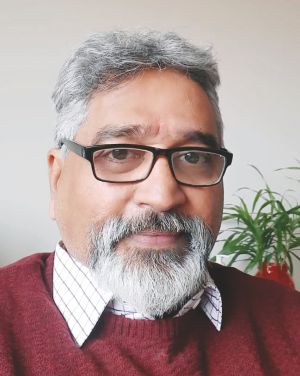
In its fresh water usage in the plant, Khanna Paper follows various control measures like closing the water loop to more than 80%, reducing the fresh water usage by reusing the rich and lean back water from the system for various dilution of stock and even some chemicals. According to Mr. SVR Krishnan, its COO, the monitoring system at the mill is so robust that there are no unmetered tapping points at the mill.
Paper Mart: How would you describe water efficiency of your operations?
SVR Krishnan: Ours is a wastepaper based eco-friendly plant in the heart of Amritsar, and the whole operations are carried out in a very responsible manner that we meet all the environment-related compliances.The processes are designed in such a way that side streams and the byproduct are taken for reprocessing and reuse inside the plant to give some other form of useful product.
With respect to fresh water usage in the plant, we follow various control measures like closing the water loop to more than 80%, reducing the fresh water usage by reusing the rich and lean back water from the system for various dilution of stock and even some chemicals, and also optimizing the usage by timely replacement of the shower nozzles and to the right size and shape with suitable pitch between them.
We also effectively use rainwater from the harvesting pits for various applications across the mill. The monitoring system at the mill is so robust that there are no unmetered tapping points at the mill, and we have shift-wise dash boards, alarm and reporting system right from the DCS to the in-charges and up to the factory manager level.
Still, there are areas where we need to improve on the quality of the treated water to increase the usage points and further reduce the fresh water consumption.
PM: What’s your aggregate annual fresh water consumption and how much have you reduced over the years?
SK: Yearly, we consume close to 32 lac M3 of fresh water, and have reduced 28-30% of our fresh water consumption through various measuring, monitoring and plant control measures.
PM: What percentage of water is recycled and how the discharged water is utilized?
SK: Almost close to 25% of water consumed is recycled in various areas of plant operations, especially in the de-inking plants and waste paper processing areas. The discharged water, after meeting the Pollution Control Board norms, is used in irrigation, cleaning and other domestic purposes.
Watch: Top Paper Companies 2023
PM: Kindly elaborate the innovative solutions you have introduced at your mill.
SK: We have started using 100% backwater from the machines by proper treatment for reducing the TSS with DAF (Diffused Air Floatation), PDF (Poly Disc Filter) and MPS (Micro Plate Settler), etc at various points in the process, including the LP and HP cleaning showers.
In the secondary clarifier, we incorporate multi Grade Filters (MGF), Active Filter Media (AGF) and Softeners to remove dirt and other contaminants for the superior quality of treated water meant for Paper and Board Machines.
Introduction of Poseidon, an advanced version of DAF, has helped in treating Disc Filter water and clarified water reuse in critical applications.
Further, cooling tower and boiler blowdown water are collected and reused for the dust and fly ash suppression and other non-critical cleaning operations. Then the fully treated final clarified water is used for horticulture and other factory cleaning purposes.
We have started using 100% backwater from the machines by proper treatment for reducing the TSS with DAF (Diffused Air Floatation), PDF (Poly Disc Filter) and MPS (Micro Plate Settler), etc at various points in the process, including the LP and HP cleaning showers.
PM: How seriously do you look at water harvesting and how much do you rely on it?
SK: Even though we are in an area which receives less rainfall, we consider harvesting it and its usage with great degree of seriousness. We have made two big U/G tanks inside the plant at two locations for collecting rainwater and storing it. This covers the majority of the areas in the plant, and we are in the process of making a few more at strategic sloped locations inside the plant. This stored water is used at many locations and also for the localized fire hydrant system, without depending on the main fire safety pumps.
PM: What is your water reduction target?
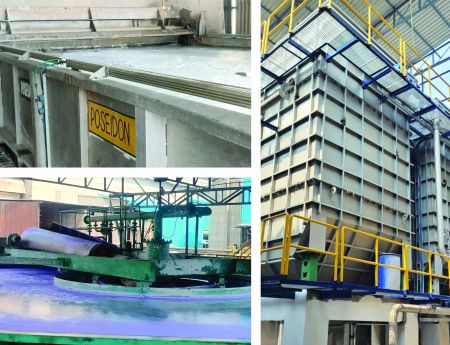
SK: We plan to further reduce water consumption by another 20% by installing additional aerators and enlarged tertiary treatment with MBBR, UF and Nanofiltration and installation of RO plant of suitable capacity in the second phase.
We are also looking into various aspects of bio-treatment, innovative mechanical filtration and the best way for reducing the COD and TDS levels in the final treated water, which will make our plant a good MLD
(Minimum Liquid Discharge) Plant in this part of the country.
Having seen and understood the criticality of fresh surface and ground water availability, we are now planning for a huge UGR (Underground Reservoir) facility for rainwater harvesting and the canal and sub-canal water from outside. This will be stored and treated for the reuse inside the plant for all the noncritical applications.
Also Read: Emami Paper Targets 10% Water Usage Reduction by 2025-26
PM: What challenges do you often face in fresh water conservation?
SK: Though every mill in the country, be it big or small, wants to be more efficient on water usage and reduce the overall mill fresh water consumption, the biggest challenge is the prohibitive capital expenditure, availability of the area for an elaborate system and the technologically sound people from micro-biology or the water chemistry background/experience to operate. Mills which are handling multiple furnishes and operating several machines with various white and dyed grades have a big challenge in process integration and process modification to improve the quality of the water for reuse.
The integrated pulp and paper mills have a big challenge on the treatment volume and treatment cost, where the low and high TDS streams are mixed before going to the ETP. The separation of the low and high TDS streams and separately collecting and treating them will give the desired performance, but again it involves a big capital cost. This appears to be the only solution for effectively handling both the streams.
Last but not the least. Fresh water conservation and recovering the good usable water from the waste streams demand a cultural and behavioural shift and that shift in gear is “somehow managing to specific controlling”. Again these things start from People. My mantra always is: “People, Planet and Profit”, and let us not look at it in reverse, which will never work in the long run.
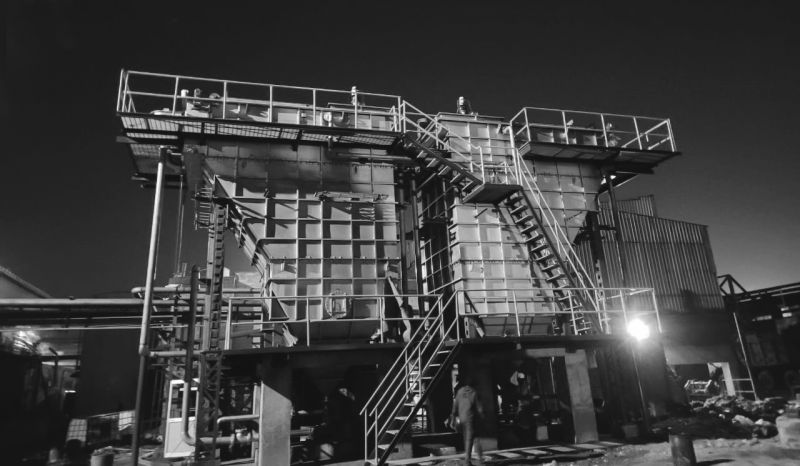