At Vijay Anand’s board mill in India, an upgrade to their traditional rubber covers proved that remarkable performance improvements are possible even with machine consumables.
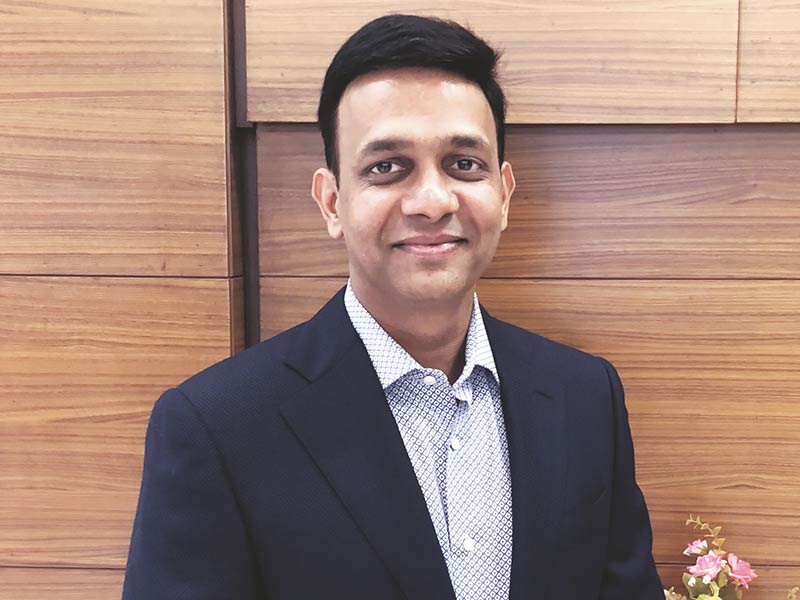
Highly loaded press rolls have a questionable reputation in terms of the reliability of the roll covers and the durability of the bearings. This proved to be true for Vijay Anand with the traditional rubber covers it has been using for several years. In the worst cases, these covers failed in de-bonding, causing unplanned shutdowns and requiring immediate roll changes.
Upgrading for better roll performance
Established in January 2007, Vijay Anand Kraft Papers is the leading manufacturer of packaging paper in India, with a capacity of 66,000 tonnes a year. The mill manufactures test liner and fluting media from recycled waste paper. The mill started to work with Valmet to plan a roll cover upgrade to improve their roll performance. The goal was not only to improve the durability and reliability of the roll covers, but also to boost dewatering by increasing the nip load. After Santosh Tiwari from Valmet and Dharam Agarwal, Managing Director of Vijay Anand, concluded the negotiations and aligned the targets, the press rolls were upgraded with Valmet Press Roll Cover PP premium polyurethane roll covers between 2016 and 2017.
Benefits that speak for themselves
The performance of the roll has significantly improved, and the first set of roll cover changes was enough to demonstrate the power of the latest roll cover technology. The benefits are clear: The rolls can be operated without internal water cooling, which means savings on maintenance and water pumping costs. Thanks to the lower rolling resistance, the energy consumption of the press section is lower, and there is no need for cooling water for the jumbo rolls.
“Now we can run with higher loads and longer grinding intervals. Our target is to achieve a grinding interval of two years,” says Agarwal.
The most remarkable benefit is the increased nip loading. The old covers restricted the nip loading to 200 kN/m, whereas the new Valmet Press Roll Cover PP enables nip loading levels above 350 kN/m. The clearly higher nip loading has also improved dewatering, and web dryness in the press section has increased from 49 to 51 percent.
After the first successful results, Valmet has executed several roll cover upgrades at Vijay Anand; so far, four Valmet Press Roll Cover PPs are in use at the mill.
Payback in less than eight months
The mill had been using traditional rubber covers since the startup of their machine in 2008. The Valmet roll cover upgrade has demonstrated that remarkable performance improvements are possible even with machine consumables. Furthermore, in the bigger picture, choosing a premium-quality product is also the best way to save costs.
Considering only the price of the premium polyurethane covers, it may seem that roll cover upgrade costs are higher with advanced products. But adding the cost savings achieved through increased dryness, energy savings and other improvements reveals that upgrading to premium covers is an excellent investment. Even only considering the savings on reduced steam consumption and the previous roll failure costs, Vijay Anand’s investment paid for itself in less than eight months.