Major challenges in the industry are necessitating next-level operational optimization to better manage costs and production efficiencies. As a result, leading pulp and paper manufacturers are beginning to invest to integrate 4IR into the overall journey so that there is a long-term roadmap and payoff.
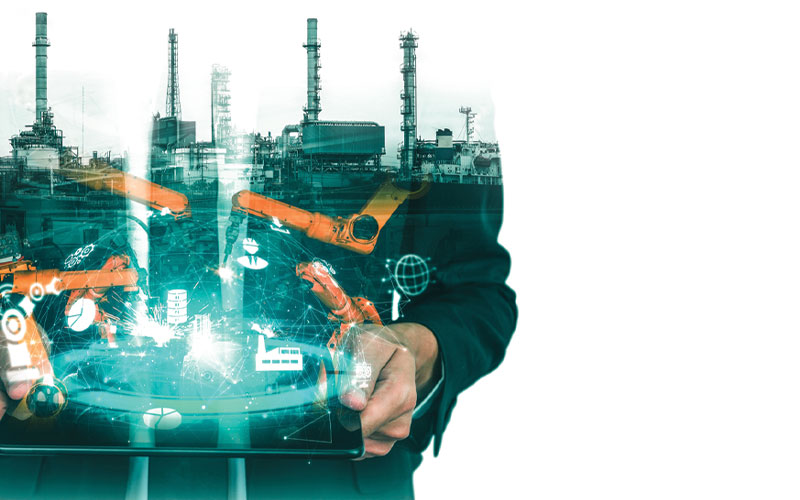
The pulp and paper industry is undoubtedly facing numerous challenges that pose significant risks to its sustainability and profitability. Due to its heavy reliance on natural resources and the associated waste and emissions, the industry is experiencing mounting pressure to minimize its environmental impact. Mills are actively seeking methods to enhance operational efficiency and decrease waste generation. As the costs of raw materials and energy continue to soar, maintaining quality control remains a persistent challenge, while a shortage of skilled labor further hampers productivity and efficiency within mills. According to a report by McKinsey in 2023, productivity in the paper sector reached its peak in 2018 but has since experienced a rapid decline. Despite some improvements noted in 2021, productivity remains 8 percent lower than the levels recorded in 2016. This downward trend underscores the necessity of finding innovative solutions to enhance productivity beyond merely expanding production capacity.
The industry is currently facing significant challenges that demand advanced operational optimization to enhance cost management and production efficiency. To effectively address these various challenges and the pressures on profitability, improved operational outcomes are essential. Prominent pulp and paper manufacturers are starting to invest in the integration of the Fourth Industrial Revolution (4IR) into their overall strategies, aiming to establish a long-term roadmap that promises substantial returns.
“At Khanna Paper, we operate two coated packaging board machines with an annual capacity of 150,000 tons, alongside two high-speed paper machines that produce all grades of writing and printing papers, copier paper, and newsprint, with a total capacity of 250,000 tons per annum,” states Mr. SVR Krishnan of Khanna Paper. “These machines are complemented by two dedicated deinked pulp lines, capable of processing 290,000 tons per annum, supplied by Lamort and Andritz, featuring fully integrated automation systems.” Furthermore, the company operates a pulping facility with a capacity of 125,000 tons per annum and a secondary fiber treatment plant that can handle 100,000 tons per annum to support the board machines. “All these production lines are fully automated and seamlessly integrated into our core operations. The facility is also backed by a fully equipped and automated effluent treatment plant,” Mr. Krishnan adds.
Silverton Pulp and Papers, leveraging extensive experience in paper manufacturing, asserts that all its machines are multiwire systems, producing both bleached and unbleached value-added products. “We possess an in-house cogeneration capacity of 21 megawatts, supported by a state-of-the-art effluent treatment plant that includes an anaerobic digester,” remarks MD Mr. Akshay Jain. “Our commitment to sustainability is evident as we work towards implementing waste-to-energy boilers that convert our effluent into gas, alongside the establishment of an anaerobic digester, and we are developing products aimed at replacing single-use plastics. Our facilities are entirely based on Distributed Control Systems (DCS) to ensure operational consistency and efficiency.”
In a DCS, control functions are distributed across multiple nodes interconnected via a communication network. Each node, commonly known as a controller or remote terminal unit, manages a specific segment of the system. These nodes interface with various sensors, actuators, and other devices to collect data and implement control commands. The communication network within a DCS facilitates data sharing among controllers, enabling coordinated real-time monitoring and control throughout the entire system.
Watch: In Pursuit of Lesser Water Footprint‘
Available Solutions
Keeping in mind the existing gaps, several solution providers have developed comprehensive solutions that could help mills to achieve their goals. Valmet provides an extensive range of automation solutions for the pulp industry, encompassing everything from individual measurements to comprehensive mill-wide turnkey automation projects. Through its advanced automation technologies and expertise in pulp processing, Valmet asserts that mills can enhance productivity, leading to improved yield and operational efficiency. The solutions offered stabilize pulp quality, augment energy production, and minimize both energy and chemical usage in pulping processes.
Valmet’s DCS comprises DNA, DNAe, and D3. The DNA system is designed to be ‘future-proof,’ addressing process automation needs across diverse industries, and is applicable for process controls, machine controls, drive controls, quality controls, and condition monitoring. DNAe represents a next-generation, fully web-based platform that offers an exceptional user experience and is built with cybersecurity as a fundamental principle. Meanwhile, D3 integrates robust hardware, straightforward software licensing, open connectivity, and a continuous migration path to optimize return on investment.
“The world around us is changing rapidly. Industrial systems like the DCS need to embrace this digital connected world,” states Jukka Ylijoki, Vice President of R&D, Automation Systems at Valmet. “Creating a genuinely open yet secure and sustainable DCS that can endure for decades necessitated a complete redesign. Every element of our newly launched Valmet DNAe was thoroughly examined to ensure it meets the reliability, performance, flexibility, and security requirements of our customers.”
AFT has introduced an innovative IIoT solution that adopts a data-centric approach to process optimization. Tailored for low-consistency refiners, the AFTLinx service aids in refining maintenance schedules and processes. According to Mr. Henri Heikkilä, Customer Service Engineer (AFTLinx) at Aikawa Fiber Technologies Oy, the solution features easily installable sensors that collect data on critical parameters such as refiner plate wear and condition assessment.
The company can acquire additional insights regarding flow, temperature, and other variables by utilizing customer-generated data or by incorporating additional sensors as necessary. The collected data is securely stored in a cloud service, ensuring easy access and strong data protection. With the AFTLinx service, which is available alongside our MaxEdge refiners, customers can, he says, take advantage of troubleshooting support from AFT’s expert team. This support encompasses assistance with startups, process optimization, and the testing of new refining methods, plate geometries, and equipment, all grounded in a data-driven testing approach. The company asserts that the AFTLinx service can be deployed with minimal disruption to existing mill systems, as sensors can be installed independently of mill automation. Additionally, there is an option to integrate AFTLinx sensor signals directly into the mill’s automation system, which can include a clash detection feature.
BTG Group’s dataPARC is another provider offering extensive solutions for managing pulp and paper operations. It addresses complex process, maintenance, and quality challenges with the industry’s premier process data analytics and visualization toolkit. dataPARC is capable of connecting various data sources and has been at the forefront of the essential IT/OT integration within the industry. It delivers data-driven insights that are meaningful to users at different operational levels.
At the DCS level, the organization offers enhanced tools such as ControlSuite and bConnect, which significantly improve the efficiency of regulatory control. Mr. Akhlesh Mathur, Head of Business, South Asia & Southeast Asia, BTG Group emphasizes that at level 3, the company has achieved remarkable success in the implementation of advanced process controls within pulp and paper manufacturing processes, boasting a wealth of established application experiences across diverse unit operations. These implementations have resulted in documented operational cost savings, enhanced quality, and a reduction in variability from shift to shift. Branded as MACSsuite, it employs proven model predictive controls to address the complexities associated with regulatory DCS level controls and to mitigate operator-induced variability. Although it is still early in the paper industry, BTG is actively pursuing mill-wide optimization projects in various regions, aiming to operate mills at the lowest possible costs while progressing towards the ultimate goal of an autonomous mill characterized by advanced process controls at level 4.
The company says it distinguishes itself from competitors through its commitment to delivering solutions that reduce costs, enhance quality, and improve efficiency, thereby creating a measurable and sustainable economic impact for customers. Following comprehensive system audits and in-depth discussions with clients, the company develops tailored solutions utilizing a variety of tools from its extensive toolbox. These solutions are implemented by locally empowered teams, with support from global subject matter experts, Mr. Mathur elaborates.
In the pulp and paper sector, the integration of IT and OT is essential for enhancing operational efficiency and facilitating uninterrupted data exchange among various systems. The implementation of OPC DA (OLE for Process Control Data Access) or OPC UA (Unified Architecture) for linking DCS or Programmable Logic Controllers (PLC) enables real-time data sharing and interoperability. Notably, OPC UA provides improved security and platform independence, making it particularly suitable for contemporary industrial settings. When these systems are integrated with SQL-based connections to Enterprise Resource Planning (ERP) systems, data from diverse sources can be efficiently queried and retrieved. Additionally, other data sources such as Laboratory Information Management Systems (LIMS) or Energy Management Systems (EMS) can be seamlessly connected to BTG solutions, Mr. Mathur notes.
OPC DA/UA facilitates real-time access to process data, significantly minimizing latency and enhancing response times for critical operations. By employing standardized communication protocols, BTG guarantees consistent and dependable data transfer between IT and OT systems. SQL-based connections optimize queries, allowing for rapid access to historical and transactional data housed within ERP systems. “Our architecture is designed for scalability, enabling the integration of further data sources and systems without sacrificing performance. Middleware solutions are frequently utilized to connect legacy systems with modern applications,” states Mr. Mathur. “This approach ensures smooth data exchange and interoperability without necessitating extensive alterations to existing systems. We employ protocol converters to facilitate communication between legacy systems and contemporary technologies. For instance, converting older proprietary protocols to OPC DA/UA standards guarantees compatibility and real-time data access.”
According to Harri Mustonen, DCS at Valmet, the requirements for a DCS have evolved significantly over the past two decades. “While the primary function of a DCS remains to link field devices to process controls, recent digitalization initiatives have driven the DCS to adapt and expand its capabilities.”
Also Read: eLIXAⓇ – Mt. Fuji: Haber at the Forefront of Industry Evolution
Collaboration
The development and implementation of a solution is merely the initial phase; the true challenge lies in its adoption, optimal utilization, and the maintenance of its benefits. The integration of a comprehensive solution necessitates a higher level of coordination, and this process is not confined to a single stage. To ensure that mill personnel can effectively utilize the automation solution, AFT offers extensive support and training. This encompasses thorough installation guidelines and practical assistance to facilitate a smooth setup. Additionally, staff receive training on how to analyze and interpret the system’s reports, enabling them to make informed, data-driven decisions for process enhancements. As data accumulation increases, advanced training is provided to help staff comprehend more complex data analysis reports, yielding insights for further operational improvements, Mr. Heikkilä shares.
BTG emphasizes the importance of involving key stakeholders, including shift operators, in the creation of tailored solutions. Their feedback on process management, emergencies, process control, and quality control is integral to this development. During the implementation phase, operators, shift engineers, and managers are engaged in great detail to refine the solution. From the project’s inception to its handover, the company dedicates significant time to training various levels within the customer organization to promote adoption. Most implementation engineers and project managers possess a background in the pulp and paper manufacturing process, which facilitates effective communication and accelerates adoption. “Maintaining the implemented solutions presents a significant challenge that is often underestimated by our clients. We offer flexible business models and on-the-ground support to help our customers sustain the benefits. There is considerable potential for improvement in Asia from this standpoint,” asserts Mr. Mathur.
Investment Return
In assessing the return on investment (ROI) for automation systems, AFT evaluates mill-specific baseline operational data, which includes factors such as unplanned downtime, typical component wear, process variability, and product quality. BTG emphasizes that to enhance the value offered to its customers, each salesperson is responsible for documenting the economic benefits of the proposed solutions for clients. Mr. Mathur notes that the typical ROI for most of our solutions is generally less than one year, contingent upon the size of the asset (production), the challenges faced, and the scope of the project. In the context of bleaching optimization, many mills achieve savings of approximately $2-10 per ton of pulp in bleaching costs, along with a reduction in brightness variability of about 20-50%. In energy optimization for lime kilns, mills typically realize energy savings of 5-20%. In power generation, mills have managed to lower their costs by approximately $1-2 per ton of pulp. Furthermore, the implementation of mill-wide dataPARC has resulted in reduced chemical and energy expenses, with a payback period of less than one year.
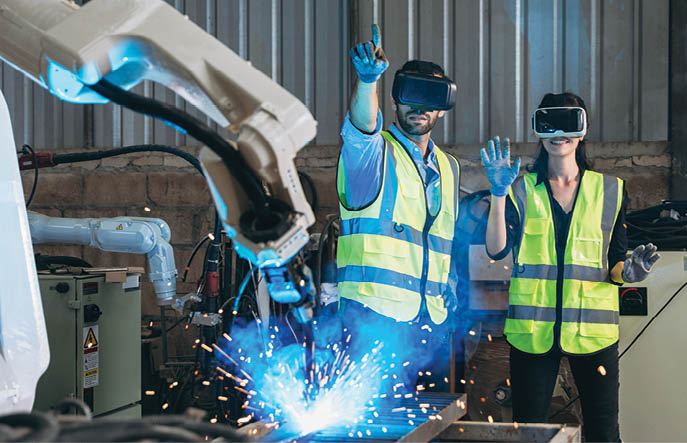
Scalability & Security
In the context of solution adoption, scalability is essential as it provides a strategic edge, allowing users to adjust to technological advancements and market fluctuations with minimal disruption. This adaptability facilitates the integration of new technologies as they emerge. To achieve this, AFT employs cloud computing, which offers the flexibility necessary for collecting and analyzing the ever-growing volumes of data. The system can also incorporate additional sensors with ease and minimal effort. While it is challenging to generalize, the majority of solutions implemented by BTG in the digital realm are designed to be scalable. For instance, with dataPARC, minor engineering adjustments may be necessary to enhance the solution when mills undergo process renovations, introduce new equipment, or add data sources and tags. Mr. Mathur notes that for APC, the solution typically adapts well to process changes; however, when equipment or stages are modified, bump tests and some modeling work are required, which can be managed flexibly by our technical support team.
Regarding security concerns in industrial settings, AFT assures that the online connection between the AFTLinx hardware and the cloud is fully encrypted. Furthermore, there is no direct connection between the cloud and the mill automation system, which significantly reduces security risks by maintaining a separation between the two systems. This strategy safeguards sensitive mill operations while facilitating secure data management in the cloud. BTG adheres to mill-specific security protocols and complies with established mill standards through its open architecture. A critical aspect that requires some initial setup time involves remote access to mill systems by BTG personnel, which Mr. Mathur emphasizes is invaluable for conducting remote work and providing troubleshooting support.
Valmet asserts that its DNAe provides comprehensive cybersecurity measures that extend from the operational field layer to IT-level communication. The various network layers and technical attributes of the system have been designed in accordance with certified Security Development Lifecycle Assurance (SDLA) methodologies, guaranteeing security from the initial line of code. Central to the DNAe is the Trusted Information Framework (TIF), which Valmet claims acts as the fundamental structure for communication and data management. The TIF framework establishes a strong basis for ensuring system security and integrity.
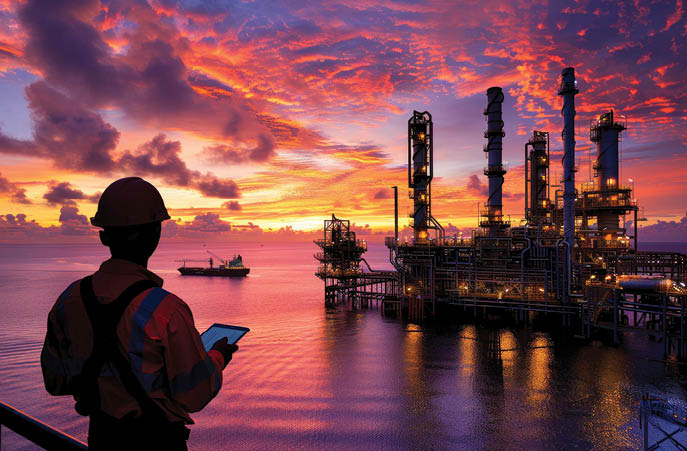
Innovations
The management of large-scale data is increasingly becoming crucial. Mr. Heikkilä states that technology enabling the seamless integration of the AFTLinx service into any type of refiner, irrespective of the manufacturer, as well as into other processing equipment, will soon be available. This advancement will facilitate a more comprehensive analysis of mill operations, supported by AFT experts and cloud technology.
Mr. Mathur indicates that there are plans to introduce several technologies across various sectors in which the company operates. He notes, “For example, leveraging our century-long expertise in consistency measurement within the pulp and paper manufacturing process, and having a complete range of measurement principles in our offerings, we have recently launched our advanced rotary consistency transmitter technology, MEKStratus. Additionally, we have introduced our ControlSuite, which includes enhanced features and benefits, with more innovative technologies set to enter the market soon.”
Significant advancements have been achieved in technology, and the availability of resources has evolved. This evolution necessitates ongoing improvements and modifications to processes, as the factors influencing the industry have changed. The industry has undoubtedly expanded and adapted over the years, with many participants beginning to embrace Industry 4.0, which emphasizes the automation of processes within the paper sector and the facilitation of AI/ML communication and self-monitoring. There is no doubt that this shift holds tremendous potential to revolutionize the entire industry, from the procurement of raw materials to the delivery of the final product to customers. While the industry has been slower to adopt 4IR technologies compared to other sectors like manufacturing or automotive, there is a growing recognition of its potential to revolutionize operations.
Understandably, the mills need to prioritize digital transformation, invest in training and development, collaborate with technology providers, and adopt a phase-wise approach to 4IR implementation. By embracing these technologies, paper mills can certainly improve efficiency, reduce costs, and enhance sustainability, which will also lend more competitive edge.