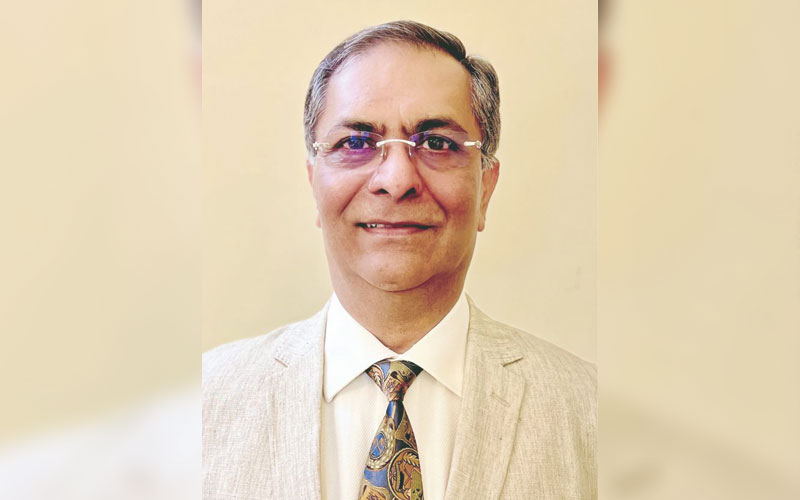
Emami Paper’s specific water consumption has decreased from 12.6 m3/ton in 2021-22 to 11.03 m3/ton in 2023-24 by implementation of various water conservation initiatives in the process. It claims that reclaimed water, comprising roughly 30% of our overall consumption, fulfills diverse roles including dust suppression, floor sanitation, horticulture, and ash conditioning. Further, around 50% of the treated effluent water is being utilized for agricultural irrigation purposes, its Director Operations Mr. Ashish Gupta informs Paper Mart.
Paper Mart: How do you ensure water efficiency in your operations?
Ashish Gupta: At Emami Paper Mills Ltd, we place paramount significance on water efficiency in our operations, employing a spectrum of strategic approaches to achieve this goal.
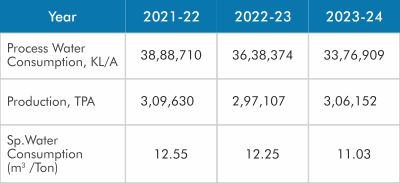
- Monitoring and Auditing: We monitor water consumption trends and conduct comprehensive audits regularly.
- Water-Efficient Technologies: Our unwavering commitment to water conservation is exemplified by our investment in cutting-edge technologies such as scan showers, MMF & Sand Filters, and the utilization of DAF filtrate in process.
- Reuse and Recycling: We implement rigorous systems for water reuse and recycling wherever viable by repurposing treated effluent for various applications and integrating closed-loop mechanisms into our industrial processes.
- Reducing Water Footprint: By embracing diverse water conservation projects and state-of-the-art technologies, we have markedly diminished our water footprint, thereby bolstering the sustainability of our operations.
- Benchmarking: We are steadfastly committed to maintaining reduced water consumption levels in accordance with national and international standards, showcasing our leadership in water efficiency and dedication to sustainability and operational excellence.
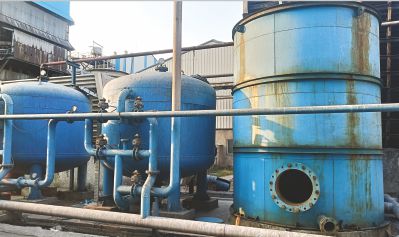
PM: What is your aggregate annual water consumption? What much has that been reduced over the years?
AG: The specific water consumption has decreased from 12.6 m3/ton in 2021-22 to 11.03 m3/ton in 2023-24 by implementation of various water conservation initiatives in the process.
PM: What innovative solutions have you introduced in different areas of your mills that have made them more water efficient?
AG: The following water conservation initiatives have led to a decrease of approximately 1500 m3/day in fresh water consumption.
- The implementation of Scan showers in the wire section of the Board Machine has led to a water saving of approximately 450 m3/day.
- Multimedia Filters (MMF) and Sand Filters have been installed in DIP#3 to reduce Suspended Solids (SS) in the Dissolved Air Flotation(DAF) filtrate. Achieved a reduction of approximately 400 m3/day in fresh water consumption.
- Installed Clariflocculator(CF2) for reduction of fresh water consumption in recycled grade boards. Achieved 200 m3/day water saving.
- Nozzle size was reduced from 1mm to 0.6mm for Press part HP Showers on all machines and achieved reduction of water consumption by 200 m3/day.
- Water from the re-winder and hydraulic heat exchanger of PM1 has been redirected back to the reservoir resulting in reduction of fresh water usage by 30 m3/day.
Watch: Top Paper Companies 2023
PM: How seriously do you undertake water harvesting, and how much do you rely on it?
AG: Water harvesting stands as a cornerstone of our sustainability efforts, and we approach it with the utmost seriousness. Recognizing its pivotal role within our water management framework, we prioritize it as a means to conserve and optimally utilize water resources. Unit has installed 20 Nos. of recharge wells, each featuring a gravel filtration system. These are strategically deployed to facilitate the replenishment of groundwater by using storm water, thereby maintaining the groundwater table. The annual recharge potential of these wells is calculated to be 26,03,874 m3, which is around 77% of our total water drawl.
PM: What percentage of water consumed is recycled, and where is the discharged water reused?
AG: Out of our daily fresh water intake of 9,600 m3, approximately 3,000 m3 of the final treated effluent water from the mill’s Effluent Treatment Plant (ETP) undergo tertiary treatment for internal reutilization. This reclaimed water, comprising roughly 30% of our overall consumption, fulfills diverse roles including dust suppression, floor sanitation, horticulture, and ash conditioning. Further, around 50% of the treated effluent water is being utilized for agricultural irrigation purposes.
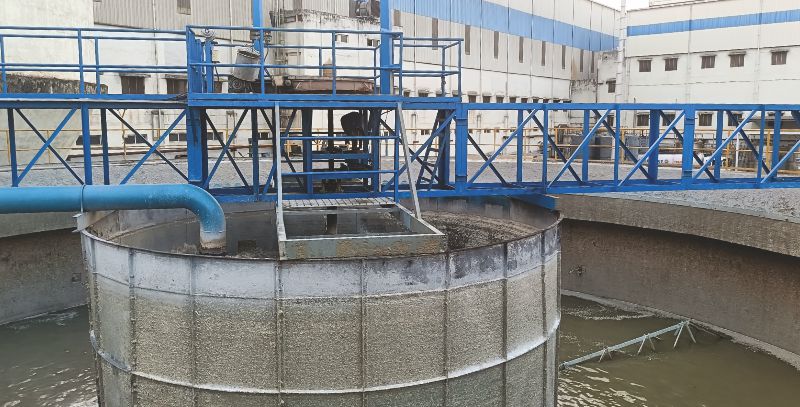
PM: What is your water usage reduction target? How do you plan to achieve it?
AG: Our water usage reduction target is 10% by 2025-26. To achieve this goal, we shall employ a multifaceted approach:
- Efficiency Measures: Implementing water-saving technologies and practices across our operations like closed loop water systems, Membrane technology, MPS technology, Filtration technology, etc. to minimize water consumption and optimize usage efficiency.
- Recycling and Reuse: Expanding our water recycling and reuse initiatives, such as treating and repurposing wastewater for non-potable/non-critical purposes within the facility.
- Process Optimization: Continuously assessing and refining our production processes to identify opportunities for water conservation without compromising on product quality or operational efficiency.
- Monitoring and Reporting: Establishing robust monitoring systems to track water consumption metrics, identify areas for improvement, and report progress towards our reduction targets.
Also Read: Kuantum Papers: Driven by Circular Economy
PM: What are the challenges you often face in making your mills water efficient?
AG: Due to the large volume of water required for manufacturing paper, the major challenge is the high initial investment and subsequent high operating costs of the water treatment systems. Newer manufacturing technologies therefore focus on reducing the consumption of water thereby reducing the investments in waste water treatment and also its operating costs. However, the constraints of handling large volumes remain with older paper machines, which are still in operation.
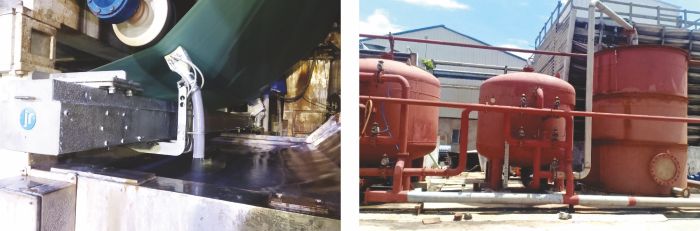
Installation of Scan Showers in Wire Part of Board Machine
Normally, high-pressure headers equipped with multiple spray nozzles are utilized for online wire cleaning – this is the usual configuration used in most paper mills, which uses excessive fresh water.
The above has been replaced by the installation of Scan showers on all wires of the Board machine. This system moves back and forth across the width of the wire at regular intervals, ensuring continuous cleaning in a cyclical manner and uses much less water. A reduction, in daily fresh water consumption by approximately 450 m3, has been achieved.
(DIP#3 / Paper Machine # 3)
Multimedia Filters (MMF) and Sand Filters have been installed in DIP#3 to reduce Suspended Solids (SS) in the Dissolved Air Flotation(DAF) filtrate. This filtered water is then utilized for wire showers in PM#3. Wire Part High-pressure showers utilize around 400 m3 of fresh water per day. By installation of above, total Suspended Solids (TSS) has reduced from 20 ppm to less than 5 ppm and achieved a reduction of approximately 400 m3/day in fresh water consumption.