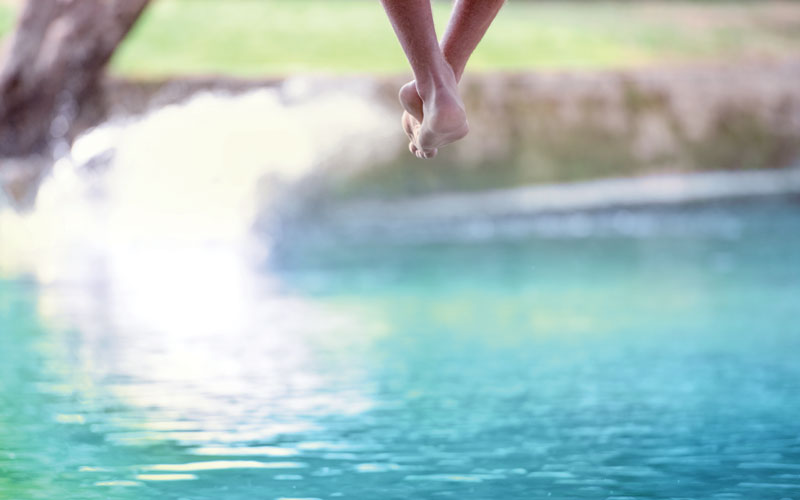
In a pulp and paper mill, water is needed in almost every part of the process, whether the facility is digesting wood chips, making fiber slurries, or washing the machinery and rollers. About 85 percent of pulp and paper industry water use is for process water, which is contaminated during the manufacturing process. Expectedly, pulp and paper mills have been under increasing pressure to adapt their processes and ensure they’re efficient enough to reduce their waste.
The State of Water
Water scarcity is becoming endemic. On average, 10 percent of the global population lives in countries with high or critical water stress, says the United Nations. It underlines poor ambient water quality in low-income countries being often related to low levels of wastewater treatment. Back in India, government think tank NITI Aayog maintains that about 70 percent of India’s surface water resources are polluted.
In this backdrop, demand for greater accountability from water intensive industries like thermal power plants, textile, pulp and paper, steel and fertilizer is rising. In a pulp and paper mill, water is needed in almost every part of the process, whether the facility is digesting wood chips, making fiber slurries, or washing the machinery and rollers. About 85 percent of pulp and paper industry water use is for process water, which is contaminated during the manufacturing process with sediments, effluent solids, chlorinated organic compounds, organic halides (AOX), and chemical oxygen demand (COD) and biological oxygen demand (BOD) contaminants. Expectedly, pulp and paper mills have been under increasing pressure to adapt their processes and ensure they’re efficient enough to reduce their waste.
Consumption
At present, 73 percent of the paper is produced from recycled fiber (RCF)-based mills while only 18 percent of production is from wood-based mills and the remaining 9 percent is from agro-based mills, says The Energy and Resources Institute (TERI). “The scenario was almost reversed in the year 1970, when production from wood-based industries was the highest i.e., about 84 percent and RCF was minimum i.e., about 7 percent.” The industry, however, has come a long way in reducing its water consumption compared to the historical consumption values. Despite the advancement in technologies and best practices, there is significant room for further improvement in water management.
Our annual water consumption is 43,80,000 m3 (i.e. 30 m3/ton of paper), says Mr. Pawan Agarwal, Managing Director, Naini Papers Limited. Before the implementation of the water charter in 2012, its consumption was 80-100 m3/ton of paper. During 2012-2013, the Central Pollution Control Board implemented a ‘charter for water recycling and pollution prevention in pulp and paper industries in Ganga River Basin’ in five identified clusters of pulp and paper industries located in Uttarakhand and Uttar Pradesh. The MD asserts that the company had worked ‘a lot on implementation of green technology and maximum recycling of treated effluent’ and it was able to reduce the same to 30 m3/ton in the subsequent years. On how it was achieved, he says that the company first identified the areas with fluctuating water consumption and took necessary measures to control the same on a daily basis. We have set benchmarks for water consumption for all major areas of the mill and adhere to the same, he explains.
As for ITC-Paperboards and Specialty Papers Division (PSPD), it adopted the Spearheading Adoption of Alliance for Water Stewardship (AWS). Its Kovai unit, it says, is the second facility in the world and the first in India to be awarded the AWS Platinum level certification. The company maintains that its total water intake for 2022-23 was around 30 mn KL, and specific water consumption has been reduced by 9 percent over the baseline year of 2018-19, despite its expanded in operations.
Pakka Limited, according to Mr. Shashi Verma, Environment Head, uses state-of-the-art Micro Plate Settler (MPS) technology to separate reject fibers from paper machine backwater and then reuses the clean water back into the paper machine low and high-pressure shower. Additionally, we have also installed MPS in the wet washing section and moulded machine plant, he stressed.
Watch: Top Paper Companies 2023
Mitigating with Innovations
“Companies are adjusting their goals, to be better stewards of the available natural resources and ensure their businesses are able to adapt to an ever changing landscape. This entails more investment in innovations and solutions. With respect to the freshwater usage in the plant, we follow various control measures like closing the water loop to more than 80 percent, reducing the freshwater usage by reusing the rich and lean back water from the system for various dilution of stock and even some chemicals, and also optimizing the water usage by timely replacement of the shower nozzles,” asserts Mr. SVR Krishnan, Executive Director, Khanna Paper Mills.
The use of MPS and DAF technologies in paper machines and wet washing areas, which has led to a significant reduction in wastewater generation, allows us to reuse water at its source, Mr. Shashi shares. “The usage of low-conductivity water in the cooling towers results in higher COC which further leads to less blowdown/purge. The water is passed through an in-house developed reject RO membrane-based RO system before being passed through the softener plant. Additionally, we’ve introduced a COD load-wise wastewater treatment facility to further improve the reusability of the treated wastewater.”
In its efforts to help mills become more water efficient, companies like Valmet, Kemira and Krofta Engineering, to mention a few, play a crucial role. “Krofta Engineering has been instrumental in assisting pulp and paper mills in India to achieve their water efficiency targets,” says Mr. Raghvendra Khaitan, Managing Director, Krofta Engineering. Dissolved Air Flotation (DAF) Technology, Anaerobic Reactors, MBBR (Moving Bed Biofilm Reactor), Sludge Dewatering Solutions are some of the solutions it caters. With over 12,000 installations worldwide and four decades of excellence, it empowers industries with innovative water treatment solutions. “Our commitment to sustainability and environmental stewardship make them a valuable partner for the pulp and paper industry for achieving water efficiency goals in Indian paper mills,” Mr. Raghvendra stresses.
On the innovations Xylem caters to help mills reduce their water footprint, Mr. Alexis Metais, Pulp & Paper Key Account Manager, Xylem, states, “Xylem supports pulp and paper mills with pumping, treatment and metering solutions for both intake water and effluent. Our technologies help to reduce color, TSS and COD in ETPs (Effluent Treatment Plants) and meet the strictest environmental discharge norms.” In India, Xylem has been collaborating with ITC-PSPD in the Bhadrachalam mill. In 2008, ITC-PSPD installed ozone bleaching in its existing fiberline and a second new bleach plant. Both lines were fed with a single ozone generator supplied by Xylem. “The ITC project was the trigger for Xylem to establish in India a service team dedicated to ozone, supporting the commissioning and maintenance of our numerous customers in different industries and water treatment plants. After 15 years of operation, ITC recently replaced its 2 bleach plants with a new Single Bleaching Line, again with ozone,” he adds.
Also Read: Integrated Strategy has Made ITC PSPD Water Positive for 21 Years
The Harvesting Approach
In addition to the deployment of innovations to minimize water footprint, most mills consider water harvesting as a cornerstone of their sustainability efforts. Emami Paper Mills maintains that it approaches rainwater harvesting with ‘utmost seriousness’. Recognizing its pivotal role within our water management framework, we prioritize it as a means to conserve and optimally utilize water resources, the company shares. ITC-PSPD states that over the years it has created rainwater harvesting potential through extensive investments in its Integrated Watershed Development Projects. The programme promotes the development and management of local water resources in moisture-stressed areas by facilitating community participation in planning and implementing such measures, whilst building, reviving and maintaining water harvesting structures.
Here, Naini Paper shares a different aspect. The aquifer inside the factory site is charged, therefore rainwater harvesting is not possible, says Mr. Pawan. However, the company has constructed ‘20 nos. gabion structures in the rain drains for high recharge of rainwater in the upper region of Ramnagar and Haldwani’.
Though we are in a less rain prone area, we seriously consider rainwater harvesting and its usage, as it is in its purest form, Mr. SVR Krishnan informs. “We have made two big U/G tanks inside the plant at two locations for collecting the rainwater and storing it. This covers the majority of the areas in the plant and we are in the process of making a few more at strategic sloped locations inside the plant. This stored water is used for the make up water at many locations and also for the localized fire hydrant system, without depending on the main fire safety pumps.”
The Obstacles
Desirable and something most want to achieve, reducing the water footprint of a mill is easier said than done. “Reduction in water consumption leads to increased levels of pollutants in the waste water which poses serious problems during treatment and makes the treatment system complex. In addition to this, obviating the impact of increased use of waste or treated waste water on quality of product is also a big challenge,” says Mr. Madhukar Mishra, Managing Director of Star Paper Mills.
Due to the large volume of water required for manufacturing paper, the major challenge is the high initial investment and subsequent high operating costs of the water treatment systems, shares Mr. Ashish Gupta, Director Operations, Emami Paper. However, the constraints of handling large volumes remain with older paper machines, which are still in operation, he adds.
According to Mr. Rohit Pandit, Secretary General, Indian Paper Manufacturers Association (IPMA), several paper mills in the country have got the best available global technology in the field of wastewater treatment to be at par with the rest of the world. He, however, asserts that technology upgradation continues to be a challenge across the board, especially for the smaller paper mills. “Indian paper mills operate in a very challenging environment of high input and raw material costs and have to face intense competition in the domestic market from duty-free imports flooding into the country. In such a scenario, investing in high-cost water efficient technologies is a huge challenge for paper mills,” he stresses.
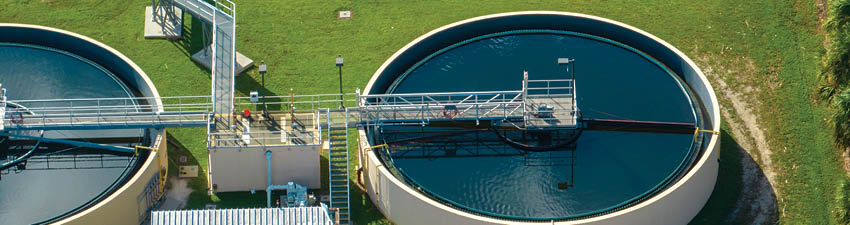
Targets and Future
The industry has made significant progress. Specific water consumption by the industry, especially the organized paper mills in the country, has come down significantly over the years. “Earlier the industry used to consume 200 cubic metres of water to produce a tonne of paper. Now, the integrated mills have reduced that to around 40 cubic metres. There is a concerted effort to bring it down further, IPMA’s President Mr. Pawan Agarwal was quoted. He attributed it to the mills’ access to the best available global technology in the field of wastewater treatment.
Emami Paper’s water usage reduction target is 10% by 2025-26, says Mr. Ashish. To achieve this goal, the company aims to employ a multifaceted approach: Efficiency Measures, implementing water-saving technologies and practices across operations; recycling and reuse, such as treating and repurposing wastewater; process optimization, continuously assess and refine production processes; and monitoring and reporting, establishing robust monitoring systems to track water consumption metrics.
We plan to reduce water consumption by 20% from the present level, says Mr. Madhukar. To achieve this target, Star Paper’s, he explains, first approach will be to optimize the fresh water consumption and increase recovery of condensate and flash steam.
Khanna Paper also aims to further bring down its water consumption by another 20% by installing the additional aerator and the enlarged tertiary treatment with MBBR, UF and Nanofiltration and installation of RO plant of suitable capacity in the second phase, according to Mr. SVR Krishnan. “We are also looking into various aspects of bio-treatment, innovative mechanical filtration and the best way for reducing the COD and TDS levels in the final treated water, which will make our plant a good MLD (Minimum Liquid Discharge) Plant, in this part of the country.”
In this futuristic landscape, Xylem sees mills becoming more and more water efficient, better closing the loops and treating recovered water. But recovering water means also treating it, Mr. Alexis states. “Considering the drive of Indian pulp and paper companies for environmental solutions, our Xylem portfolio as well as the reach and expertise of our Indian colleagues, I strongly believe the next 5 years will bring successful collaborations of Xylem with the Indian pulp and paper industry to solve water.”
Mr. Raghvendra feels that the future of water management in the pulp and paper industry is a critical concern, and he maintains that it will centre around water use and reuse, effluent discharge monitoring, and sustainability and responsibility.