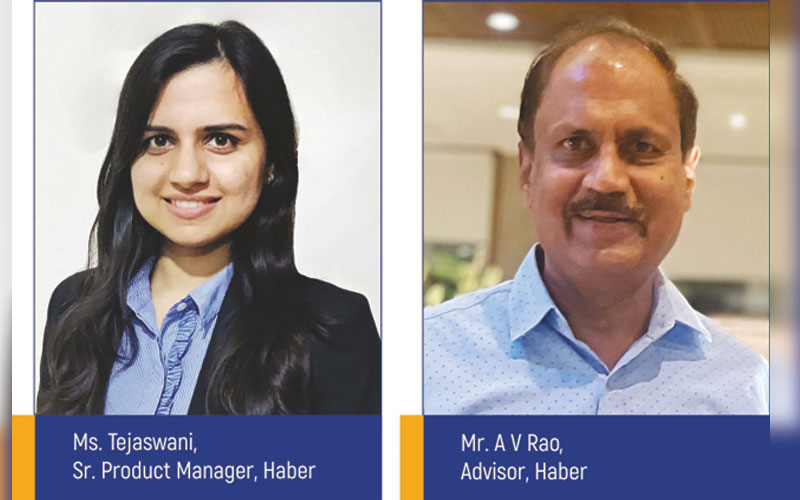
With a strong belief in transforming unstructured data to actionable intelligence through the power of AI, Haber focuses on bringing the latest technologies to bolster our industry, bringing deep industry and process expertise, and state-of-the-art, AI-driven automation software to maximize plant efficiency and output. Their latest product, Mt. Fuji, bridges the gap between IT and OT data by collecting real-time information. In an interview with Paper Mart magazine, Ms. Tejaswani, Sr. Product Manager, and Mr. A. V. Rao, Advisor at Haber, shed light on the latest opportunities in the paper industry and how Haber, through its AI-driven plant management services has become a catalyst in transforming this space.
Paper Mart: In the paper business environment, our industry deals with vast amounts of process data on a daily basis. Post the advent of Industry 4.0, where maximizing data potential has come to the forefront, what key challenges does the industry face? And how can we address these challenges?
A.V. Rao: Managing colossal amounts of data in the manufacturing sector poses considerable challenges, especially on an organizational level. The industry often grapples with maintaining physical copies of process transactions. This data will be of no use when one wishes to analyze a current problem on historical data. The data will be in an unstructured form and require digitization to do any analysis.
Tejaswani: Enter Mt. Fuji – a solution that can run through huge amounts of data in a jiffy and can provide real-time analysis and alerts. It facilitates informed decision-making, contributing to cost reduction and increased profitability.
Watch: JMC Paper Tech Launches New Subsidiary JMC Papers
PM: Can you share specific features or functionalities within Mt. Fuji that aids in real-time analysis and decision-making in the context of the paper business environment?
AV: Mt. Fuji reduces defects, enhances efficiency, and aids in planning. Its key benefits are cost-effective production, issue traceability through batch auditing, and the ability to use & standardize inputs from various sources such as PLC, DCS, ERP, MES, historians, and such.
TJ: The platform offers real-time alerts, total performance visibility through “Golden Batch” comparison, and increased process stability, amongst other features, helping users across all levels & departments in an effective and efficient decision-making process.
PM: You mentioned the concept of a “Golden Batch” in Mt. Fuji. Could you provide more details on what constitutes a Golden Batch, and what are its benefits in optimizing process functioning?
TJ: The “Golden Batch” in Mt. Fuji, represents the gold standard of production. It serves as a benchmark for continuous improvement in the manufacturing process, continuously enhancing analysis. With Golden Batch comparison, Mt. Fuji optimizes process functioning, providing a reference point for comparison with individual batches and conventional multi-batch charts.
AV: Mt. Fuji will enable a comprehensive diagnosis covering a wider area of the processes and their parameters. It will enable employees to improve productivity beyond human capabilities.