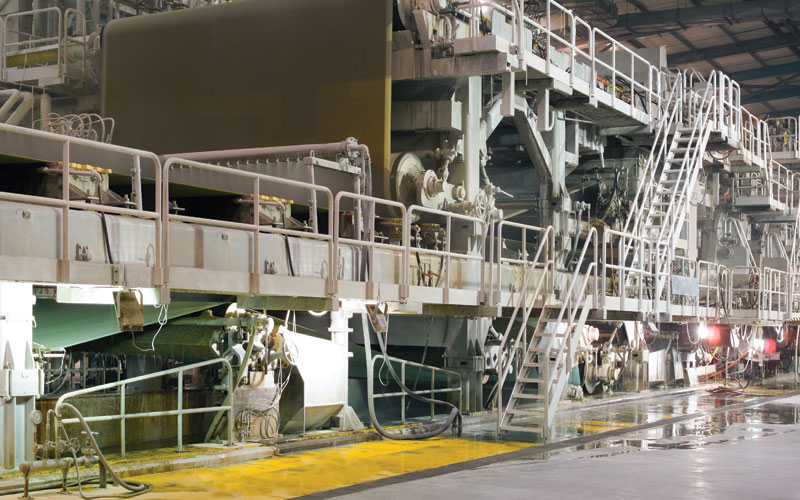
The growth of the Indian pulp and paper industry has resulted in a notable increase in the need for papermaking machinery, fostering an ecosystem primarily led by international machinery manufacturers, while simultaneously providing opportunities for domestic companies to expand. Over the years, numerous homegrown machinery manufacturers have emerged, successfully playing formidable roles in the sector.
India currently boasts an estimated annual paper production exceeding 25 million tonnes, supported by over 800 paper mills. Rising demand for high-quality packaging in sectors such as FMCG, textiles, and pharmaceuticals, along with the growth of e-commerce, growing preference for packaged ready-to-eat meals, and a ban on single-use plastics are driving the growth of the market. As a result, there has been a notable increase in the need for papermaking machinery, fostering an ecosystem primarily led by international machinery manufacturers, while simultaneously providing opportunities for domestic companies to expand.
The papermaking process involves the need for the continuous movement of substantial quantities of materials, making the design and mechanization of materials-handling equipment a crucial element in the advancement of the industry. While the paper machine is often seen as the hallmark of mechanization within the paper sector, it is important to note that every phase of production, from tree harvesting to the delivery of the final product, has experienced a rise in mechanization.
Over the years, numerous homegrown machinery manufacturers have emerged, successfully positioning themselves as dominant players in the sector. During the 1970s and 1980s, the Indian pulp and paper industry anticipated significant technological advancements when Beloit Inc. of the USA, a prominent global technology provider, formed a partnership with the Indian firm Jessop & Co. Ltd. Additionally, the German company Voith GMBH established a 50:50 joint venture with Larson & Toubro, while the Finnish company Valmet collaborated with Mechano Industries Ltd. of Kolkata.
However, Mr. Ashish De, a prominent advisor and consultant in the Indian paper and paperboard industry, notes that these initiatives did not come to fruition at the onset of the new millennium. Consequently, large integrated paper mills in India became reliant on European machinery manufacturers, while smaller and medium-sized mills turned to sourcing outdated machinery and equipment from Europe, the United States, and Japan. This trend led to the emergence of several companies that engaged in reverse engineering, ultimately diversifying into additional areas beyond their primary expertise. Many of these organizations have increased their business volume by providing cost-effective solutions, Mr. De explains.
Entering the Arena
Our journey commenced in 1976 with the establishment of a foundry division dedicated to producing refiner plates for the pulp and paper sector, Mr. Madhure S. Desarda, Director of Parason shares. However, the initial phase was fraught with challenges. Parason faced stiff competition from imported machinery, necessitating the bridging of significant technological gaps and the establishment of a robust presence within the industry.
Currently, the company operates in over 63 countries, with more than 10 manufacturing units and upwards of 5,000 refiners. We are actively involved in over 1,236 research and development projects and have strategically positioned ourselves to provide innovative solutions, emphasizes Mr. Desarda. This commitment is evident in the excellence of our world-class facilities, which are designed to push the boundaries of innovation.
Another notable domestic company is Scan Machineries, which began its journey in 1989 with a small order for the rebuilding of a pope reel, driven by a vision to develop innovative and reliable solutions tailored to the diverse needs of the global paper industry. Mr. Aashish Nargunam, Director of Scan Machineries Private Limited, states that there was a rising demand for high-quality machinery capable of enhancing efficiency, sustainability, and cost-effectiveness in paper mills.
The early challenges included comprehending the varied requirements of different markets. For Scan Machineries, establishing a dependable supply chain and balancing cost with quality were significant obstacles. These challenges were mitigated through continuous learning, formation of strategic partnerships, and a steadfast commitment to superior engineering standards. Mr. Nargunam highlights that their experience enables them to produce customized solutions, catering to the unique needs of their clients worldwide.
A notable journey that traces back to the early 1970s is that of JMC Paper Tech. A business established by Dr. Yesha Patel’s grandfather and his family, initially concentrating on the local market. As time progressed, the company developed a robust reputation for its quality and craftsmanship in supplying machinery for paper production. In 2002, the leadership transitioned to Dr. Patel’s father, Mr. Rajni, who further broadened the company’s scope by founding JMC Paper Tech. Currently, the third-generation Dr. Yesha serves as the CEO of the company. She emphasized that with the implementation of advanced technological solutions, the firm began to compete effectively with global manufacturers and exporters, carving out a niche on the international stage.
The company now has a presence in 25 countries, collaborates with over 200 clients, and has successfully completed more than 225 projects. As a third-generation enterprise, we continue to enhance our legacy by integrating innovation with tradition to address the evolving demands of the industry, the CEO remarks.
Watch: In Pursuit of Lesser Water Footprint
Their Machines, Lifespan and Aftersale
In the process of selecting machinery for our mill, we assess a variety of factors to ensure they align with our operational and sustainability goals, states Mr. Sushil Kumar Khetan (CEO – Operations) of Kuantum Papers. He emphasizes that performance and efficiency are paramount. “It is essential for us to have machines capable of meeting our production requirements while maintaining high output levels. Cost considerations are also significant; we meticulously evaluate both the initial acquisition cost and the long-term operational expenses, including energy consumption and maintenance.”
Furthermore, it is imperative that the machinery produces high-quality paper that consistently adheres to rigorous specifications. He also highlights the importance of advanced features, particularly those that promote automation, minimize waste, support environmental sustainability initiatives, and ensure easy access to spare parts and maintenance services, all while complying with local environmental and safety regulations.
Parason asserts that its machines are built to be durable and dependable, with a typical lifespan exceeding 25 years, capable of processing all types of paper grades, including writing-printing, tissue, kraft, virgin pulp, and recycled pulp. The company claims to provide extensive maintenance services, encompassing both periodic and preventive care, to guarantee optimal performance throughout the equipment’s lifecycle. It also boasts of a strong global support team dedicated to addressing its clients’ after-sales needs. “We are committed to continuously innovating our machinery to meet the specific requirements of our clients,” asserts Mr. Desarda. He further emphasizes that their machinery is both cost-effective and reliable, leading to enhanced performance and an extended operational lifespan. Hydraulic Headbox, Press Section, and Parason Maxi Shoe are the key paper machines it caters.
Similarly, JMC Paper Tech specializes in providing machinery that accommodates a wide variety of paper grades and pulp types. Their advanced equipment is adept at producing high-strength kraft paper, testliner, fluting medium, duplex board, writing and printing paper, as well as sack kraft paper. These products find application in multiple sectors, including packaging, printing, and heavy-duty sacks. The machinery ensures that the output adheres to the highest standards of strength, durability, and print quality, thereby establishing benchmarks within the industry.
According to Dr. Yesha, the lifespan of their equipment ranges from 20 to 30 years. Constructed from materials such as carbon steel cylinders and precision-engineered components, the machines incorporate advanced technology to enhance durability and performance. This design philosophy aims to maximize efficiency and longevity. The company also offers comprehensive maintenance schedules, training programs for client teams, and tailored preventive maintenance services. Their after-sales support includes on-site support, and remote diagnostics for early problem identification, alongside annual maintenance contracts for routine inspections and preventive care, as well as prompt spare parts supply to reduce downtime. Key offerings include the kraft paper machine and duplex board machine for industrial paper production. For writing and printing paper, they provide headbox section, forming section, pressing section, drying section, surface sizing, calendering, top dewatering former, and various accessories.
Mr. Nargunam states that their machines are designed to manage a broad range of paper grades, encompassing printing and writing papers, kraftliners (both coated and uncoated), testliners (both coated and uncoated), and fluting medium. The company also specializes in the production of packaging papers, including corrugated board liners and carton boards. Its advanced machinery is capable of processing a range of specialty paper grades, such as machine-glazed, greaseproof, and flexible packaging papers.
Regarding pulp types, the equipment can handle virgin pulp, recycled fibers, and various other pulp sources, including mechanical, chemical, and semi-chemical pulps. Machines supplied three decades ago continue to operate effectively with regular maintenance. We manufacture machines designed for durability, utilizing high-quality materials and cutting-edge manufacturing techniques that guarantee longevity even in challenging conditions, says Mr. Vinod Nargunam, Executive Director, Scan Machineries. “Our after-sales support encompasses a thorough maintenance program, offering both scheduled and on-demand service visits. We provide spare parts, troubleshooting assistance, and remote support to resolve issues promptly. Our objective is to reduce downtime for our clients and ensure their operations function seamlessly.”
Another key player in the industry is Line O Matic, a prominent manufacturer of paper stationery machinery, paper converting machinery, and packaging machinery, boasting over 50 years of experience and a production facility spanning 3,50,000 sq. ft. in Ahmedabad, Gujarat. Its machinery is primarily tailored for the converting sector, focusing on folio size sheeters and cut size sheeters. The cut size sheeter efficiently transforms paper into various formats, including A4, A3, FS, and legal sizes. In contrast, the folio size sheeter accommodates a broad spectrum of writing and printing papers, as well as different types of boards, such as folding box board (FBB) and duplex board. This adaptability enables us to fulfill the varied requirements of our clients in the paper converting industry, remarks Mr. Uday Patel, Founder of Line O Matic. “To guarantee optimal maintenance and after-sales support for our customers, a dedicated customer service department has been established.”
Line O Matic boasts an annual production capacity that surpasses 300 machines, with production lead times typically varying from 2 to 6 months, contingent upon the specific model and its detailed specifications. The company also offers customization options designed to fulfill the unique requirements of each customer. In a similar vein, Scan Machineries emphasizes providing tailored solutions, and collaborating closely with clients to adapt their machinery to meet specific needs. The lead times for the production and delivery of its new machines and rebuilds generally range from 5 to 12 months, depending, of course, by the project’s scope, complexity, and the degree of customization needed. Meanwhile, operating a production facility in Sanand, Gujarat, covering an area of 15,000 square meters, JMC Paper Tech has the capability to manufacture 5 to 6 complete paper machines each year which include comprehensive setups for paper production, stock preparation, and pulping systems.
What They Say
Guided by the vision of ‘Atmanirbhar Bharat’ and the transformative initiative of ‘Vocal for Local’, Indian manufacturers of pulp and paper equipment have made significant advancements in recent years, propelling the industry forward, states Mr. Khetan. He emphasizes that as India navigates the post-globalization landscape, these manufacturers are crucial to the nation’s quest for self-reliance. Their profound understanding of local market dynamics and resources enables them to create machinery that is tailored to specific requirements, thereby improving efficiency and reducing operational costs.
Mr. Khetan further notes that the proximity of these manufacturers facilitates quicker service and after-sales support, which is essential for maintaining smooth production and minimizing downtime. “In a time when adaptability is paramount, the role of Indian pulp and paper equipment manufacturers transcends mere support; they are pivotal in fostering innovation and ensuring operational resilience. Their contributions enhance our competitiveness on a global scale, positioning our company for enduring success and growth within the industry.”
Recently, Mr. De has observed an increase in the involvement of domestic engineering firms in the development of the Indian paper and board sector. However, he points out that this engagement is primarily concentrated in the realm of paper and board machinery. “There is limited participation in the pulp mill segment,” he notes, citing several factors for this trend. The primary issue is the lack of adequate forestry resources, which discourages investment in integrated pulp and paper mills. Consequently, their involvement is largely restricted to small to medium-sized paper and board machines that utilize recycled fibers or market pulp.
Larger paper and board machines, exceeding 100K TPA, continue to be supplied by international vendors, Mr. De observes. The domestic machinery manufacturers have significantly contributed to increasing business volume, particularly within the low-average quality segments of final products. However, such projects often lack longevity, with many failing to achieve their intended capacity and consistently deliver quality grades, he stresses.
Regarding the equipment utilized by Kuantum Papers, Mr. Khetan states, “We have sourced various process machinery, including paper machine equipment, rewinders, pumps, motors, agitators, and paper cutting and finishing machinery from Indian manufacturers. Furthermore, we have procured advanced pulping equipment such as vertical and continuous digesters, washing systems, and storage tanks locally. Essential utilities, including boilers, turbines, electrical panels, transformers, air compressors, HVAC systems, steam and condensate systems, water treatment plants, effluent treatment plants, and cooling towers, are also sourced domestically, ensuring reliability and prompt service when required.”
While imported machinery may possess specialized features, Indian manufacturers are advancing with new technologies, particularly in automation, which improves both efficiency and sustainability. Overall, Indian machinery presents a cost-effective and flexible solution, reinforcing our dedication to economic growth and environmental sustainability, he asserts.
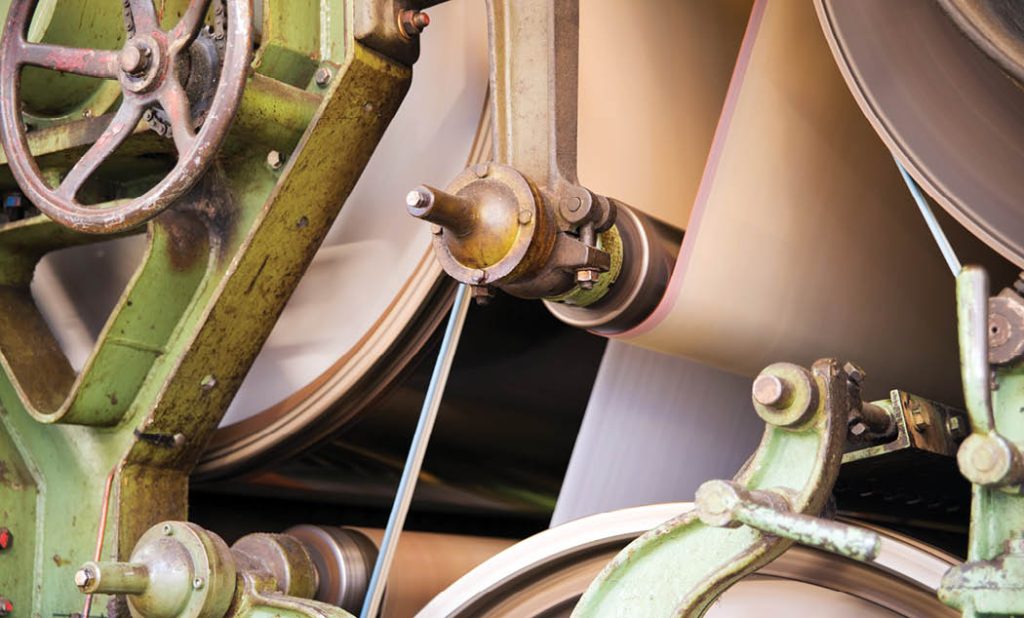
Comparison
Mr. Khetan recognizes the advantages of utilizing Indian machinery, yet he also points out its limitations. “Certain Indian equipment may lack the advanced features and automation that imported machines provide. Although local manufacturers are making progress, their research and development capabilities may not always match those of international brands, which can restrict technological advancements in some instances.” For highly specialized or large-scale operations, his company frequently opts for imported machinery due to its enhanced capabilities. While Indian machinery presents considerable advantages, he emphasizes the importance of thorough evaluation to ensure it aligns with both operational requirements and long-term sustainability objectives.
Mr. De observes that many Indian manufacturers have honed their skills in specific components, including pumps, refiners, drying cylinders, winders, vacuum pumps, and other auxiliaries. However, he underscores a lack of technology-driven solutions for complete projects, particularly for larger paper or board machines. He states, quite candidly, that there is no comparison between the technology offered by global European suppliers and that of domestic vendors, except in a few component areas. He highlights that the overall performance consistency, particularly regarding efficiency and safety features, is often lacking in domestic supplies. “There is consistently a technological gap between what is available from overseas suppliers and what we observe in domestic offerings.”
Challenges
The primary challenge facing Indian machinery manufacturers is achieving a level of quality, performance, and efficiency that allows them to compete with their European counterparts, Mr. De maintains. The domestic market’s business volume, economies of scale, and budget-friendly projects fail to attract sufficient investment in the manufacturing infrastructure necessary for producing highly specialized and advanced machinery, he elaborates.
Mr. Desarda identifies several significant challenges for Parason, including market volatility, inconsistencies in raw material supply, and shifting customer preferences. However, he acknowledges that these challenges compel the company to remain adaptable and proactive, which enables it to effectively address the changing demands of clients and the wider market.
For Line O Matic, Mr. Uday outlines challenges such as disruptions in the global supply chain, increasing raw material costs, the necessity for customization to satisfy varied market requirements, and a shortage of skilled labor. He notes that tackling these issues necessitates ongoing improvement and flexibility within their operations.
Dr. Yesha notes that paper mills have unique needs influenced by their production processes and local conditions, making the management of client expectations and customization requests a frequent obstacle. To address this, his teams collaborate closely with clients from the project’s outset, ensuring the delivery of tailored solutions that meet specific requirements while maintaining high performance standards. Additionally, he highlights the challenge of sourcing high-quality components, which can be affected by global supply chain disruptions. To counter this, the company has established a diverse supplier network and maintains a significant inventory of essential parts, ensuring that projects remain on track.
Sustainability
Sustainability is, it says, central to the operations of Scan Machineries. The company is dedicated to minimizing its environmental impact across manufacturing processes, the equipment it provides, and the paper production activities of its clients. “In our production facilities, we implement energy-efficient practices, reduce waste, and use recyclable materials. Our machinery is engineered to enable paper mills to function more sustainably, incorporating technologies that conserve water and energy, produce eco-friendly and compostable products, lower emissions, and optimize fiber usage without compromising strength characteristics.”
At Line O Matic, sustainability is ‘a core principle that guides its manufacturing practices’. The company operates a 200 KW solar power plant and adopts various strategies to promote sustainability, including enhancing energy efficiency, minimizing waste, recycling, utilizing eco-friendly materials, designing sustainable products, and implementing water conservation techniques.
Likewise, Parason views sustainability as a fundamental approach to fulfilling industry requirements while making a positive contribution to the environment.
Also Read: From Imports to Innovation: How India’s Paper Industry Embraces Self-Sufficiency
Policy Intervention
As India nurtures its indigenous manufacturers, it confronts the formidable challenge of achieving a delicate equilibrium between permitting mills to import crucial machinery and ensuring there sufficient room in the domestic market for the homegrown players. Mr. Uday underlines the need for policies that foster innovation, investment, and sustainable development. “Key initiatives may include incentives for domestic production, the promotion of export opportunities, and support for small and medium enterprises. These strategies would contribute to establishing a more resilient and competitive manufacturing environment in the nation.”
The government ought to allocate resources towards the development of industrial clusters and specialized parks for pulp and paper equipment manufacturers, equipping them with essential infrastructure such as power, water, and transportation, according to Mr. Guru Krishna, Chief Marketing Officer of Abirami Pumps, a prominent industrial pump manufacturer in India. “Additionally, it can promote collaborations between manufacturers and research institutions to facilitate knowledge exchange and innovation, particularly in sustainable technologies and practices.”
Dr. Yesha maintains that tax incentives or grants aimed specifically at the R&D sector could stimulate advancements in energy efficiency and automation, addressing the capital-intensive characteristics of the industry. “Public-private partnerships could further enhance resource sharing, making cutting-edge technologies more attainable for smaller manufacturers.” She underscores the importance of skill development programs to mitigate the shortage of skilled labor in the sector.
The Future
In five years, Parason is poised to maintain its leadership in the industry through advanced innovations, its director says. The company, according to him, will prioritize development of sustainable technologies, enhancement of machine efficiency, and expansion of its global footprint. “Future innovations will be guided by a dedication to inspire, innovate, and implement solutions that address the changing requirements of its clients and the industry at large.”
Scan Machineries aims to solidify its status as a global frontrunner in the pulp and paper machinery domain. The company intends to broaden its market reach, especially in the Americas, Middle East, and Africa, while continuing to push the boundaries of innovation in automation, sustainability, and smart manufacturing. Currently, it is engaged in several pioneering projects that focus on eco-friendly production processes for various paper grades. These advancements are expected to not only lower operational costs for clients but also assist them in meeting the growing demand for sustainable paper production.