Mills across India have taken conscious measures to promote and adhere to sustainability. From sourcing of pulp for the paper production to the entire chain of manufacturing paper and paper products, mill owners across the country and around the globe are looking for methods, techniques and technologies to make their operations sustainable. During a CII conference, Mr. Pawan Agarwal, Managing Director of Naini Papers, emphasized on the need of environmentally sustainable operations that is the need of the hour for the pulp and paper industry. He said, ‘‘We all know that paper is the most sustainable product. But we need to think of our processes also. We have to adopt and adapt technologies that make our process environmentally friendly and these processes are available. We have taken technologies from Europe and Asia and have adapted them to suit our requirement, scale of operations and economy of scale. We have to reduce our footprints in terms of water and energy consumption, and we have done some tremendous work in the past couple of decades.’’
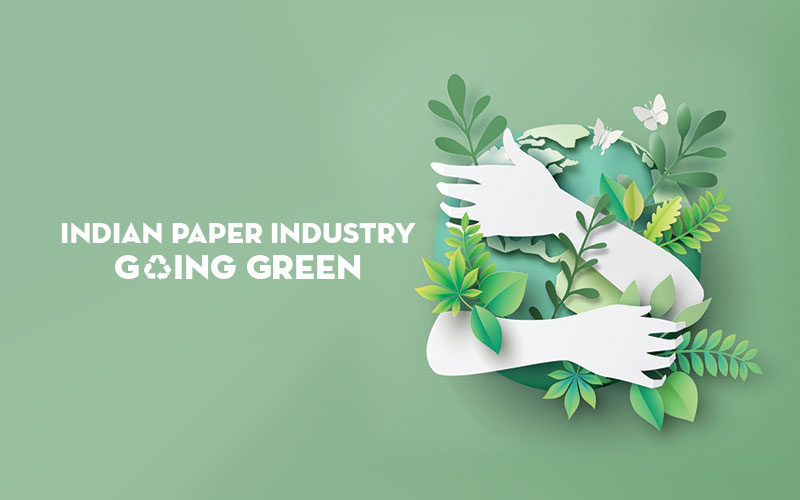
Dispelling the Myths of Paper
Paper is one of the most environmentally sustainable products on the Earth; It is biodegradable, bio-compostable, and one of the most recycled products of the planet. Yet, the paper products and paper industry, in general, is surrounded by myths.
One such myth is that the paper is harmful for the environment as it cuts down trees and forests and thus affects the overall balance of the ecosystem. The disbelief is not just limited to this false information but has also led to campaigns such as ‘Save Paper, Save Forest’ to create chaos and disbelief for paper products. Another myth that created disruptions for the paper manufacturers is that the commercial and exotic plantations will take over the indigenous species and compromise the biodiversity. Apart from that, the rise of digitalisation in the country added fuel to fire suggesting that the electronic media will soon overcome the need for paper and in the coming times, paper will be completely lost to civilization as the world will become paperless.
But over the period of time, people across the world realized the importance and the sustainable characteristics of the paper as there was a huge dump of single-use plastic that was not only difficult to decompose but also released hazardous elements to the environment. So, brands and businesses across the world took a U-turn and realized that paper is not only a sustainable product but also a product that can be easily recycled or decomposed without causing much harm to the environment.
According to Mr. Pawan Agarwal, paper is an economically viable and environmentally feasible alternative to single use plastic. Many industries are looking for opportunities to replace single use plastic with paper such as the food and beverage industry, cosmetic industry, e-commerce, packaging industry and many more, thus leading to the booming potential of the sector. The myth of ‘Save Paper, Save Forest’ has been dispelled over time and it has been duly recognized that paper has been the most sustainable product.
Watch: In Pursuit of Lesser Water Footprint
Paper Industry: A Sustainable Model
Over 70 percent of fiber in the Indian paper industry is obtained from recycled pulp, whereas virgin pulp constitutes 28 percent of the pulp obtained to make paper. Recycling is a key component for the paper industry creating an economically viable and sustainable model for circular economy.
As per Mr Lalit Garg, Chairman, MRAI (Material Recycling Association of India) Paper Committee, India’s paper recycling industry is playing an important role to build India’s circular economy as a sustainable model. The paper recycling industry has the advantage of being pioneers in promoting the concept of a circular economy. We can’t succeed unless we make the circular economy a success.
The paper industry uses renewable raw materials to produce a recyclable product. Most of the paper mills in India have green certifications such as ISO 14001:2015, FSC COC, and FSC Controlled Wood, etc. showcasing how the industry is inherently sustainable without causing any damage to the environment.
There are many mills like ITC PSPD that are not only bringing sustainable models of the paper industry to the table but taking it to the next level with Sustainability 2.0, an agenda that reimagines sustainability and calls for inclusive strategies that support sustainable livelihoods, pursue newer ways to fight environmental degradation and water scarcity, enabling the transition to a net-zero and circular economy.
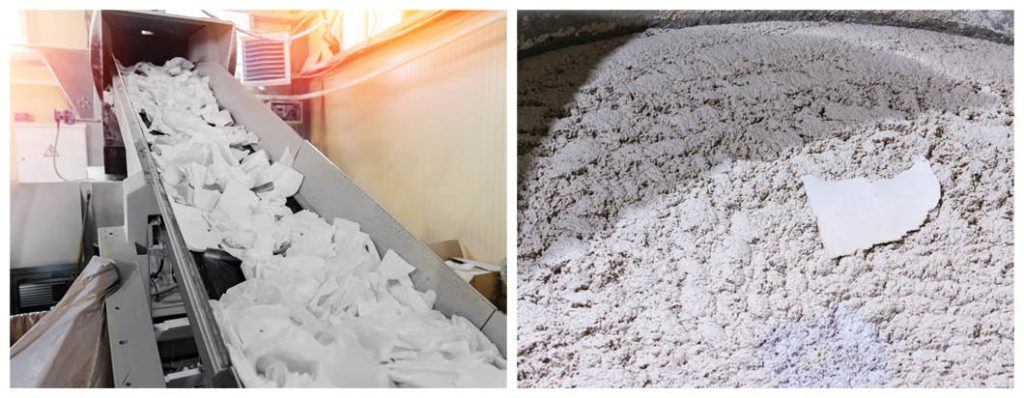
Responsible Sourcing of Pulp
For the production of paper, the sourcing of pulp plays a crucial role. Mills all over the world are embracing different ways to source the highest quality of pulp for paper production.
In order to source a consistent and higher grade virgin pulp, many paper mills across India have been practicing agro farm forestry or social farm forestry. For instance, ITC’s Paperboards & Specialty Papers Division (ITC PSPD) practices a social and farm forestry program to promote sustainable forest management practices in the value chain and secure the supply of pulpwood for its paper mills. Apart from sequestering carbon, this programme provides significant environmental benefits, such as improving the productivity of the wasteland. ITC provides high-yielding clonal saplings to farmers, along with technical support and extension services for tree farming. This helps alleviate risks for farmers by providing alternate tree-based revenue. This extensive afforestation programme has created a green cover of over 1.1 million acres, supporting over 212 million person-days of employment for farmers while creating a sustainable and competitive fibre chain for ITC PSPD.
Another interesting sourcing technique that is gaining traction is clonal forestry. Under this, paper mills invest in state-of-the-art clonal production centers. For instance, JK Paper, through research and development initiatives, has developed short-rotation clones of subabul and eucalyptus, with a duration of not more than three years, allowing farmers to generate higher annual revenues.This clonal approach has helped in ecological restoration, as well as adaptability growth and productivity at degraded sites. Furthermore, this technique aided JK Paper in overall reduction in the resources used for irrigation such as soil, water, electricity and many others.
West Coast Paper Mills adopts the clonal technology for their tree improvement strategy, and aims to increase the effectiveness of the land.
Apart from sourcing the pulp from coniferous trees, mills are also producing pulp using wheat straw, wild grass, bagasse, and rice husk as they are sustainable and beneficial to the local farming community. Such sourcing also prevents stubble burning contributing to the poor AQIs of the region. Seshasayee Paper and Boards sources bagasse from its associate company, Ponni Sugars (Erode) Limited. The Erode unit of the mill obtains about 10% of the pulp from bagasse, which is a by-product of the sugar industry. Kuantum Papers too uses agro-residue such as wheat straw, wild grass, bagasse, and rice husk, to produce papers.
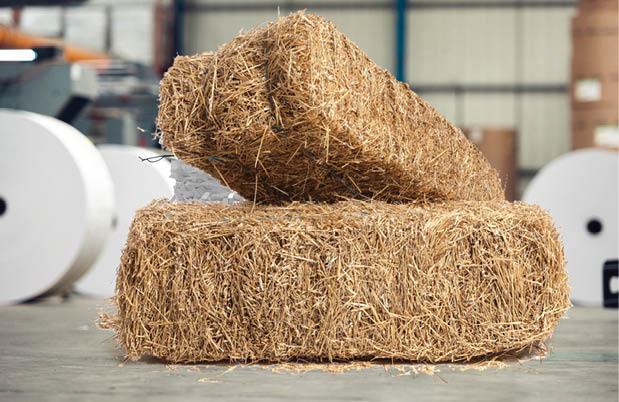
Paper pulp is also sourced from wood chips and veneer waste which is a by-product of the wood industry. JK Paper, Satia Industries, and Kuantum Papers reutilizes wood chips and veneer waste, ensuring that the valuable forest resources are used efficiently and responsibly. By repurposing these materials, the company contributes to the conservation of forests and the reduction of deforestation. JK Paper’s modern disc choppers ensure uniform chip size, low dust generation and lower power consumption. This helps in improving their overall pulp yield percentage which is an essential factor for paper production.
Green and Clean Paper Production Process
Following the efficient sourcing of pulp for paper production, the paper production process also needs to be sustainable and environmentally friendly without compromising on the quality of the paper. Fortunately, there are many technological suppliers all across the world, catering to this need of the pulp and paper industry. These technologies not only make paper manufacturing sustainable but also make sure that there is optimal use of the resources available, making the paper production cost-effective in the long-run.
Modern technologies have enabled mills to achieve economies of scale along with resource conservation. For instance, JK Paper uses de-barkers that enhance the processing capacity of daily wood feed to over 40%. Apart from that, the mill uses disc filters that help in improving fiber recovery and reduce water consumption.
Water and Energy Conservation
Paper production is traditionally a water and energy intensive process and therefore paper mills are continuously working to reduce water and energy consumption in the paper making process. The pulp and paper mills in India are turning to processes that reduce the consumption of water and switching from fossil fuels to green energy like biopower energy to produce papers.
Seshasayee Paper and Boards Limited that has come up with structured, and innovative Lift Irrigation Scheme used in its Erode unit where the company treated its waste water, and the treated water is used to irrigate nearly 2140 acres of land in which local farmers grow sugar cane and tree crops like Casuarina and Eucalyptus. This innovative irrigation scheme has caught the attention of overseas experts and UNDP that not only shows the commendable water conservation system but a circular model of sustainability.
Kuantum Papers’ approach to water efficiency is equally notable. Their initiatives have resulted in a reduction of freshwater consumption by 2500 m3/ day. They managed to reduce their water consumption by 6 m3 per ton of paper last year, and have made it possible for the company to utilize it in over 2,000 acres of land through a network of pipelines laid by them. This year, through the installation of Twin Roll Presses (TRPEs) in their wood and agro pulp mills, the company further saved 3 m3 of fresh water per ton of pulp, enhancing washing efficiency and reducing effluent pollution. Also, the introduction of surface water (canal water usage) by the mil has reduced its reliance on groundwater and decreased their ecological footprint.
Naini Papers too has reduced its freshwater consumption from 1900 m3/ day to 1200 m3/ day, after the installation of IBS shower systems in the paper machines.
Apart from the water consumption method, the mills also strive to reduce energy consumption and turn to green energy to produce power. One such example is Trident Group. Their strategy is to phase out coal consumption and ramp up renewables and other forms of clean energy to ensure operational efficiency. The Group converts food and biomass waste into electricity via biogas plants. They are working on increasing biomass fuel to reduce reliance on fossil fuels. They have used 41.3% of biomass in fuel mix in FY 2023-24.
The mill is also equipped with multi fuel fully automated AFBC boilers with intelligent load management system that enables the mill to receive 110 kg/cm2 steam pressure generated through combustion of biomass and coal, consequently generating 40 MW power. The recovery boilers fired using Black Liquor(effluent) generate 65 kg/cm2 steam pressure helping to generate 10 MW of power, making the entire plant self-sufficient in terms of power and steam.
ITC PSPD has made significant investment in a highly efficient recovery boiler at its Bhadrachalam unit, which reduces over 1,50,000 tonnes of coal per year, expanding ITC’s renewable energy footprints. Moreover, ITC Bollaram unit runs on approximately 100 percent renewable electricity which is a prominent achievement in itself.
Tamil Nadu Newsprint and Papers Limited (TNPL) has employed an eco-friendly process where bagasse wash water is treated in a bio-methanation plant to produce biogas. This biogas replaces furnace oil in the lime kiln of the paper mill. This is the first registered Clean Development Project from the pulp and paper industry, which reduces approximately 45,000 MT of CO2 annually.
TNPL has also installed 35.4 MW wind farms at Devarkulam and Perungudi in Thirunelveli district of Tamil Nadu.
Air Emission Management and GHG Reduction
The Indian pulp and paper mills deploy electrostatic precipitators across its boilers, along with scrubbers, dust extraction systems, dry fog systems, and bag filters to reduce air emissions during the paper manufacturing process. Air emissions are monitored through Ambient Air Quality Monitoring (AAQM) stations, with real-time data transmitted to the respective Pollution Control Boards.
Andhra Paper Limited has taken a proactive approach to reduce air emissions through infrastructure upgrades. By expanding the recovery boiler ESP to four fields and replacing 90 electrode plates in the coal-fired boiler’s electrostatic precipitators, the mill’s dust collection efficiency has significantly improved. The installation of an extra ambient air monitoring station has enhanced the mill’s monitoring capabilities, demonstrating the company’s commitment to environmental stewardship and regulatory compliance.
Another critical factor for the paper industry is GHG emission. In India, GHG or Green House Gas emissions are classified as Scope 1 and Scope 2 where Scope 1 is the emission from combustion of fossil fuels at the mill site, whereas Scope 2 is indirect GHG emissions associated with the purchase of electricity, steam, heat, or cooling. Paper mills in India are striving to reduce their GHG emission in their operations, but somehow it is a challenging task for the pulp and paper industry.
The India GHG Program, led by WRI India, the Confederation of Indian Industry (CII), and The Energy and Resources Institute (TERI), is a voluntary, industry-driven framework for measuring and managing greenhouse gas emissions.
Over recent years, the program has gained momentum with the release of India’s National Action Plan on Climate Change, the Low Carbon report, that showcases initiatives for pollutant trading from industrial plants, and the mandatory energy efficiency trading scheme. These developments have significantly aided the Indian paper industry in achieving the nation’s energy and carbon reduction goals.
Satia Industries has made a significant move to mitigate greenhouse gas (GHG) emissions. SIL has implemented a Precipitated Calcium Carbonate (PCC) plant which captures 24,400 cubic meters per hour of carbon-dioxide produced, as a byproduct of fuel combustion in their boilers, preventing it from being released into the atmosphere.
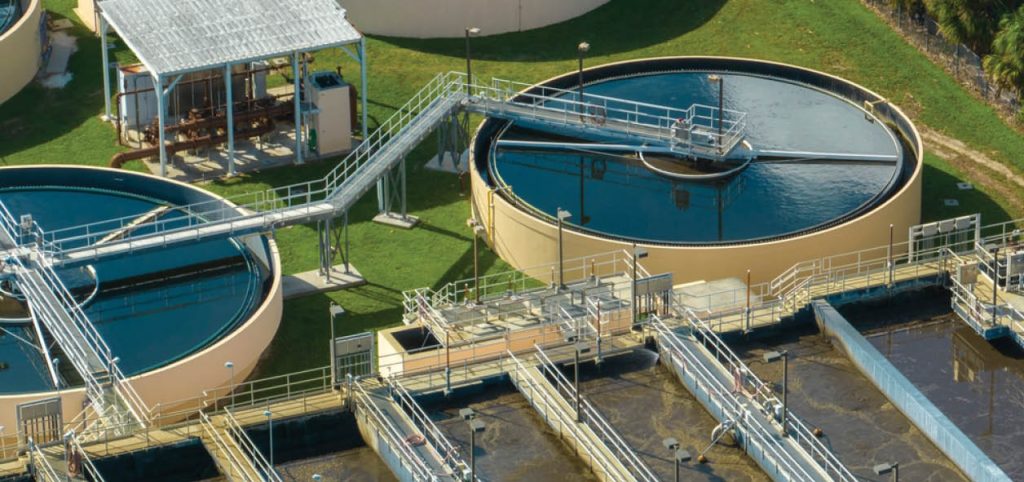
ECF Bleaching
Bleaching is another step in the paper manufacturing process that uses extensive chemicals and hazardous elements that can be a threat to the environment. Therefore, the Indian paper mills have adopted techniques that reduce the amount of hazardous substance in paper bleaching. Paper mills such as Satia Industries use ECF (Elemental Chlorine Free) bleaching technology that minimizes the formation of dioxins and other toxic substances that can result from conventional chlorine bleaching.
The use of ECF technology not only benefits the environment but also enhances the quality of their paper. It produces paper that is brighter and stronger, meeting the high standards expected by our customers while maintaining costs and environmental integrity.
West Coast Paper Mills too is involved in chlorine free (ECF) bleaching processes that has enabled the production of consistent quality of high-bright and high-strength pulp with improved cleanliness and lasting freshness with least pollution load.
Also Read: ITC Spearheading Sustainability in the Pulp & Paper Industry
Waste Water Treatment
Waste water and effluents is one of the most significant concerns for the pulp and the paper industry. Mills use Effluent Treatment Plant (ETP) to treat waste water. Effluents from pulp and paper mills contain solids and dissolved matter.
The ETP treatment used by the industry is mostly divided into two main process-primary and secondary treatments. In the primary stage, solids are allowed to settle and removed from wastewater. Principal methods used to remove solids from pulp and paper mills’ effluents are screening, settling/clarification and flotation, sand filtration, disinfection, demineralization. The method chosen depends on the characteristics of the solid matter to be removed and the requirements placed on the purity of the treated water. The separation of solids from the effluents is accomplished with the help of screens, grid chambers and settling tanks.
The secondary stage uses biological processes to further purify wastewater. The biological process is further broken down into aerobic and anaerobic treatment. The anaerobic process where the organic matter in the waste water is broken down in the absence of oxygen creating effluent with low BOD, COD and TSS. This process also produces biogas which is again used for energy consumption. This is followed by aerobic treatment. The most commonly used aerobic treatment is the activated sludge process. Systems for activated sludge are based on high quality surface aeration, fine bubble aeration or jet aeration depending on the type of wastewater. After final clarification, further treatment can consist of filtration, denitrification or effluent softening.
The ETP of Naini Papers comprises an activated sludge process and a state-of-the-art DCS-based bio-methanation plant from the Netherlands for high effluent load drains followed by tertiary treatment. The company recycles approximately 50% ETP-treated effluent after the secondary stage for wet washing of raw material and wetting of bagasse.
Trident Group treats water through its effluent treatment plant located in its Punjab unit and uses the same water for gardening and horticulture purposes. The company is one of the largest among industries, in terms of water recovery from waste streams capacity and best in class technology implementation, as per its ESG report.
Zero-Liquid Discharge
One technique that is fast gaining attraction in the pulp and paper industry for effluent-to-raw water recycling is zero-liquid discharge (ZLD). A ZLD treatment system utilizes advanced technological water treatment processes through which industrial wastewater is essentially reduced to dry solids/salts. This allows recovery of additional water streams that can be integrated onto interplant water network systems. ZLD is becoming a necessary waste management practice due to its ability to reduce air and water pollution as well as emission of greenhouse gases.
Sehasayee Paper and Boards is one such mill that practices zero liquid discharge in its Tirunelveli unit, where treated waste water is recycled and reused in the process and the remaining treated water is discharged for plantation within the mill premises.
Century Pulp & Paper Mill has also achieved zero liquid discharge (ZLD) in its wastewater treatment process by incorporating technologies such as ASP for separate treatment and complete recycling of recycled paper plant wastewater for raw material washing.
By-Product and Future Technologies
The pulp and the paper industry is not only becoming water and energy efficient but also reutilizing its byproducts for different industries. For instance, the fly ash produced during the paper making process is used in the cement industry, while the lime sludge and lime grit is used as raw material for quicklime which is used in the manufacturing of iron and steel and also used to make bleaching powder which is again used in the pulp and paper industry.
TNPL has established a cement factory for the conversion of mill wastes, such as lime sludge, fly ash, lime grit, and bed ash rejects into superior-grade cement. The initiative formed as a part of the company’s solid waste management system.
In the year 2023-24, TNPL produced 2,00,155 MT of cement. The cement kiln flue gas is also used as an input for manufacturing of precipitated calcium carbonate (PCC) in an on- site plant. Wastes generated in the process, such as lime sludge and lime grit, are used as raw material in the lime kiln of TNPL and its cement plant, respectively.
Another interesting technology that is forthcoming in the pulp and paper industry is carbon capture technology, which utilizes chemicals known as amines to trap carbon dioxide generated by pulp mills. The process involves separating the carbon dioxide from the amines using high-temperature methods, resulting in pure streams of carbon dioxide that can be condensed into fluid form for later utilization. However, scaling this technology for widespread application remains an area of ongoing research, with the substantial investment required for the process posing a significant challenge.
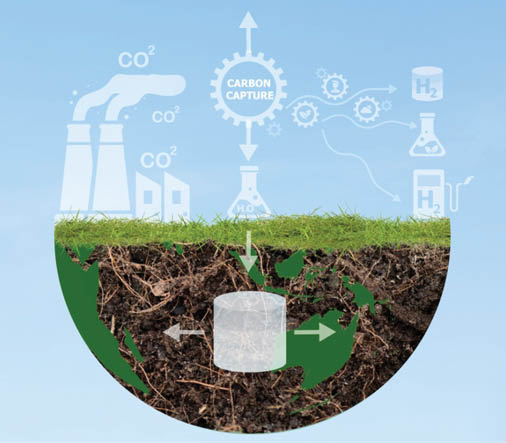
This process opens interesting opportunities for the pulp and paper industry as the captured CO₂ can be used within the pulp mill itself, to precipitate and recover lignin from black liquor, which can then be used to produce polymers or biofibers. Other opportunities for the use of the captured CO₂ include the production of e-fuels, like e-methanol or e-methane, or green ammonia that can provide comprehensive support to the pulp and paper mills.
To sum up, these examples from various paper mills clearly showcase that the pulp and paper industry is highly sustainable, continuously innovating, and upgrading itself to meet environmental standards. Paper mills are consistently striving to conserve and reutilize resources efficiently, building a circular ecosystem that optimally utilizes resources for paper production. They are also implementing innovative solutions to achieve net carbon-negative targets and demonstrate environmental stewardship.