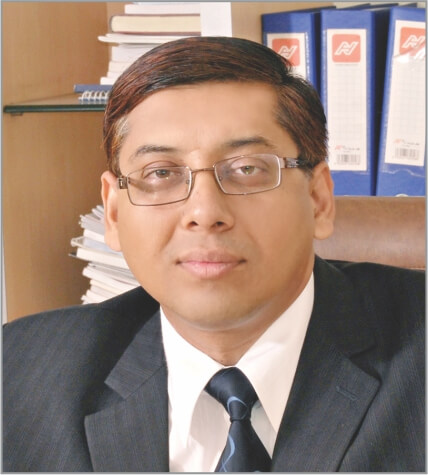
Currently, Naini Papers’ annual water consumption is 43,80,000 m3 (i.e.30 m3/ton of paper). The company has set benchmarks for water consumption for all major areas of the mill and adheres to the same. We identify the areas with fluctuating water consumption and take necessary measures to control the same on a daily basis, says its Managing Director, Mr. Pawan Agarwal.
Paper Mart: How do you ensure water efficiency in your operations?
Pawan Agarwal: We ensure water efficiency in our operations by regular monitoring of the water consumption. We identify the areas with fluctuating water consumption and take necessary measures to control the same on a daily basis. We have set benchmarks for water consumption for all major areas of the mill and adhere to the same. We revise the benchmarks after constant achievement of the same.
PM: What is your aggregate annual water consumption? What much has that been reduced over the years?
PA: Currently, our annual water consumption is 43,80,000 m3 (i.e.30m3/ton of paper). Before the implementation of the charter in 2012, the consumption was 80-100 m3/ton of paper. After the implementation, we worked a lot on implementation of green technology and maximum recycling of treated effluent and we were able to reduce the same to 30 m3/ton in the subsequent years. Further reduction will affect the paper quality since the TDS gets accumulated in the system. Only membrane technology can further reduce the fresh water consumption.
PM: What percentage of water consumed is recycled, and where is the discharged water reused?
PA: Approximately 50% of the treated effluent is recycled in the process and the remaining is discharged in the nearby drain after tertiary treatment. However, we have installed a 2 MLD ZLD plant to further recover 1800 m3 of fresh water from the discharge. Therefore, we are able to recycle 70% of discharge.
Watch: Top Paper Companies 2023
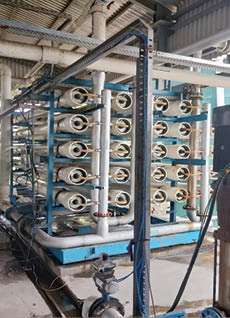
PM: What innovative solutions have you introduced in different areas of your mills that have made them more water efficient?
PA: We have intoduced many innovative solutions such as:
- Installation of Efficient IBS showering system on paper machine, wet end to reduce water consumption drastically.
- Complete recycling of paper machine effluent to pulp mill by passing through Krofta.
- Installation of state-of-the-art DCS-based Biomethanantion plant from Hydrothane (Netherland) for High effluent load drains.
- Use of ETP treated effluent after secondary stage for wet washing of raw material and wetting of bagasse wet bulk storage.
- Installation of Reverse Osmosis (RO) system followed by MEE & ATFD system – Capacity 2000 m3 day.
PM: How seriously do you undertake water harvesting, and how much do you rely on it?
PA: The aquifer inside the factory site is charged therefore rainwater harvesting is not possible. However, we have constructed 20 nos. gabion structures in the rain drains for high recharge of rain water in upper region of Ramnagar and Haldwani.
The catchment area of these nallahs is about 16 km2 which receives an annual rainfall of 1930.20 mm and an annual rainfall volume poured over it is 30.88 MCM. If 25 % of this volume is recharged it will amount to 7.72 MCM (i.e. 77,20,000 m³) which is approximately 1.5 times the annual water withdrawal (43,80,000 m3) by Naini Papers Limited.
Our water usage reduction target is 20 m3/ton of paper. We are planning to achieve it by further implementing the membrane technology for effluent recycling and adoption of green technologies.
Also Read: Khanna Paper Plans to Reduce Water Consumption by Another 20%
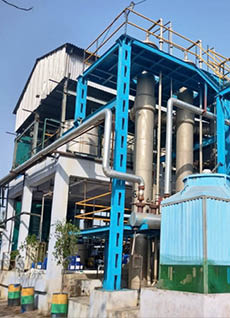
PM: What is your water usage reduction target? How do you plan to achieve it?
PA: Our water usage reduction target is 20m3/ton of paper. We are planning to achieve it by further implementing the membrane technology for effluent recycling and adoption of green technologies.
PM: What are the challenges you often face in making your mills water efficient?
PA: Firstly, the quality of paper is affected if we further recycle the effluent, since the same leads to accumulation of pollution load and TDS within the system which deteriorates the quality of paper. Secondly, the cost economics for implementation of membrane technology for recycling the treated effluent is very high, we have been working on the same for the last 4-5 years, and we are able to reduce the cost from 200 m3/KL to 120 m3/KL. But still the same is on the higher side. Also, the implementation of latest green technologies involves a huge cost, however we are implementing the same in a phased manner.