As the global pulp and paper industry braces up for rapid technological advancements, BTG Group, provider of integrated and highly-specialized automation and digital process solutions for the industry, makes the industrial mills future-ready with solutions that drive their costs down, improve quality and increase efficiency. With over 100 years of experience in specialty sensors and analyzers at the foundation level, BTG Group has recently launched rotary consistency transmitter technology MEKStratus and ControlSuite with added features and benefits. More technologies are on the way to the market, Mr. Akhlesh Mathur, Head of Business, South Asia & Southeast Asia, BTG Group, revealed this and much more, during an exclusive interview with Paper Mart.
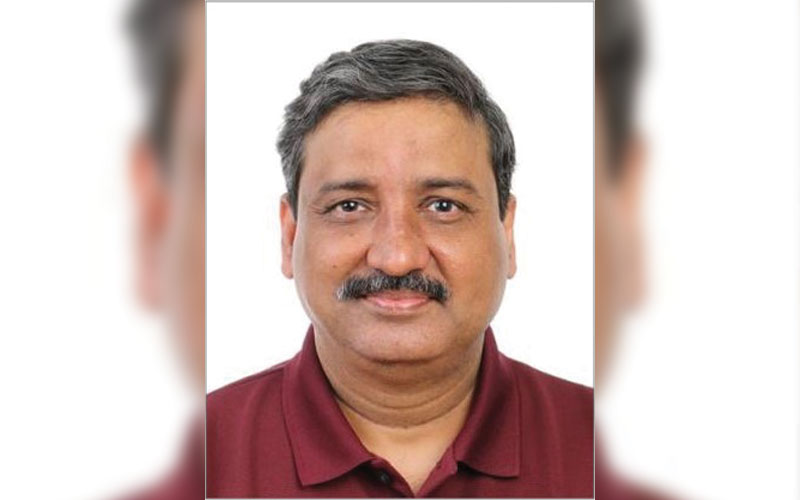
Paper Mart: What specific automation solutions do you cater to paper mills? How do they enhance their operational efficiency?
Akhlesh Mathur: BTG is a niche player focused on automation and digital services to the global pulp & paper industry operating as an “Automation arm” of leading paper machinery manufacturer Voith Paper. With over 100 years of experience in high-end specialty sensors and analyzers at the foundation level in process controls hierarchy, we provide eyes to the process. We have a proven mettle in specialty measurements from pulp mill to paper machine and in most cases, our solutions are considered as industry standards.
At level 2, BTG, through the acquisition of Capstone Technology USA, has been very successful in expanding the installed base of data management tool called dataPARC across the global pulp & paper industry. The tool can connect with various data sources and has been leading the much-required IT/OT integration in our industry. The website of dataPARC provides data-based meaningful insights to various user levels across operations to enable quick decision-making towards improving quality, reducing waste and enhancing operational efficiencies. At the DCS level, BTG also provides value-added tools like ControlSuite and bConnect, making the regulatory control more efficient.
At level 3, we have been extremely successful in implementing advanced process controls in pulp & paper-making processes and have a plethora of established application experiences across various unit operations with documented operational cost savings, improved quality and minimizing shift-to-shift variability. Branded as MACSsuite, we use the proven model predictive controls to overcome the challenges of regulatory DCS level controls in complicated processes and overcome the challenges of operator induced variability. Though early for the paper industry, BTG is running mill-wide optimization projects in various regions with a target to operate mills at lowest possible costs and ability to change gears towards the end-goal of an autonomous mill at the epitome of process controls as level 4.
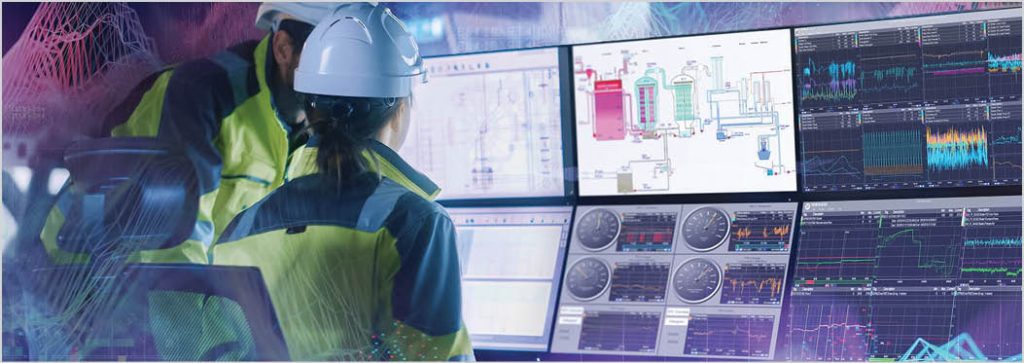
PM: What main features make them unique?
AM: While we maintain a leadership position in various business lines we operate in, what sets us apart from our peers is our incessant desire and drive to provide our customers with solutions that drive their costs down, improve quality and increase efficiency, thereby providing a sustainable economic impact that is measurable. We do this by engaging with our customers focused on their challenges. After system audits and deep interactions with customers, we craft customized solutions using various tools in our toolbox and implement the solutions through our locally empowered teams supported by global SMEs. The passion of our team and the impeccable relationship we share with our customers is indeed a unique point of departure.
PM: How do your technologies integrate with the existing machinery and software systems in the mill? Please elaborate.
AM: In the pulp and paper industry, IT/OT connectivity is crucial for optimizing operations and ensuring seamless data flow between various systems. Using OPC DA (OLE for Process Control Data Access) or OPC UA (Unified Architecture) to connect DCS or Programmable Logic Controllers (PLC) allows for real-time data exchange and interoperability. OPC UA, in particular, offers enhanced security and platform independence, making it ideal for modern industrial environments. When integrating these systems with SQL-based connections to ERP systems, the data from discrete sources can be queried and retrieved efficiently. Other data sources like LIMS or EMS can easily be connected to BTG solutions seamlessly.
OPC DA/UA provides real-time access to process data, significantly reducing latency and improving response times for critical operations. By using standardized communication protocols, we ensure consistent and reliable data transfer between IT and OT systems. SQL-based connections allow for optimized queries, enabling quick access to historical and transactional data stored in ERP systems. Our architecture supports scalability, allowing for the integration of additional data sources and systems without compromising on performance. Middleware solutions are often employed to bridge the gap between legacy systems and modern applications. This allows for smooth data exchange and interoperability without the need for extensive modifications to the existing systems. We utilize protocol converters to enable communication between legacy systems and new technologies. For example, converting older proprietary protocols to OPC DA/UA standards ensures compatibility and real-time data access.
Our global technical teams critically review feedback to identify and address integration gaps, ensuring that our solutions are tailored to each installation. We creatively combine various software tools and emerging technologies to deliver customized solutions. Local experts, supported by global SMEs, play a crucial role in ensuring that our integrated solutions meet the specific needs of individual customers
Watch: In Pursuit of Lesser Water Footprint‘
PM: What support and training do you offer to help mill staff effectively use your solutions?
AM: We believe that developing and implementing a solution is one thing but adopting the solution by customers, maximizing the utilization and sustaining the benefits by the customer’s operations team is a completely different ball game. To this effect, as stated earlier, we involve key stakeholders including shift operators in developing customized solutions, collecting their feedback on how they handle process, exigencies, process control, quality control etc. We then involve the operators, shift engineers and managers during the implementation process in very great detail in developing the solution. From project initiation to hand-over, we spend disproportionate time providing training to different levels in the customer organization to drive adoption. Most of our implementation engineers and project managers have a background in the pulp & paper making process, which helps in talking the same language to drive faster adoption. Sustaining the implemented solutions is a major challenge, often undervalued by our clients. We have flexible business models and on-ground support for our customers to sustain the benefits. There is a lot of scope of improvement in Asia from this perspective.
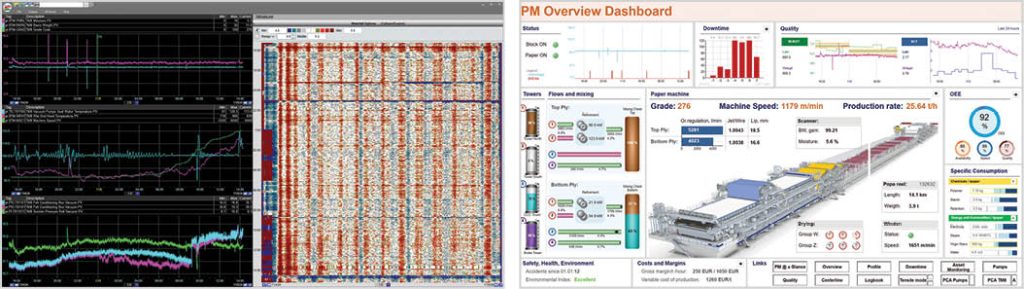
PM: What are the typical ROI and payback periods for your automation systems in paper manufacturing? Please share some case studies.
AM: To drive selling value to our customers, every salesperson in BTG is charged with documenting the economic impact on our clients for the proposed solutions. While we do sell products, our overarching aim is to maximize our solution sales to our customers. Typical ROI for most of our solutions is less than a year, depending on the size of asset (production), challenges and scope.
Most of the mills save anything between USD 2-10 per ton pulp in bleaching cost and brightness variability reduction of 20-50 percent with bleaching optimization. Energy optimization in lime kilns leads to mills saving 5-20 percent energy usage in the majority of cases. Our power pants have helped mills to reduce their power generation costs by USD 1-2 per ton of pulp. We have helped mills increase their paper ash by USD 2-4 per ton of paper. The mill-wide dataPARC implementation leads to reduced chemical and energy costs, and also guarantees payback for one year.
PM: How do you ensure the scalability of your solutions to accommodate future growth or changes in production needs?
AM: Though it is hard to generalize, most of the solutions that we implement in digital space are scalable. In case of dataPARC, sometimes some minor engineering work is required to expand the solution when mills rebuild processes or add equipment, data sources, tags etc. For APC, the solution generally works well with the changes in process but when equipment or stages are altered, bump tests and some modelling work is required, which can be handled by our technical support resources in a flexible manner.
PM: How do you address the security concerns associated with implementing automated systems in industrial environments?
AM: BTG digital solutions have a pretty open architecture (unlike a “black box” approach). We follow mill-specific security policies and adhere with the mill standards. The critical piece that consumes some initial setup hours is with remote access to mill systems by BTG resources, which is extremely helpful in doing a lot of remote work and troubleshooting assistance,
PM: What measures do you take to ensure the reliability and uptime of your automated solutions?
AM: System uptime and utilization of KPI’s are tracked automatically and included in the daily, weekly and monthly reports auto-generated by BTG systems. These statistics are a focus area during regular review meetings with our clients in the project stage. They are also under the microscope in the sustainability phase. When the usage or reliability drops, it is flagged for joint review and actions mandated to correct.
Also Read: Toscotec Launches a New Generation Design of TT Brain DCS
PM: Please explain how your systems contribute to sustainability operations of mills in reducing waste or improving energy efficiency?
AM: Since the past few years, BTG has started to track the carbon impact on solutions delivered to our customers. As one of the KPIs, we include carbon savings in our daily reports. For instance, in bleaching optimization projects, in most cases, we have recorded documented carbon footprint reduction of 3-5 kg per ton of pulp. This is highly valued by our industry, given the spotlight on ESG initiatives across the pulp and paper industry globally.
PM: Please provide case studies of successful implementations in paper mills.
AM: BTG’s dataPARC solutions have a significant global presence, with installations at over 1,000 mill sites, including more than 300 specifically in the pulp and paper industries. In India, BTG is currently managing two major dataPARC projects, alongside other enterprise-wide license users of dataPARC. Additionally, BTG has implemented Advanced Process Control (APC) solutions in 300 unit operations globally, covering pulp mills, paper and tissue machines. Out of these, eight projects are in India.
In Stora Enso, Ingerois Mill implemented BTG’s dataPARC solution to enhance operational performance. The system supports variability reduction through Statistical Process Control and Centerlining, and includes dashboards for visualizing KPIs, monitoring energy consumption, and advanced troubleshooting. Palm Group selected BTG’s Digital Solutions to support operations excellence across their five paper mill sites. The software spans all unit operations, including recycled paper and board machines, de-ink plants, stock preparation, effluent treatment, wastepaper separation, and CHP plants. By using BTG tools, Catalyst Paper USA was able to shift from a reactive to a proactive approach in their operations, significantly improving their process efficiency.
These examples highlight the versatility and effectiveness of BTG’s dataPARC & MACS solutions in optimizing operations and achieving significant performance improvements in the pulp and paper industry. For any sort of case studies and references, we provide information on a case-by-case basis.
PM: What innovations or trends do you see shaping the future of automation in the industry? What new innovations are you planning to launch?
AM: Pulp and paper mills are becoming bigger, complex and efficient, which require automation systems to help increase reliability, improve efficiency and reduce costs. At the same time, the resources are becoming very scarce and exponentially expensive. This is indeed challenging as the efforts to return ratio is demanding. BTG continues to work with our customers, our parent company Voith, our industry peers and co-suppliers to make things easier for the mill operations team using our tools and solutions while continuously looking for ways to upgrade our technology, expand our offerings, become more relevant and add value to our partnership with the industry.
We have plans to launch quite a few technologies in different spaces that we operate in. For instance, utilizing our 100 years of experience in consistency measurement in pulp and paper making process and having all measurement principles in our portfolio, we recently launched our leading rotary consistency transmitter technology MEKStratus. We have also launched our ControlSuite with added features and benefits. Some more technologies are on the way to the market.