AFT has introduced its new Industrial Internet of Things (IIoT) solution, AFTLinx™ Service, designed to enhance process optimization through a data-driven approach. This innovative technology focuses on optimizing maintenance schedules and refining processes. AFTLinx service features easy-to-install sensors that gather critical data that can be deployed independently, or the sensor signals can be directly integrated into the mill’s automation system, offering flexible functionality. The system is fully encrypted and includes an automatic backup facility, ensuring uninterrupted operations and continuous monitoring of mill functions. In an exclusive interview with Paper Mart, Mr. Henri Heikkilä, Customer Service Engineer (AFTLinx) at Aikawa Fiber Technologies Oy talks about this new automation technology and how it has benefited the pulp and paper mills across the globe.
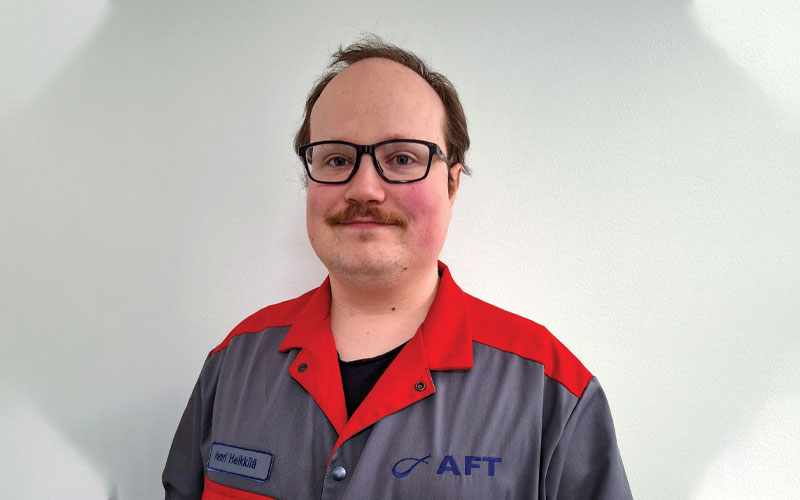
Paper Mart: Can you briefly tell us about your company?
Henri Heikkilä: AFT is a global supplier serving customers in pulp and paper, food, and mineral markets with engineered components, capital equipment, and system optimization services. With over a century of experience, we specialize in stock preparation, screening, refining and paper machine approach flow systems. Our expert solutions are tailored to the customer’s furnish, their application, and the end product being produced in order to optimize their return on investment. We have manufacturing facilities and sales offices in the Americas, Europe and Asia to best leverage our deliveries and services.
The company focuses on an incident-free work environment with high safety standards, equipping employees with the necessary skills to operate machinery efficiently and with proper safety standards in various areas of work. The company also delves into R&D, developing fundamental research into real life solutions. To accomplish this, AFT works closely with a network of pulp and paper research centers, looking for new development opportunities for performance wear components and equipment. The company also prioritizes processing and sustainability, ensuring energy reduction and fiber quality.
PM: What specific automation solutions do you cater to the paper mills and how does it enhance the operational efficiency?
HH: AFT has developed a new IIoT solution which brings a data-driven approach to process optimization. Designed for low-consistency refiners, AFTLinx service helps us optimize maintenance schedules and the refining process. The solution includes easy to install sensors for data gathering on critical parameters like refiner plate wear and condition measurement.
We can gather additional information such as flow, temperature, and other variables by using customer generated data or by adding more sensors if needed. All gathered data is securely stored in a cloud service, ensuring convenient access and robust data protection.
Watch: In Pursuit of Lesser Water Footprint‘
PM: What features make this automation solution unique?
HH: With the AFTLinx service, offered alongside our MaxEdge™ refiners, customers can benefit from troubleshooting support provided by AFT’s team of experts. This includes assistance with startups, process optimization, and testing of new refining methods, plate geometries, and equipment, all having a data driven approach for testing.
PM: How do your technologies integrate with the existing machinery and software systems in the mill? Please elaborate.
HH: AFTLinx service can be implemented with minimal interference to existing mill systems, by installing sensors completely independent from mill automation. There is also the option to integrate AFTLinx sensor signals directly into the mill’s automation system. This can be set to include a clash detection system.
PM: What support and training do you offer to help mill staff effectively use your solution?
HH: To help mill staff effectively use our automation solution, we provide support and training to the staff. This includes detailed installation instructions and hands-on assistance to ensure a seamless setup. Staff are also trained on how to read and interpret the system’s reports, empowering them to make data-driven decisions for process improvements.
As more data is gathered, we offer advanced training to help staff understand deeper data analysis reports, providing insights into further operations.
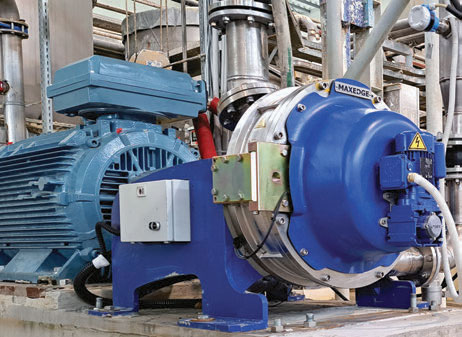
PM: What are the typical ROI and payback periods for your automation systems in paper manufacturing?
HH: When calculating ROI for our automation systems, we take into consideration mill-specific baseline operating data such as unplanned downtime, typical component wear, process variability, and product quality.
PM: How do you ensure the scalability of your solutions to accommodate future growth or changes in production needs?
HH: To ensure scalability of our solution, we use cloud computing which allows flexibility in gathering and analyzing ever-increasing data quantities. Additionally, we can easily add or modify additional sensors to the system with minimal effort.
PM: How do you address the security concerns associated with implementing automated systems in industrial environments?
HH: To address security concerns in industrial environments, we ensure that the online connection between the AFTLinx hardware and the cloud is completely or fully encrypted. Additionally, there is no direct link between the cloud connection and the mill automation system, which minimizes security risks by keeping the two systems separate. This approach protects sensitive mill operations while enabling safe and secure data management in the cloud.
Also Read: A New Era Begins with Valmet DNAe
PM: What measures do you take to ensure the reliability and uptime of your automated solutions?
HH: For reliability and uptime of our automated system, we have built our AFTLinx hardware in such a manner that even after sudden blackout or other power outage, the system automatically begins its operation without any need for human intervention. The data is also backed up locally. So, in the situation of a connection failure, the system automatically stores the data until the connection is restored, ensuring that no critical information is lost.
PM: Please explain how your systems contribute to sustainability operations of mills?
HH: Optimizing the refining process and determining best practices are significant methods to extend plate life. By carefully monitoring variables such as plate wear, consistency, and energy use, mills can not only enhance the overall efficiency of the refining process but also minimize plate wear and optimize energy efficiency to lower operational costs.
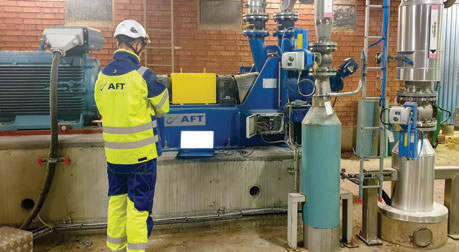
PM: What innovations or trends do you see shaping the future of automation in the industry?
HH: In the future, handling big data is going to become more and more important. Technology to incorporate AFTLinx service seamlessly not only to any type of refiner, regardless of manufacturer, but also to other process equipment will be available soon. This will allow a more thorough analysis of mill operations with the help of AFT experts, cloud computing, and machine learning.