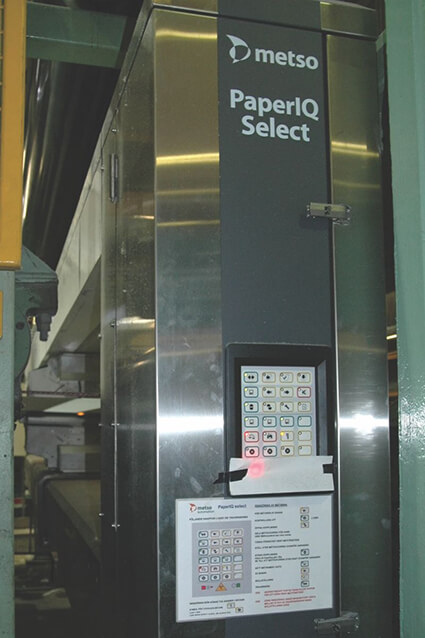
A new Metso PaperIQ Select system gives the mill more consistent quality, less in-mill waste and satisfied customers. Revamped caliper control strategy reduced sheeting waste by 60%.
It’s a typical story after twenty years or so. Paper machine quality control systems from the 1980s must be replaced because they are technically obsolete. The critical issue is that spare parts supplies are drying up and finding the experts to repair them is getting increasingly difficult. Many have retired. The costs of service are climbing and system failures are beginning to affect machine productivity and paper quality. Simply put, it’s time to change or face the consequences.
However, if an immediate leap in product quality or efficiency can be achieved at the same time, a QCS system replacement can be a win-win situation for a paper mill. A liability is removed and a more valuable process quality management asset replaces it. After all, there have been major advancements in QCS sensing and control technology over the past ten or twenty years. Added together the service cost savings, improved customer satisfaction and waste reduction and you have a good return on investment.
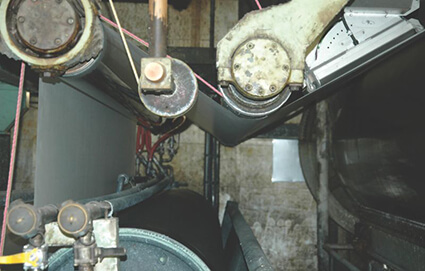
Nordic Paper in Säffle, Sweden has gained such a quality boost, and solved the service cost problems as well, as an aging 1980s-vintage QCS system on PM2 has been replaced by Metso’s PaperIQ Select system. The mill is now producing more consistent product quality with less in-mill waste and satisfied customers. The mill produces 30,000 tonnes per year of greaseproof paper with the totally chlorine free (TCF) fiber furnish supplied by an on-site sulfite pulp mill. Nordic papers have a wide range of end uses due to their resistance to oils, water, atmosphere and heat, creating a protective barrier for foods, cookware and food preparation surfaces. The papers find end uses as baking parchment papers, baking cups, food packaging, take-out food wrapping papers, and some specialty laminating and release papers.
Service cost driven, quality focused
The obsolete system on PM2 was replaced with a new PaperIQ Select system in October 2009. PaperIQ Select is Metso’s most recent offering. As reported by Jakob Isaksson, Automation Engineer for Metso Mill Services, solving the service problems of the old QCS was a primary driving factor behind the investment. Problems with dwindling supplies of spares, lack of service expertise and reliability-related machine downtime had to be solved. Metso Mill Services looks after all maintenance in the mill. Of course, modern QCS systems like PaperIQ Select are more service friendly than previous generations, with extensive predictive maintenance diagnostics and quick-change module replacement procedures. This lowers the long-term costs of ownership.
After evaluating competitive offers, the mill decided on the Metso PaperIQ Select system. A previous generation Metso PaperIQ Plus system with automatic color control was installed on PM3 in 2007, and that good internal mill reference helped to make the repeat order for PM2 decision clear and logical.
The system on PM2 comprises a scanner at the reel with grammage, moisture and caliper measurements and a single-sided scanning moisture measurement before the size press, where the moisture level is controlled between 6 to 7%. The PM2 system also includes a new Metso formation sensor, called IQFormation, which was installed on the reel scanner in March 2010. The development of this image capture and analysis capability was a significant advantage for Nordic Paper as formation is a key quality of their products, many of which are used for wrapping food.
In addition to alleviating the escalating service costs, the mill staff was focused on how a modern QCS could help them to make more consistent quality for their own on-site baking paper sheeting line and for the converting lines of external customers. White greaseproof baking paper and baking cup papers for muffins and cakes are the major products produced on this 4.2 meter width machine which has a design speed of 250 m/min. The grammage varies from 38 to 75 gsm.
Uniformly low air permeability is one of the primary quality specs of this heavily refined sheet, as it indicates good barrier resistance to fat and moisture penetration. Good formation and consistent moisture are key requirements, as is uniform crossdirection caliper. Mattias Wigelius, PM2 Production Manager, says. “Even profiles are very important for our converting processes and those of our customers. We produce some small rolls (1 meter width) and the converting lines are slowed down if the profiles across the roll width are not so good. Roll hardness differences cause wrinkles and there can be problems with the forming of baking cups.”
Machine direction grammage and moisture controls are coordinated with the system’s IQwetendMD model predictive controller. The system manages the cascade control of nine steam sections in the main and after dryer sections. Cross-direction caliper control was re-implemented in the new system by interfacing to an existing induction profiler on the machine calender.
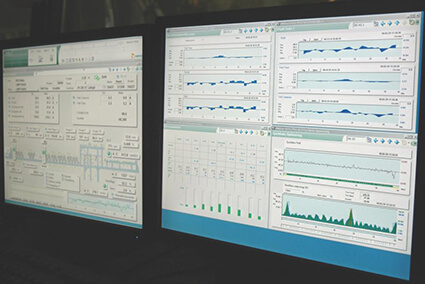
Better working effectiveness
One of the major goals of the project was to streamline and integrate the operator interface so the operators would have a much better view of the entire operation and would therefore control it better. Typical of older QCS systems, the operator interface and control operation was not consolidated in one place. The video interface station showed quality profiles, but the system’s supervisory control functions were distributed to panel controllers. This scattered and awkward operating method was resolved by removing the panel controllers and consolidating all measurements and controls in a unified DNAUse operator interface. Operators can now see cause and effect relationships for the paper quality and machine controls and their time trends. The more compact system also freed up much more space in the control room.
Wigelius says the better process overview has made a positive contribution to the operators working effectiveness. Profile resolution is better, so operators are more conscious of optimizing the sheet uniformity. “The operators see more and spend more time cleaning fabrics. It’s had a noticeable affect on quality,” he adds. Grammage changes are faster, as well.
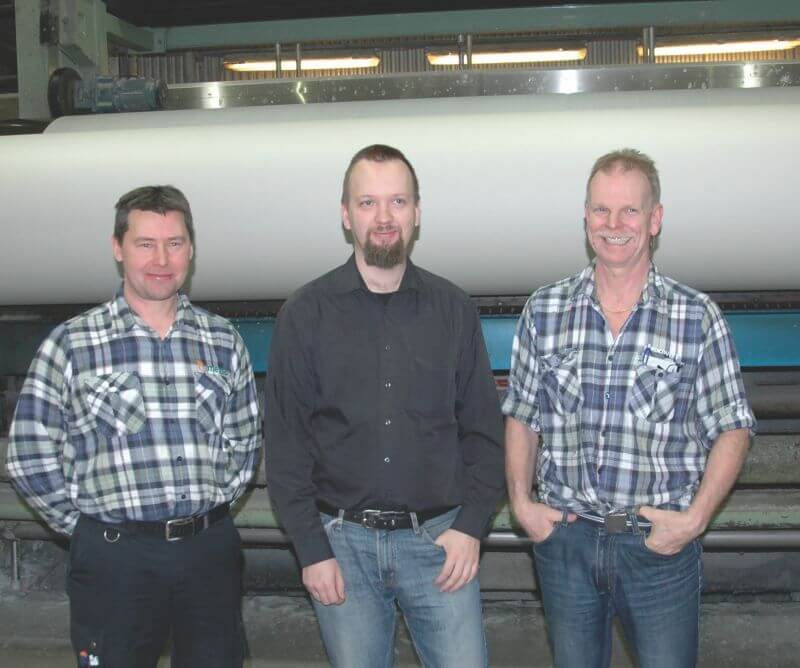
60% less sheeting waste; customers notice
The uniformity of the caliper profile has had the most significant impact on paper reel quality and how it converts into sheets. Wigelius states, “After the change of the system our sheeting department reports the waste for hard or loose edges totally disappeared and the reels are also much smoother than before. All this is due to the improved control with the new Metso system. The waste is down by 60% – about 6 tons per month less waste. Of course, our other (external) customers notice and are aware of smoother and better reels.”
Although the control of caliper is accomplished with the same number of profiler actuator zones, each control “cell” has much more information about the CD profile since sensors are faster and more precise and the CD resolution has improved by leaps and bounds from the 1980s. The IQwebCD control algorithm takes full advantage of this improved resolution and helps to recover paper quality quickly after a break or other upset. The Metso IQWebCaliper sensor has a CD resolution of 10mm, so across a web width of 4.2 meters there are 420 points which can be used for control. The result is faster and more precise control as seen by Nordic Paper.
The PM2 system started up quickly with paper quality established without delay. The excellent quality has been maintained, according to Wigelius, “I know our quality is better than before, and that results in lower broke in the mill and fewer claims.”
* Mark Williamson is a Journalist Engineer specializing in Paper industry based in Thornhill, Ontario, Canada