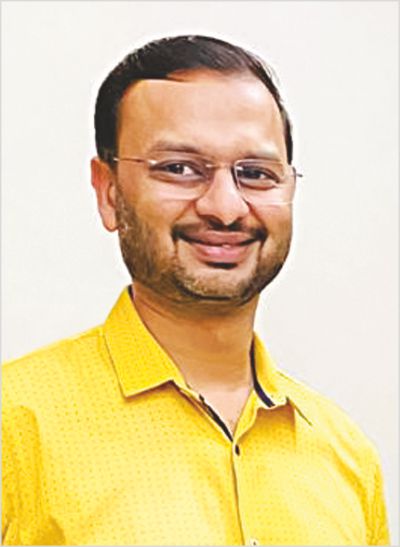
The water conservation journey in Bindals Papers Mills was initiated in 2015. It identified the areas where it could implement the above strategy. The company is working on 5-R Strategy i.e, Reduce, Reuse, Recover, Recycle and Recharge. Their water consumption was approximately 55 KL/T and reduced significantly and reached around 16.5 KL/T (2023-24), informs Mr. Ankur Bindal, its Managing Director.
Paper Mart: How do you ensure water efficiency in your operations?
Ankur Bindal: In Bindals Papers Mills Ltd, we are working on 5R strategy i.e. Reduce, Reuse, Recover, Recycle and Recharge. The water conservation journey in Bindals Papers Mills Ltd was initiated in 2015. It identified the areas where we could implement the above strategy. Different areas in all plants were identified i.e. pulp mill (wet washing, bleaching plant and pump sealing area); chemical recovery plant (pump sealing water and evaporator cleaning water); power house (MGF recharge water); and paper machine (complete recycling of machine white water) and started working one by one in each area.
PM: What is your aggregate annual water consumption? What much has that been reduced over the years?
AB: Our aggregate water consumption is 16 to 17 KL/T of finished product. We have a long journey from 2014 where our water consumption was approximately 55 KL/T and reduced significantly and reached around 16.5 KL/T (2023-24).
PM: What percentage of water consumed is recycled, and where is the discharged water reused?
AB: Approximately, 65 -70 % water is collected, treated, cleaned and recycled in different processes. Discharged water meets norms of regulatory authorities and is discharged in a common drain.
Watch: Top Paper Companies 2023
PM: What innovative solutions have you introduced in different areas of your mills that have made them more water efficient?
AB: We have adopted the innovative scheme i.e. “reduce water consumption at source” and it minimizes discharged effluent towards ETP.
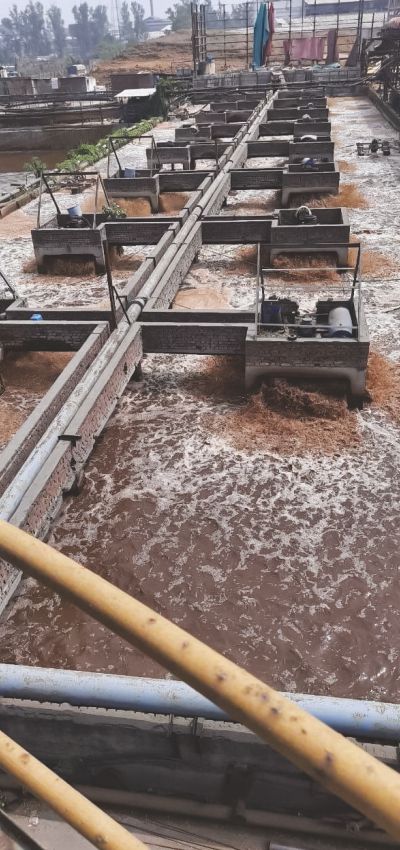
- Bindals Papers Mills started recycling Paper Machine back water after treatment in PDF (Poly disc filter) i.e. cloudy water into pulp washing of final bleached washer (D1 stage) and counter current washing at EOP & D0 washer.
- We are treating the remaining cloudy water in DAF followed by a micro filter and it is very clear water having TSS around 10-12 mg/l and is being used in the paper machine process (wire & felt LP showers).
- We are recycling wet washing effluent after neutralizing, sedimentation process back into raw material washing, and further we are installing anaerobic digester to recover bio-gas which will be used in Lime Kiln as a fuel.
- Our Chemical Recovery Plant and Power house are on ZLD through micro filters and entire wastewater is recycled within the process.
- Pump sealing water is also recovered in the vibro screen and recycled back into pump sealing.
- Further there is no discharge from the Paper machine to ETP. To make “zero liquid discharge”, we have installed Sedicell and tube settler in the paper machine process.
- Centricleaner rejects are treated at Hills screen followed by belt filter press and solid waste is sent to sister concern for board manufacturing and wastewater is treated at tube settler and finally sent to DAF.
- All rejects from plants are treated in Sedicell and accept water is sent to Cloudy water while solid part is sent to hill screen for treatment along with centricleaner reject.
- The entire wastewater is treated and recycled in Pulp Mill and Paper machine/Stock Preparation, and there is “zero liquid discharge” from paper machine to ETP.
So, Bindals Papers Mills have invested a huge amount to save water and now only the Bleach Plant discharged effluent is received in ETP for treatment as the above strategies ‘reduce at source’ is adopted and running successfully, and by which we are able to achieve such low water consumption.
Approximately, 65 -70 % water is collected, treated, cleaned and recycled in different processes. Discharged water meets norms of regulatory authorities and is discharged in a common drain.
PM: How seriously do you undertake water harvesting, and how much do you rely on it?
AB: Rain water harvesting is the main necessity of today and tomorrow as all. Many zones have been converted from safe to critical or most critical zones because of the decreasing trend of water level.
We are fully relying on this technology and have adopted 12 numbers of ponds in the nearby villages and recharged them with rainwater. The ponds have the capacity of recharging approximately 9,47,992.50 KL water per annum.
Also Read: Pakka Aims to Reduce Freshwater Consumption to 25 kl/MT in 2024-25
PM: What is your water usage reduction target? How do you plan to achieve it?
AB: We are the lowest water consuming industry and we have reduced water consumption approximately 70 % in the last 10-11 years, and further our target is to reduce it up to 12-15 KL/T of finished product. To achieve the target, we are planning to install additional secondary and tertiary treatment in ETP i.e. Extended Aeration, Activated Carbon filter and Micro filtration /Ultrafiltration/MBR/Membrane Filtration, etc.
PM: What are the challenges you often face in making your mills water efficient?
AB: Reducing water consumption and recycling treated water was a big task for us, and during this journey we had faced many challenges such as 1) increasing of process chemical consumption and 2) rise in back water temperature.
Through team efforts and R&D innovation, we addressed all the issues and now all process parameters as well as chemical consumption are within industry specification.