After commissioning its first 400 TPD multilayered kraft paper plant in 2016, Paswara Papers Ltd. started working on a new kraft paper and board unit, whose first phase of 40,000 tonnes to start commercial production in December 2018. The overall project of 140,000 tonnes annually is expected to be fully commissioned in 2020. After completion of the new project, the combined capacity of the company would stand at over 265,000 tonnes annually. Notably, the company is exporting more than 70 percent of its produce from the plant commissioned in 2016.
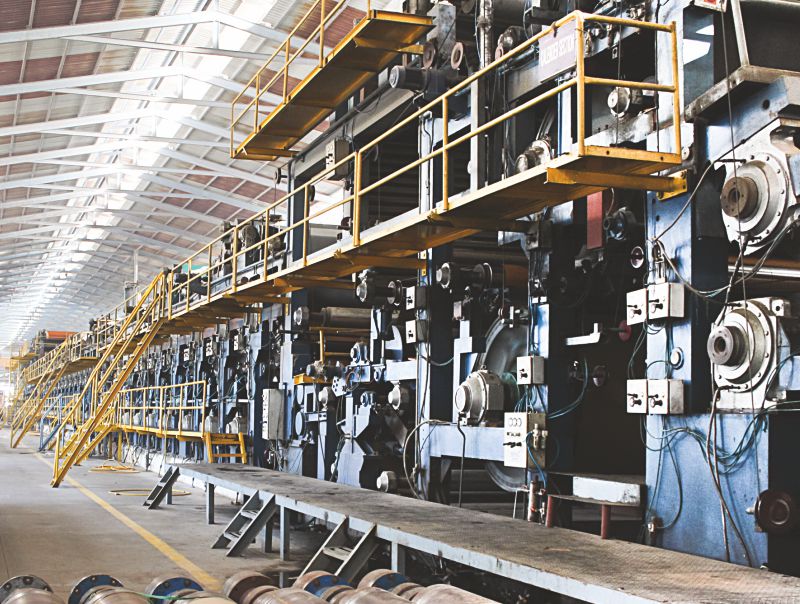
Paper Mart recently interviewed Mr. Arvind Kumar Agarwal, Chairman & MD, Paswara Papers Ltd and Mr. Vinod Agarwal, Director, Paswara Papers Ltd. on the latest developemnts at the company and the new project. Excerpts:
Paper Mart: Brief us about Paswara Papers Ltd and the multi-layer Kraft mill that you commissioned in 2016.
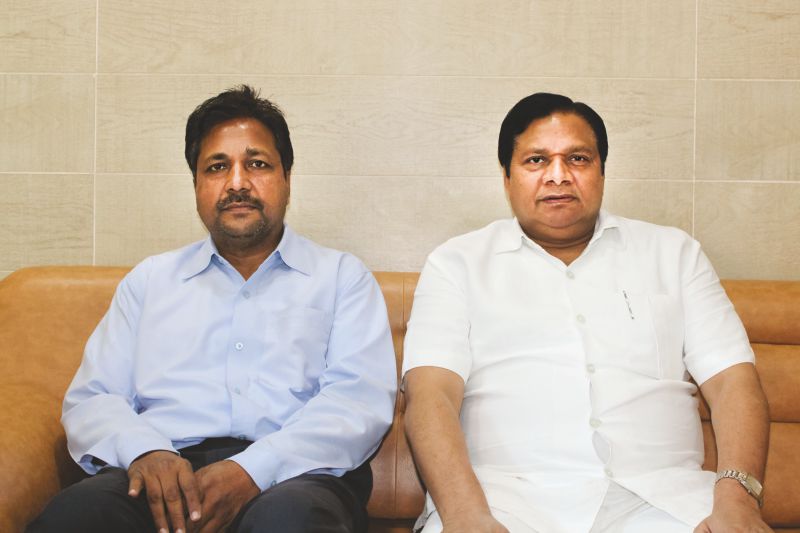
Mr. Vinod Agarwal, Director, Paswara Papers Ltd.
Vinod Agarwal: Paswara was started in the year 1984. We started with the manufacturing of strawboard with a capacity of 10 TPD. The strawboard was used in making bangle boxes in Firozabad, UP. Thereafter, in 1990, the group installed machinery in the same place for manufacturing media kraft paper with a capacity of 10 TPD. After the machines and technology went obsolete, we decided to stop the production on the two machines in 2016.
The company envisaged a mega Greenfield Project in the year 2012 under the Uttar Pradesh Udyog Nivesh Nidhi. In 2014, we signed an MoU with the UP Government in UP Investors’ Conclave at New Delhi to establish a mega project with an investment of INR 400 Cr. The project was completed in 2015 while the commercial production began in October 2016. This probably is the swiftest execution of a project in India which gave us a state-of-the-art multi-layered karft paper mill, equipped with the latest equipment from around the globe.
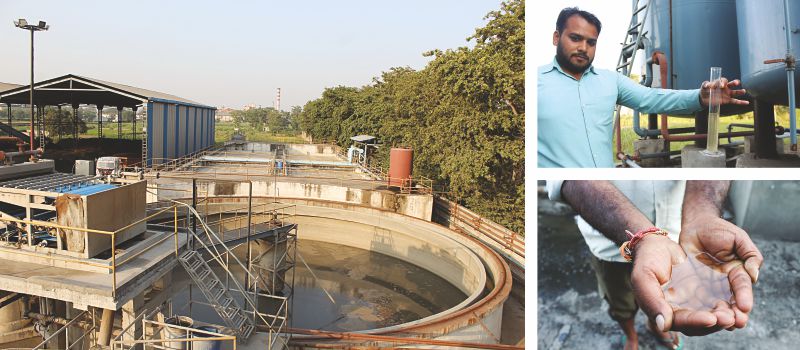
The manufacturing capacity of the mill is 400 TPD, making us one of the biggest multi-layer kraft paper mills in India. The unit in the coming times will also produce white-top coated multi-layer kraft liner for packaging of garments, pharmaceuticals, food products, and such other products used in daily life. The 70 percent of the production is being exported to countries like China, Malaysia, Canada, and Sri Lanka.
PM: Is it true that Paswara is investing in yet another project at the site?
VA: Yes! We are going to invest INR 400 Cr in under the 2017 scheme of Uttar Pradesh Udhyog Nivesh Nidhi. An MoU has been signed in the month of February (2018) with the current CM of Uttar Pradesh. Mr. Narendra Modi, who was also present at the Investors’ Summit, emphasized the fact that investors must commission projects as soon as possible. The UP Government has approved only a few (around 4-5) such projects; Paswara is one among them. The work on the project is already underway, and an investment of about INR 30 Cr has already been made.
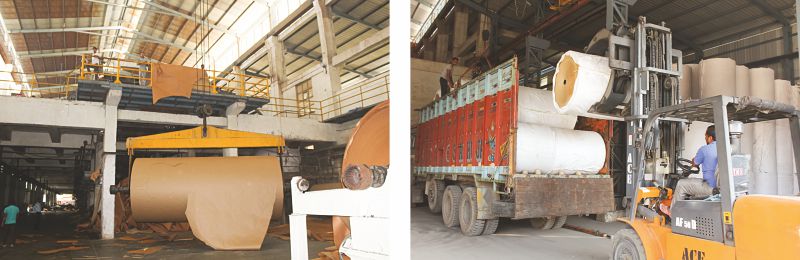
We will initially make MG kraft paper and kraft board, about 40,000 tonnes per annum, whose production would hopefully begin by December 2018. Soon after realizing this production, we would start working on making around 100,000 metric tonnes of high RCT paper by the year 2020.
Arvind Agarwal: In other words, the new project is divided into two phases and the total capacity is planned to be 140,000 TPA. The 40,000 TPA of production (for MG kraft paper and kraft board), which was locked for the first phase, has been started with an investment of INR 30 Cr. The commercial production for the first phase will start by December 2018. In the second phase, the remaining 100,000 TPA of capacity for high RCT kraft paper will be generated. The second phase will come to closure by 2020. It may be possible for us to increase the investment or add more capacity during that time.
Our total capacity will become 265,000 MT per annum after the completion of the new project. The discussions for benefits are ongoing with the State Government. The concessions from the Govt. include reimbursement of GST on a quarterly basis. The government has been a huge help throughout the project, who directed the officials to resolve project related issues immediately when reported by the people involved in the mega projects.
PM: Can you specifically tell us about the technology that you have installed in the new mill?
VA: The plant that came into operation in 2016 was equipped with high-tech machinery, mostly imported from China but based on the best and latest European technologies. We are happy with the machine as we are able to make some of the best quality kraft paper, which our international buyers are quite satisfied with. In the pulp section, we have installed three poly disc filters which are an useful addition, quite helpful in fiber recovery. The process water from paper machine, passing through the poly disc filter via side hill screen, results in recovery of valuable fibers to be reused. Though these filters are a bit costly, recovered fiber compensates that by decreasing the total manufacturing cost. Also, the fiber waste will not go in the water stream, where maximum pollution is caused by the fiber particles. Moreover, this technology has helped us achieve the zero liquid discharge.
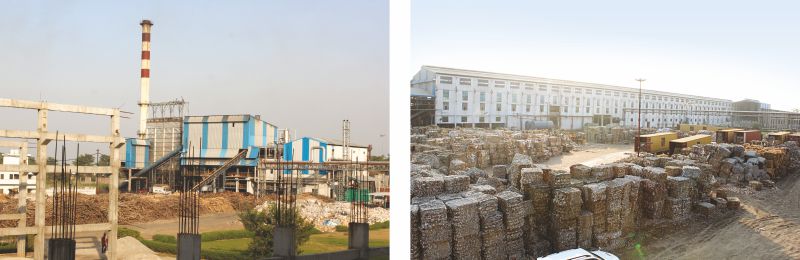
Coming to the environment, I would say Paswara is one the most committed players on the front. We have a well-functioning, two stage ETP in place with pre-primary and primary treatment mechanisms for the effluents from the mill. The water quality after the treatment is flawless and we use 100 percent treated water back in our processes, even in high pressure showers. Moreover, for curbing air pollution, we have installed an electrostatic precipitator (ESP) in our 6 MW captive power unit to filter and remove fine particles, like dust and smoke, from a flowing gas.
On the automation side too, we are not behind. Machines are based on DSC and PLC, and the manual intervention in mill is minimal. There are some semi-automation based technologies in our existing mill, but we have decided to replace them with full-automation based technology. In the new mill too, we are going to go fully-automated. I am glad to share that we are working in sync with the most updated technologies for the pulp and paper mill.
PM: Tell us about the quality of the kraft paper that you are making in the new mill.
VA: As far as multi-layer kraft paper goes, our quality is truly at par with our international peers, one reason why we are exporting over 70 percent of our produce. We can even export 100 percent, but to cater to the needs of the Indian market is also important to us. Therefore, we are supplying 30 percent of our production domestically. Our exporting strength vindicates we are making products of international quality.
We are making high strength multi-layered kraft paper. It has a total of three layers with colored top layer. People demand a golden yellow color which is good for printability and makes the surface smooth. The GSM range of the kraft paper we make is 125-300 GSM. Our machine, however, is capable of making paper up to 400 GSM. But the market demand is from 125-300 GSM. Besides, the BF range of the paper is 18-35.
PM: How have you been preparing yourself to make paper that meets RCT based specifications?
AA: The BF and GSM concepts were popular in the Indian market up till now. Gradually, as the international markets only work on the RCT based paper, the Indian market is also adapting to the trend. India will see this trend becoming the norm in the coming years. The foreign countries have high-speed machines and so does Paswara Papers. It is therefore easy for us to export most of our material as we conform to the quality standard requirements of the international customers. The other mills in India are not able to export much, couldn’t install high tech machines and construct a well-established mill because they lack true technical knowhow, which we are good in.
PM: Can you be a bit specific about the demand based quality difference between India and overseas countries? How do you cater to such demands?
AA: Earlier, we were working according to the Indian quality standards. As soon as we opened our products for the export market, we started receiving international inquiries and visitors from abroad. The buyers from abroad came and stayed with us for quite some time in order to help us develop the quality they desire. They developed the quality of our products according to their requirements. The way they helped us in the quality development process really amazed us. We thought of producing the same quality products for the Indian market too.
The moment we started exporting our products, we targeted to position our mill up to the level of the international mills and that we eventually did. Today, we can happily say that we have one month advance orders. We now don’t cater to the Indian and international market separately. We rather started covering the international market with our international quality which automatically benefitted the Indian market.
PM: How did the international customers help you in the quality development?
AA: The international customers stayed with us and participated in evolving our production process. Many of our customers visited our mill and stayed for 3-5 days — helping us with the setting of the pulp section; guiding us thoroughly about how to do cutting and packing of the paper; telling us how many joints should be there in a roll; and what should be the diameter of the roll. We used to make rolls with smaller diameters as machines in the Indian mills are smaller in size. The international machines, on the other hand, are much bigger producing rolls with big diameters. They directed us to increase the dia size and made the packing as per their own specifications.
Moreover, these customers taught us other things as well such as the loading of the containers be done in their supervision. After the loading of the containers, the batch of goods was dispatched. It has now been more than four months since we began dispatching their orders. Had they not been satisfied, they wouldn’t have made the repeat orders. The order repetition means your product has gained momentum in the market. This learning from international customers has really helped us improve our working. They educated and informed us about the things we weren’t aware of previously. Besides, they paid us 30 percent more than what we usually get from the Indian market. That’s why we agreed for the alteration in our production process. Nevertheless, it has ultimately benefitted us.
PM: Where are you exporting right now? Also, tell us about demand growth in the packaging sector?
AA: We are exporting to China, Malaysia, Sri Lanka, and many other places. Someone from our team has also gone to the UK for meetings. So, we may soon export to the UK as well. There is a lesser number of mills in the UK but the country has a vast number of corrugators. Our existing capacity has already been booked. The proposed capacity will be supplied to the UK for sure. Although we are trying to set our business in the UK, we cannot dilute our current markets. We have to create a balance within our businesses. In India, we are supplying our products to big names like Bikaner and Patanjali.
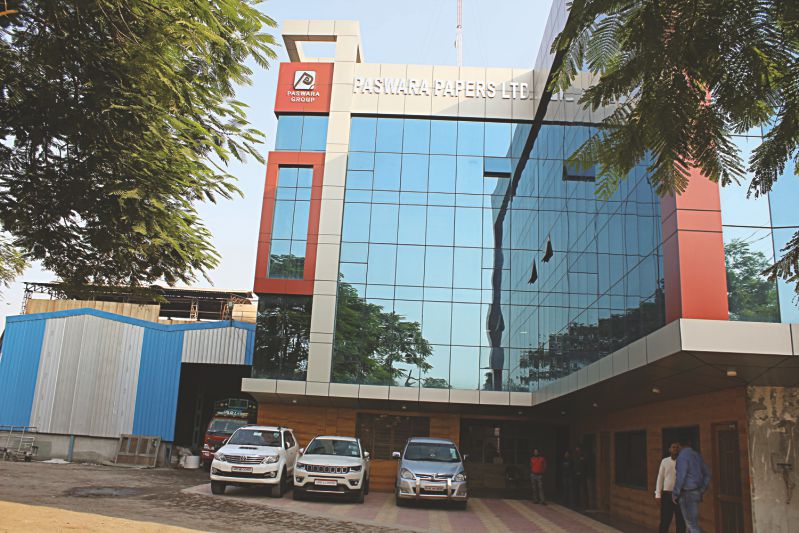
After entering the export market, we realized there is a humongous demand in packaging and it is increasing every day. The packaging material is used in everything. Paper is fast replacing plastic. Thus, we see a big push in the demand in the packaging sector. Every year the packaging paper demand is increasing by 15 percent. The person who is putting the latest technology and maintains his infrastructure neatly will be successful in the export market. The buyer will only buy from you when he is completely satisfied with the production process of your mill.
PM: Will the export market remain consistent as it is now apparently? What do you think?
VA: The selling price in the market is fixed. We have to work according to the market and its demand. We need to see how to decrease the input cost and reduce the overall cost of production. The reduction in cost will happen when we will work on the economies of scale. That’s why we have put a 400 TPD plant in which the cost of production and running costs are to be less enabling us to compete well in the market. This is a buyer-driven market, so volume plays a big role.
The countries that used to import paper from China are now facing a shortage of paper because of China’s wastepaper import ban. We are now targeting these countries – the countries which we never explored in the past. We would try to enter those markets and develop them more in future.
PM: Tell us about the raw material scenario at Paswara Papers.
VA: We import the wastepaper as well as use the domestic material in our mill. We import the wastepaper because of its quality; the fiber of imported wastepaper is stronger than the domestically available one. After using strong fiber in our products, we are able to make the quality equivalent to that of international standards. The ratio of the imported and domestic raw material is 50:50.