The PrimeScreen X is ideal for all types of screening applications, regardless of the raw material.

May 5, 2019
Well-known with over 5,400 installed pressure screens in numerous stock preparation lines worldwide, ANDRITZ presents the latest evolution in screening – the PrimeScreen X. The innovative design of the new screen builds on the successes of the widely valued ModuScreen family, but offers innovative key benefits. Improvement in energy efficiency, screening performance, and maintainability are significant.
According to Sampo Köylijärvi, Global Product Manager for RCF screening and flotation systems at ANDRITZ, “The development of the PrimeScreen X has been ongoing for three years – from the initial engineering design, to prototyping, through to two years of mill testing in the most demanding OCC applications.”
Improved design and innovative key benefits
Top-feed inlet of stock: The design takes advantage of gravity to quickly remove heavy contaminants. With this top-down design, abrasive contaminants, which cause wear to the rotor and screen basket are not forced to flow slowly upward through the entire screen. Top-down also improves the removal of light rejects, preventing the accumulation in the feed area and extending the life of wearing components.
PrimeRotor and foils for increased efficiency and lower power consumption: The screen can be equipped with the new PrimeRotor, which improves screening efficiency and reduces energy consumption by up to 25%. The PrimeRotor foils are interchangeable with any other ANDRITZ foils and the rotor could be installed in any screen type available on the market.
Easier maintenance: Changing baskets and rotors is a time-consuming work. The PrimeScreen X uses a uniquely designed drive flange to connect the rotor to the hub, so maintenance or replacement is quick and easy. The innovative clamping system to fix the screen basket allows for faster changes.
Optimized screen basket height-to-diameter ratios: The PrimeScreen X is designed so that the optimized screen basket height-to-diameter ratios meets with the requirements of different furnishes and applications. This helps to reduce the thickening factors and leads to a better control of fiber loss as well as to reduced potential for plugging.
Results from the first installation
After extensive internal testing in ANDRITZ’s Stock Preparation Pilot Plant, the first commercial installation of a PrimeScreen X50 was as a primary coarse screen in a 1350 bdmt/d OCC line.
The main targets of the installation were defined as follows:
- Improve quality
- Minimize energy consumption
- Achieve longer screen basket lifetime
The PrimeScreen X50 was installed in parallel to an existing conventional screen from another supplier and began operating at full production from the start, using the same rotor tip speed, flows and consistency settings that were in place for the existing screen.
The rated capacity of the X50 was 705bdmt/d. First samples of the PrimeScreen X compared to the competitive unit are shown in Table 1.
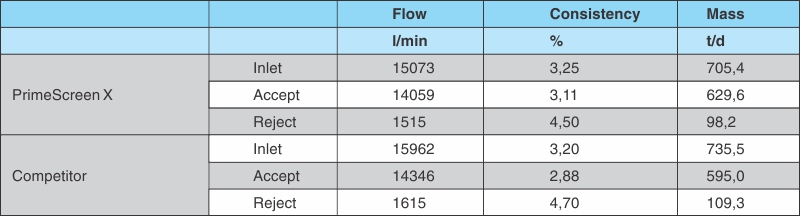
The competitive screen that was replaced, had 250 kW installed power and operated at ~69% load (Table 2). The PrimeScreen X had 132 kW installed power and operated at ~78% load. This reduced energy consumption by 40% (173 to 103 kW) over the existing competitive screen.

The screen rotor in the PrimeScreen X was an ANDRITZ LRs design. The ANDRITZ rejector screen basket (0.6 mm slot) actually had 21% less open area than the rejector basket in the existing screen. Even with this constraint, the PrimeScreen X operated with 5.5% higher capacity and had remarkably better screening efficiency – especially in stickies removal (77.5% stickies reduction for the PrimeScreen X v/s 56.4% for the existing screen).Side-by-side comparative data for the twoscreens is shown in Table 3.
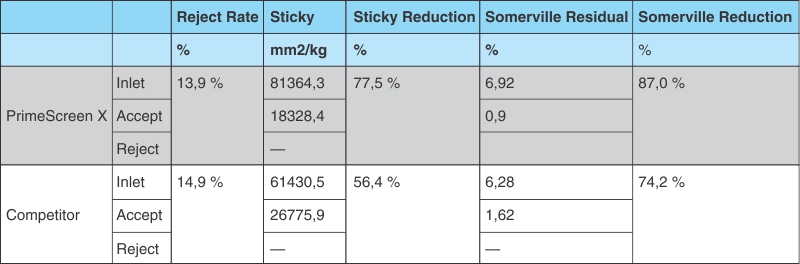
The PrimeScreen X is a natural evolution of the ModuScreen pressure screen family. Targets for the development were to improve both the energy and screening efficiency, while making the unit easier to maintain.For this mill’s coarse screening process, the average screen basket life in the existing screen was 6-8 months. When the PrimeScreen X was opened up for inspection during a shutdown, 10 months after installation, slot widths and profiles were excellent. The underside of the rotor, too, was exceptionally clean. Since that initial inspection, the mill ran the screen basket 22 months in the PrimeScreen X before changing it.
The PrimeScreen X is exceptional for all screening applications – brown and white grades – recycled or virgin – including coarse, fine, broke, thick stock and fractionation duties.