One of the leading suppliers of the key technologies and services for pulp and paper production has been continuously working on various critical fronts to make its pulp and paper lines efficient, both yield and consumptions wise, apart from offering some of the most advanced systems and tools in recovery and automation areas. The company eyes some lasting tie-ups in India with the demand of advanced and durable technology growing keeping environment and quality in view.
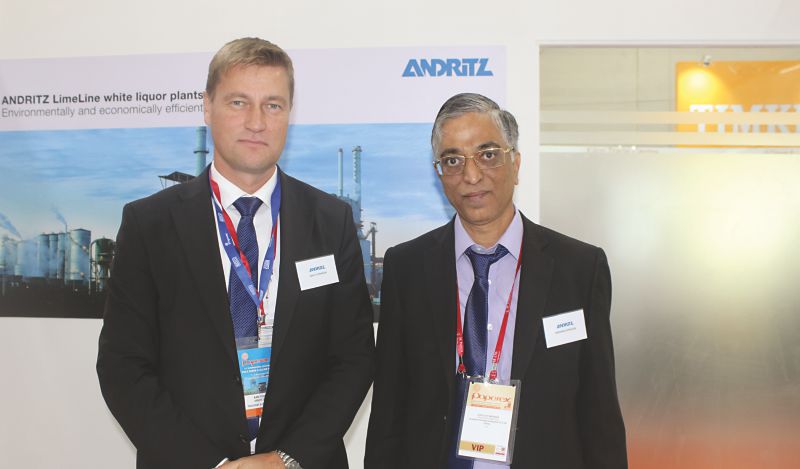
Paper Mart recently conducted a detailed interview with Mr. Kari Tuominen, President and CEO, ANDRITZ Oy, Finland & Mr. Sridhar Gopalan, Executive Director, ANDRITZ Technologies Pvt Ltd, India. The interaction broadly covered a host of technological issues and alternatives, where ANDRITZ has a lot to offer, especially in areas of fiber line optimization, mill wide energy efficiency development and minimizing the wasteful consumption patterns in a pulp and paper mill.
Paper Mart: ANDRITZ has been active in the Indian market since long. Our readers would like to know what the journey’s been like for ANDRITZ from when it started doing activities in India to till now.
Kari Tuominen: ANDRITZ’s activity in India goes long way back. However, in 2008, the company’s structure in India took a definite shape as it is seen now. At that time, Sridhar Gopalan was looking for a suitable location, which we found in Chennai and started looking for professional people to be employed. Very soon, we established the company and locked the location. The key people chosen then are still working with us. They started building up the expertise and knowledge, especially in the recovery cycle of a pulp mill. Over the years, the expertise and capacity built here in India became an integral part of our operations worldwide.
Much of the key engineering, quality control, and startup services for all our boilers around the world today are handled from Chennai. For example, world’s largest recovery boiler having a capacity of 12000 tonnes of dry solids per day is in Indonesia and much of its site work, startup, and commissioning exercises have been overseen by ANDRITZ’s Chennai arm. And one of the reasons why the boiler started so well and is running efficiently is the Indian expertise and people. For certain product groups, the Chennai office is a fundamental part of our excellent operations worldwide. During these years, the activities have been expanded into other product areas gradually. And also, into other business areas like engineered wear products for the pulp and paper industry and services required therein. We have also been increasing the number of people annually – from the figure of one in 2008, we are now at a level of 300 people in Chennai.
PM: ANDRITZ as a company and technology provider for the pulp and paper industry have a long range of products. We would like to know the recent innovations and technology upgradations.
KT: To elaborate a bit, ANDRITZ is a supplier of complete pulp mill process system – from wood processing, fiberlines and pulp drying to evaporation, recovery boiler, white liquor plants, power boilers, gasifier, lignin separation, and you name it! We don’t really supply for one department but really look at the complete mill system and integrate the pieces well together. We are putting emphasis on several things simultaneously in order to deliver the best expected of us. First of all, if we think about a delivery project, it has to be delivered on time and within the budget. For example, the mill in Brazil – Fibria Três Lagoas second pulp production line, the world’s largest single line pulp mill, was started a couple of months ago and started on time. Starting up within time and ramping up the production to the designed capacity as quickly as possible are among our first targets and we have succeeded in achieving that.
Moreover, our work on optimum capacity utilization has been tremendous in recent times. Consequently, during the first year of the operation, the mills have been achieving 90 percent of the designed capacity whereas it used to be around 70-80 percent just a few years back. The lifecycle of the mills of clients needs to be optimized so that they can always keep production level high and have high availability in all the areas. On the overall basis, these are the really important targets.
On top of that, we have been consistently concentrating on safety, quality, and cost optimization. If you think about the cost structure of the pulp manufacturing, raw materials constitute the largest part of the operating cost, followed by chemicals, energy, and of course, labor. But, on the raw material side, if we talk about wood, we are making sure that most of the wood is converted into saleable pulp.
To elaborate further, in the wood processing plant, we have had for a long time a unique chipping concept – the horizontally-fed HHQ-Chipper, which produces excellent high chip quality and minimizes the rejected part of the wood. Also, in the wood processing, a system called ChipperEKG, effectively monitors chipper operations and diagnoses performance or maintenance issues, for example, if a knife has been hit and needs a replacement. If you don’t replace it, you would make worst quality wood chip. A system immediately tells the operator when it is the time to change the knife. CrusherEKG does the same monitoring for bark crushers.
In the fiberline, we have developed a process concept called A-yield, which means that we get the highest pulp yield out of the wood going into the digester. Our Lo-Solids cooking process, which has been used for over 20 years, is still an outstanding cooking method. With some of our clients, we apply polysulfide cooking system, which actually increases the yield. A mill in Finland has been using this polysulfide system for four years and it has proven to increase the yield by 1-2 percentage point, which is a substantial improvement. In the fiberline, ANDRITZ has lots of unique features. For example, we do not remove the uncooked particles of wood before the oxygen delignification stage instead let them go through the oxygen stage where these uncooked particles can actually be turned into saleable pulp rather than taking them out of the processes and burning them. This feature of not removing knots and rejects and locating screening after the oxygen delignification is unique for ANDRITZ. For pulp washing we use DD-Washers (Drum Displacer). DD-Washers allow the knots and other uncooked particles to get carried with the pulp for the next process stages, thus allowing to locate the screening plant after the oxygen delignification.
Our bleaching sequences are very effective with low environmental load. That is also due to the reason that the DD-Washer is very efficient as pulp washing equipment. The chemical consumption figures in ANDRITZ’s fiberlines are really benchmarked. DD-Washer technology in the fiberline provides excellent washing results and lowest chemical consumption so far.
In the drying section, we have been improving the efficiency of our dryers so that we come up with narrower machines and produce much more pulp. This is the result of our Twin Wire technology. Besides in the drying section, the blow box design has been improved for improved heat transfer and reduces the size of the dryers.
Going to the recovery cycle, ANDRITZ evaporation plants are based on lamella technology. With this technology we ensure excellent heat transfer and make sure that the evaporation systems do not get plugged. We continuously produce black liquor with very high dry solid content – typically 80-85 percent of black liquor dry solid content. That’s a requisite for a high energy recovery boiler, which we call HERB recovery boilers. Those were introduced 15 years ago and by introducing these high energy features in a recovery boiler, we have really been able to provide our customers with excellent energy efficiency for the mills. Since then ANDRITZ HERB recovery boiler has been continuously developed and today we are offering a wide range of energy improving solutions from which the customer can select the concept most suitable for them. Today, the power sales into national grids are a big income for our customers. Thanks to these energy efficient technologies!
In the white liquor plant, we have been continuously developing our filtering systems, which provide a system where the solid waste streams are minimized. Also, our lime kiln technology is very efficient. Our lime filters are efficient and they provide very low sodium carry over and very high dry solid contents, maximizing the energy efficiency of the whole system. In many of our plants, our clients are looking for full-mix concepts. That has led to the fact that quite many new pulp mills have gasification plant included in the concept. We take the bark and also the screenings rejects from the wood handling and gasify them; use that gas as a fuel in the lime kiln. Such a system was getting popular in the 1980’s but due to lower fuel prices and gas prices, the profitability went down a little bit. But now, with increased fuel prices again, this concept of gasifying has a very short payback time.
One of the new things which are coming up is lignin separation. Rather than burning the lignin in the recovery boiler some of our clients want to separate the lignin and make more value-added products out of the lignin. The market for the lignin has been limited so far, but gradually we see more and more markets opening up for the same. We have developed new systems for producing sulphuric acid of commercial grade out of non condensable gas streams. The sulphuric acid produced can be used in the mill for internal purpose. Producing internally can avoid purchase of the acid from the external sources. In European and South African mills, we have been separating methanol already from black liquor for a long time. That methanol has been liquefied and quite often burned in the kiln as an extra fuel. However, the methanol contains some nitrogen. We have developed systems to remove the nitrogen completely and also the sulphur to sell the methanol to an outside user as an industrial grade methanol. It means the value of the methanol is 2-3 times higher than the value of when you burn it in the recovery boiler.
PM: There are many individual and separate processes in the pulping. How does automation play a role in the ANDRITZ technology offered to the pulp and paper industry?
KT: First of all, everything starts by preparing mills with balances – mass balances, energy balances and so forth. You deliver the mill according to those balances. That’s where our expertise as ANDRITZ comes in. As I explained, we look at the pulp mill holistically and the balance has to match. During our delivery projects, in many cases, we build simulation tools, which at the same time is a training tool for our clients, and which is like a living replica of the existing future mill concepts. With that simulation tool, we can test and verify design concepts and process control logic quickly at low cost and low risk. At the same time, we can utilize this kind of automation for training purposes of operators.
Then, we of course have advance control systems, which improve the operations within one process area, and at the same time interact with the advanced control tools of other process areas. So, the whole mill gets to be a living, unified control loop. Then, with the immense possibility of the IOT world, utilizing automation and available information has just expanded. We utilize this information on our Metris platform to provide advanced solutions to our customers. We call them Optimisation of Process Performance, OPP systems, which include smart sensors, big data analysis, augmented reality, and so forth. With our highly effective computerized tools we can help our customer to optimize their process using the data collected from their process. This also helps us identify areas where the improvement could be made; for example, identifying valves that are not operating in an optimal way. By finding these bottlenecks, with these analytical tools, we can increase the capacity and production level of the mills. In addition, to be able to quickly help our customers we are providing online support from our Metris customer support center enabling 24/7 support with nominated process resources. Such automation plays a huge role in the complete lifecycle of the modern mill deliveries as well.
PM: There is much regulatory pressure on the Indian pulp and paper industry to reduce its consumption patterns in water, energy, and of course, chemicals. How does ANDRITZ approach the consumption reduction targets through its system?
KT: As said earlier, ANDRITZ helps in building pulp and paper mills with concepts that also incorporate the idea of lowest consumption of resources. Let’s talk about the chemical consumption first! The chemical consumption in the fiberline starts with excellent quality chips which provides continuously good operational environment for the digester system where we use our Lo-Solids cooking technology providing easily bleachable pulp. Then the main key for the low chemical consumption is our DD-Washer technology, which is a very effective washing device to remove the cooking chemicals from the brown pulp and also the reaction products after the oxygen stage. The pulp will then, therefore, be well bleachable and very clean when it enters the bleach plant. And, when it enters the bleach plant you have to make sure that the mixing phenomena are effective. We have put a lot of R&D into our medium consistency technology, both in terms of pumps and mixers that operate at optimal conditions. The mixing has to be very good and reaction tower design optimal to prevent channeling so that we can really utilize the reaction time which is designed for the bleaching stage. After the bleaching stage, there is then again the very important part, i.e. DD-Washers which in a way are multi-stage washers due to the possibility to fractionate the filtrate coming from the washer to a cleaner and dirtier fraction. In terms of chemical consumption, all these factors affect and enable us to provide our clients with low chemical consumption.
If we think about water consumption, it’s exactly the same. With a good washing technology, you don’t need to use that much water for washing. In today’s world, when we aim at very low effluent volumes, we have to reutilize the filtrates that are generated in the mill someway. The concept of the modern pulp mills includes that part or all of the alkaline part of the bleaching filtrate is returned back to the recovery cycle through brown stock washing. Quite often, there are some chlorides included in that alkaline filtrate which means that in the recovery cycle you have to make sure that the chlorides are removed to prevent corrosion and plugging in the recovery boiler. There we have processes like leaching (ALE) and crystallization systems (ARC) to remove the additional chlorides. We have also developed systems where we can utilize the treated effluent after the effluent treatment plant and return it to certain places in the pulp production.
Sridhar Gopalan: There is a huge potential for India to learn how to use water in a very careful way and try to minimize the effluent discharge, and try also to make the industry sustainable and greener.
PM: How far the Indian pulp and paper industry has been responsive to your kind of technology and have been adopting the innovations that have been done by you in different processes of pulping?
SG: We have already done successful projects with ITC and have just completed a very good project with them. It was done in partnership. We are not selling any equipment to ITC. We are working together with them on a kind of benefit sharing arrangement. We tried to minimize the water consumption and improve the water balance. Also, we tried to make it greener, economical, and environment-friendly while using the bleach plant effluents. That’s one example.
Another example is that we are on the verge of joining hands with another major corporate soon to do the OPP, i.e. optimization of plant performance. By using the IIoT concept and the virtual expertise from the global ANDRITZ operations, we have this augmented reality to get more and more efficient mill wide operation managed in a holistic way, i.e. try to look at the mill as one single entity. We have also delivered lots of equipment to various clients. But unfortunately, we didn’t have any major investment in India in the recent times. There has not been any major Greenfield expansion in India. As soon as it happens, we will definitely have a pleasure of participating in a much bigger way in this country than what has been the case in the last 3-4 years.
PM: Can you comment more on how the industry can optimize the uses of wood rejects as well as the lignin?
KT: Many of our clients have the internal targets of making the pulp mill completely fossil fuel free. The gasification of bark and screening rejects is very natural way of doing that because the lime kiln is the biggest area for fossil fuel usage in a pulp mill today. You can very easily achieve the target of a fossil fuel free mill.
As mentioned earlier, most of our customers when they plan a new mill, they look at the alternatives, and at least reserve a space for future possibility of installing such a system. For the lignin separation, the technology is there waiting for the lignin demand to increase. We see the lignin demand is increasing and our clients are finding more and more applications for the lignin usage. Especially for the mills, which have been operating for a longer time and have a recovery boiler limiting the production, this is a very effective way of unloading the recovery boiler by taking out the lignin and there is a certain payback for that.
PM: Few words on the growth outlook of India and how ANDRITZ is positioned to help the Indian pulp and paper industry to meet the challenges and opportunities.
KT: We have a lot of technologies for the industry to take benefit from. It’s just to start a discussion with the client about their needs and we can present even more than what we are asked to offer in the first place. This is not only pertaining to our pulping technology. Also, our paper technology including board and tissue machines and especially the recycled fiber treatment systems are world class with energy efficiency. As we see the packaging grade manufacturing growing in the future, we see that this kind of technological offering that we have is a very good alternative for the Indian industry.
SG: Basically, we at ANDRITZ are able to synthesize the technological advancements with Indian design and engineering expertise and get the best of both the worlds to meet the customer requirements. We are very positive about the major contribution to industry from ANDRITZ to have more sustainable, economical, and efficient technology with a greater emphasis on ‘Make in India’. We would like to localize the content as much as possible in line with the Govt.’s plan and make it more affordable and beneficial to our industry.