Riding high on technological advancements, Ecosure is planning to scale up its investment in Indore and set up one of the world’s largest molded fiber factories in the next five years. This was revealed by Mr. Gunjan Saxena, Director – Strategy and New Business Innovation, Ecosure Pulpmolding Technologies Limited and Mr. Mohit Kumar, Managing Director & Chief Visionary Officer, Ecosure Pulpmolding Technologies Limited, in a joint interaction with Paper Mart magazine.
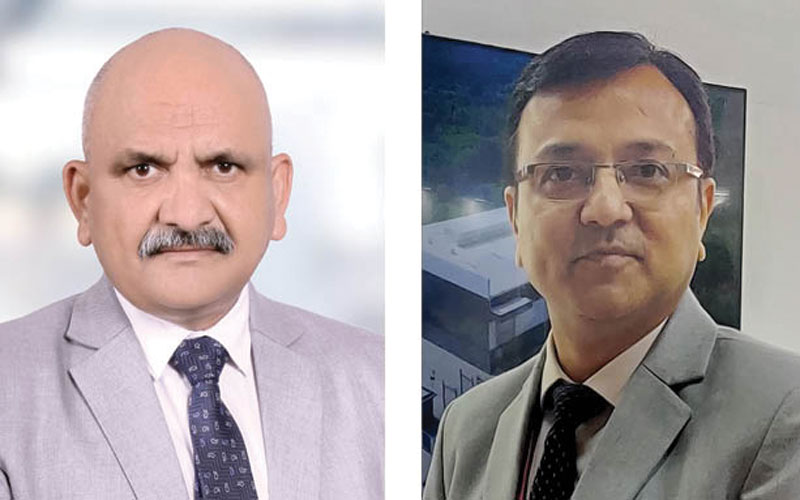
Paper Mart: Please share your business history, how it all began, your major milestones and achievements.
Gunjan Saxena: Ecosure Pulpmolding Technologies Limited was co-founded by Mr. Mohit Kumar, me, Ms. Kritika Tripathy and Mr. Kamal Rana in November, 2019. We are a leading manufacturer of pulp molding machines. We have so far manufactured and installed quite a good number of semi-automatic fiber pulp molding machines, while some are under process. We are a relatively young company, just about four-year-old. Our headquarters is in Greater Noida, Delhi-NCR. We also have an office in Ahmedabad for our export business and another in Bangalore. However, we are not limiting ourselves. We want to invest more in terms of infrastructure, resources as well as enhance our physical presence across India.
PM: Shed light on your acquisition of Indore-based Thermo9. What was the intent behind this acquisition & what benefits do you foresee arising out of this?
GS: It is about time that we focus on our global growth. We need a product which can really add value to the market. Our first acquisition was in Indore. They were good at making machines, had technology and proven working models. This company was Thermo9, which has now been rechristened as Thermo9 Eco-Pack LLP. Mr. Mohit is one of the founders in this company and Mr. Shankar Kinge is the co-founder. Thermo9 makes all kinds of advanced machines, with reduced power consumption. We manufacture fully automatic fiber former pulp molding machines that are all servo driven, trimming free and have an automatic stacking & counting system.
Our market for these machines is not in India. Though Indian buyers can make purchases, we are mainly targeting Europe because Europe requires labor free and energy-efficient machines. When they invest in green technology, they look for energy efficiency. We are targeting the European and American markets or any other emerging economies where fully automation or intelligent working is in demand. We are equipping ourselves to launch these new generation machines globally. We are also on the lookout for appointing agents or partners. We are open to make alliances with like-minded entrepreneurs across the world, to have factories globally.
PM: Throw light on the current scenario and future growth prospects of the Indian packaging & pulp molding industry. What are your future plans to reap benefits of the growing sector?
GS: We feel that this market will grow because there is a sudden surge in demand for markets, which don’t want to buy products from China. Market is growing for packaging. We are also planning to scale up our investment in Indore to set up the world’s leading molded fiber factory. This will happen in the next five years’ time. Before our IPO comes, we will be ready with the groundwork and infrastructure because demand brings investment in the market. We are waiting for the right demand in domestic markets.
Watch: Top Paper Companies 2023
PM: Please share information about your manufacturing setup and its capabilities.
GS: We have reached a certain level of capability in terms of having a lot of dedicated vendor facilities and sub-vendor outsourcing. Our assembly unit is under expansion and is doubling now. But we feel that we cannot expand much in a single location. So we are setting up unit 2 and unit 3 at Indore. These units will manufacture both manual and automatic machines. Currently, we make 20 pulp molding machines a month, which is a very small number, looking at the global scenario. Our idea is to double this figure within the next two years.
We are working on setting up a demo plant-cum-training facilitation center-cum-product manufacturing unit. We have already acquired a land of four acres in Indore to set up this greenfield project, which is targeted to be ready by October 2024.
This plant will also help us in doing some Research and Development (R&D), which is a continuous process. When you are going global, you should have machine development in terms of zero breakdown and zero maintenance. We will be using this plant not only for demonstration of our skills, but also to upgrade our technology and software, to find out the areas which need further improvement, and to replace certain futile designs. We are also working on finding a low-cost raw material alternative.
PM: Plastic ban is one of the key drivers of growth in the sector. However, a lot is there to be done on the legislation implementation side. What are your views on this?
GS: Single-use plastic is banned worldwide, including in India and this topic was raised in the recent COP 28 summit held in Dubai. The Plastic Waste Management (PWM) Rules made plastic illegal in July, 2022. However, the compliances and control on production are very poor in India. In the last one year, 70 new single-use plastic manufacturing units were installed, which is a very alarming number. We are very seriously working with the National Green Tribunal (NGT), some NGOs, related Ministries and other like-minded people to work parallelly with the government on this. There is a slowdown in the molded fiber industry and a boom in plastic pollution due to non-implementation of PWM rules. It’s a big threat for both the industry and the environment.
PM: What is your USP that sets you apart from others?
GS: We were earlier buying or rather sourcing machinery from Taiwan & China, and setting up the projects in India. During the pandemic, there was a lot of uproar about the Chinese products and technology. We then thought of making machines in India and developed indigenous machines. A lot of learning happened during the process, which helped us in making things faster. Based on their exposure in the European and the US markets, both the Chinese and the Taiwanese experts taught us about pulp molding. Our workforce got trained from the best of minds, which now reflects in their work. We have a fleet of well-trained service engineers, which help us in executing multiple turnkey projects in one go.
We have also installed the ERP software, which has helped us immensely in areas such as manufacturing and inventory management. It has become easier to ensure quality control, synchronize various work locations, and ensure real-time communication transactions. We did our own research and realized that learning outgrows faster in India because there is no point in reinventing the wheel. We have not reinvented the wheel, what we have done is ‘re-efficient’ the wheel, which means wherever the wheel was inefficient, we made it more efficient. Now all our machines are energy-efficient, made as per the European standard, and available at an affordable price.
Also Read: Bionova: Pioneering Sustainable Packaging Solutions
PM: Kindly tell us about your clients.
GS: Our major clients include Eco Greenware in Kichha, Uttarakhand; Multibiopack in Valsad, Gujarat; Bagazo Ecocare in Morbi, Gujarat; Ecosoul Home in Noida; Anuradha Green Collar Manufactory Private Limited in Jhajjar, Haryana, and Eco-Con in Bengaluru.
Satia Industries in Punjab purchased FiberFormer ECOFA 9570, a fiber pulp molded machine from us. They have now become our repeated customers.
We supplied a wheat straw pulp mill solution to Australia’s first fiber pulp molded plant. The export order involved installation of the first-of-its-kind all servo driven, trimming free, auto counting & auto stacking fiber pulp molded machine FiberFormer at COPAR Pty Ltd, supported by Innovation Club in Australia.
PM: Please share your future plans.
Mohit Kumar: We have finalized another patch of land in Madhya Pradesh, where we will set up our own demo plant, an agro-based micro pulp unit, in a completely integrated way. We will use rice straw, wheat straw or bamboo to make pulp and then it will be forward-integrated with a tableware manufacturing unit as well as a small unit for industrial packaging also. For this, we will make an investment of INR 30 crore. We want to showcase our capabilities.
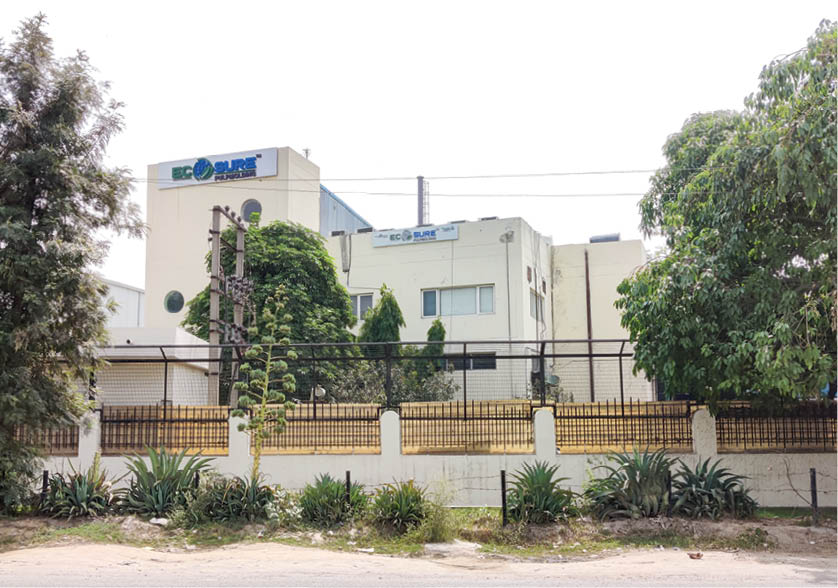