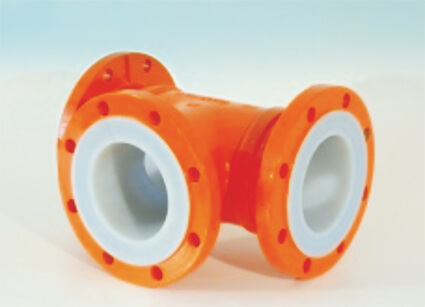
Fluoropolymer-lined systems based on PTFE/PFA prove to be economical and useful alternatives to metallic alloy piping in many applications like handling corrosive solvents in Chemical and Pulp & Paper industry like transfer of Chlorine dioxide (Cl02), NaOH, H2S04 acid etc. Few key points of this technology along with critical success factor has been discussed in this paper after having intensive experience in using Fluoropolymer lined pipes and components for handling corrosive chemicals. In Certain applications Fluoropolymer PTFE /PFA has become alternative choice to exotic material like Titanium, Tantalum, and Zirconium etc. Paper companies in India like TNPL, ITC, Century, West Coast, Abhishek Industries and many more have been benefited with this technology based solution.
The Pulp & Paper industries face a continued and growing need for the containment of corrosive or harmful products and intermediates that reduce the service life of conventional piping and vessels. Fluoropolymers has opened the door of all new opportunities to handle corrosive solvents like Acids (H2SO4), Bleaching chemicals, Chlorine dioxide (CLO2) in Fiberline. Our R&D invented first Fluoropolymer Teflon® PTFE in 1938 which became prime material for handling corrosions in early 50’s.
Critical success factors for Fluoropolymer Lined components in Pulp & Paper Industry
The items listed below must be considered during the selection, design, and operation of Fluoropolymer-PTFE/PFA lined pipe in pulp&paper applications.
Key Operations:
• Chlorine Di Oxide Transfer Line
• Chemical handling in Fiber line&Bleaching Cycles
• Acid (H2SO4) Handling&Caustic extraction.
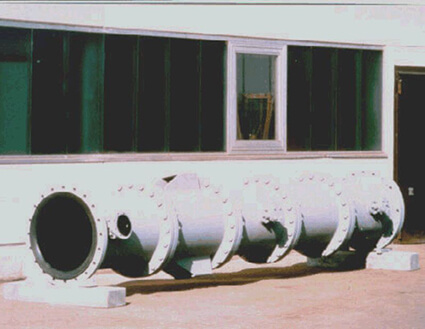
Liner Selection
Industrial polymers have been used since the 1950s to handle both aggressive and extremely pure process fluids. These fluoropolymers have been used in applications such as corrosion-resistant lining for process equipment which includes Lined metallic piping, fittings columns, vessels, pumps, and valves.
PTFE-lined systems offer more cost-effective service than many metal systems. This is due to their comparable installed cost coupled with lower life-cycle cost. Fluoropolymer liners are often used in chemical services with aggressive chemicals at temperatures approaching 235-250° C. The plastic lining also eliminates concern about chloride stress cracking of stainless steel.
Definition of Lined components & Liner Material selection
Fluoropolymer-lined piping combines a structurally sound metallic shell with a corrosion-resistant plastic liner. The most common plastic liners are polytetrafluoroethylene (PTFE), polyvinylidene fluoride (PVDF), polypropylene (PP), Perfluoroalkoxyalkane copolymer (PFA), perfluoro ethylene propylene copolymer (FEP), ethylene-tetrafluoroethylene copolymer (ETFE). Liner selection is primarily dependent upon the Types & concentration of chemicals, Vacuum/ Pressure conditions and normal operating temperature. The maximum temperature rating for the plastic liner may be lower for installations handling highly aggressive chemicals. PTFE has highest popularity for liner material because of high chemical inertness to nearly all chemicals, Higher temperature stability & economically feasible.
Process Operations-Thermal Cycling
For Vacuum application, Generally PTFE lined pipes up to 8 inch size works fine. For larger sizes thicker liners and counter Vacuum arrangement can be considered. Minimizing the occurrence of thermal cycling in hightemperature permeating applications and controlling the cool down cycle of the process can maximize service life of the plastic-lined piping system.
Selection of right Fabricator
Selection of right fabricator is equally important for successful application of Fluoropolymer lined piping & components in chemical handling. Fabricator should follow the right guidelines during processing and handling of fluoropolymers. Their facility should meet general good manufacturing practices and products must be qualified inline with internationally recognised standards.
ASTM Qualification Standard for Lined Piping and Components
The American Society for Testing Materials (ASTM) has established standards for common plastic-lined piping products. The ASTM F1545 specifications cover requirements for workmanship, dimensions, design, construction, working pressures and temperatures, test methods, identification markings, and the materials used in the construction of the final product.
Installation & Maintenance
The successful use of lined system also depends upon installation process. Various factors like selection of right flange design, gaskets, applying torques during installation should be followed as per suppliers engineering manual. In case of Fluoropolymer lined systems, specific torque ranges to be implemented & Re-torquing is required after 24 hrs to avoid any chances of leakages. Periodical visual inspections are recommended to check any Liner, flanges, gasket failure etc. Destructive testing can be performed by statistical sampling method.
Chemical compatibility testing and Failure Analysis
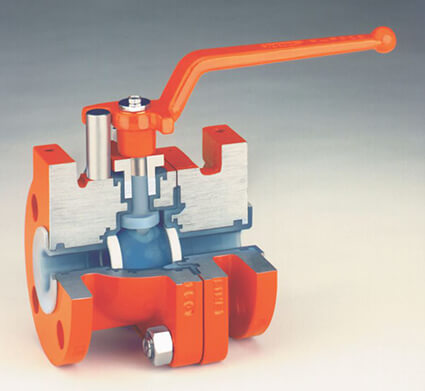
Generally, fully fluorinated polymers like PTFE, PFA are almost resistant to all known solvents except few alkali metals, whereas in case of new solvent mixtures & different temperature conditions, it is recommended to check chemical compatibility with material supplier.
Design considerations
Common venting systems used by plastic-lined pipe manufacturers are a series of 1.6 mm (1 16 in) to 4.0 mm (5 32 in) diameter holes in the metallic shell, or a helical groove system inside the housing that connects flange vents (Figure 1). The venting system provides a pathway for permeating chemicals (vapor) to escape.
Case Histories
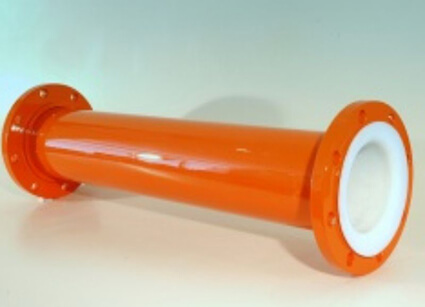
Case 1: As an alternative to stainless steel, non-metallic materials such as “TEFLON PTFE“ have gained increasing acceptance in paper industry due to their excellent chemical resistance and successful long term performance. As per above figure, verification of excellent performance is in D stage chlorine dioxide bleach stage seen at TAPPI USA where after 10 years of continuous service, TEFLON shows no evidence of cracking or failure. The inside surface of the liner was smooth and clean.
Case 2 (TNPL): Tamilnadu Newsprint & Papers Ltd located in southern India where Metso had supplied the fibreline. In Year 2007-08, complete TEFLON® lined pipes and fittings for fiber line as well as for Chlorine dioxide line were manufactured and supplied by a Fluoropolymer lined component supplier from India. They are member of DIPPN network and their facilities were qualified by DuPont Engineering USA.
Conclusion:
Fluoropolymer-lined systems prove to be both useful and economical in Pulp & Paper applications. Such systems help protect the process equipment and minimize loss of the chemical process fluids, which protects the environment. Use of proper engineering designs will offer large amount of cost saving & safety of handling corrosive solvents like ClO2 , H2SO4, NaOH etc in fiberline pulp & paper industry. These designs should acknowledge the major factors namely: service conditions, process fluid chemistry, and liner material. Indian Pulp & Paper industry is getting benefited with this technology in a big way.