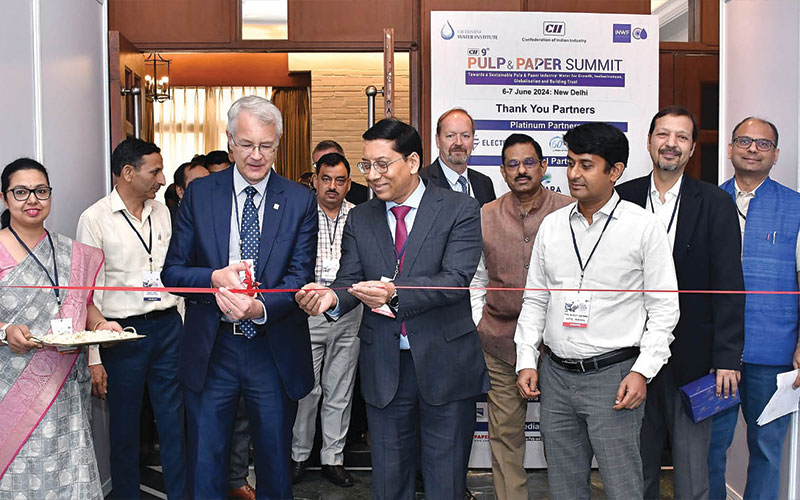
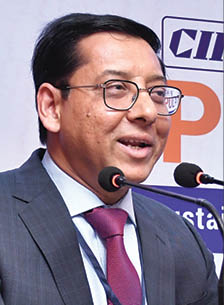
These are exciting times – were the words of Mr. Pawan Agarwal, Chairman – CII Pulp & Paper Summit, President – Indian Papers Manufacturers Association (IPMA) & Managing Director, Naini Papers while delivering his keynote address at the ninth Confederation of Indian Industry (CII) Pulp and Paper Summit aimed at a sustainable pulp and paper industry. The INR 95,000 crore industry is close to INR 1 lakh crore, and it is one of the highest providers of employment in the country, he shared. “Half a million direct families are given employment and more than 1 million indirect employment. No major schemes of the government can be fulfilled or achieved without the contribution of the pulp and paper industry.” He emphasized the need for paper in achieving missions such as the Literacy mission of India and Swachh Bharat Abhiyan, or clean India mission, with the former requiring paper to produce textbooks as well as notebooks and the latter needing compostable paper to mitigate the plastic menace in the country.
Besides the obvious prospects, the Indian pulp and paper industry isn’t free of challenges which are quite prominent in nature. The biggest being the availability of fiber. According to the Managing Director of Naini Paper, the composition of fiber is 71- 72% recycled, 8-9% agro-based and the rest is wood-based. Where do you get this 71-72% raw material from when India’s recovery rate is only 50 percent? Mr. Agarwal, who is also the President of Indian Paper Manufacturers Association (IPMA) asked. The industry is forced to import waste paper, causing a long-term impact on the cost efficiency of the mills. The remedy he suggested is to give a push to the virgin fiber-based industry.
He maintained that the challenge was not restricted to wastepaper and virgin-based fiber. “For agro-based fiber, I can see competition coming from ethanol producers. Whatever is left out from the sugar ribs is going for ethanol production in terms of generating steam and fuel.”
The issue, according to him, stems from lack of access to land. “Despite the fact that 2 million hectares of land has been used by the paper industry to plant trees in the last one and a half decades, the country still has so much barren land available, mostly degraded forests, and unutilized across the country. We have been demanding the government to provide this land to us”, Mr. Agarwal urged. It will give environmental and economic benefits, and will lead to sustainable environment development; the trees will provide the required carbon sequestration and economic benefit, generate additional employment, provide raw material to not only the paper industry, but to all wood-based industries. Moreover, they grow in four years; today there are species which can be harvested in three and a half years.
Why is this crucial and why should the emphasis be increased? Paper is an environmentally sustainable product. Paper, per se, is biodegradable, bio-compostable, and it’s the most recycled product. “In Europe, the percentage of recovered paper is 74-75 percent. In India, it is 50 percent, but it is growing. It’s believed that in the next five years, the target is to touch 65%,” Mr. Agarwal shared. “We are making all concerted efforts, but we have to think of our processes also. We have to adopt technologies, we have to adapt.”
Watch: Top Paper Companies 2023
He recalled the time when electronic mails became a phenomenon, and the slogan- ‘Don’t Print, Save Paper, Save Forest’ – that caused a lingering strong ripple. But that myth has been dispelled, and today paper has been recognized as the most sustainable product, economically as well as environmentally feasible as an alternative to single use plastic. Despite an official ban imposed on single-use plastic, the menace continues to be a big hazard. There lies the opportunity, he pointed out. “Today a lot of companies are innovating to use paper in place of single use plastic. You take FMCG, healthcare, cosmetics and you name a thing which is being packed in single use plastic.” Giants like Unilever, Nestle and Britannia are all working to replace plastic with paper. There lies the opportunity, he said. “If all these companies turn to paper packaging, the country’s production won’t be able to meet the complete requirement.”
These great opportunities also shine light on the challenges the industry faces, particularly its ‘water guzzling’ image or water footprint. Though it has, in this respect, made great strides, it yet can’t rest on laurels. Most mills have succeeded in bringing down the consumption of fresh water from 150 meter cube per ton to even less than 20 meter cube per ton in some cases, and less than 50 meter cube per ton in case of integrated paper mills. This can be attributed to the efficient and result-oriented effluent treatment plants. But there are still big challenges, and they exist since there are bigger opportunities, and Mr. Agarwal was of the opinion that the industry should encash on the opportunities.
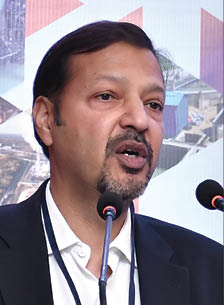
Water is the lifeline of the pulp and paper industry, and the industry, globally, is one of the largest consumers of freshwater. In India, we consume between 15 to 40 cubic meters of water to produce one metric ton of paper, shared Mr. Pavan Khaitan, MD of Kuantum Papers and here, in this vast range, lies the huge opportunity to save and make every drop count.
In this context, the words of Paul Coleman, the former CEO of Unilever, ‘we cannot choose between economic growth and sustainability, we have to have both’ clearly resonate. Water shortages and stresses faced by people in India are becoming endemic, and the industry needs to take a lead in water conservation. “Innovative practices like closed loop water systems are being executed and implemented by a large number of paper mills in India. A lot of technologies like NBR, MBBR, MVR, and many, many more are available. Global organizations are putting their weight behind these technologies and spending in their R&D to ensure that they become successful,” Mr. Khaitan explained. These technologies are going to help conserve water and also contribute to reducing the environmental impact. They are bettering ecosystem health, ensuring improved biodiversity, mitigating impact of climate change which is real and present, enabling economic necessity for both agriculture and industry, ensuring an equitable human health and well-being structure.
“The accessible fresh water available to all of us put together is just 0.5% of the entire water available. So we need to take heed and we need to take effective steps,” Mr. Khaitan maintained. “At Kuantum our efforts towards water reduction are clearly objective and focused. It forms the ethos of all our processes and in the past two years our efforts have helped save 15% water in our process and in the next two years it has taken to double the target to 30%.”
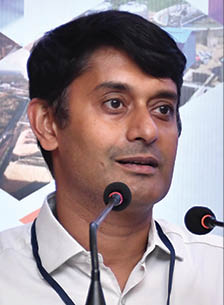
When we talk about policy, a large part of our discourse is about how to make India better, said Mr. Amit Verma, Director, Circular Economy Cell, Economics & Finance Cell, Niti Aayog. “How do we address the challenges of vision of net zero by 2070. It is an industry which nobody can ignore. It is an industry which has to function and which has a strong possibility of becoming a more sustainable industry as compared to plastics.” He went on to elaborate the scale of plastic pollution which paper can solve, and highlighted the environmental impact caused by a company churning out about 13 billion packets of sachets in five years which will neither be collected nor recycled.
While referring to Mr. Agarwal’s plea to allow the industry to have access to the ‘degraded forest lands’, he said, “Not all wastelands are suitable for growing trees, and not all of it is suitable for plantations. I would also like to caution that certain areas do seem like wasteland, but they are themselves an ecological biosphere for certain species which can survive only in those kinds of dry areas. We also need to be cognizant of the fact that there are species like the great Indian buzzard which can only survive in a deserted landscape.”
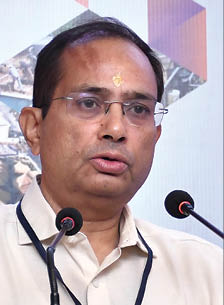
Central Pollution Control Board’s Dr. AK Vidyarthi reminisced about the time, in 2012 when a concerted effort was made and prepared some structured program focusing on water conservation in the pulp and paper industry through technological interventions as well as through adoption of place-limitation practices. “And it was the first time for the paper industry that in 2012 and 2015 we thought about specific fresh water consumption norms focusing on water conservation. In 2012-15, we set a target of about 40-50 cubic metre, broadly for the agro-based, wood-based, bleach grade paper base. Now these mills have achieved about 20 to 30 cubic metre of especially fresh water consumption.”
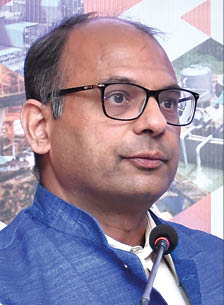
On why the pace of the progress has not lived up to the expectations, Dr. Kapil Kumar Narula, Executive Director of CII-Triveni Water Institute, said, in several forums, our own spending on R&D in India is far less than any other country that we would love to compare ourselves with. “Be it the US, be it many parts of the countries of Europe, I guess this spending has to increase. Our spending is perhaps very less and this needs to be 0.5% of our GDP. But I think the R&D spending really needs to go up to at least within the range of 5 to 8%.”
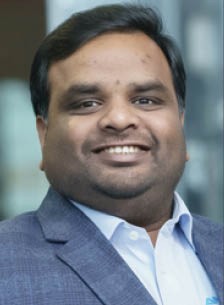
Water utilization has been decreasing quite drastically, and this is significant, says Dr. Naveen Chenna, Director of Research and Innovation, Andritz PULP and Power, Finland. He highlighted technologies such as Ash Leaching and Ash Re-Crystallization actually emerging globally, putting less fresh water and the growing trend of making the zero discharge liquid systems. “If you look at North America customers, they are typically operating between 15 to 45, and 50 cubic metres. Then the South American mills are operating between 15 to 40 cubic metres, the southern European pulp mills are in the 20 cubic metre range, and the northern pulp mills in Finland and Sweden are using less than 20 in good cases, and the worst cases above 50 or 60.”
So the global, Dr Chenna observed, trend has been decreasing, and depending on the geographical location, water utilization is quite different. However, he averred that we will never go to zero effluents, but can always go towards zero effluents. “We are developing a program quite intensely with our customers called the ‘kidney concept’. Most of the pulp mill waters can be recycled, but due to different components, heavy metals, COB, and others, we cannot reutilize them again and again. So we are developing this kidney concept to be placed at different parts.”
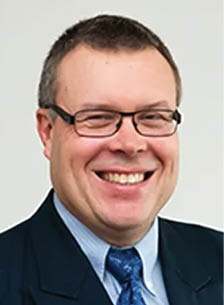
On new ways to aerate water even without extra energy, Mr. Jukka Hakola, COO, Sansox, said, we know that in the world, the quality of water is going down, and the big reason for that is that wastewater treatment plants are not fulfilling what they should do. Maybe the fact that 80% of the wastewater goes untreated in the world into nature, he stressed, and went on to maintain that the pulp and paper industry is doing their share. He brought up OxTube, the company’s modular solution which can be retrofitted, easily removed, cleaned and installed in many stages of the water treatment process. It can be integrated into any water flow system of fresh water processing and waste water treatment, where the OxTube provides systems with the comprehensive oxygenation and aeration. “It’s a pipe-like device, water flows through, it can be either free suction or compressed air that goes into the pipe and it’s dissolved in it. It is fast, it does it really fast and can treat different amounts of water between one to 450 cubic meters per hour,” the Finnish COO stressed.
Another renowned application which found a prominent place at the event was Xylem’s Ozone Bleaching. Its first industrial application started almost 20 years ago, it marks a clear milestone in the development of pulp bleaching methods. Ozone is a 3-atom oxygen molecule produced from oxygen. It has the highest oxidation potential among the bleaching chemicals. It reacts very fast (seconds to minutes) with the pulp and limits the need for large equipment with long reaction time. Ozone, according to Mr. Alexis Metais, Pulp and Paper Account Manager at Xylem, as compared to the other bleaching chemicals, is the true alternative to chlorine in terms of its chemical reactions with the lignin structures. Contrary to chlorine dioxide, ozone does not form coloured byproducts but degrades these compounds. This effect is of interest when ozone is used at the end of the bleaching process to improve the final pulp brightness and to reduce the chemical cost.
Also Read: Valmet Audit Can Reveal Equipment’s Condition for Maintenance Planning
The two-day event inaugurated by the Ambassador of Finland to India, Mr. Kimmo Lahdevirta witnessed several paper companies sharing the remarkable progress they have made, and numerous wastewater treatment technology companies explaining how partnering with them could help mills achieve predefined targets as well as what more could be done.
As water is needed in almost every part of the process in pulp and paper mills, whether the facility is digesting wood chips, making fiber slurries, or washing the machinery and rollers. Mills have been under increasing pressure to adapt their processes and ensure they’re efficient enough to reduce their waste. Today, water scarcity is becoming more endemic. According to the United Nations, on an average, 10 percent of the global population lives in countries with high or critical water stress. However, observing the technological advancements, the concerted efforts initiated at the industry level and the clear regulatory policy is in place, what is evident is that the industry is on the right track or rather close to achieving its targets. It, no doubt, has all the valid reasons to concur with Mr. Agarwal’s ‘These are exciting times’.
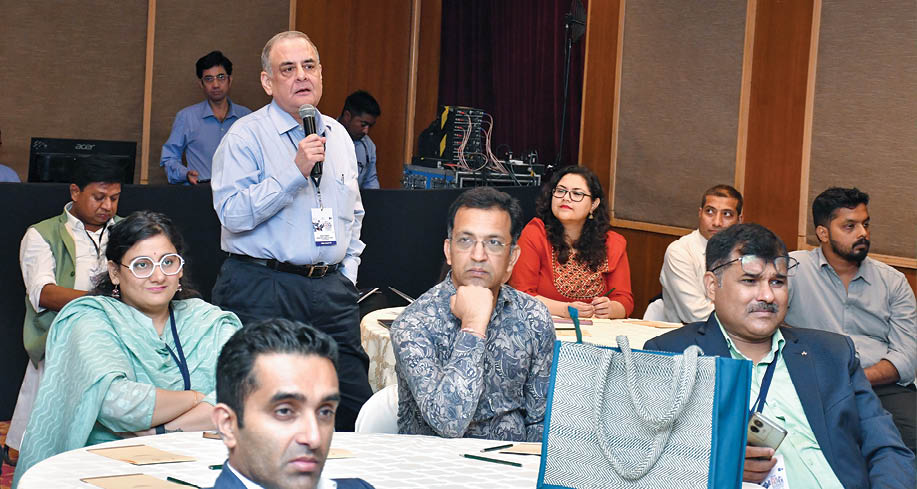