Tamil Nadu Newsprint & Papers Limited (TNPL), with an annual production capacity of 4,40,000 tonnes writing & printing paper and 2,00,000 tonnes of specialized boards, has recently announced a capital expenditure plan worth INR 600-650 crore for FY25 and FY26. In an exclusive interview with Paper Mart, Dr. Sandeep Saxena, IAS, Additional Chief Secretary / Chairman and Managing Director, TNPL, talks about the mill plans to revamp its steam and power system and the installation of a 100 TPD tissue paper manufacturing machine to enter into the tissue paper segment, using the investment.
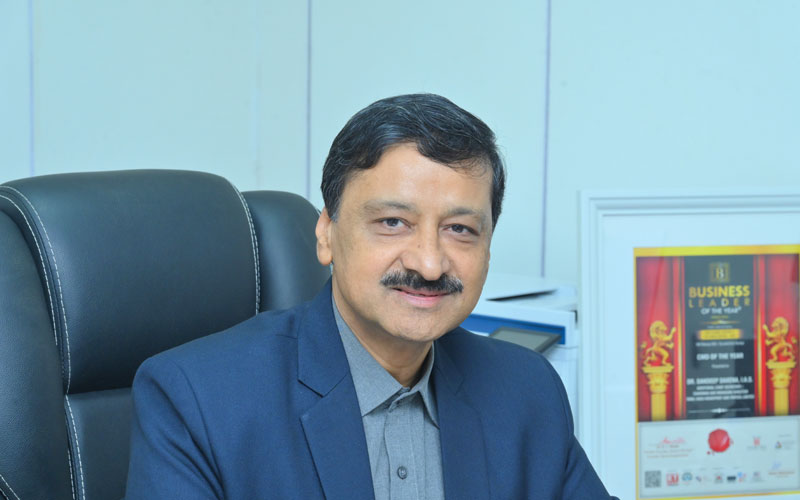
Paper Mart: Kindly walk us through the illustrious journey of Tamil Nadu Newsprint & Papers Limited (TNPL), highlighting major achievements and crucial milestones.
Sandeep Saxena: Tamil Nadu Newsprint & Papers Limited (TNPL), established by the government of Tamil Nadu, has been a trailblazer in the paper manufacturing industry and is recognised globally for its innovative approach and commitment to sustainability.
Founded in 1979, TNPL’s mission was to produce high-quality newsprint and writing paper using bagasse, marking a significant step towards environmentally conscious manufacturing.
Some of the mill’s milestones are:
TNPL commenced its journey in 1984 with an initial production capacity of 90,000 tonnes per annum (TPA), comprising a 70 TPD hardwood pulp mill, a 200 TPD chemical bagasse pulp mill, a 275 TPD BLSD recovery island, and a 26 MW power plant, setting the stage for future growth.
By 1996, TNPL expanded its capacity to 180,000 TPA with the installation of its second paper machine. This expansion included a 100 TPD hardwood pulp mill, a 400 TPD chemical bagasse pulp mill, a 650 TPD BLSD recovery island, and an increased power plant capacity of 36.5 MW.
The year 2000 saw further strides in power generation, with the plant’s capacity increasing to 61 MW. The company’s production capacity was also raised to 2,40,000 TPA with the rebuilding of its original paper machine.
In 2007-08, TNPL launched the Mill Development Plan, which saw the mill’s pulp capacity raised to 300 TPD for hardwood pulp and 500 TPD for chemical bagasse pulp.
The installation of a 1300 TPD BLSD recovery system and a further expansion of the power plant capacity to 81 MW helped strengthen the company’s eco-friendly credentials. Additionally, TNPL switched to elemental chlorine-free bleaching, a significant step in reducing its environmental footprint.
Continuing its expansion, TNPL increased its production capacity to 4,00,000 TPA in 2010, eventually reaching 4,80,000 TPA. The pulp mill capacity was enhanced to 330 TPD hardwood pulp and 550 TPD chemical bagasse pulp. In 2012, the power plant was revamped to provide an impressive 103.62 MW of power, further bolstering TNPL’s green energy initiatives.
In 2014, TNPL ventured into the packaging board sector with the establishment of its Unit-2 in Trichy. This greenfield project involved the construction of a plant capable of producing 2,00,000 MT of packaging board, accompanied by a 30 MW power plant. The commercial production of Unit-2 commenced in 2016, further diversifying the company’s product offerings.
Continuing its growth trajectory, Unit-2 underwent an expansion, which included the installation of a 400 TPD hardwood pulp mill, a 950 BLSD per day recovery boiler, and an increase in power plant capacity to 50 MW.
TNPL’s remarkable journey from a modest paper mill to a global leader in eco-friendly paper manufacturing has been marked by consistent innovation, expansion, and an unwavering commitment to sustainability. As TNPL continues to grow and innovate, it remains at the forefront of the paper industry, setting new standards for environmental responsibility and operational excellence.
Watch: In Pursuit of Lesser Water Footprint
PM: Please tell us about your infrastructure setup and annual manufacturing capacity.
SS: TNPL’s Unit-1 is equipped with advanced infrastructure designed to produce premium writing and printing paper. The annual production capacity at Unit-1 is 4,80,000 tonnes per annum (TPA). The facility is supported by a 330 TPD hardwood pulp mill and a 550 TPD chemical bagasse pulp plant, ensuring a consistent and sustainable supply of raw materials for paper manufacturing.
The facility also features a 1300 TPD BLDS chemical recovery system, which plays a crucial role in minimizing waste and ensuring the efficient recovery of chemicals used in the papermaking process. The 103.63 MW in-house power generation capacity is another highlight of Unit 1, enabling the plant to meet its energy requirements through renewable and sustainable sources and reducing dependence on external power grids.
Furthermore, TNPL has integrated its water and effluent treatment plants within its infrastructure, ensuring responsible water usage and efficient management of effluents, in line with its environmental commitment. Other essential utilities and infrastructure further support the plant’s seamless operations.
TNPL’s Unit-2 is a key player in the company’s diversification strategy. Specializing in packaging board production, the facility has an annual production capacity of 2,00,000 TPA, with a focus on high-quality packaging board products that cater to the growing demand in the packaging industry.
Unit-2 houses a 400 TPD hardwood pulp mill, which ensures a reliable source of pulp for the production of packaging board. The plant is supported by a 950 TPD BLDS chemical recovery system, helping maintain sustainability and optimize the use of resources. Addition of 20 MW increase the in-house power generation capacity to 50 MW ensures that Unit-2 operates efficiently with minimal environmental impact, supported by renewable energy sources.
Just like Unit-1, water and effluent treatment plants are integral to Unit-2’s infrastructure, ensuring compliance with environmental standards while maintaining sustainable water usage.
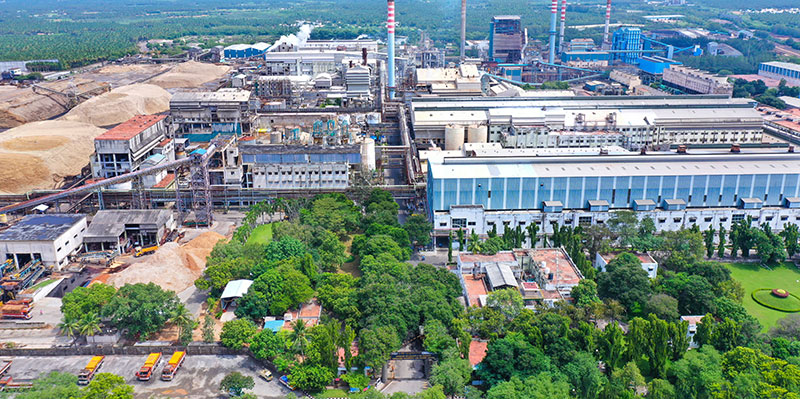
PM: TNPL recently announced capex worth INR 600–650 crore over FY25 and FY26. Kindly tell us about the new growth initiatives, which you plan to achieve with this capex.
SS: TNPL has announced a capital expenditure plan worth INR 600-650 crore for FY25 and FY26. This strategic investment aligns with TNPL’s vision to enhance production capabilities, embrace renewable energy, and ensure uninterrupted operations, further strengthening its position as a leading player in the pulp and paper industry.
Some of the key growth initiatives are:
We have recently installed a pulp mill in Unit II, at Mondipatti, Tamil Nadu. In addition, we are revamping our steam and power system to conform to the latest safety and environmental standards.
We have also decided to install a 34,000 TPA tissue paper machine. This state-of-the-art machine will manufacture the following tissue paper grades: facial tissue paper, toilet tissue paper, towel tissue paper, and napkin tissue paper.
We expect to start production by Feb 2026.
This project will cost INR 340 crore (inclusive of GST), and its scope is the installation of a state-of-the-art tissue paper machine capable of producing high-quality tissue paper in grades ranging from 13 GSM to 40 GSM. The machine will primarily utilize in-house hardwood pulp, ensuring superior product quality. This project will enable TNPL to tap into the growing tissue paper market and diversify its product portfolio.
The second key initiative is the installation of a 2 MW rooftop solar power plant (1 MW each at Unit I & II). The project will cost INR 9 crore (inclusive of GST), and the scope of this solar plant is to reduce carbon emissions and enhance energy efficiency. The project commenced in January 2024 and scheduled for completion in June 2025 The project supports TNPL’s commitment to sustainability and renewable energy adoption.
The third key initiative is the revamping of the steam and power system at TNPL Unit-I. The project cost INR 250 crore (inclusive of GST), and the scope of the project is the installation of a 125 TPH, 104 kg/cm², 525°C AFBC boiler along with a modern fuel handling plant to address bottlenecks and ensure uninterrupted steam and power supply to the mill. The project commenced in June 2024 and is scheduled for completion in April 2026. This upgrade will improve operational efficiency, enhance reliability, and ensure seamless power and steam supply for manufacturing processes.
These initiatives reflect TNPL’s relentless pursuit of environmentally sustainable operations and technological advancements that not only support the mills’ green energy goals but also position the company for future growth, enhancing its capability to meet global standards and customer demands in the competitive pulp and paper market.
PM: How do you maintain a competitive edge in the segment?
SS: TNPL invests heavily in technology and R&D with a regular upgradation and modernisation plan. Our marketing and production team is actively involved in exploring new markets and customers. Our customer centricity gives us loyal, long-term customers. Further, investing in IT and automation keeps our quality up to international standards and improves our efficiency. We are also actively implementing Industry 4.0 to maintain our competitive edge.
PM: Kindly give us an overview of your market footprint.
SS: TNPL manufactures approximately 4,40,000 MT of paper and 2,00,000 MT of packaging board. All the material is sold through our 110 dedicated dealers spread across the country. TNPL also exports approximately 24% of its total production to international markets. We export in 60 countries, including developed countries like the USA, the UK, Italy, the Netherlands, Turkey, etc.
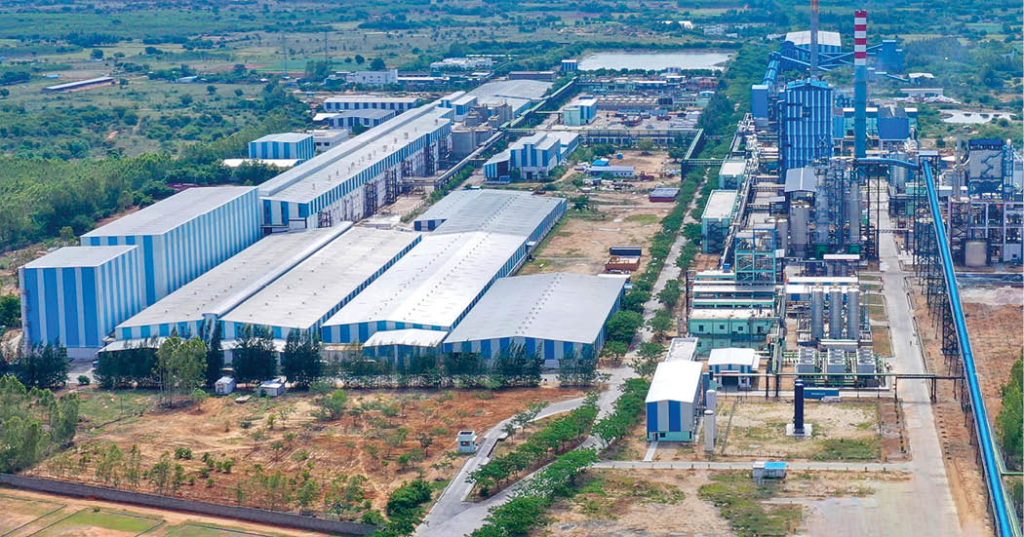
PM: Please elaborate on how R&D plays a critical role in the growth of a company?
SS: At TNPL, innovation and sustainability go hand in hand, driven by a dedicated R&D team that plays a vital role in fostering growth and operational excellence.
Bagasse, a by-product of sugarcane, forms the cornerstone of TNPL’s raw material strategy. By utilizing approximately one million tonnes of bagasse annually, TNPL not only supports sustainable manufacturing but also prevents the exploitation of around 30,000 acres of forest land. This green approach aligns with the company’s mission to preserve the environment and promote sustainable paper production.
The development of TNPL’s GreenPal brand, which champions the use of 100% bagasse-based paper, exemplifies its pioneering efforts in sustainable paper manufacturing.
TNPL’s R&D team continually undertakes innovative projects to improve product quality, process efficiency, and environmental sustainability.
Some of them are:
- Deposit Control and Oxidative Biocide Program: Monochloramine-based oxidized biocide has extended machine running times from 45 to over 70 days by ensuring efficient bacterial control.
- Bulk Enhancer Trials: The introduction of cross-linking polymer bulk enhancers eliminated high-cost BCTMP usage in TCR 70 GSM, leading to savings of INR 250 per tonne of paper.
- Colour Reduction Study: Polymer-based solutions were identified to significantly reduce effluent colour in secondary and primary clarifiers.
- Water Conservation and TDS Reduction: Trials reduced foaming in effluents, lowered TDS levels, and optimized sodium content in secondary clarifiers.
- Sand Content Reduction in Pulp: Chemical trials aimed at reducing sand content and improving moisture content in pith press outputs.
- Hydrogen Peroxide Stabilization: Enhanced stabilization techniques reduced chemical consumption and decomposition in pulp mills.
- Wash Aid Chemical Trials: Foam and alkali loss reduction initiatives led to increased pulp production and maintenance efficiency.
- Innovative Raw Materials: Trials with Senna spectabilis demonstrated its suitability for hardwood pulp production.
- Anti-Scalant Program: Scaling issues in chemical bagasse and hardwood pulp processes were addressed to improve production uptime.
The R&D team also focuses on energy-efficient production processes that lower operational costs and reduce greenhouse gas emissions. One of the standout achievements of TNPL is biogas generation through anaerobic digestion of bagasse leachate water. This renewable energy source supports power generation, reduces fossil fuel dependency, and contributes to the mill’s circular economy initiatives.
TNPL also coordinates with government agencies like the Department of Scientific and Industrial Research (DSIR), Bureau of Indian Standards (BIS), and Central Pulp & Paper Research Institute (CPPRI). The company publishes technical papers in leading national and international journals to share its innovations and advancements with the global community. Through its comprehensive R&D efforts, TNPL continues to lead the way in environmental sustainability, product innovation, and operational efficiency, setting new benchmarks for the paper industry while preserving natural resources for future generations.
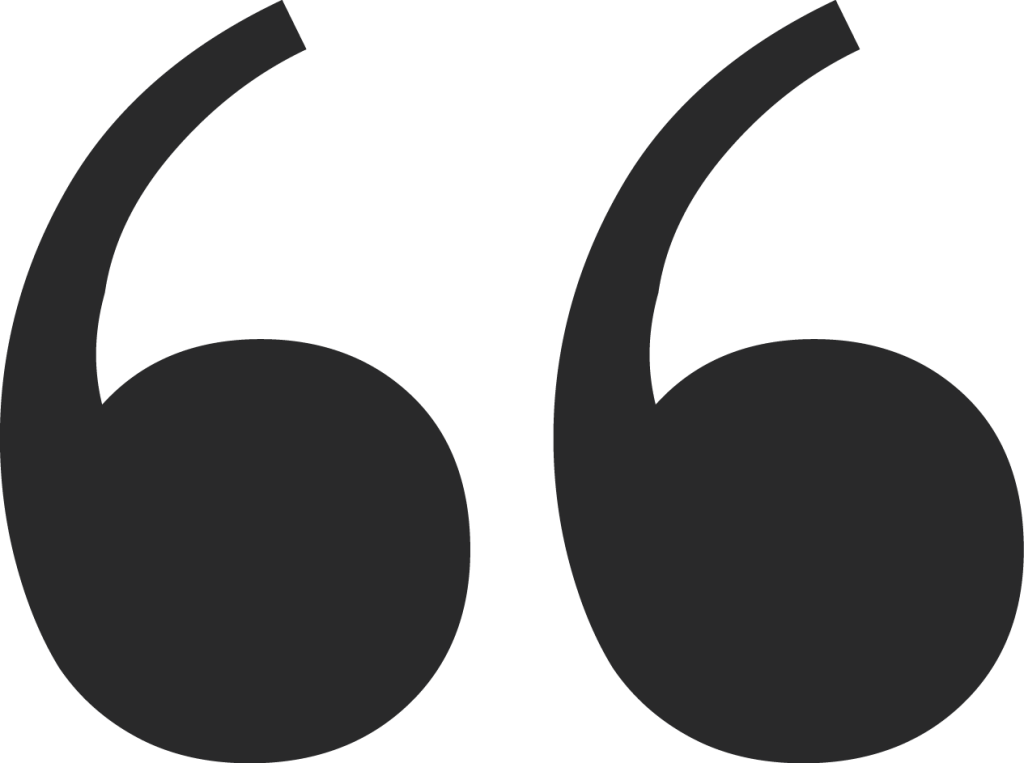
By utilizing approximately one million tonnes of bagasse annually, TNPL supports sustainable manufacturing and prevents the exploitation of around 30,000 acres of forest land.
PM: What are the green initiatives adopted by the mill?
SS: TNPL is renowned as the world’s largest eco-friendly bagasse-based paper mill, emphasizing sustainability and energy efficiency. The company has formed strong ties with sugar mills and established captive plantations to ensure a consistent and sustainable supply of raw materials.
TNPL took its first steps towards green energy in 1993-94 by installing windmills with an initial capacity of 15 MW. By 2007, this capacity expanded to 35.5 MW. TNPL also introduced a bio-methanisation plant, which converted high-COD effluent into biogas, replacing 15 metric tonnes of furnace oil per day.
In 2012, the company became the first in the paper industry to install a lime sludge and fly ash management system, a project aimed at reducing waste and producing 600 TPD of cement from waste materials, which was later increased to 900 TPD.
The company is also committed to reducing its carbon footprint, which is evident in its partnership with OMYA to produce Precipitated Calcium Carbonate (PCC) from CO₂ extracted from flue gases. This PCC is utilized in the paper production process, further reducing the environmental impact of the company’s operations.
TNPL has also implemented a Treated Effluent Water Lift Irrigation Scheme, which irrigates 1,460 acres of dry land through a society formed with 1,200 farmers in TNPL Unit-1. Additionally, drip irrigation has been carried out on 500 acres of land in Unit-2, showcasing TNPL’s dedication to sustainable agricultural practices. These green energy initiatives not only support TNPL’s operations but also contribute to the state’s renewable energy goals.
Also Read: Orient Paper & Industries Infuses Sustainability in Its Product Innovations
PM: Please share your views on the recent trends in the pulp and paper market. How do you see the market evolving over the years?
SS: Paper as a commodity has seen a lot of changes. Paper has moved from being a source of writing/archiving data and communication to a means of sustainable packaging. The writing and printing segment is declining, and there is growth in the tissue and packaging segment. While these changes are more pronounced in the developed world, there is still room for growth in India, Africa, and Asia. The reason for this growth is primarily demographics, as these countries have a large and growing young population who need paper for their education.
With increasing movement towards the environment, there is a lot of focus on eco-friendly, sustainable materials, as they are totally recyclable and biodegradable/compostable in nature. This property of paper has led to many applications for packaging. Today, packaging paper and board constitute more than 60% of the total paper demand.
Although the overall growth in the global paper market is very low, at 1% P.A., due to the overall decline in the writing and printing segment, the packaging segment is on the upward trend. The Indian market is growing at approx. 5% PA. While growth is lower in the writing and printing segment, the packaging grades, like Kraft/paperboard, are growing at a quick pace. With increasing consumerism, we expect this segment to grow even faster. Tissue is another segment that has bright prospects in India.
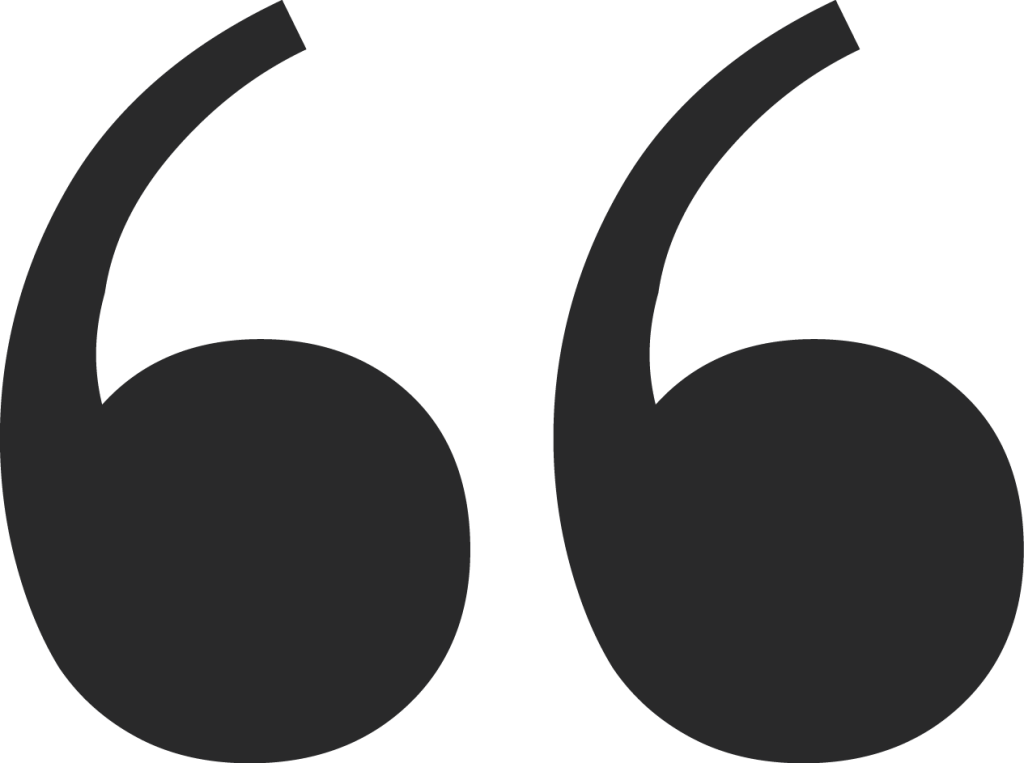
The development of GreenPal brand, which champions the use of 100% bagasse-based paper, exemplifies TNPL’s pioneering efforts in sustainable paper manufacturing.
PM: List some of the major challenges faced by the industry. How can they be overcome?
SS: The paper industry, including companies like TNPL, faces significant challenges that impact its operations and growth. Some of these challenges are rising imports and market competition, raw material availability and cost, environmental regulations and sustainability, and technological advancements and digitization.
The Indian paper industry has seen a substantial increase in paper and paperboard imports, escalating from 1.145 million metric tonnes in 2021-22 to 1.929 million metric tonnes in 2023-24—a 68% surge over two years. Imports from countries like China and ASEAN nations have notably intensified, with increases of 181% and 247%, respectively, during this period. This influx poses a threat to domestic manufacturers, including TNPL, by exerting downward pressure on prices and market share.
Moreover, securing a consistent and cost-effective supply of raw materials is a persistent challenge. Factors such as agricultural dependency, competition for resources, and environmental regulations can disrupt supply chains and escalate costs. For instance, TNPL has experienced significant increases in wood prices, adversely affecting profitability.
Further, the industry is under increasing pressure to adopt sustainable practices and comply with stringent environmental regulations. This necessitates investments in eco-friendly technologies, waste management, and sustainable sourcing, which can be capital-intensive.
Lastly, the rise of digital media has reduced the demand for traditional writing and printing paper. To remain relevant, companies must innovate and diversify their product offerings, which may require substantial research and development efforts.
To navigate these challenges, TNPL and similar companies can consider strategies like developing new products, such as high-strength paper for packaging, that can open new revenue streams and reduce reliance on traditional paper markets. Moreover, investing in sustainable raw material sourcing, like using bagasse can mitigate raw material shortages and appeal to environmentally conscious consumers.
Adopting advanced manufacturing technologies can improve efficiency, reduce costs, and enhance product quality, helping companies stay competitive against imports. Further, exploring new markets domestically and internationally can help offset the impact of increased imports and tap into emerging demand areas.
By implementing these strategies, TNPL can strengthen its position in the market, enhance sustainability, and ensure long-term growth despite the prevailing challenges.
PM: Are you planning to launch any new products in 2025? Where do you see TNPL five years from now?
SS: TNPL has exciting plans for new product launches and expansions. In 2025, the mill is proposing the installation of a 100-tonne-per-day tissue plant at TNPL Unit II, marking its entry into the dynamic tissue products segment.
Looking ahead, in the next five years, TNPL aims to strengthen its position in the paper and pulp industry, focusing on sustainability, innovation, and diversification to stay ahead of the curve.
Some key areas of focus include TNPL plans to introduce new products, such as notebooks, using their paper and boards. The mill is also exploring the potential of paper in various industrial applications, beyond traditional writing and printing papers. TNPL is also committed to environmental stewardship and is working to enhance operational efficiencies, reduce costs, and improve product quality.
With these strategic plans in place, TNPL is poised for continued growth and success in the next five years.