Forbes Marshall, a leading technology provider for energy efficiency, safety, productivity, and environment monitoring, has launched several new products in steam engineering. The company is also one of the first ones to come up with an IoT backbone both in hardware and software to enable digitization of factory data, specifically process data, to be monitored and diagnosed. With a range of gas analyzers and dust analyzers from CODEL International, its UK based group company, Forbes Marshall can now better serve the global pulp and paper industry.
Paper Mart recently interviewed Mr. D.K. Kuvalekar, Director-Technology & Enginnering, Forbes Marshall. Excerpts:
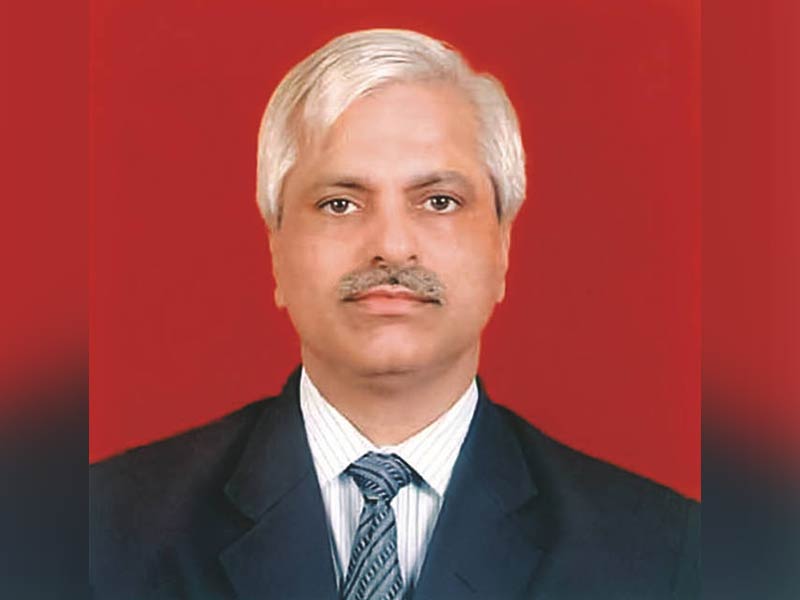
Enginnering, Forbes Marshall
Paper Mart: Tell us some of the new developments at Forbes Marshall in general and for the pulp and paper vertical in particular. Is this true you are planning a new factory? If yes, kindly let us know some project details and the key areas of focus for the planned facility.
Forbes Marshall: Forbes Marshall is constantly innovating on its product range to provide customers with energy savings. Our steam and condensate systems now run on a new proprietary platform called the ER series which provides optimal performance at affordable costs and provides an IoT backbone for data analysis and monitoring. We were the first company to introduce boilers connected to the internet, much before IoT became a buzzword and we have developed several products that are cloud connected, with a view to improve maintenance schedules and system uptime.
We have invested in a new factory that recently won the most outstanding factory design award instituted by Institute of Architects India
We have invested in a new factory that recently won the most outstanding factory design award instituted by Institute of Architects India. We are embarking on a new expansion plan that will further enhance our production capacity to meet the growing demands of India and international markets.
PM: What are some of the key milestones that your award winning mega facility has covered since its inception? Have there been any further investments in this facility?
FM: We have embarked on a phase 2 expansion plan to double our steam products and systems production capacity to serve our customers in major markets and bring in enhanced operational effectiveness.
PM: As a pioneering facilitator of energy efficiency, safety, productivity, and environment monitoring, tell us some of your newest additions in innovative product line, especially in steam engineering and environment monitoring for the pulp and paper industry.
FM: We have had several new products in steam engineering like the compact thermodynamic steam trap range, flash jet pumps that minimize flash steam venting, a new range of SG iron control valves for accurate pressure and temperature control with inbuilt smart positioners. Thus, one could say that Forbes Marshall is constantly innovating on improved products that would deliver enhanced performance for a faster paper machine or pulp section with lower energy consumption.
We are in a better position to help the pulp and paper industry address stringent pollution control norms with our range of gas analysers and dust analysers, not just for CEMS but also for process stacks, from CODEL International – UK, which is a Forbes Marshall group company.
We have an IoT backbone both in hardware and software and our EverSense platform enables digitization of factory data and specifically process data to be monitored and diagnosed.
We are in a better position to help the pulp and paper industry address stringent pollution control norms with our range of gas analyzers and dust analysers, not just for CEMS but also for process stacks, from CODEL International – UK, which is a Forbes Marshall group company.
PM: Forbes Marshall has designed some of path-breaking equipment for the process industry under its domain of utility management and instrumentation. Give us a brief outlook how these products changed the conservation approaches in the recipient industry over a period of time.
FM: The pulp and paper industry needs an integrated approach to energy savings and we have always strived to ensure that we focus on the entire system rather than on individual products. Integrated approach means that we look at all aspects of plant operation – production rate, quality, safety and energy consumption and then look at interconnected parameters, thereby devising the most optimal solution. The deep study of the overall steam network together with the process enables us to provide a solution that exactly matches the needs of the particular plant or subsystem. The emphasis on a clean factory through reduced environment emissions is also part of our offerings to the pulp and paper. Thus Forbes Marshall is uniquely placed to offer integrated solutions that encompass all aspects of the plant.
The pulp and paper industry needs an integrated approach to energy savings and we have always strived to ensure that we focus on the system rather than individual products.
PM: How closely do you think the steam or energy conservation/efficiency is related to overall environment conservation strategy? What are some of the critical ways and means Forbes Marshall can suggest the industry to adopt expeditiously or urgently?
FM: Energy and Environment is very closely related and linked. This is obvious. The average energy intensity of Indian pulp and paper is declining at a rate of @2.5% and if the global benchmarks have to be met we need to accelerate the pace of energy intensity reduction to about 5% on an average. This is not easy but will need sustained efforts by all stakeholders –the mills, the technology suppliers and the policy frameworks. Every mill needs to commit itself to a 10% energy reduction year-on-year, and make it their priority for attention and investments. The obvious wastages need to plugged forthwith. Energy efficient best practices based on available technologies with attractive paybacks, which may need investment, need to be adopted. The global next practice can be taken up once the first two stages of implementation have been covered. Thus every mill needs to define a 5-year energy reduction roadmap, which needs to be diligently followed, with expert advice where needed.
The average energy intensity of Indian pulp and paper is declining at a rate of @2.5% and if the global benchmarks have to be met we need to accelerate the pace of energy intensity reduction to about 5% on an average.
PM: Given the increasing regulatory pressure on the environment side, the pulp and paper industry may be keen in knowing what Forbes Marshall can do to help them through its complete package of pulp and paper environment monitoring?
FM: Rather than reacting to regulatory pressure, I would suggest proactive engagement with local governments and pollution control authorities to implement what is needed, be it CEMS for stacks or water or effluent treatment issues. We do have a comprehensive range of solutions that enable our customers measure what they are emitting both into the air and water bodies. We can help them conduct a comprehensive audit of their current systems and then make recommendations for meeting the new benchmarks set by the authorities, and more so in terms of international best practice. Our wide range of CEMS analyzers for gases like SOx, NOx and CO and dust analyzers, in addition to our water quality analyzers for BOD, COD, TDS, pH and conductvity and DO2 form a part of modern plant needs.
Rather than reacting to regulatory pressure, I would suggest proactive engagement with local governments and pollution control authorities to implement what is needed, be it CEMS for stacks or water or effluent treatment issues.
PM: This is a buoyant phase for the Indian pulp and paper industry, full of Greenfield projects, expansions, rebuilds, and other project activities. How is Forbes Marshall doing in terms of growth in supply of its products and systems? Kindly give some details!
FM: As mentioned earlier, Forbes Marshall is in close connect with the growing demands of green field projects and brown field expansions. We also help existing plants to get more output with less energy from their current assets. We have gained a deeper understanding of the needs of the pulp and paper industry owing to our close association, and this has helped us design and engineer complete integrated systems for many of our customers. We provide solutions right from concept and design stage, to engineering of these systems right up to project implementation. This is done completely in house, with our proprietary technology developments. Our extensive sales and service network covers almost every paper cluster and enables our customers benefit from our quick response teams that have been deployed across these pockets.
PM: Tell us your views on the present growth of the Indian paper industry and its continuance. Has this growth been able to tap on the latest technological trends, or could it do better?
FM: The Indian pulp and paper industry surely has good potential to expand as the per capita consumption of paper is bound to rise as economy scales. The only question is how do we scale up? The need to consolidate and establish world scale capacities with good progressive management of energy and environment issues is essential. Managing costs well while maintaining quality of the product will catapult the Indian pulp and paper sector to scale global heights for the right reasons, and not just as a low cost substitute.
The Indian pulp and paper industry surely has good potential to expand as the per capita consumption of paper is bound to rise as our economy scales. The only question is how to we scale up?
Many mills are engaging global suppliers to design and engineer their plants and thus I do see an openness in the Indian pulp and paper industry to adapt to the latest technology.
PM: You may add something, something which we might have left untapped by above questions?
I think Indian paper sector could do well to establish their local Indian standards for energy efficiency and benchmark them against global values. The fact that many mills use local raw materials and this causes deviation from global standards.
FM: I think the Indian paper sector could do well to establish local Indian standards for energy efficiency and benchmark them against global values. Many mills use local raw materials for production, causing deviations from global standards. First knowing the worst and best energy efficiency values for Indian mills would be the starting point to assess internal practices. These standards need to then align with TAPPI standards and mills need to create a roadmap to reach those standards. Thus if the Indian industry shares performance data especially from an energy perspective, it would initiate a culture of collaboration in the journey towards implementing best practices. The CII Paper Tech and IPPTA seminars indeed contribute a great deal to this objective. But what is needed to close the loop is documentation of these standards.