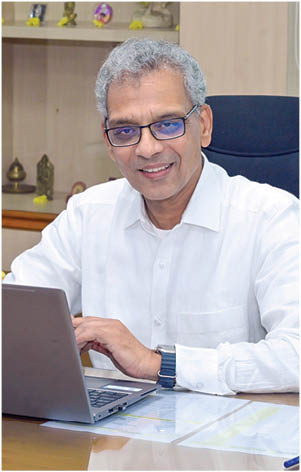
The cornerstone of Tamil Nadu Newsprint and Papers Ltd (TNPL) water efficiency approach lies in the ingenious reuse of freshwater. The company goes above and beyond by implementing robust recycling mechanisms for process water. In essence, TNPL’s water efficiency practices epitomize the synergy between industry and ecology, says Dr. M. Saikumar ( I.A.S), Additional Chief Secretary/ Chairman & Managing Director, Tamil Nadu Newsprint and Papers Limited.
Paper Mart: How do you ensure water efficiency in your operations?
M. Saikumar: At Tamil Nadu Newsprint and Papers Ltd (TNPL), manufacturing writing and printing paper isn’t just about meeting demand; it’s about doing so responsibly, with a keen eye on environmental stewardship. One of the key pillars of this ethos is the relentless pursuit of water efficiency across its operations.
The cornerstone of TNPL’s approach lies in the ingenious reuse of freshwater. Here’s how TNPL achieves it: water consumed for one process operation isn’t simply discarded after use. Instead, it’s meticulously repurposed for other plant operations, effectively closing the loop and minimizing wastage.
The company goes above and beyond by implementing robust recycling mechanisms for process water. This involves a multi-tiered approach:
- Recycle of Untreated Effluent Water: In a pioneering move, TNPL recycles one process effluent water without any treatment, showcasing TNPL’s dedication to maximizing resource utilization while minimizing environmental impact.
- Partial Treatment and Recycle: Recognizing the importance of water quality, TNPL subjects one process effluent water to partial treatment before recycling it. This ensures that the water meets stringent quality standards while still reducing the burden on freshwater sources.
- Full Treatment and Recycle: Taking their commitment towards water stewardship to the next level, TNPL subjects another portion of process effluent water to full treatment before recycling it. This ensures that the recycled water not only meets quality standards but also aligns with the sustainability goals.
- Reuse for Agriculture: TNPL doesn’t stop at internal operations; they extend their water-saving efforts to benefit the wider community. Treated effluent water from the paper-making process finds a new lease of life in agriculture, contributing to the irrigation needs of local farms. This circular approach not only conserves water but also fosters agricultural sustainability.
In essence, TNPL’s water efficiency practices, epitomize the synergy between industry and ecology. By reimagining water usage as a closed-loop system and leveraging innovative recycling and reuse strategies, TNPL sets a precedent for responsible manufacturing in the paper industry.
Rainwater harvesting structures spanning approximately 40,813 square meters adorn the mill area, ensuring that every drop is captured and utilized optimally. But TNPL’s dedication extends beyond the immediate boundaries, with rainwater harvesting structures integrated into the fabric of the surrounding landscape.
Watch: Top Paper Companies 2023
PM: What is your aggregate annual water consumption? What much has that been reduced over the years?
MS: In the fiscal year 2020-21, TNPL’s aggregate annual water consumption stood at 39.3 cubic meters. The specific water consumption per ton of paper production was reported at approx. 42 cubic meters.However, the company’s dedication to sustainability and efficiency has driven remarkable progress in water conservation over the years. By the fiscal year 2023-24, TNPL had achieved a substantial reduction in its water consumption, with the aggregate annual figure shrinking to an average daily consumption of 31.25 cubic meters. This being one of the best in the industry for an integrated pulp and paper mill.
TNPL has significantly slashed its specific water consumption per ton of paper production, from 42 cubic meters in 2020-21 to 26 cubic meters in 2023-24. This represents a remarkable 38.1% reduction in specific water usage per ton of paper produced over the course of four years, underscoring TNPL’s unwavering commitment to sustainability and environmental stewardship.
TNPL’s journey towards water conservation exemplifies the profound impact that conscientious corporate initiatives can have on mitigating environmental challenges. By continually striving for efficiency and sustainability, TNPL sets a precedent for responsible industrial practices, demonstrating that economic growth and environmental stewardship can indeed go hand in hand.
PM: What percentage of water consumed is recycled, and where is the discharged water reused?
MS: One key metric of TNPL’s water stewardship efforts lies in its recycling endeavors. Around 7,000 – 8,000 cubic meters per day (M3/day) of clarified Paper Machine effluent are meticulously treated and recycled from the Effluent Treatment Plant (ETP) to the Pulp Mill – Back Water Clarification Plant for Bagasse Washing System. Additionally, approximately 2,000 – 3,000 m³/day of treated effluent water find purposeful reuse in the pulp mill – bagasse yard for make-up and wet storage of bagasse. Moreover, an impressive 8,000 – 9,000 m³/day of treated effluent water are repurposed mill-wide for various process usage, gardening, and green belt development.
This concerted effort culminates in a commendable 50% – 60% of water recycled after treatment at the ETP, significantly alleviating the strain on freshwater reserves. Notably, TNPL’s commitment extends beyond internal operations; the company actively engages in inter-plant water transfer, further optimizing resource utilization.
However, TNPL’s commitment to water sustainability transcends mere recycling. The discharged treated effluent water finds new life in agricultural endeavors through the TNPL Effluent Water Lift Irrigation Society (TEWLIS). Established in 1987 under the Tamil Nadu Societies Act, TEWLIS epitomizes community empowerment and environmental stewardship. Around 27,000 m3/day of treated effluent water flows into TEWLIS, irrigating arid lands and fostering economic empowerment among farmers in adjacent villages.
PM: What innovative solutions have you introduced in different areas of your mills that have made them more water efficient?
MS: Hardwood and Chemical Bagasse Pulp Mills: In the hardwood pulp mill, TNPL has instituted innovative practices such as returning pump seal water and hydraulic oil cooling water to the Water Treatment Plant, resulting in daily water savings of 300 cubic meters. Furthermore, buffering Wetlap 1 filtrate and paper machine backwater in the Mechanical Bagasse Pulp tower has allowed for reuse, contributing another 1200 cubic meters of water savings per day. Similarly, in the chemical bagasse pulp mill, TNPL has successfully replaced fresh water with filtrates for various processes, resulting in substantial water savings.
Deinking Plant: The Deinking Plant at TNPL has witnessed a revolution in water usage through the strategic reuse of Wetlap filtrates. By reusing Wetlap #3 filtrate within the plant and channeling Wetlap #2 filtrate through designated lines, TNPL has achieved remarkable daily water savings of 1200 cubic meters each.
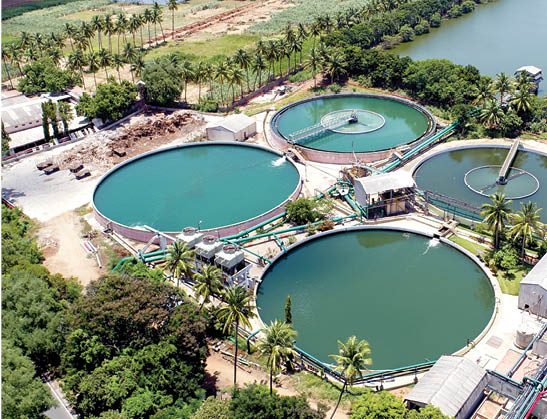
Paper Machine Area: TNPL has strategically installed On-Off valves in the fresh water line at the Deculator vacuum pump seal water pit, preventing overflow in PM#1, thereby saving an impressive 500 cubic meters of water daily. Additionally, the diversion of vacuum pump gear box cooling water in PM#1 to the vacuum pump sewer pit has resulted in further savings of 200 cubic meters per day. Similar innovative measures in PM#2 and PM#3, such as diverting steam and condensate pump sealing water and processing Uhle box water to white water, have collectively contributed to significant water conservation efforts.
Soda Recovery Plant and Power Boiler: By returning pump seal water and vacuum pump seal water from the Alfa#2 evaporator to the Chemical Bagasse Fiber line, TNPL saves an impressive 960 cubic meters of water daily. Moreover, innovative practices such as reusing baby cooling water for pump cooling and diverting blowdown water from the cooling tower to the Water Treatment Plant have further enhanced water efficiency, saving 960 cubic meters and 600 cubic meters of water per day, respectively. Additionally, the utilization of treated effluent water for ash handling has led to a daily water savings of 500 cubic meters.
PM: How seriously do you undertake water harvesting, and how much do you rely on it?
MS: With a meticulous understanding of this crucial resource, TNPL has effectively implemented rainwater harvesting structures both within and beyond the confines of the mill.
Rainwater harvesting structures spanning approximately 40,813 square meters adorn the mill area, ensuring that every drop is captured and utilized optimally. But TNPL’s dedication extends beyond the immediate boundaries, with rainwater harvesting structures integrated into the fabric of the surrounding landscape. In the cement plant, an additional 813 square meters are devoted to harvesting rainwater, amplifying TNPL’s impact on water conservation.
Furthermore, TNPL’s commitment to sustainability echoes through its housing colony, where rainwater harvesting structures covering an expansive 35,107 square meters are in place, catering not only to industrial needs but also fostering sustainable living for its employees.
Yet, TNPL’s vision extends far beyond its immediate operations. The existing balancing reservoirs (1 to 5), spanning an impressive 3,69,500 square meters, serve as a testament to TNPL’s holistic approach to water management. Additionally, man-made rainwater collection ponds (1 to 4), covering 20,300 square meters, stand as reservoirs of hope, capturing and preserving the essence of rain for times of need.
In total, a staggering 4,66,533 lakh square meters of rainwater harvesting structures have been meticulously integrated into TNPL’s operations, underscoring their unwavering commitment to water conservation.
But TNPL’s efforts extend beyond mere infrastructure. The stored rainwater harvested through these structures isn’t just a reserve; it’s a lifeline during times of scarcity. As the flow of river Cauvery dwindles in the scorching heat of summer, TNPL relies on the stored rainwater to sustain its operations, ensuring continuity without burdening the already strained natural resources.
Also Read: JK Paper: Leading the Way in Water Efficiency
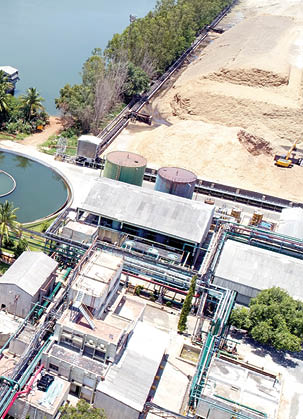
PM: What is your water usage reduction target? How do you plan to achieve it?
MS: As part of its integrated management policy for the fiscal year 2024-25, TNPL has set a target to sustain average fresh water consumption below 30KL per ton of paper production. Achieving this target requires mill-wide implementation of water conservation projects, reflecting TNPL’s commitment to environmental stewardship and resource efficiency.
By adopting the circular economy approach to water conservation, TNPL has made significant strides in reducing specific water consumption over the years. From 47 m3/MT in 2014-15 to 26 m3/MT in 2023-24, TNPL has demonstrated its commitment to resource efficiency and environmental responsibility.
PM: What are the challenges you often face in making your mills water efficient?
MS: Pulp Mill Operations: In the pulp mill, TNPL emphasizes the continuous recycling of EOP water as a cornerstone of water conservation. While this practice significantly reduces water consumption, it also presents a double-edged sword. The relentless recycling leads to the accumulation of heavy-scale deposits in process equipment, increasing the risk of major breakdowns. Moreover, the lack of treatment in the continuous water recycling compromises the quality of the end pulp, undermining TNPL’s commitment to excellence.
Paper Machine Operations: The persistent reuse of water triggers the formation of stubborn scale deposits in process equipment, jeopardizing the quality standards prescribed for the end product. Any deviation from these standards not only tarnishes TNPL’s reputation but also hampers its competitiveness in the market. Maintaining product quality is paramount for TNPL, and any compromise in water efficiency directly impacts this objective.
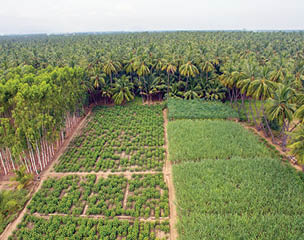
Impact on Social Responsibility: Beyond operational concerns, TNPL acknowledges its social responsibility concerning water usage. Implementing water conservation projects is not merely a business imperative but also a commitment to sustainable development. By reducing the flow of treated effluent outside the mill premises, TNPL endeavors to support local communities, particularly farmers residing in nearby villages. Through initiatives like the “TNPL Effluent Water Lift Irrigation Society” (TEWLIS), TNPL contributes to agricultural sustainability by providing irrigation water sourced from treated effluent. However, any shortfall in supplying treated effluent to TEWLIS could potentially ignite social issues, highlighting the delicate balance between industrial efficiency and societal welfare.