Tamil Nadu Newsprint and Papers Limited, India’s first bagasse-based paper mill having annual production capacity of 6,00,000 TPA, is looking forward to taking this figure to 1 million TPA by 2030. The company has incorporated a number of environment-friendly initiatives, such as establishing a factory for the conversion of paper mill wastes into high-grade cement and making ingenious reuse of freshwater. The company shares with Paper Mart, “Being the torch-bearers of sustainability and circular economy, we strive to make sure that almost no waste from any process is disposed of without making sure that it cannot be used for any other operation.”
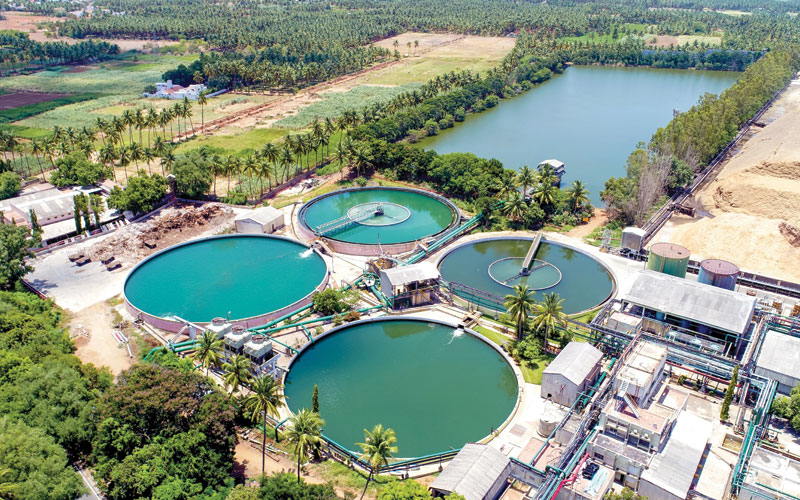
Tamil Nadu Newsprint and Papers Limited is a responsible organization, committed to environmental goals through strategies like resource conservation, recycling, ecosystem restoration, biodiversity preservation, and awareness initiatives.
Sustainable Sourcing of Raw Materials
Tamil Nadu Newsprint and Papers Limited (TNPL) was built on the concept of protecting the environment for both present and future generations. We have perfected the technology of manufacturing writing and printing paper from bagasse, an agricultural residue obtained from sugarcane. Our certifications, including ISO 9001, ISO 14001, ISO 50001 and ISO 45001, highlight our commitment to excellence and environmental responsibility. By implementing various advanced technologies, mill operations and also with maximum recycling, TNPL has become one of the most environmentally benign mills in the country with the lowest specific water consumption. We are also exploring the possibility of moving towards Zero Liquid Discharge, by adopting modern technologies.
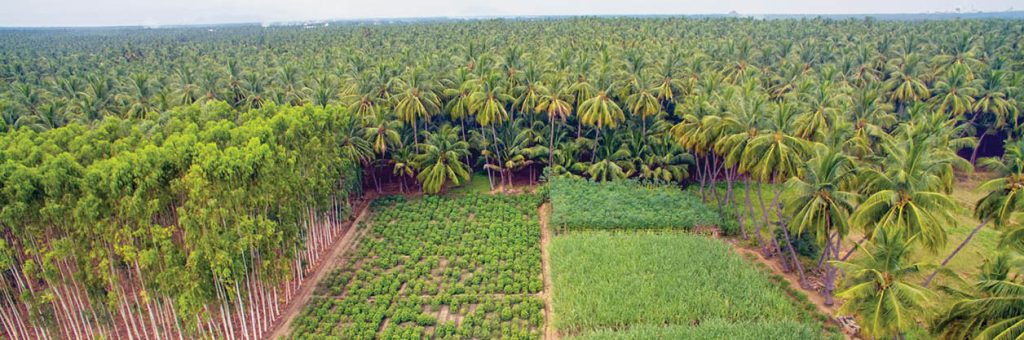
Environment-Friendly Manufacturing Technologies
At TNPL, manufacturing writing and printing paper isn’t just about meeting demand; it’s about doing so responsibly, with a keen eye on environmental stewardship. The company employs an eco-friendly process where bagasse wash water is treated in a bio-methanation plant to produce biogas. This biogas replaces furnace oil in the lime kiln of the paper mill. This is the first registered Clean Development Project from the pulp and paper industry, which reduces approximately 45,000 MT of CO2 annually. We also convert wood dust into biofuel, which is utilized in the paper mill’s boiler as an energy-efficient and safe alternative to fossil fuels.
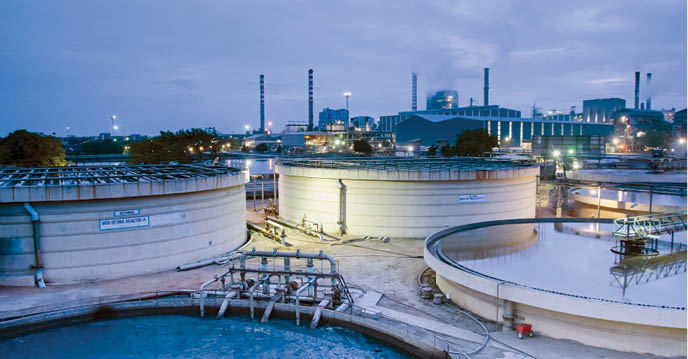
Circular Economy
Being the torch-bearers of sustainability and circular economy, we strive to make sure that almost no waste from any process is disposed of without making sure that they cannot be used for any other operation. We are firm believers that waste from one process could be the fuel to another. So, we optimize and utilize all the waste generated from our paper, paperboard and cement plants and ensure that it is repurposed at all levels. We are a responsible organization committed to preserving our ecosystem and reducing our carbon footprint. We have ventured into generation of green energy through renewable energy resources and have installed 35.4 MW wind farms at Devarkulam and Perungudi in Thirunelveli district of Tamil Nadu. To utilize the unused lands available between the erected wind electric generators in Devarkulam, our plantation department has taken up planting eucalyptus in about 275 acres of land. About 2,300 tons of EH pulpwood has been transported to Unit I in Kagithapuram from the captive plantation so far. Considering the growing demand for paper and paperboards, TNPL has implemented backward integration to meet the raw material requirement by enhancing the farm forestry and captive plantations in the farm lands. The company has supported 45,738 farmers to raise pulpwood plantations to an extent of 2,33,774 acres in the last 19 years.
Watch: In Pursuit of Lesser Water Footprint
Waste to Cement
TNPL is the only company in the Indian pulp and paper industry to establish a cement factory for the conversion of mill wastes, such as lime sludge, fly ash, lime grit, bed ash rejects into superior-grade cement. The initiative formed part of the company’s solid waste management system. In the year 2023-24, TNPL produced 2,00,155 MT of cement. The cement kiln flue gas is also used as an input for manufacturing of precipitated calcium carbonate (PCC) in an on-site plant. Wastes generated in the process, such as lime sludge and lime grit, are used as raw material in the lime kiln of TNPL and its cement plant, respectively.
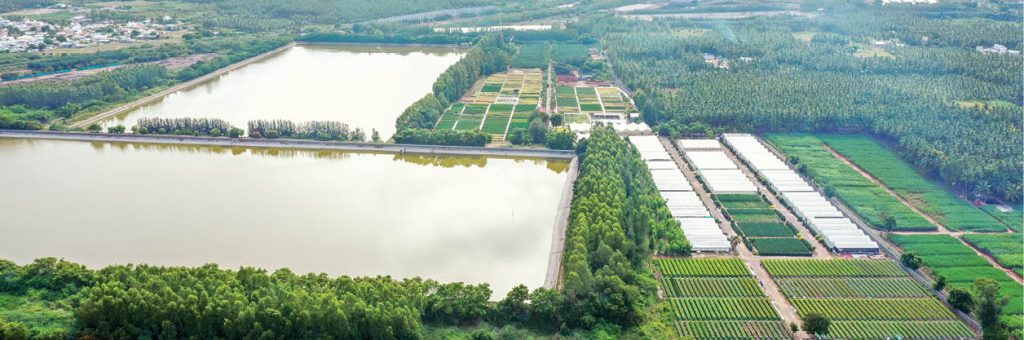
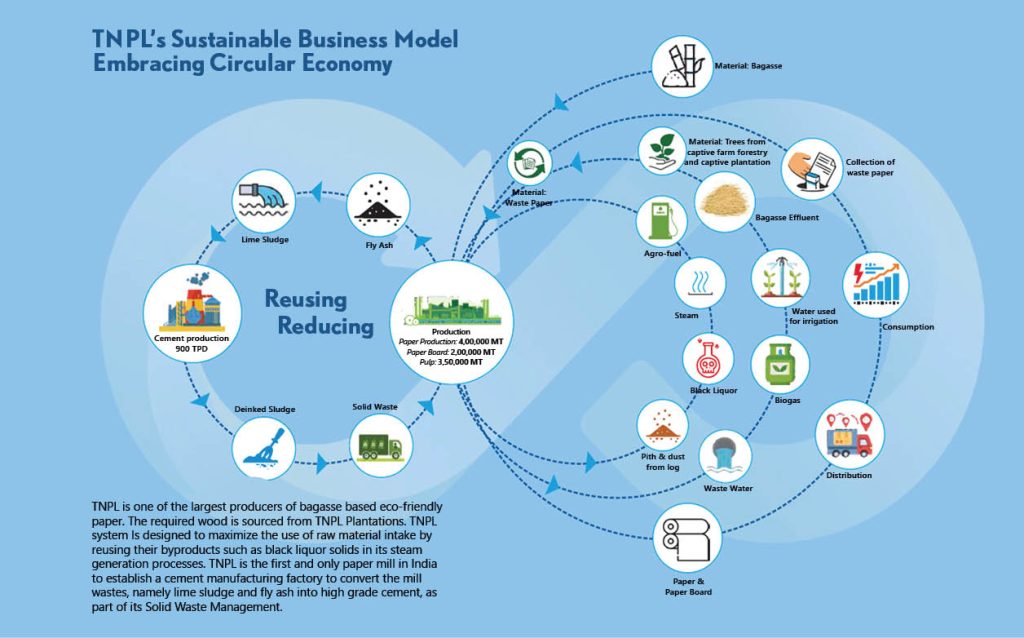
Water Efficiency
The cornerstone of TNPL’s approach lies in the ingenious reuse of freshwater. Water consumed for one process operation isn’t simply discarded after use. Instead, it’s meticulously repurposed for other plant operations. TNPL recycles one process effluent water without any treatment. Next, the company subject’s one portion of process effluent water to partial treatment before recycling it. This ensures that the water meets stringent quality standards while still reducing the burden on freshwater sources. Another portion of the process effluent water is subjected to full treatment before recycling, ensuring that the recycled water not only meets quality standards, but also aligns with the sustainability goals. The company doesn’t stop at internal operations, but extends its circular approach to benefit the wider community. Treated effluent water from the paper-making process contributes to the irrigation needs of local farms, fostering agricultural sustainability. By reimagining water usage as a closed-loop system and leveraging innovative recycling and reuse strategies, TNPL sets a precedent for responsible manufacturing in the paper industry. Besides, the company has integrated 4,66,533 lakh square meters of rainwater harvesting structures into its operations, underscoring an unwavering commitment to water conservation.
Also Read: Trident Group: Bringing ‘The Good Paper’ to the World
Ecological Management and Biodiversity Preservation
Biological diversity encompasses all life on Earth, including plants, animals, and microorganisms. TNPL is striving to lead the industry in biodiversity through innovative plantation efforts. Our Unit-II in Mondipatti has developed a green belt over 650 acres, with 6.84 lakh trees covering 74 percent of the area. This area supports 162 tree species, 68 shrub species, 169 herb species and 95 bird species, among others. It II is also home to 34 grey slender loris, a primate listed as ‘near threatened’ species by the IUCN.
We have established a biodiversity park around Unit-I in Kagithapuram, comprising over 170 tree species across 6.07 hectares. The park attracts a good number of butterflies, birds, reptiles and animals, while also enhancing pollination and local microclimate.
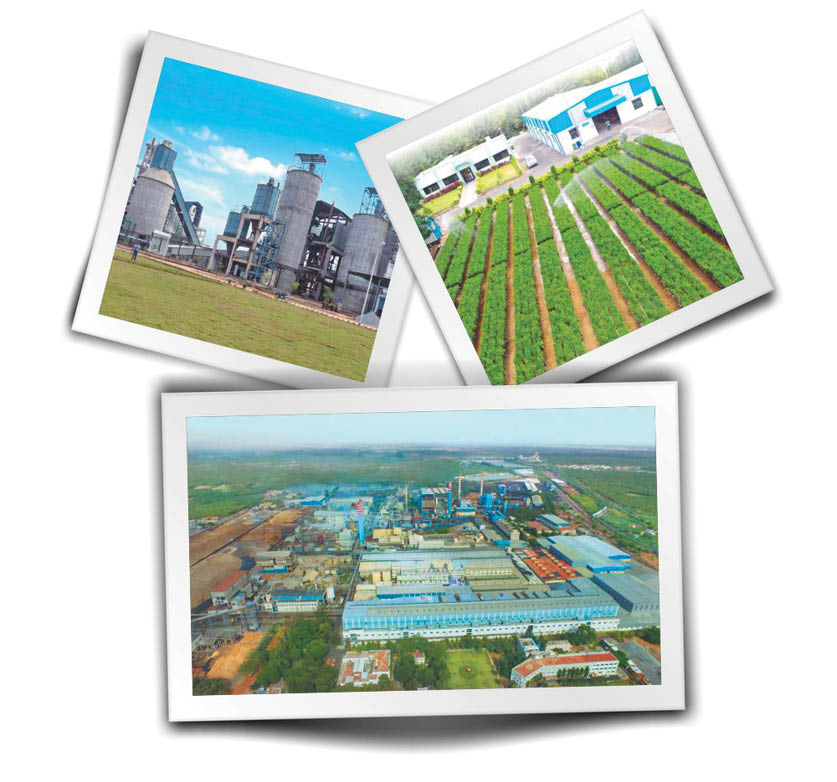
Value from Waste
The organic waste generated from the process of pulp mill is effectively utilized as a fuel to generate wealth from waste. Total 1,53,309 MT of internally generated organic waste such as bagasse pith, wood dust and pulpwood bark resulted in conservation of 50,251 MT of imported coal. About 3,78,592 MT of black liquor solids generated during 2023-24 was fired in a chemical recovery boiler to produce power and high pressure steam. This has further reduced the consumption of 2,18,959 MT of imported coal.
The state-of-the-art bio-methanation plant in Unit I of TNPL has generated 83,05,983 m3 of biogas during 2023-24, out of which 74,40,402 m3 is utilized in SRP and 3,96,039 m3 in power boiler. This has resulted in reduction of 4464.24KL furnace oil consumption in SRP-lime kiln and 707 MT imported coal in power boilers. E-waste amounting to 3.06 MT was disposed of to authorized recyclers by TNPL (for Unit I & II), for 2023-24. About 1000.125 MT of plastic waste was recycled by TNPL (for Unit I & II) as a brand owner, through a waste management agency, towards achieving extended procedure responsibility (EPR) target, of the plastic waste management rules (PWM) 2016 in FY2023-24.
TNPL aims to manufacture paper and paperboards of top-notch quality and achieve over 1 million TPA by the end of 2030. We plan to become the numero uno choice for our customers, providing them with high-quality products at the most affordable and competitive price, while creating a culture of safety & sustainability.
Source: TNPL’s Annual Report