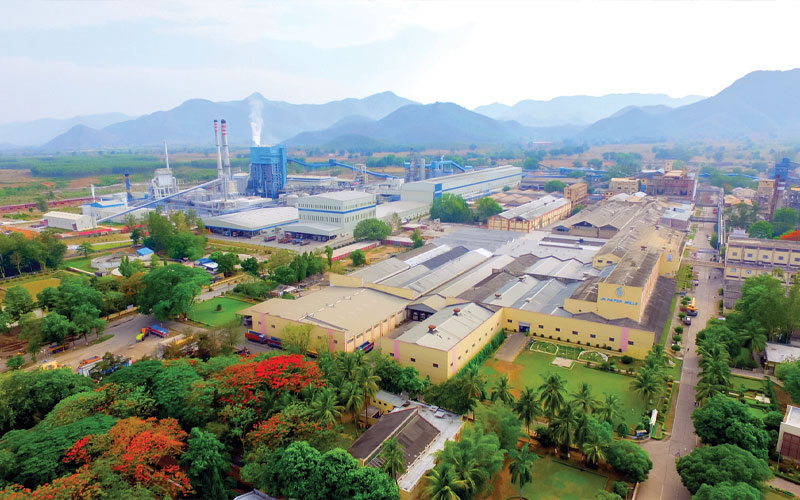
With the rising concern for water stress, JK Paper has always been committed to conserving water. The company has adopted proactive measures to focus on water resource development in irrigated areas. JK Paper is not only redefining industry standards but also shaping a brighter future for generations to come. It has taken significant steps to reduce its freshwater consumption and effluent generation per metric tonne of paper.
Water covers 70 percent of our planet, and it is easy to think that it will always be plentiful. Estimates suggest, some 1.1 billion people worldwide lack access to water, and a total of 2.7 billion find water scarce for at least one month of the year. Water plays an important role beyond being a critical component of the pulp, paper, and packaging produced. Climate change is altering weather patterns and water availibility around the world, causing shortages and droughts in some areas and floods in others. In this backdrop, efforts made by water-intensive industries have come under close scrutiny. In a pulp and paper mill, water is needed in almost every part of the process, whether the facility is digesting wood chips, making fiber slurries, or washing the machinery and rollers. Hence, it becomes important for the mill owners and other stakeholders to take significant steps to achieve water efficiency in their operations. However, deciding where to start can be challenging
Being a major player in the paper industry, JK Paper has been working towards achieving water efficiency all across its units. By embracing advanced technologies, process innovation, and efficient resource management techniques, they have made significant strides in reducing their freshwater consumption and effluent generation per metric tonne of paper. The company has achieved exceptional milestones in terms of water conservation, setting industry benchmarks with some of the lowest consumption rates in India’s wood-based paper sector. Some of the exceptional unit- wise initiatives taken by the company are highlighted below:
Unit CPM, Songadh, Gujarat
- Adopted emission control technologies such as electrostatic precipitators, scrubbers, bag filters, closed conveyor hoods, etc. to help capture and treat pollutants before being released into the atmosphere.
- Installed advanced treatment technologies in its effluent treatment plant infrastructure to improve the treatment and disposal of wastewater generated during production.
- Recycled primary sludge in low-grade paper making, reintroducing the wastewater into production.
- Implemented water recycling and reuse systems to treat and reuse water from various processes, reducing the overall demand for freshwater and minimizing wastewater discharge.
- Introduced efficient water management practices (internal and external water audits), which optimized water use.
- Identified water loss or inefficiency areas through the water audit team, implementing water-saving technologies such as low-flow fixtures and equipment.
Watch: Top Paper Companies 2023
Our company has achieved exceptional milestones in terms of water conservation. Our water consumption at Unit JKPM, Rayagada has reduced to 27 m3 per ton of paper through water saving schemes.
Unit JKPM, Rayagada, Odhisa
- Reduced water, steam, coal, and power consumption per ton of paper over the years by implementing various water and power-saving schemes, reducing GHG emissions and becoming carbon positive.
- Commissioned a tertiary clarifier for reduction of color in treated effluent.
- Promoted plantation across 168,000 Ha, involving 100,000 farmers in Odisha, Andhra Pradesh, West Bengal and Chhattisgarh under the ‘Clean Development Mechanism’, enhancing farmer revenues through carbon sequestration.
- Created temporary sand bank bunds to divert water towards its side from the opposite bank.
- Ensured emissions and effluents remained below prescribed norms.
- Reduced water consumption to 27m³ per ton of paper through water-saving schemes.
- Adopted electro-static precipitator in all boilers, scrubbers, dust extraction systems, dry fog systems and bag filters. The air emissions were monitored through AAQM stations and real-time data was transmitted to relevant Pollution Control Boards.
Also Read: Naini Papers: Embracing Technology with Innovation
Unit SPM, Sirpur, Telangana
- Adopted waste reduction measures (disc filters in paper machines) to minimize fiber loss and freshwater consumption.
- Installed high-pressure, high-efficiency fluidized bed combustion boiler for co-generated power.
- Installed a non-condensable gas collection system to collect non-condensable gases and incinerate them in the lime kiln.
- Installed log washing system on yard stacked wood to reduce dust emission in chipper area.
- Supplied treated water to two neighbouring villages of 250 acres.
- Installed sewage treatment plant for treating domestic effluent; the generated effluent was used for green belt development.
- Installed centralized refining system resulted in power saving of around 576 kW (36 kWH/T of paper).
- Improvement in lime purity from 78% to 83%, leading to a reduction in chemical consumption.
- Water consumption reduced from 100 Cu.m/tonne of paper in FY22 to around 45 Cu.m/tonne of paper.