1.0 Introduction
Chemical Recovery Process is used to meet the following objectives in an integrated paper mill:
- To treat and dispose waste liquor generated from pulp mill, thereby reducing the environmental pollution.
- To recover the alkali used for pulping, thereby reducing fresh alkali consumption
- To burn the organic matter and beneficially use the thermal energy for the generation of high pressure steam.
The Fig. No.1 shows the Kraft Pulping and Recovery Cycle with unit processes and unit operations. The process can be explained in 4C i.e. Concentration, Combustion, Causticization and Calcination.
The purpose of this Paper is to explain the impacts of black liquor properties on various stages of chemical recovery operation, which will help to understand and to improve the performance of the Chemical Recovery Process.
2.0 Classification of Black Liquor Properties
The black liquor properties can be classified into FOUR groups:
(A) Chemical Properties:
- Total solids, total dissolved solids and total suspended solids
- Specific Gravity and Density
- Residual active alkali
- Inorganic and Organic compounds and its ratio
- Organically bound sodium
- Elemental analysis of black liquor solids;
-
- Process Elements: C, H, O, S and Na and
- Non Process Elements: Si, Ca, Al, Fe, Mg, K, Cl etc.
(B) Physico Chemical Properties:
(Influenced by chemical properties, important for black liquor Handling and Evaporation)
- Colloidal stability at higher concentration
- Viscosity and Rheological behavior at different solids concentration and temperature
- Foaming tendency; Foam coefficient and Foam index
- Boiling point elevation
- Surface tension
(C) Thermal properties
(Influenced by both chemical and physico chemical properties)
- Calorific value (HCVand NCV)
- Swelling volume ratio (SVR)
- Thermo gravimetric analysis (TGA)
- Integral procedural decomposition temperature (IPDT)
- Temperature of ignition (TIG)
- Specific heat
- Thermal conductivity
(D) Polymeric Properties
- Polymeric substances from lignin and carbohydrates and some Lignin carbohydrate complexes (LCC)
- Dialysis in cellulose membrane
- Molecular sieve chromatography (Gel filtration)
3.1 Black Liquor Composition, Residual Active Alkali and Process/Non Process Elements
Black Liquor Composition
Black liquor is a complex solution of organic and inorganic compounds and its concentration is influenced by chemical charged, pulp yield, digester operation and pulp washing parameters. Black liquor solids are divided into two parts:
(i) Inorganic compounds:
NaOH, Na2S, Na2CO3, Na2SO4, Na2SO3, NaCl etc.
(ii) Organic compounds:
- Lignin (large colloidal macromolecules containing many aromatic groups of related structures like catechols, quinines)
- Poly Saccharides (cellulose and hemi cellulose)
- Extractives (resin acids, fatty acids and neutrals)
TABLE NO.1: TYPICAL COMPARISION BETWEEN HARDWOOD AND NONWOOD BLACK LIQUORS
Particulars (% Dry solids) | Agro residues B/L | Eucalyptus B/L |
Organics | 68-72 | 65-68 |
Lignin | 28-32 | 40-42 |
Lignin Carbohydrate Complexes | 10-15 | 2-4 |
Hemicelluloses | 8-18 | 1-2 |
Organic Acids | 10-15 | 15-20 |
Inorganics as NaOH | 28-32 | 32-35 |
Salient features of black liquor composition are given as below:
- Higher alkali consumption indicates degree of degradation of carbohydrates, more proportion of organic acids and less RAA level.
- Higher Sodium Carbonate indicates less caustisizingefficiency.
- Higher Sodium Sulphate indicates less reduction efficiency and/or more make up chemicals.
- High organically bound sodium indicates more degradation of carbohydrates, more formation of organic acids.
- Ratio of Na/S is an index of TRS emission.
- Presence of sodium as resin soaps is an index of foaming tendency.
Effect of Residual Active Alkali:
- Stability of colloidal alkali lignin; at pH 9-10 lignin precipitates.
- Polymerisation of Saccharinic acids leads to increase black liquor viscosity.
- Sodium carbonate and Sodium sulphate precipitation; higher RAA lowers critical solids limit for sulphate and carbonate precipitation because of common ion effect as it will lower solubility of Sodium carbonate and Sodium sulphate.
- Higher Alkali increases swelling volume index (SVI) initially but very high alkali level suddenly drops SVI of BLS during combustion
Effect of Non Process Element:
Non-process elements are the elements other than those normally part of the pulping & recovery cycle. Table No.2 gives level of non process elements in different hardwoods.
TABLE NO.2: LEVEL OF NON PROCESS ELEMENTS IN DIFFERENT HARDWOODS
Name of NPE (%) | Casurina | Cashew | Poplar | Saubabool | Eucalyptus |
Silica | 0.06 | 0.03 | 0.03 | 0.02 | 0.08 |
Calcium | 0.1 | 0.2 | 0.02 | 0.2 | 0.07 |
Potassium | 0.11 | 0.26 | 0.2 | 0.25 | 0.27 |
Chlorides | 0.03 | 0.03 | 0.02 | 0.04 | 0.02 |
NPE build up in the recovery cycle is very rapid and can cause severe damage to process equipment by the way of plugging of the flue gas passage through massive deposit build up. The following Table No.3 gives the effect of various NPE on chemical recovery process:
TABLE No.3: EFFECT OF VARIOUS NPE ON CHEMICAL RECOVERY PROCESS
S.No. | Non Process Element | Impacts on chemical recovery process |
1. | Silica (Si) | -Scaling on evaporators, filters, wires, screens, furnace etc. -Higher smelt melting temperature,more problem of freezing near spout. -Poor white liquor quality. -Poor reburnt lime quality (over burnt lime). -Operational problems in lime mud reburning |
2. | Chlorine (Cl) | -Increasing scaling and corrosion rate. -Adversely effect ash fouling characteristics, lower sticky temperature on heat transfer surfaces |
3. | Calcium (Ca) | -Increases water soluble scales on evaporator tubes. -Poor white liquor quality. |
4. | Iron (Fe) | -Formation of corrosion and scaling products like Fe2O3, FeS and Fe SO4 on vapor side evaporator tubes. -Presence of Fe2O3 dust on economizer tubes accelerates SO3 formation, leading to NaHSO4 formation. |
5. | Aluminum (Al) | -Scale formation along with Na and Si increases on evaporator tubes |
6. | Phosphorous(P) | -Affects reburnt lime quality. – Operational problems of ringing formation in lime kiln. |
7. | Potassium (K) | -Poor white liquor quality. -Adversely effect ash fouling characteristics, lower sticky temperature on heat transfer surfaces |
3.2 Viscosity:
Viscosity is a very important property for black liquor handling (pressure drop), heat transfer and mixing operations. It is necessary to keep black liquor in colloidal stability and free flowing in concentration and combustion stages of Chemical recovery process. Black liquor viscosity depends on nature and amount of polymeric materials (lignin, extractives and hemicellulose) and amount of cooking alkali used. Strong black liquor is Non Newtonian in character and its viscosity is function of concentration, temperature and pH.
Fig.No.2 shows the effect of viscosity on evaporator capacity. An increase in viscosity by a factor of 10, can decrease evaporator capacity by 0.5 times. Similarly a decrease in viscosity by a factor of 10 can increase evaporator capacity by 1.5 to 2.0 times ( Viscosity changes -15%).
Fig.No.3 shows effect of liquor solid content and temperature on mean droplet size.
Mean droplet size decreases by about 20% as temperature increases 400C at constant %TS Viscosity changes -15%). Similarly mean droplet size increases by about 33% TS increases 60 to 70%TS (Viscosity changes +48%)
Fig No. 4 shows effect of residual effective alkali on changes on viscosity. Viscosity changes are significant at higher %TS.
Fig No.5 shows effect of heating of black liquor from HW Pulping.
Fig No.6 shows reduced viscosity as a function of reduced solids for black liquor.
3.3 Boiling Point Elevation (BPE):
BPE is an important property for Design and Performance of black liquor evaporators.
BPE increases with increase in concentration and increases sharply at above 50% TS.
BPE increases linearly with molar sum of Na+K in BLS. Pulping variables (Chemical charge, Pulp yield, Liquor causticity, Liquor sulfidity, Chloride content, Sulfate reduction) change BPE value. BPE adversely affects the performance of MEE at higher concentration.
BPE =Boiling temperature of B/L- Boiling temperature of water.
3.4 Fouling Tendencies:
Foaming causes difficulty in evaporation (due to entrainment) and pulp washing (restriction in spray wash liquor contact with pulp sheet on BSW).
Foaming leads to increase in corrosion and scale formation.
Foaming increases due to presence of organic acids, gums, polymeric compounds, resin acids etc.
Foaming is estimated as Foam index and foam coefficient.
Foam Index=Volume of B/L becoming foam X 100/ Volume of B/L Sample
Foam Coefficient= Volume of foam / Volume of B/L Sample
Various defoamers like Sulphonated castor oil, Turpentine, Kerosene, Cotton seed oil are used to control foam. Mechanical foam breakers, Thermal shocks or Impingement baffles are also used for defoaming of B/L.
3.5 Surface Tension (TS):
ST is important property in determining the droplet size at the time of atomization of black liquor for combustion (spray drying) and nucleate boiling. Viscosity and Surface tension influence spray size distribution and droplet combustion. ST decreases with increase in concentration and temperature of B/L. At fixed temperature, ST falls rapidly with increasing solid content (10 to 40% TS).Organic part of B/L influences strongly ST.
3.6 Calorific Value (CV):
Tall oil and turpentine are most important agents in lowering ST. It is significant for design and operation of recovery boiler and also required for its performance analysis. The calorific value is strongly influenced by black liquor composition (elemental analysis) and indicates amount of heat released during combustion in Bomb calorie meter. Organics contents contribute to calorific value while Inorganic contents act as diluents. Pulping parameters (AA, Yield) changeCVof BLS. The following Table No.4 gives heating values of different constituents of black liquor.
The following Table No.4 gives heating values of different constituents of black liquor.
Components | Heating Values ( MJ/kg) |
Softwood Lignin | 26.900 |
Hardwood Lignin | 25.110 |
Carbohydrates | 13.555 |
Resin, Fatty acids | 37.710 |
Sodium Sulphide | 12.900 |
Sodium Thiosulphate | 5.790 |
The following Table No.5 gives Calorific values of black liquor of different raw materials
Raw material | Calorific Value (k Cal / kg DS) | Organics % |
Rice Straw | 2600-2700 | 58-65 |
Wheat Straw | 2800-3000 | 54-58 |
Bagasse | 3200-3400 | 56-60 |
Bamboo | 3200-3340 | 52-62 |
Hardwood | 2800-3200 | 55-65 |
Pinewood | 3500-4100 | 53-65 |
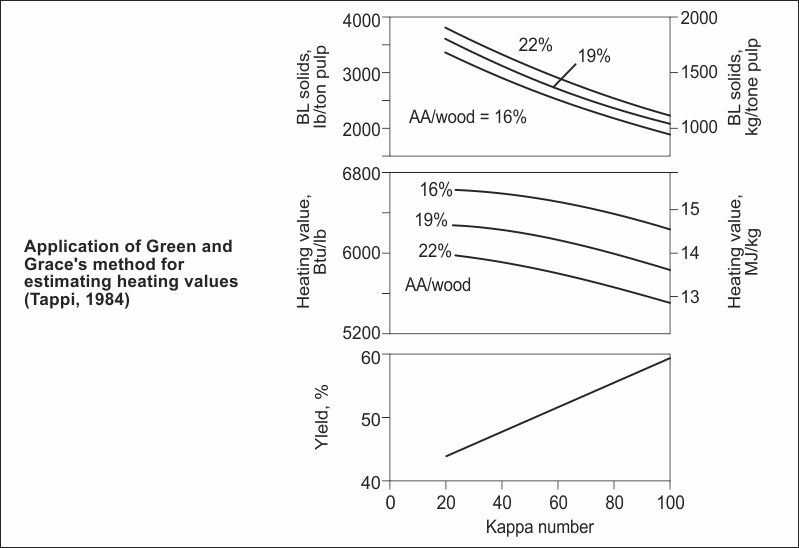
3.7 Swelling Volume Ratio (SVR):
SVR estimation is a semi qualitative method to assess the burning characteristics of black liquor solids. SVR dictates the height of Char bed in combustion zone.
SVR is defined as volume of black liquor solids when roasted at 300 deg. C for one hour as ml/gm. High SVR indicates a porous ignited bed with free air passage and complete incineration. Low SVR is due to higher inorganic load, soap content, black liquor aging and higher extractives.
4.0 Thermal Treatment of Black Liquor
This is based on theory of thermal depolymerisation of high molecular mass organic residues i.e. lignin polysaccharides as well as cleavage between lignin carbohydrate complexes which ultimately results in formation of lower molar mass components. During heat treatment of black liquor at 35% TS, black liquor is subjected to elevated temperature (more than pulping temperature) for specified time. There is significant reduction in black liquor viscosity, thereby increasing concentration and improvement of black liquor combustibility, thus improving thermal performance of recovery boiler.
Bagasse black liquor contains appreciable amount of dissolved Lignin-Ply Saccharide complexes. The presence of these high molar mass lignin carbohydrate complexes (LCC) is one of the main reason of abnormal high viscosity of black liquor and making it difficult to process in evaporator.
For retrofitting of heat treatment system, black liquor is withdrawn from evaporator system at 35-40 %TS and subjected to heat treatment process. Then again it is sent back to MEE system for further concentration.
The following Table 6 gives effect on Physico Chemical Properties of bagasse black liquor.
DP of isolated hemi celluloses is decreased from 125 to 85.
Table No. 6 (b) Effect on Viscosity:
Concentration % TS |
Without heat treatment, viscosity in mPaS at 90 0C | With Heat treatment, viscosity in mPaS at 90 0C |
55 | 250 | 60 |
58 | 400 | 85 |
60 | 600 | 100 |
62 | 880 | 135 |
64 | 1300 | 200 |
The following Table No.7 gives effect on Combustion Behavior of bagasse black liquor.
Table No.7 Effect on Combustion Behavior:
Particulars | Before heat treatment | After heat treatment |
Calorific Value Cal/g | 3420 | 3310 |
IPDT 0C | 454 | 414 |
TIG 0C | 763 | 730 |
Activation Energy kJ/mol | 113 | 58 |
SVR ml/g | 7 | 13 |
Based on performance analysis, the processing of thermally treated black liquor gives the following improvements in Recovery System:
(i) Increase in evaporation capacity: 12-15%
(ii) Increase in thermal efficiency: 12%
(iii) Additional steam production: 60 TPD for 100 TPD Pulp Mill Plant
(iv) Elimination of Direct Contact Evaporator
(v) Reduction in gaseous emission.
5.0 References:
1. | Macdonald R.G.,” Pulping of Wood,” Vol. I | 1969 |
2. | Gerald Hough, ”Chemical Recovery in Alkaline Pulping Processes | 1985 |
3. | TAPPI Kraft Recovery short note, TAPPI Press | 1996 |
4. | Terry N.Admns and Wm James Frederick, “Kraft Recovery Boiler “TAPPI Press, USA | 1997 |
5. | Johan Gullichsen and Carl-Johan Fogelholm,” Chemical Pulping, Book 6B”,Finnish Paper Engineers Association and TAPPI Press | 1999 |
6. | IIPTA Workshop on Chemical Recovery | 2001 |
7. | AGM and IPPTA seminar on” Developments in Pulping and Chemical Recovery” | 2005 |
* Assistant Professor (Chemical Recovery), DPT Indian Institute of Technology, Roorkee (IITR), Saharanpur Campus, Saharanpur (UP)-247001