The Indian integrated paper industry has long relied on European machinery manufacturers for high-quality equipment, with many small and medium-sized mills using redundant machines due to budget constraints. However, domestic manufacturers are now transforming this trend by reverse engineering existing technologies and expanding their capabilities. While this shift is promising, further investment in research and development is essential to elevate their standards and compete with global players.
By Ashish De
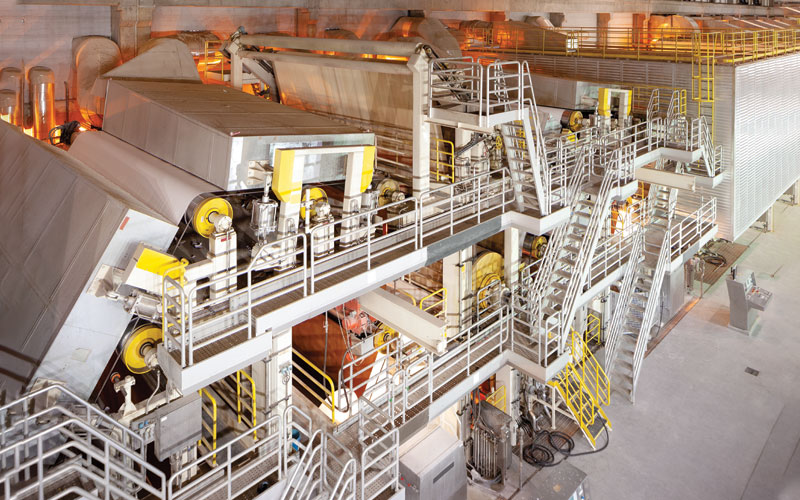
Machinery and equipment are the lifeblood of any industry, and the paper and pulp sector is no exception. Serving as the backbone of production, technological advancements and evolution in paper machinery are crucial for fostering growth and innovation. They ensure that the industry not only survives but thrives in a competitive landscape.
The growth of the Indian pulp and paper industry goes back to the years 1970-80, when Beloit of the USA, a leading global technology provider, joined hands with Indian manufacturing company Jessop & Co; major German technology solution company Voith GMBH collaborated with Indian construction company L&T to form a joint venture; and finally Finish Stalwart Valmet joined hands with Mechano of Kolkata with the aim to transform the sector. Unfortunately, none of the joint ventures sustained.
The beginning of the new millennium saw the Indian integrated paper industry depending on European machinery companies. It also saw small-and medium-sized paper mills using machinery and equipment from the redundant mills of Europe, the US, and Japan due to budget constraints. However, the ambition of domestic machine manufacturers and paper mills for high-quality components has prompted domestic manufacturers to begin reverse engineering, allowing for expansion beyond their core competencies into various areas of paper machinery.
As a result, many organizations have expanded their business volume, offering cost-effective solutions for budget-restrained entrepreneurs who want to enter the paper or board manufacturing segment. These organizations understood the large gap between the demand and supply of the basic commodity. Paper. Fuelled by the nation’s literacy campaign, the industry experienced a production-driven growth. But quality was relegated to the back seat. The emergence of a significant shift, concerning quality, accelerated the growth trajectory.
With liberalization and the opening of the economy, product quality became a key focus across all segments of the industry. While this was well underway, the rise of electronic media dampened the demand for paper in several segments, forcing the industry to adapt. A shift toward the consumer packaging segment, driven by its motto ‘Quality as a way of life’, ensured a significant growth. This growth fuelled a resurgence in the packaging paper and board sector, marking the revival for the industry.
With this move, many key players, including the small and medium segments, started accepting the need for quality everywhere. Many mills started investing in modern machinery. However, the homegrown machinery manufacturers mostly were into the reverse engineering process, as the ROI of these ventures did not motivate them to invest heavily in research and development. This resulted in high demand for chinese-made machinery due to their cost-effective solution, especially for the small and medium-size paper mills. The large domestic mills, however, continue to depend on the European vendors, mainly due to their cutting-edge technology, efficiency, and reliability which became a barrier for the homegrown manufacturers. The reality also underscores that the notion of self-reliance continues to elude the industry.
Watch: In Pursuit of Lesser Water Footprint
Limitations
Over time, many domestic pulp and paper equipment manufacturers have increased their involvement in the growth of the industry. However, their participation remains largely confined to paper and board machinery. One of the main reasons limiting the investment in integrated pulp and paper mills is inadequate forestry resources. As a result, many small to medium-sized paper and board machines rely on recycled fibers or market pulp. Large paper mills are still predominantly dependent on overseas machine manufacturers.
While domestic machinery producers have contributed significantly to increasing the production volumes, the final product often ranges from low to average quality. Many usually offer a low-cost solution that attracts new investors and entrepreneurs looking for a quick return or short-term gain. But, apparently, these start-ups might not be able to sustain in the long run. They have struggled to reach the designed capacity and are unable to provide the high-quality grades required by the paper industry, prompting the need to onboard foreign suppliers.
Comparison with Foreign Suppliers
Though Indian manufacturers have developed expertise in various components, such as pumps, refiners, drying cylinders, winders, vacuum pumps, and few other auxiliaries, there is still a lack in the complete upgradation of the line or the total project, especially for large-size paper or board machines. To be honest, there is no comparison between the technology provided by the European vendors to that of domestic vendors, in terms of overall performance, efficiency, and safety features. There is always a generation gap between the two, as most of the domestic machinery is developed through the reverse engineering process, while European machine manufacturing companies rely and invest heavily on R&D, thus staying at the forefront of technological advancement. Their machinery is compatible with integrating the latest automation, digital monitoring, and efficiency, and thus helping enhance the overall features of their equipment and taking production to the next level.
When choosing machinery, paper mill owners must thoroughly understand their product, current market demand, projected growth, and export potential. These factors are critical, as any investment should be evaluated concerning revenue generation and long-term profitability
By partnering with high-end European technology providers that offer optimal operational scale and efficient project execution, domestic manufacturers can revolutionize the industry over time and enhance their competitiveness.
Right Machinery in a Cost-Effective Manner
When choosing machinery, paper mill owners must thoroughly understand their product, current market demand, projected growth, and export potential. These factors are critical, as any investment should be evaluated concerning revenue generation and long-term profitability. In the pulp and paper industry, few entrepreneurs possess both the financial resources and the strategic vision required for economies of scale, paired with a skilled project management team capable of delivering successful projects.
Before choosing a machinery supplier, it’s vital to finalize the project size based on the expected return on investment. For production capacities under 100,000 tons per year, domestic or Chinese vendors are often the most cost-effective option. However, for production volumes exceeding 200,000 tons per year, advanced machinery from foreign suppliers is usually the better investment. These machines, known for their high efficiency, durability, and energy savings, have consistently exceeded expectations in India, often operating at over 125% of their designed capacity. They offer reliable performance and maintain operational efficiency on a daily basis.
All in all, the mill’s success depends on having an experienced team of project managers capable of making smart, strategic decisions to ensure that the company selects the most suitable and cost-effective solutions for its unique needs.
With faster delivery times than foreign suppliers, Indian machinery provides customizable options at much more affordable prices.
Evaluating Indian Machinery
The biggest advantage of procuring machinery from Indian manufacturers is their cost-effectiveness. Along with faster delivery times compared to foreign suppliers, Indian machinery offers customization options at a much more affordable price. These “Make in India” machines can yield solid short-term returns. Experienced local engineers deliver on their promises at significantly lower costs while possessing a deep understanding of local demands and operations. On the other hand, one cannot completely negate the disadvantages of these domestic machinery. Most of these local machineries are energy inefficient and have much lower reliability due to the absence of advanced integrations, lack of engineering precision, and insufficient application support.
Also Read: Kuantum Papers: Maintaining Edge with Indian Machinery
Scope of the Indian Machine Manufacturers
The volume of business, the scale of the economy, and budget-friendly projects have advanced our paper machine manufacturing sector but are not enough motivation for investments in the manufacturing infrastructure for highly specialized and advanced machinery at the vendors’ end.
In order to build high-end advanced machinery for the paper and pulp industry, Indian machine manufacturers must collaborate with European manufacturers as we look to European vendors for advanced technology in the paper machine manufacturing sector. Additionally, the Europeans are not willing to move to India as it would incur large investment on their part for setting up manufacturing units in the country. So, this is a win-win situation for both.
Although India is slowly advancing as the technological and manufacturing hub with its Ease of Doing Business, and Make in India initiatives, there is still a divide in the technology sourcing based on the scale, business strategy, and the capacity to sustain the investment load.
Indian paper mills with capacities of up to 100,000 tonnes per year can rely on suppliers from India, China, and Korea. However, domestic players aiming to compete in the premium segment with the right economies of scale still depend heavily on European vendors. This reliance showcases the significant untapped market that requires substantial investment, deeper R&D, and intensive resource allocation to fully capitalize on its potential.
Indian manufacturers can draw inspiration from various technological companies present globally that possess the necessary strategies and adequate scale to meet the demands of the mills. Despite relying entirely on European vendors and facing high annual investments per ton of installed capacity, Indian paper mills have still achieved impressive returns on investment.
To summarize, by partnering with technology providers that offer optimal operational scale and efficient project execution, domestic manufacturers can revolutionize the industry over time and enhance their competitiveness. This strategic alignment will empower them to match or even surpass European vendors in both technology and scale, fostering a more robust and innovative future for the sector.
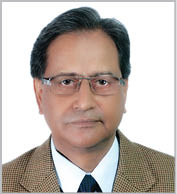
About the author:
He serves as an advisor and consultant in the paper and paperboard industry. Previously, he held the position of Chief Executive of New Projects at JK Paper and served as Vice President of Business Development and Operations at ITC PSPD in Hyderabad.