Major upgrades and a series of smaller innovations have been incorporated into the new ANDRITZ PrimeFilter D to improve performance and reduce maintenance. The new design includes the latest bagless technology, which is well-proven in over 65 installations to date. The upgraded PrimeFilter D has been well-received already – 15 units have been started up and more orders are being received from leading papermakers.
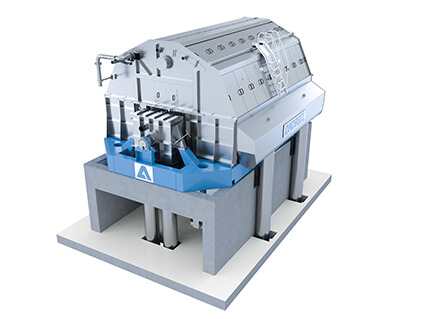
When engineering the new PrimeFilter D (Figure 1), ANDRITZ specialists evaluated the performance of over 600 disc filters the company has installed around the world, spoke with customers, and re-examined the design from end-to-end. The result is a disc filter that is perfectly suited for thickening all kinds of pulp and operating at higher consistencies, and for producing excellent quality filtrate when applied as a save-all for fiber recovery in PM white water systems.
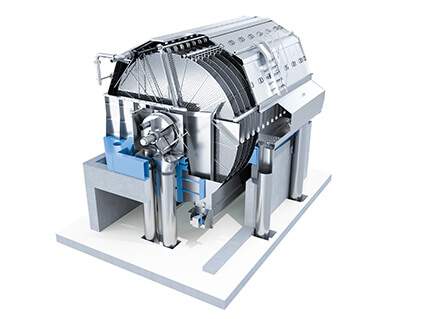
MAJOR UPGRADES TO TECHNOLOGY
The PrimeFilter D fuses several key technological innovations into one unit to improve throughput and reduce both investment and operating costs.
HHw for even the most demanding thickening applications. HHw stands for High consistency, High freeness, and a wider distance between discs. This enables PrimeFilter D to handle higher feed consistencies and higher freeness pulps. ANDRITZ’s integrated feedbox with patented infeed chutes (Figure 2) provides individual feed for each disc in the PrimeFilter D. A new feature is the ability to add an optional second feed at the bottom of the vat to avoid creating a “dead zone” for pulps with high drainage rates while keeping the vat bottom properly diluted.
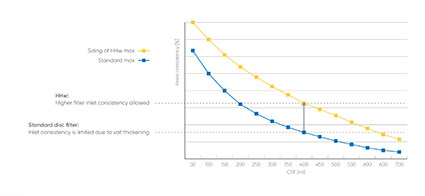
Feed consistencies with the PrimeFilter D can be considerably higher than a standard disc filter. This comparison (Figure 3) shows the feed consistency range at any given CSF of the PrimeFilter D compared to a standard ANDRITZ DF38 unit.
In the HHw design, there is more distance between the discs and the outlet chutes. This creates fewer rubbing forces on the surface of the fiber mat and reduces the tendency for the mat to peel off when the disc sector is submerged.
Disc guiding rolls with internal bearings ensure smooth, stable, and guided rotation of each filter disc. This results not only in smoother operation, but also longer life of the filter internals.
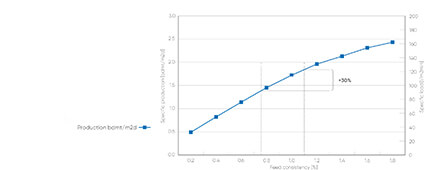
The HHw technology allows PrimeFilter D to reach higher specific loads for a given feed consistency. (Figure 4) shows that raising the feed consistency from 0.75 to 1.1% results in a 30% increase in specific production (in terms of bone-dry metric tonnes per day). Or, if the production is not needed, the filter could be smaller (30% less filter surface area) to achieve the same production load.
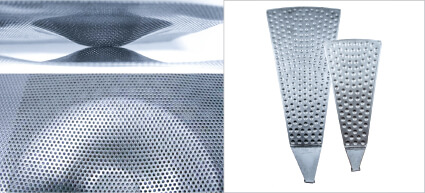
Conical Cell bagless sectors for uniform fiber mats, long life and less maintenance: The Conical Cell bagless sector design of the PrimeFilter D (Figure 5) offers significant improvements in terms of operation and maintenance.
Since the sectors are basically flat, they produce a very uniform fiber mat that is easily doctored off in one piece. The way the plates are manufactured results in a 5% increase in effective filtering surface compared to a flat sector fabric. The open design is easy to clean.
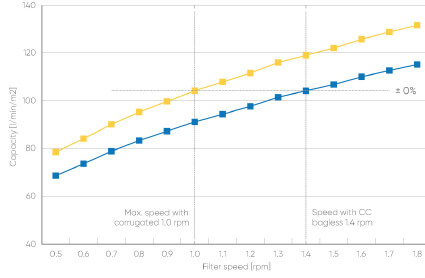
Compare this to the performance shortcomings inherent in other bagless sector designs, particularly “corrugated” sectors. The asymmetrical corrugated design creates hydraulic flow impingements. The fiber mat is not uniform due to the peaks and valleys of the corrugations. This lowers the maximum rotational speed and therefore limits the capacity of the filter. Overlapping areas in the sector interior makes cleaning more difficult, and there is a tendency for inside scaling.
Because of this, the Conical Cell sector allows a filter to run faster than a corrugated sector. An example is shown in (Figure 6), where the maximum rotational speed of a corrugated sector is 1 RPM for this grade of pulp. The PrimeFilter D’s Conical Cell allows the disc to rotate in a range of 1.4-1.8 RPM for that same grade, accounting for a production boost of 15-20%.
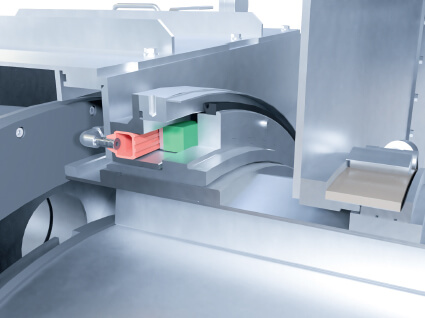
Two-level shaft sealing for improved reliability and filtrate quality: A significant technical improvement in the PrimeFilterD is its advanced double sealing arrangement (Figure 7). The sealing is outside the filtrate valve making it easy to access. This eliminates the possibility for fibers to enter the filtrate directly. Ease of access allows the seal to be exchanged without removing the filtrate valve housing, covers, and sealing support. In addition, no realignment of the filtrate valve is necessary after a seal exchange. A rubber hose inside the shaft seal is inflated with compressed air to provide uniform surface contact with the sealing ring around its entire circumference. Other filters utilize an asymmetrical three-point spring system that creates uneven sealing forces, which can cause uneven wear of the seals and a shorter lifetime.
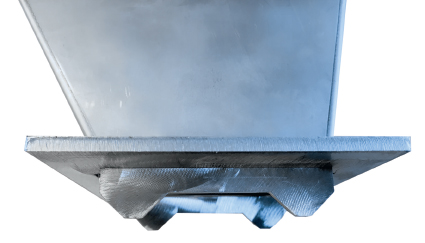
A RANGE OF OTHER DESIGN IMPROVEMENTS
The PrimeFilter D has a simple, ruggedized system for installing and locking the disc sectors into place with guide bars at each end. Integrated into the base of each sector is a tapered positioning plate (Figure 8) that guides the sector into position in the shaft. A rugged rubber seal covers the sector foot flange to ensure sector-to-shaft sealing for stable vacuum and enhanced filtrate flow.
Knock-off nozzles have been redesigned to make it easy to flush out fibers and deposits. A simple hand lever engages the easy-cleaning function while the filter is in operation.
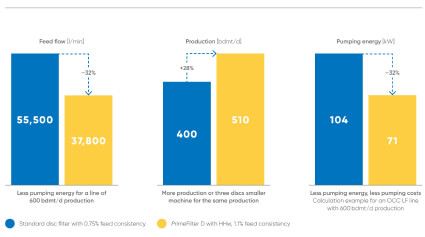
THE COMPLETE PACKAGE
The new PrimeFilter D delivers superior throughput and operation (Figure 9). The uplift in production can be a 30% gain per disc surface area. Inlet consistencies up to 2% are possible. Up to 30% less pumping energy is consumed due to less water in the suspension and reduced water recirculation requirements.
The fiber mat created on the ConicalCell bagless sectors is optimum in terms of formation and uniformity. The bagless sectors eliminate the need to shut down to change filter bags and the improved design for aligning and supporting disc sectors ensures overall smooth operation.