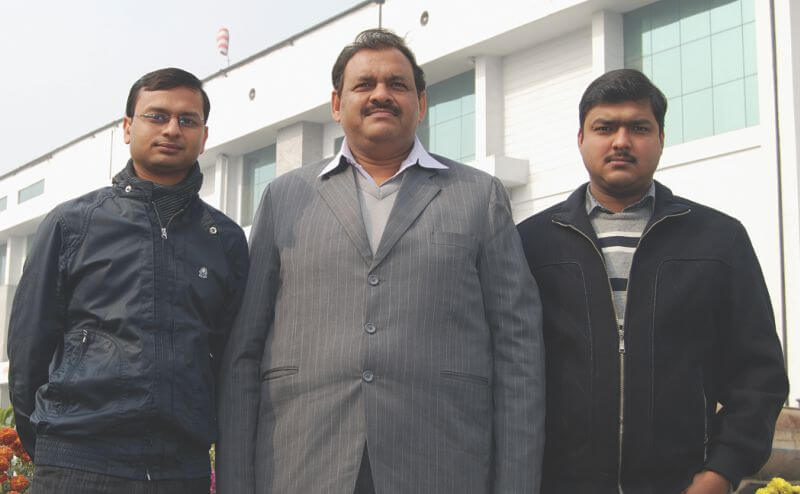
First paper came on reel in 1990 on the 30 TPD kraft paper machine setup in the name of Bindlas Duplex. The machine now produces 90 TPD Kraft paper
• 50 TPD duplex board machine was established in 1995, which now produces 130 TPD duplex board.
• In 1998 purchased Tehri Pulp & Paper Mill. Now same machine produces 125 TPD double layer kraft paper.
• Introduced 200 TPD triple wire kraft paper machine in 2007 which is now being targeted to produce 250 TPD.
• Took over Agarwal Duplex in 2001 and modernized existing 2 duplex board machines of 30 TPD & 45 TPD to produce coated duplex board. Today it produces 150 TPD altogether on both the machines.
• 25 TPD tissue machine was installed in 2007 to produce hard tissue and MGposter grades.
Bindal Paper: Outlook of the Project
Bindal group identified a significant investment opportunity in the high end printing and writing paper sector by setting up a modern greenfield plant in M u z a f f a r n a g a r , U . P . w i t h a manufacturing capacity of 300 TPD. The project was conceptualized in the year 2007 with an initial capacity of 200 TPD, which was later increased and the production came on stream in 2009.
The 5 meter wide paper machine with a production speed of 800 mpm is supplied by Servall – Walmsleys. The fourdrinier machine is capable of producing copier, surface sized and non surface sized maplitho grades in 57-100 gsm from a raw material mix of wood pulp (approx 15%) and bagasse or wheat straw. In the finishing section, rewinders are from Globe Radio, sheet cutter from Greatwall, Phillipines and recently a second-hand ECH Will copier line is being sourced. Critical components like head box, top formers fromPMPoland, calendering from Gapcon.
In the pulp mill section, continuous digesters are from Hindustan Dorr Oliver, washing & bleaching section from Wenrui – China, screens from AIMS and a wood pulp section with 6 vertical digesters out of which 3 are in use. For power requirement 15 MW turbine is installed from Triveni and 100 tons boiler is sourced from Cethar Vessels with 65 kg pressure and coal and pith (25 to 30%) as the input.
The Next Level: Strengths & Challenges
Raw Material
For Raw Material Mr. Rakesh Kumar said “Raw material is both a challenge and strength for us”. In a year, 6 months we use bagasse & 6 months wheat straw. Raw material is strength for us because it is available locally in the radius of 120 km. Whereas, importing waste paper is logistically expensive as we are located far from the port, thus waste paper based capacity was not a viable option.
In terms of challenge:
• The availability of raw material is short because there is good number of agro based mills in this region. The raw material is not available in excess and if a new mill comes up with big capacity it will create a real hue and cry situation.
• Sugar mills have also put up co-generation plants which has shortened the supply of bagasse.
• The prices of raw material have increased from Rs.1000/ton to 2200/ton in the period of 5 to 6 years.
• Out of the total consumption of bagasse & wheat straw in Muzaffarnagar based paper mills we consume40% of the total raw material.
On technology
On technology front Mr. Ankur Bindal elaborated “We have been able to achieve overall efficiency of 75-80% with the existing technology we are operating on. We are at par in water consumption but with the new technology coming in we may lack by 20 to 30% in terms of steam & power consumption. We are producing paper upto 90 brightness which is equivalent to A-grade paper mills and we have been able to replace them by offering good quality product at a lower price. But, there are some aspects we need to look upon i.e. we have to improve our packaging and finishing sections”.
Enlightening about the HR policies
Enlightening about the HR policies of Bindal, he said “It depends on the outlook towards manpower. We believe in retaining the people.Weresist on employing fresh engineers from the institutes as their work span is less than a year and they move ahead for more lucrative jobs. We had employed experienced people to ensure consistency in all the operations. For us every day is a new challenge, we face a serious challenge of manpower as people are demanding more. Most people prefer to work where the mills have colonies and people like to go there rather than come to us. To attract them we have to give more remuneration to them. So, if we also develop colonies it will be easy for us to attract people.
Mantra’s that worked for Bindal Papers
• There should be no compromises in technology; we should look upon the long term benefits of them in terms of efficiency, economic viability and value rather than present cost of it.
• We should differentiate between the process people & project people i.e. right people for the right job.
• Waste paper industry should be near the ports.
• Planned investment is very necessary as it is a capital intensive industry.