ProJet’s Power Cleaner 2.0 is expected to be delivered to Keryas Paper Industry in the Q4 of 2022. The 2.0 version has a unique 3-stage self-cleaning station, that makes the system superior in terms of runnability compared to competitors.
August 18, 2022
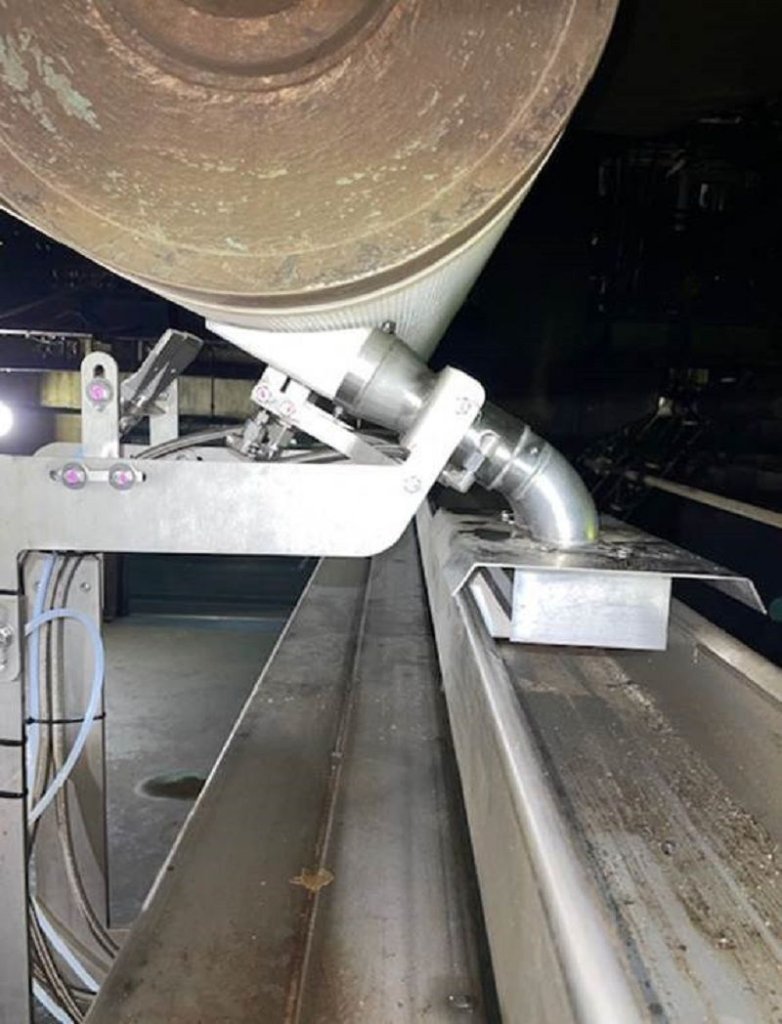
Oman-based Keryas Paper Industry LLC has ordered two power cleaners (dryer fabric cleaners) for their Paper Machine 1 (PM1) from ProJet. The new cleaners will be installed on the first and the second Unirun. The value of the order has not been disclosed.
Notably, ProJet has already supplied more than 40 power cleaners to paper mills in the Middle East in the last decade. The HP cleaners are installed in the forming and press sections as well as the dryer sections of the machines.
Watch: IVAX Paper Chemicals Interview
The PM1 produces corrugated medium and kraftliner, utilising 100 percent OCC. Since OCC can cause huge contamination on the dryer section, Keryas Paper Industry has selected ProJet yet again. The equipment is scheduled to be delivered in Q4 of 2022 whereas the installation and the startup are expected to take place later in 2023. The Power Cleaner will be ProJet’s Power Cleaner 2.0, which is the upgraded version.
The upgrade consists of a smaller cleaner head, more nozzles at a higher pressure and an improved vacuum/discharge system. The 2.0 version has a unique 3-stage self-cleaning station, which ensures that the system is superior in terms of runnability compared to its peers. The combination of all these improvements is an enormous increase in cleaning efficiency and a reduction in maintenance.
Also Read: Keryas Paper Industry: Leading Paperboard Producer in Oman with 180,000 MTPA Capacity
Applying a ProJet Cleaning Solution guarantees consistently clean dryer fabrics from beginning to the end of usable dryer fabric life. Consistently clean fabrics deliver the following significant manufacturing advantages:
- No chemical cleaning will be required to maintain fabric cleanliness.
- No shutdowns will be required for fabric cleaning. This will provide increased manufacturing productivity and profitability.
- Maintaining consistently high dryer fabric air permeability increases available dryer capacity.
- Better CD moisture profiles will be maintained.
- Sheet curling, caused by uneven drying, will be eliminated.
- Dryer fabric life will be substantially improved.
- Much less contamination will be deposited on dryers, doctor blades, and felt rolls.