The Indian Pulp and Paper Technical Association (IPPTA), in collaboration with ICCMA and WICMA, hosted a two-day zonal seminar on November 17-18, 2024, at Hyatt Place in Chhatrapati Sambhajinagar (formerly known as Aurangabad). The event centered on the theme of ‘Manufacturing Various Grades of Paper to Meet the Emerging Demand of Packaging Industry’ bringing together industry experts and stakeholders to discuss emerging drivers and innovations in the packaging sector.
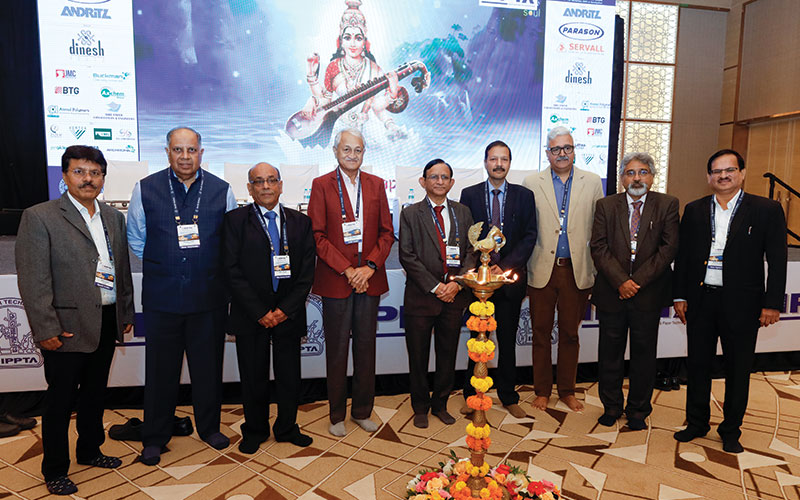
The event was attended by the industry leaders and dignitaries including Mr. Pavan Khaitan, President, IPPTA, and Mr. S.V.R. Krishnan, Vice President, IPPTA. The chief guest for the w was Mr. Ramchandra Neelkanth Bhogle, President, ICC, Maharashtra, along with Guest of Honour, Dr. VS Sakpal, Vice Chancellor, MGM Univwersity, and Special Invitee, Mr Anil Loya, President WICMA.
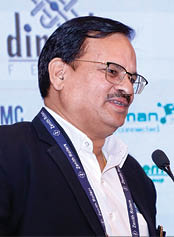
The event began with the keynote address delivered by Mr. Shekhar Desarda, Chairman of the Programme Committee and CMD, Parason Global. In his address, he talked about the paper industry which produces 5 lakh tonnes of paper on the Godavari bank (Aurangabad) and provides employment to 2 lakh people across the region. He further talked about the growing dominance of the packaging sector within the paper industry, noting that kraft paper accounts for 70-80% of the total paper production, driven directly by the growing demand for packaging solutions.

Following this was a welcome address by Mr. M.K. Goyal, Secretary General, IPPTA, who gave further insights into the industry. He revealed that the global kraft paper market is currently USD 17 billion. In 2032, it is expected to grow to about USD 27 billion at a CAGR of 8%.
According to the International Market Research Consultancy Service, 10.2 million tons of kraft paper has been consumed by the corrugation industry in 2023. And in 2032, this consumption will double, showcasing the growing potential of the packaging industry.
Mr. Goyal stated “In India, the paper production is about 25 million tons, out of which about 5.5 million tons is writing and printing, about 4.5 million tons is paper board, and 14 million tons is kraft paper. So, 10.5 million tons of kraft paper goes to the corrugation, and the rest is used in paper bags, packaging, wrapping and many sectors. It is nearly 78% of the total production with manufacturing industrial belts in Thane, Belapur,Pimpri-Chinchwad (Pune), and Aurangabad. Aurangabad is the third largest belt which contributes 12 to 13% of the GDP of Maharashtra.”
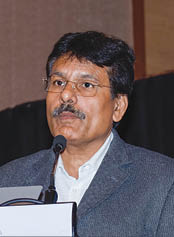
Continuing the discussion, Mr. Anil Loya shared his insights on how IPPTA has been instrumental in promoting knowledge sharing, networking, innovation, and synergy within the industry. As the President of WICMA, he highlighted the association’s 57-year-old legacy in upgrading box manufacturers. He emphasized the role of their state-of-the-art R&D lab in Andheri, Mumbai, which is fully equipped for comprehensive box testing. Notably, this lab stands out as the only facility, apart from IIT, authorized to issue UN certification for boxes.
In his address, he also highlighted the challenges faced by the paper industry, particularly the growing pressure to adopt sustainable practices and the disruptions in the supply chain, which have become significant obstacles. However, he emphasized that by embracing innovative technologies and integrating sustainable practices, the pulp and paper industry can overcome these challenges, maintaining a competitive edge, and effectively meeting the future demands.
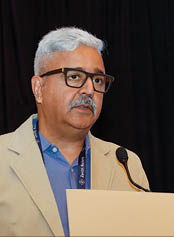
Moving ahead, Mr. Ramiah Muthusubramaniam, CEO, Packfora, talked about the paper making technique which has been a cornerstone of human culture, communication and education.He emphasized three key aspects: the role of IPPTA in the pulp and paper industry, the industry’s evolution over the last 20 years, and its future outlook.
He further highlighted that around a decade ago, the Indian paper industry had a production capacity of approximately 13 million tonnes. Today, this has grown to 25 million tonnes—an increase of 12 million tonnes in just 10 years—signaling tremendous future potential. He noted that the Indian paper industry is currently valued at USD 10 billion, trailing the US and China.
With rising disposable incomes among the middle class and innovation at the forefront of the Indian paper industry, combined with the rapid growth of quick commerce and e-commerce, the industry is poised for significant opportunities—particularly in the packaging segment, which is undergoing a transformative phase. Furthermore, the per capita consumption of paper in India is expected to multiply substantially, creating a massive demand to cater to this growing population.
He further emphasized the emerging innovations in the paper sector, highlighting advancements such as biosensors and health and wellness applications that propel the industry beyond its conventional uses. However, he also pointed out a significant challenge—the lack of self-reliance in fiber production—which poses a critical threat to the nation’s paper industry.
Mr. Muthusubramaniam asked the industry leaders to step up and work towards collection and recycling of paper waste to deal with this shortage. He revealed that India is currently collecting about 45% of the paper back into its system, as compared to PET bottles where the return percentage is 90%, while globally, Sweden is collecting 91% of the paper back to the system, inspiring us to move rigorously towards the initiative.
He further added that water conservation is a part of the USD 5 trillion economic journey in India. He suggested that the paper industry could adopt closed-loop systems and carbon-neutral production methods, aligning with the nation’s goal of achieving carbon neutrality by 2070.
Mr. Muthusubramaniam emphasized that the country and its industries must move from table stake sustainability into futuristic sustainability which is about urban neutrality and GHG reduction. The industry leaders should not only evaluate their own operations but also assess the environmental footprints of their ecosystem and supply chain partners in the market.
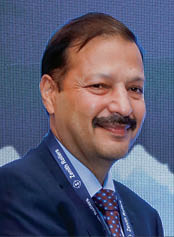
Taking the discussion forward, Mr Pavan Khaitan talked about unprecedented growth and rise of packaging demand due to rapid urbanization, e-commerce and a push towards sustainability. He talks about and prioritizing quality and consistency in the packaging segment.
According to a World Packaging Organization report, packaging materials must meet the increasingly stringent regulations regarding strength, safety and sustainability. Implementing automation and advanced control systems can enable the paper industry to meet these standards. Mr Khaitan added that the AI-driven quality checks have been proven to reduce defects in production by 30-40% . He further adds that industries can collaborate with research universities to take a positive step in this direction.
IPPTA also highlighted that the multi-state holder partnerships have helped improve production efficiency by about 20%. IPPTA will continue to foster such initiatives and encourage its members to engage in efforts that benefit both the industry and the environment.
Watch: In Pursuit of Lesser Water Footprint‘
Technological Innovation and Multi Disciplinary Approach in the Packaging Industry
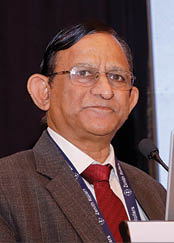
Taking the subject of innovation forward, Dr. V. S. Sapkal, Vice Chancellor of MGM University talked about the integrated solutions and membrane technology. He says that the membrane technology is designed in such a way that it can be used in micro filtration, ultra filtration, nano filtration and reverse osmosis depending upon the physicochemical structure of the membrane. The technology has brought transformation in the operations by reducing the consumption of water, increasing the energy efficiency, and increasing productivity in the paper industry.
The rise of artificial intelligence, machine learning, and data science can further give predictive data for performance optimization of any process. He further talked about the big trend of digitization that is rapidly expanding in the educational system. He believed that no technology can replace paper, and the paper industry can integrate with the digital and IT industry, to increase the performance of the core industry.
With the National Education Policy promoting multidisciplinary education, paper technology can integrate with fields like artificial intelligence, machine learning, and design. This approach fosters cross-disciplinary collaboration, enabling the industry to leverage knowledge from various fields for more effective and innovative solutions.
Paper vs Plastic
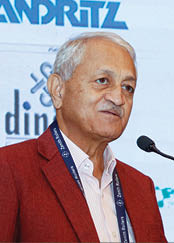
Mr. Ramchandra Bhogale, highlighted the theme of plastic vs paper emphasizing the shift in perspectives over the year. He highlighted how a narrative was built that the paper can destroy the ecosystem to pave the way for the rise of the plastic industry and how over the years people realized that paper, being biodegradable and easy-to-dispose is rather a companion to the environment, while plastic, with its non-biodegradable nature and the release of harmful plasticizers, poses a much greater threat to the environment.
He further stated that with innovation, paper is replacing many conventional products and emerging as a leading player in the packaging sector. Luxury packaging and innovative solutions like bagasse-based packaging are overcoming previous limitations, bringing the much-needed change to the world.
The pulp and paper industry is at a critical juncture that could provide real growth. By encouraging young minds to innovate freely, the country can create new paper products and applications that can drive the industry to new heights and achieve the unimaginable.
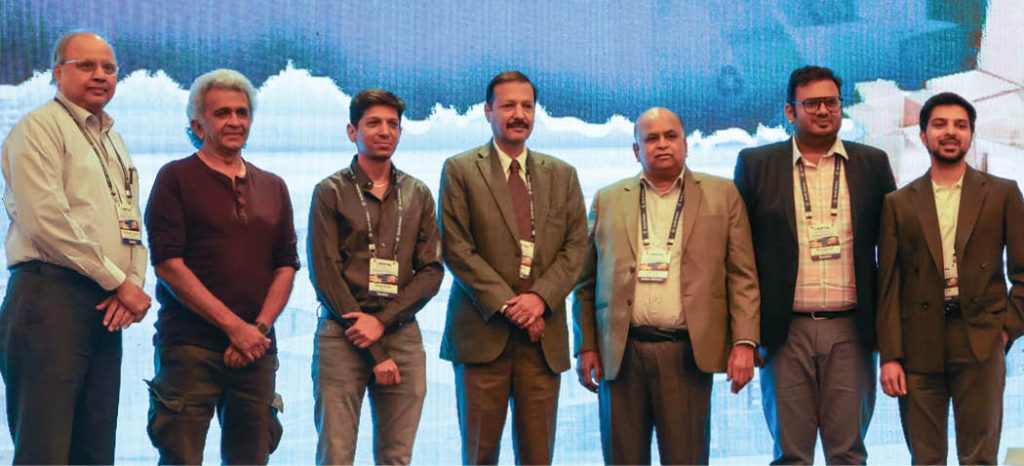
Expanding Possibilities of Paper – Emergence of the New Markets
The second day kickstarted with a session on the theme of Expanding Possibilities of Paper – New Markets. It explored innovative applications of paper beyond the traditional use. With the rising demand for sustainable alternatives, paper is now making trips in the area like eco-friendly packaging, furniture and retail solutions. This shift opens new opportunities for growth in emerging markets. By combining innovation with sustainability, paper is transforming industries and meeting evolving customer needs. The session focused on how to transform the industries and meet the growing demand for eco-friendly alternatives.
Mr. B. R. Rao, Founder Member of the Bharat Paper Foundation and Chairman of the session, addressed the misguided and false narrative that has been framed around the paper industry. He says, “Everybody talks about sustainability and bioregulation, but in advocating these terms, some resort to ‘greenwashing’ in the paper industry. As paper enthusiasts, we have the responsibility to provide a clear picture to society about what paper truly is, and how it actually benefits the environment, rather than harming it.”
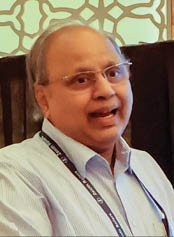
Following this, Mr. Ramkumar Sunkar of Bhargavi Paper Industries discussed the concept of square drums made from 100% kraft material for use in the chemical industry. Traditionally, round or cylindrical drums, often made from paper or metal, were used to package and deliver a wide variety of products from industries such as pharmaceuticals, fine chemicals, agrochemicals, and food.
However, this conventional form of packaging has limitations in terms of space utilization and environmental sustainability. To address this, Mr. Sunkar offered an innovative packaging solution in the form of Square Fiber Drums, which are fully recyclable and biodegradable.
He further explained, “In the past, drums used in the chemical industry were made from a combination of materials such as wood and metal. The metal parts had to be cut off before disposal, which not only incurred additional costs for users but was also not environmentally friendly. The new packaging, however, is crafted entirely from 100% kraft material with a square design, including a square base. They are easy to reuse and recycle, and the drums feature hand-rolled cutouts for easy handling. Available in various sizes, these drums are designed to be placed on a CP3 pallet of 1140 by 1140 size. Due to the square shape of the drum, the loadability of the container is also very high offering both operational and environmental advantages.’’
The square drums developed by them enable optimum consumption of space, are cost-effective and sustainable, have supreme strength and stability, are easy-filling and emptying, have robust strength and stability, and have high-resistance to pressure.
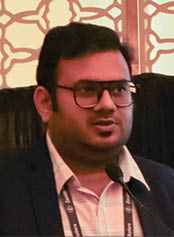
Taking the discussion forward, Mr. Niraj Agrawal, Director, Hexacell Packaging, talked about the eco-friendly protective paper packaging solution such as Honeycomb paper boards, Honeycomb paper separators, Honeycomb paper pallet and many more that serve as a substitution to wood, thermocol (EPS), styrofoam and other plastic packaging materials. They are made from kraft paper and wheat paste, and are 100% recyclable and biodegradable. He said, ‘‘We use six layers of paper glued together to create a net-like structure, which is then expanded and laminated into a honeycomb sheet. It’s similar to how plywood is created and then fabricated into furniture.’’
The Honeycomb paper packaging solutions offer more strength than 5 ply and 7 ply corrugated sheets and have a unique shock absorbing mechanism which prevents products from damages while they are in transit. The unique honeycomb design uses the least amount of paper and is one of the strongest designs found in nature. Paper Honeycomb products can quickly adapt to any situation, and can hold heavy weights. The disposal cost of the product is nill, making a perfect choice for paper manufacturers and industry applicants.
Sustainability in the Packaging Sector
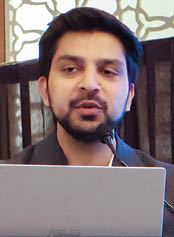
Mr. Raag Todi, Director, CanPak Trends, talked about sustainability. He said, ‘‘There are 2 aspects of sustainability. One aspect of sustainability is in the raw material production process and the second aspect is in waste disposal. In a country like India, we are very much focused on the waste disposal aspect. There are four ways by which waste is disposed of. It includes incineration, recycling, composting and landfills. When incinerated, the paper produces much less carbon emission than plastics do. And in the landfills, paper decomposes much faster than plastics. This is why everyone has moved towards paper in the recent years.’’
He further added that there are three key things that the packaging industry should focus upon. First, possessing the technology to produce high-quality paper, and source it regularly. He emphasized on the need to adopt high-quality paper and sourcing practice on a wider scale, to all small and big industries across the regions.
Secondly, the need to focus on improving the water resistance properties of paper, as this is an area where paper currently falls short. By adding the water-repellent coatings and incorporating them into the production process, the paper industry can significantly enhance the water resistance and ensure the continued acceptance and growth of paper in various applications.
Lastly, puncture resistance is another critical area. Puncture resistance refers to a material’s ability to withstand the force of a sharp object or impact without breaking or puncturing. In the context of packaging materials, this property is useful especially when it comes to protective packaging, food packaging, and shipping.
While some of the more technologically advanced plants in India are already implementing these improvements, it’s important that the industry as a whole focuses on these aspects to keep up with the evolving trends.
Also Read: Paper Mart Emagazine Oct-Nov, 2024
Paper Packaging in the Food Industry
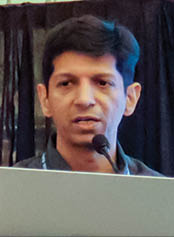
Mr. Shlok Kedia, Director, Ginni Gopal Boards, discussed the significance of paper packaging in the food industry. Mr. Shlok Kedia, Director, Ginni Gopal Boards, said, ‘‘We need to come out of the perception that paper is mainly used for outer packaging, and see the different applications of paper packaging, opening our eyes to see more useful applications of the paper in primary packaging. When I say primary packaging, it means that the paper is coming directly in contact with the product and it needs to be given much more importance. Further, we also need focus paper product which is an industry in itself.’’
He further cites an example, saying, “In a pizza box, we do the printing and ensure everything is taken care of on the top side. However, the bottom side often goes unnoticed. If the quality of bottom paper or box is better, the shelf life of the product can increase, and if it is not proper, then the product can be harmed and in turn the user of the product can also harmed.’’
He further talks about the standardization of paper and paper boards. He says, ‘’Using alternative paper sources is not a viable solution when you are supplying your products to multinational companies, as it risks issues like duplication and quality inconsistencies. To address these challenges effectively, it is crucial to establish uniform standards and shades across the industry. For instance, in duplex paper, there are noticeable inconsistencies—bluish, yellowish, varying degrees of darkness, and lightness—depending on the region. This lack of standardization creates unnecessary complexity and hinders seamless collaboration with global clients.Standardizing shades and quality across the country is essential to ensure reliability and consistency, enabling us to better meet the expectations of multinational companies while fostering trust and long-term partnerships.’’
Paper Furniture
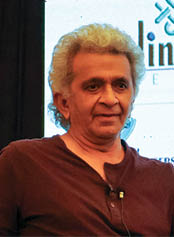
Taking the panel discussion to the end, Mr. Haresh Mehta, MD, Jayna Packaging talked about his revolutionary work in the collapsible cardboard furniture. He believes that anything can be done with a paper. He says, ‘‘I strongly believe that many things used in day to day life, made of metal, wood, plastic can in turn be made from paper. I would say this is one of the best and greatest wonders of engineering in a century to come. So, rather than throwing away the shipping boxes, the jumbo boxes, the shipout, and the pallets, it can be used in various ways such as children’s furniture. ‘’
According to him, paper furniture is an upcoming market where everything from hangings on the wall to the furniture in the house can be made from paper. One can turn this commodity into a brand.This is one of the best innovations and there are many places in Mumbai that have already applied this innovation where chairs, tables, ceilings, floor, almost everything is made of these collapsible cardboard materials.
With the rapid growth of quick commerce and e-commerce, the Indian paper industry is poised for significant opportunities—particularly in the packaging segment.
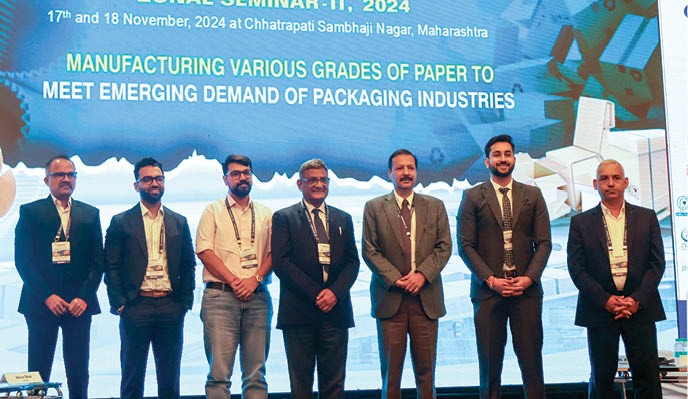
Odour: A Critical Issue for the Paper Sector
The session was followed by another panel discussion on the challenges of odour in the paper industry. Odour in packaging materials is a critical challenge pertaining to quality issues, particularly in industries like food and cosmetics, where product integrity is paramount. Foul odour can compromise customer experience and brand reputation. Addressing this challenge requires innovative solutions in material selection and production processes to ensure odour-free packaging.
This session focused on the challenges faced by the pulp and paper industry, particularly addressing the odour issue, and the market feedback of two industry leaders who faced challenges related to odour, followed by the industry solution provided by the other three members of the panel.
Mr. Rakesh Kumar Jain, Technical Expert, UNIDO, said, ‘‘We found odour in the paper, particularly in packaging paper, which contributes more than 70-75% of the country’s production. This issue is largely caused due to the poor quality of process water, a problem that has been worsened by the closure of the backwater systems in India. To address this, we should use biocides that are eco-friendly to control microorganism growth in the process water. Determining the microbial content in the water is crucial to assessing quality parameters and establishing the appropriate indicators for subsequent trials.’’
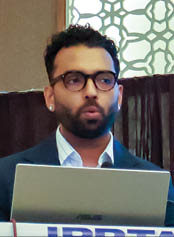
Following this, Mr. Saurabh Khetan, Director of Khetan Packfine, shared his personal experience of dealing with the challenge of odorous paper, which resulted in significant losses for his company. He explained, “I was not really aware of foul-smelling paper until 2017, when it hit us personally. One of our customers sent an email saying that containers packed with confectionery had been rejected due to odour, and a debit of INR 3 million was charged to us for detention, damages, and repackaging they had to undertake in the European continent. This incident led us to learn about a standard called TAPPI’s T 483 cm-23 which defines the permissible levels of odour. We then established this standard at our end, educated our customers about it, and later realized that this was limited to a few partners in the country, rather than being widely implemented throughout the country.”
Mr. Vishnu Shirodhkar of Lavino-kapur Cotton further advanced the discussion by sharing his personal experience with corrugated cartons, which transferred its odour to the product, leading to extremely negative feedback from customers. He explained, “We conducted some analysis with the help of IIT and found that the root cause of the issue was the quality of kraft paper, including factors like gum quality, moisture percentage, storage variations, and unclean transition conditions. We identified moisture as a major culprit, along with the recycled material used in the production of kraft paper.’’
He believes that the odor problem presents more of an opportunity than a challenge that will unlock doors to innovative ideas and solutions for the paper industry.
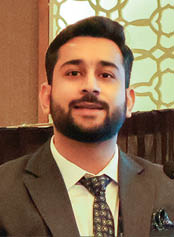
Mr. Shiva Sharma from Anmol Polymers proposed a solution to eliminate the foul odor in recycled paper production. To address the issue, he recommended a good biocontrol program and use of a good oxidizing agent for rapid action against microbial growth. He further emphasized that monitoring the bacterial activity using measurement tools like ORP (Oxidation-Reduction Potential) is crucial to keep a check on bacteria. The industry can use BS101 to deal with the total bacterial count of yeast and fungi, and BS115 for Sulfate-Reducing Bacteria (SRB).
He also highlighted the importance of chlorine dioxide (ClO2), stating, “ClO2 is very selective in its reaction. It targets specific microorganisms without causing significant damage to the substrate.” He concluded, “Another way to prevent the situation is to have a proper water treatment system so that the water used in the process is clean and odor-free.”
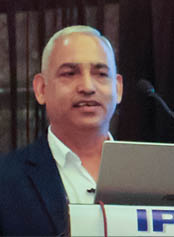
Mr. Raj Kumar from Parason proposed a solution using the aerobic resistance system in the Effluent Treatment Plant (ETP) to recycle water. He explained, “In an aerobic digestor, we transport the bacteria, which helps to produce bio CNG, a form of green energy that can be utilized in the power boiler or for power generation.” He highlighted the benefits of this system, saying that there is a 70% reduction of bacteria in aerobic digestion, and the chemical oxygen demand also comes down. Mr. Kumar further emphasized the efficiency of the process, stating, “Through this method, we can produce methane up to 60-65%, which is a very good value for usage.”

Finally, Mr. Varun Shah of Shree Ajit Pulp and Paper Solution addressed the management of water emissions, focusing on recycled kraft liquor (black liquor), which poses a significant odour challenge, along with starch, another key factor contributing to odour-filled paper. He emphasized, “We should have quality control in starch addition and be selective about which starch we use to reduce the odour issue.” Mr. Shah also recommended incorporating antimicrobial agents to reduce microbial growth, stating, “Incorporation of antimicrobial agents can reduce microbial growth and help mitigate the odour.” He stressed the importance of effective wastewater treatment, adding, “It is very important to effectively treat your wastewater.”
He concluded the session by emphasizing the importance of a proactive approach to managing paper odour before it becomes a widespread issue for the industry. He also highlighted the need for comprehensive training for all employees to ensure they are fully informed about the best practices for addressing odour problems in the paper sector.
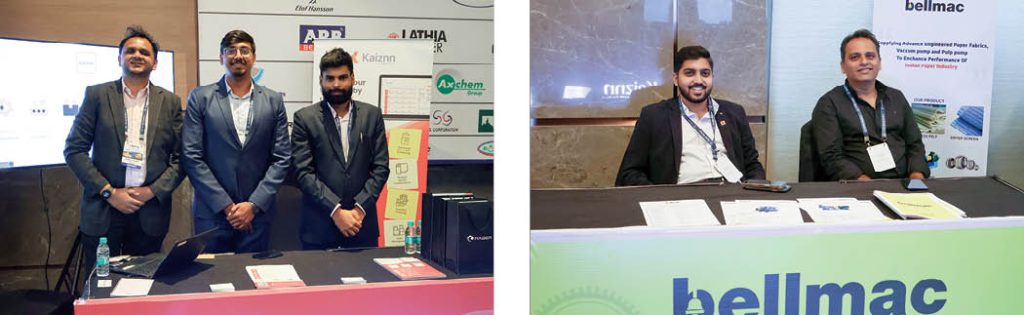
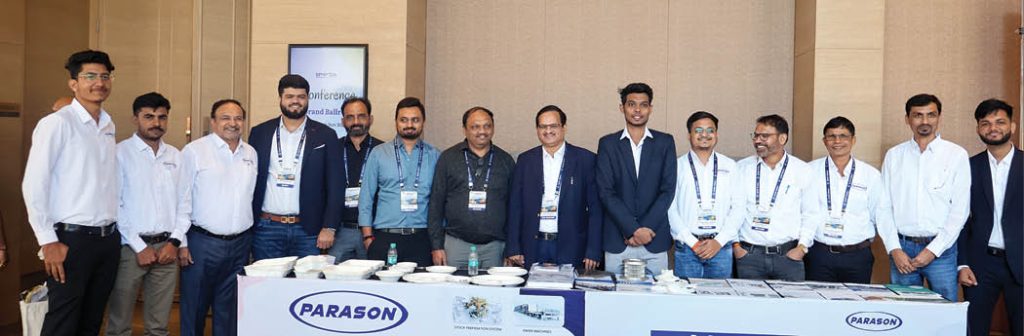
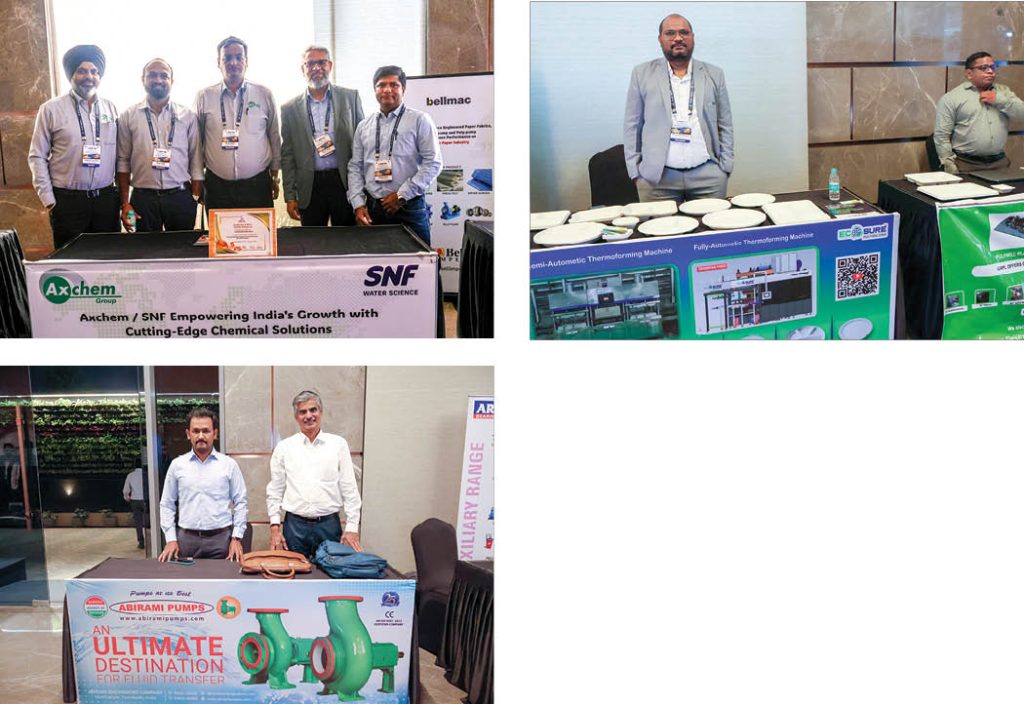