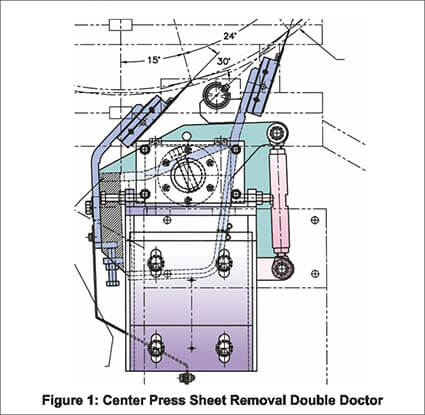
Abstract:
There are many applications on a paper machine where the installation of double doctors will help to improve machine efficiency through reduction of sheet breaks and elimination of rewetting. This paper will discuss the history of double doctors, the principles of how this technology works and the many benefits associated with the installation of double doctors. It will describe the many different applications where this technology can be successfully installed on paper machines and results from various installations.
Introduction:
Doctors tend to be one of the most neglected pieces of equipment on a paper machine which is quite surprising considering they are highly critical pieces of equipment in maintaining and improving paper machine runnability. For many years there were 3 main reasons for doctoring a roll on a paper machine:
• Sheet Removal: The Doctor System must be correctly located for removal of the sheet from the surfaces of rolls and cylinders and to assist the machine operators in transferring/transporting the sheet of paper from the wet-end to dry-end of the machine prior to the reel.
• Roll Cleanliness: The Doctor System must be correctly designed to help with the removal of fiber and dirt from the surface of rolls and cylinders, thus maintaining roll cleanliness and improving paper quality and machine efficiency.
• Roll Conditioning: The Doctor System must be correctly designed to ensure that the doctor constantly conditions the roll and cylinder surfaces, without causing damage, so ensuring that a top quality product is produced on the machine. For example using an abrasive type fiberglass blade to polish a rusty old drying cylinder that has been put back in service.
In recent years, another very important reason for doctoring has come to light.
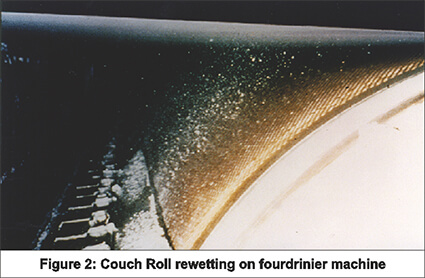
• Water removal: There are many areas on a paper machine where we can see rewetting. Installation of double doctors on couch rolls and suction press rolls helps eliminate this rewetting and improve paper machine runnability.
In most of the Indian paper mills couch rolls and suction press rolls do not have double doctors and we can clearly see a rewetting problem with most of these applications.
History:
Due to the surface texture of granite it is possible for dirt and fiber to get inside small cracks and fissures on the roll surface and get below the level of the doctor blade making it impossible to doctor off.
Similar to a foil blade on the fourdrinier of a paper machine, when the surface of the roll passes a doctor blade at high speed a partial vacuum is created behind the doctor blade. This vacuum pulls fine and dirt particles off the roll surface and they build up on the back of the doctor blade until they form “crumbs” that become heavy enough to fall off, go through the press nip and cause a sheet break. Sometimes these crumbs are actually sticky and don’t fall off but continue to build up until the blade actually starts to lift away from the roll, if there is a sheet break when this is happening it will cause sheet passing and potential damage to the doctor and press felt.
In addition to this problem, most paper mills were installing steam showers to try to increase machine production and to improve moisture profile control. This caused additional heat distortion problems for single doctors on press applications. The solution to all of these problems: Double Doctors
For press roll double doctors, the second blade holder and blade act as a crumb catcher to prevent “crumbs” from going back into the nip and causing a sheet break. A shower is installed between the two doctor blades and is directed behind the lead blade to prevent dirt build-up thus preventing the lead blade from lifting away from the roll. Cladding and insulation can also be included on this type of double doctor to eliminate any heat distortion problems associated with steam showers in close proximity. The end result of this type of double doctor is reduction of sheet breaks and improved efficiency. Many machines in India today are being upgraded to have a binip (or similar) press arrangement. Double doctors for these types of upgrades are a must.
Water removal Double Doctors:
Double doctors for water removal can be installed in many applications such as suction press rolls, suction pick-up rolls, blind drilled press rolls, suction pressure rolls for tissue machines, but the most common place is the suction couch roll application upon which we will base the following discussions. As mentioned above, water removal double doctors are not common in the Indian pulp and paper market and most couch rolls in this market do not have double doctors. Most machines have a simple rubber wipe as shown below. Please notice the amount of water that gets past the wipe and rewets into the wire and paper web.
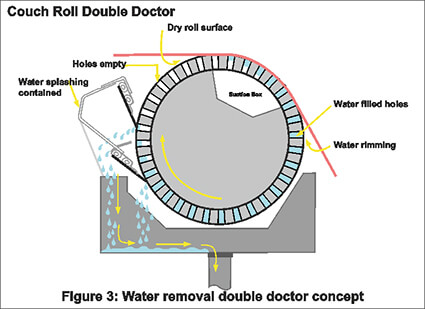
The same principles apply to water removal double doctors that apply to sheet removal press double doctors. The “foil effect” of the roll surface passing a doctor blade at high speed creates a partial vacuum behind the doctor blade. For water removal, this vacuum pulls water and fiber from within the drilled holes. Therefore, the lead doctor blade removes rimming surface water and cleans the roll surface, but it also creates a partial vacuum behind the lead blade which pulls water out of the drilled holes. A second blade is needed to remove this water ejected or pulled out of the drilled holes, hence there is a need for double doctor technology, for water removal.
Benefits derived based on the installations of water removal double doctors:-
• Rewetting is eliminated and most installations have experienced 1-3% increase in sheet dryness post couch with a double doctor as compared to the old rubber wipe mounted on the save-all.
• The rubber wipe i s not consistently touching with the same pressure therefore rewetting is inconsistent resulting in wet streaks. With a double doctor, all the water is removed therefore no wet streaks and improved moisture profile.
• A dryer stronger sheet entering the press section usually results in a reduction of sheet breaks.
• Some of the installations have resulted in improvement in wire life and pick up felt life.
• Partial vacuum created by the blades keeps the holes open and clean, with less risk of hole plugging which in some instances results in less time between roll changes.
Important Design Considerations: Doctor Support
When designing a doctor support, we normally try to design so that the blade line passes as close as possible to the centre of the doctor pivot point. This will ensure that the energy transmitted into the doctor passes through the stronger point of the construction and at the same time, minimizes the effect of turning moments around the pivot.
The centre of gravity should be located as close as possible to the pivot, so that the support always has a turning moment towards the surface of the roll or cylinder. This is to produce a very safe doctor installation. If holding restraints, such as pneumatic cylinder or turnbuckles are removed or fails, the doctor will rest up on roll surface and not fall away from roll causing possible injury.
A doctor beam is normally supported in two bearings at the tending and drive sides of the machine and it will have some natural deflection. Careful engineering calculations are required with any doctor design, to minimize this deflection and to ensure maximum allowable deflection on any support is not exceeded. In addition to minimizing the natural deflection in the design of the structure, it is important that the doctor beam is machined to compensate for this calculated (verified by measurement) deflection. It is also important to ensure that when the doctor is in its operating position that net deflection with respect to the roll surface being doctored is zero.
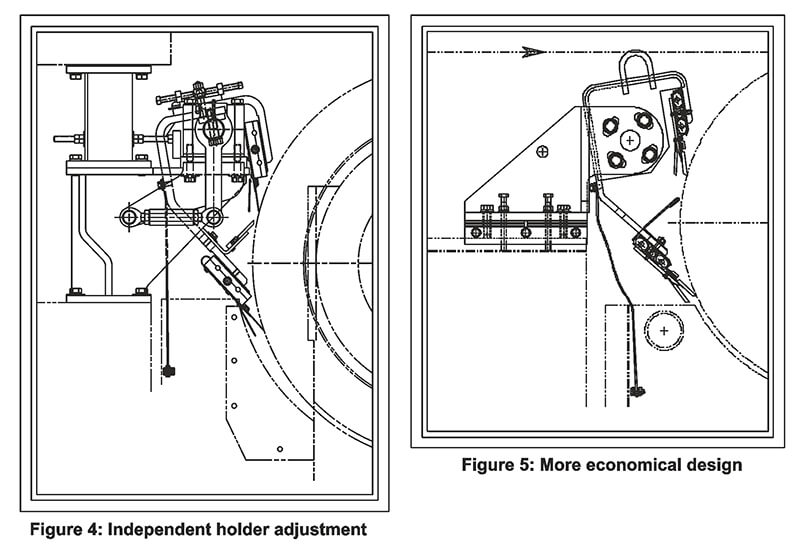
Another extremely important consideration regarding doctor support design is the natural frequency of the doctor. If the doctor natural frequency is the same frequency at which the roll rotates, then the doctor will vibrate and give very poor doctoring results and risk damage to the roll cover. To ensure the doctor will not vibrate due to the resonant critical speed of the roll, computer simulation is used to calculate the doctor deflection, moment of inertia, and natural frequency. The roll rotational frequency at maximum paper machine design speeds should never exceed75% of the doctor’s natural frequency.
Stress relieving of the support structure after welding and prior to machining is essential. This is usually done by vibration method.
Important Design Considerations: Blade Holders
For both sheet removal and water removal type double doctors, self contouring flexible type blade holders are a must. The “K” Flex double tube type holder is shown in figure # 6.
With this type of blade holder the blade is held by a flexible top plate with bolted on fingers on 2” (or 50 mm) centers. These fingers are individually pivoted from the bottom tube tray bolted directly on the machined surface of the doctor support structure. Between the bottom tray and the fingers, there are two air tubes on either side of a pivoting rod. Inflating the right hand tube (shown on figure 6) pushes the blade against the roll. Since this tube itself and the top plate are flexible the blade will self contour and follow exactly the shape of the roll surface. This is especially important on sheet removal applications as any point where the blade does not contact the roll could be a potential place where the sheet could get past the blade potentially causing a sheet wrap or even damage to a felt or to the doctor. By regulating the air pressure in the load tube we can easily adjust blade loading pressure to the desired level and ensure uniform blade contact pressure across the roll face. Exhausting the air flow from the right hand tube and switching air flow into the left hand tube (as shown on figure 6) allows the blade to lift away from the roll for easy blade changing.
Sheet removal positions, especially press doctors, are very demanding applications and often see the highest blade loading pressures of any doctor on a paper machine. It is critical that the blade holder is of very heavy duty design, while still maintaining its flexibility.
For water removal double doctors, the lower profile “finger on top” K Flex Klean design blade holder (see figure 7) is preferred. This blade holder operates exactly the same way as the K Flex. The only difference is we move the finger from the underside of the top plate to the top side. This allows the air loading tube to fully contact the underside of the top plate and the tube tray thereby completely sealing the blade holder and not allowing water to flow through the blade holder.
Conclusions:
Proper and effective doctoring is critical in providing good paper machine runnability. Double doctors are a cost effective way in realizing improvements in efficiency. The addition of double doctors to critical sheet removal press applications can result in a reduction in the number of sheet breaks and improved paper quality. Similarly water removal double doctors help to prevent sheet rewetting and improve sheet dryness at the couch, suction press and suction pick up roll applications.