Ruchira Papers is known for of its value-added W&P products and has carved a distinct niche in the market for its agro-residue based products including kraft paper. The company is setting up another W&P plant in Punjab in order to augment its capacity and add more firepower to its product range. The new plant is to be commissioned within 3 years.
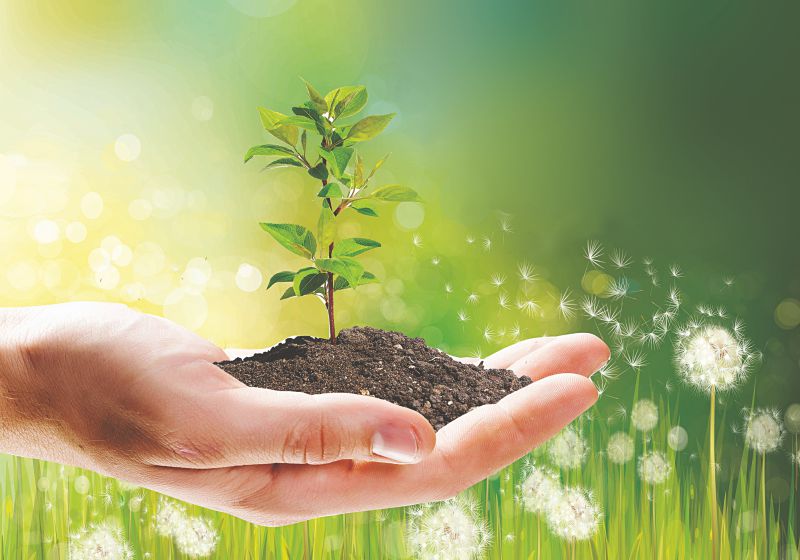
Paper Mart recently conducted a detailed interview with Ms. Ruchica G Kumar, V.P. – Marketing, Ruchira Papers Limited to know the companies experiences in the past and priorities in coming times.
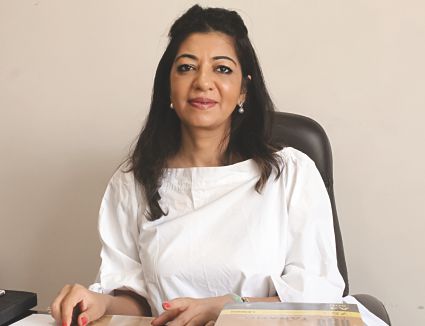
Paper Mart: Tell us about the journey of Ruchira Papers so far. What have been the major landmarks of the company?
Ruchica G Kumar: It was in the year 1980 when three young men, my father Mr. Subhash Garg, his younger brother Mr. Umesh Garg, and Mr. Jatinder Singh, came together and decided to do something out of the box. The three were all very different personalities, but they came up and thought of Ruchira Papers. It was a modest start. We started with just 7 tonnes per day of kraft and used agricultural waste as our raw material.
We thought of diversifying to writing-printing and set up a mill for the same in the year 2006. I would say venturing into writing-printing was the best step taken by the company. It was a bold step that has paid off well in time and Ruchira has carved a very particular niche for itself in the W&P market.
Because of the divine blessings, path of passion, dedication, and honesty of the three founding directors, the small manufacturing unit producing 7 TPD of Kraft paper has emerged today as professionally run 400 TPD paper of writing-printing and kraft range of products. The kraft paper production is about 230 TPD and W&P paper is about 170 TPD.
PM: Ruchira Papers is to set up a Greenfield project in Punjab. Brief us about the project and the time it would take for coming into production.
RGK: Yes, we are in the process of putting up a plant in Punjab because of the close proximity of raw materials in the region. The company has proposed to set up a new W&P paper plant of 100,000 TPA (approx) in Chamkaur Sahib, Punjab along with a 25 MW cogeneration power plant for captive consumption and a chemical recovery plant. The total land requirement is 191 acres and presently we are in the process of acquiring the land and have applied for the environmental clearances. We have almost acquired 90 percent of the land. The production will take around 2.5 years.
Investing in W&P paper was a planned decision. We already have two machines of kraft. We initially considered everything and then decided to strengthen our hands in what we are doing already. Being in the field, we know about the demand of the W&P paper and it is going to grow steadily in the coming years. The demand for W&P segment is expected to grow at a CAGR of 4.2 percent and reach 5.3 million tonnes in FY19. Also, there are no new mills coming up for writing printing in the coming years, an ideal situation for us to think of increasing our capacity in W&P paper.
PM: What were the challenges that Ruchira has gone through especially on the environmental front?
RGK: Initially, it was difficult to even make the corrugators try our kraft paper because we were unknown to the market and the people back then were unwilling to put their faith in paper made out of agricultural waste. The corrugators were not even willing to try it. I remember the three partners travelling pan-India to convince people to at least try the paper first. Starting from something as basic as that, it was of course a challenge! The quality also had to keep on getting better with time.
Speaking of the environmental compliance challenges, we have been more than good with that. Of course, we have timely inspections but the environment and government agencies know that we are doing everything by the book. Environmental issues are the major concern for the survival of any pulp and paper producing company. Any expansion or Greenfield project must be based on environment-friendly technologies.
PM: Please elaborate more on your measures to address various environmental challenges which you face as a paper manufacturer?
RGK: In present market scenario, where awareness towards the environmental protection is increasing day by day, the viability of any environment-friendly concepts stands vindicated amply by wise customer preferences and increased regulatory pressure. Our paper is made from agricultural waste and waste paper that means we are conserving forest that helps in making a clean environment. Besides, norms and standards prescribed for an agro-based mill are met thoroughly by Ruchira by incorporating sufficient changes in process, practices, and technology from time-to-time.
Moreover, we have taken care in every section to eliminate/reduce the pollution at generation points itself. Chemical recovery system takes care of black liquor from both the pulp mills. Agricultural residues (biomass) are being used as a fuel such as rice husk, bagasse, forest waste plants, etc. The company believes in conservation of water and result of which is that the consumption of water per tonne is way less than the norms as prescribed by the Pollution Control Board for the paper industry. Coal is replaced by upla, pith, leaf cutting and rice husk, which are used as fuel in the boiler for making steam to conserve natural resource.
Ruchira Papers has also demonstrated deep commitment to preserving the environment through various energy conservation practices. CII (Confederation of Indian Industry) energy audit team conducted a Detailed Energy Audit of Ruchira Papers including all thermal and electrical equipments. Various energy saving proposals were suggested and since then the company has been in the process of implementing the proposals in a phased manner. Implementation of some of the proposals has resulted into reduced power consumption (per tonne of paper) which has added to the profitability and economic viability of the company. The company was also accredited with an appreciation letter from CII for contributing to the power conservation. Besides, the company has set up and properly maintained essential effluent control facilities as per the norms of the Central State Pollution Control Board.
PM: Being an agro-based mill, Ruchira Papers has never shied away from investing in right technology at right time. Tell us a short story of your technological journey as a papermaker.
RGK: Ruchira Papers always believes in generating more from less and is consistently focused on achieving better efficiencies. We have always invested in latest technologies at right time. During the year 2015, we did de-bottlenecking that resulted in an increase in production as well as improvement in quality and better economies of scale. During the last quarter of FY18, we have completed the modernization of kraft unit and W&P paper unit which has enabled us to produce the value-added products. So, Ruchira Papers always believes in investing in the latest technologies.
Our Plant is based on an environment-friendly concept. As said above, since the inception of company in 1983, we have followed all the guidelines and regulations of environment law prevailing in the country. In 2008, we started our conventional chemical recovery plant to recycle all the Black liquor (main pollution creating substance in the pulp and paper Industry) generated in our pulping process as a spent liquor from cooking of raw materials.
PM: Tell us about the raw material composition. Also, do you face any limitation because of the raw material supply?
RGK: We basically use bagasse, wheat straw, and sarkanda, which all are seasonal. The procurement of the raw material is never too difficult for us. Our raw material suppliers have been with us for a very long time now. They are very loyal to Ruchira. We don’t have any issue with the supply, pricing, or quality of the raw material. The farmers or contractors come to us and give us the raw material. Besides, there are 3-4 sugar mills in the vicinity who supply bagasse almost uninterrupted. In the kraft unit, we use waste paper as well. For writing-printing, we use agro-based raw material and about 3-5 percent of softwood pulp, which is imported. The percentage varies as per the paper quality requirement and season wise availability.
Therefore, the raw material scenario for us is thankfully unchallenging. We don’t struggle with that at all. We procure enough raw materials as per the requirement. Even though the price of the raw material fluctuates, the availability remains good. I have also learned that the raw material challenge is not a unified challenge, i.e. it varies from region to region, from mill to mill.
PM: Tell me the continuous improvement in the quality as well as branding of your product both in the kraft side and writing printing side.
RGK: I will start with writing-printing first. You must know certain notions about agro-based paper prevailing in the market, especially the complaints about dust in the paper and that the paper is not meant for bulk production like in big publishing houses. With new technologies, we have been able to actually make the big publishing housing use our paper now. The bulk has also seen significant improvement with appropriate changes in technology and raw material composition. The market feedback has been good, and the demand has also risen proportionately. The company of late has succeeded in raising its products quality on crucial parameters like brightness, opacity, bulk, etc. We have an in-house lab for quality control, assisting us reach the desired quality parameters.
The paper quality evolves with the market preferences, and vice versa. For example, at one of the conferences, a dealer who was really impressed came to us and urged to do the ARSR test on our paper for the possible use in stiffener segment. To our surprise, we matched the standards of the stiffener test. We didn’t even think of getting into that segment at first, but with feedback from the consumers, we realized that we can expand into a lot of new markets. Stiffener paper is exclusively designed to perform in converting applications that go in various applications, e.g. for soaps packing.
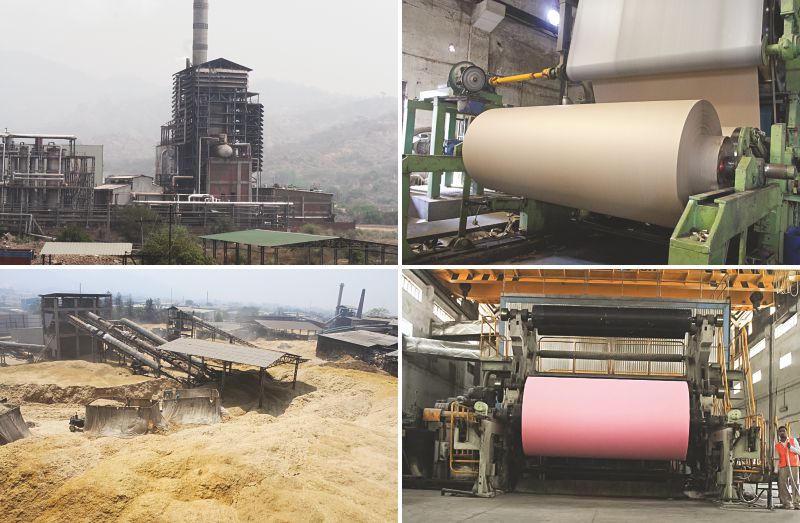
Talking about the products, I would say the supply of our product range is fairly immune to seasonal fluctuations in raw material availability. We have a wide range of popular products, with different names signifying our culture and environmental pro-activism. Instead of using modern names, we used names which connect more to our Indian roots. Our product KORA is used for notebooks, textbooks, stationery, note pads, and registers. SAFEDA is for high-quality notebooks, textbooks, stationary, and notepads. KARIGAR is high bulk paper used for printing, drawing sheets, cards, notes, and labels. GEHUA is for brochures, annual reports, diaries, paper bags, and envelopes. MELA is for color printing, bill books, brochures, leaflets, advertising material, spiral notebooks, bill books, handbills, scrapbooks, and lottery tickets. MELA is for high compression kraft paper, tube grade (high ply bond), corrugated board boxes, paper bags, paper drums, and ream wrappers. TARANG is a multipurpose office paper for copiers and printing.
It is the earthiness and earth-friendliness behind Ruchira’s paper which makes it a different proposition in the market. We really want the consumers to feel that. Big companies now prefer sustainable paper products made from sustainable and renewable resources, like ours. We in fact are in talks with many such companies, who actually don’t want to leave any carbon footprint.
PM: Ruchira Papers use agricultural residues as a raw material in the papermaking process. How does the paper industry should take a stand for the environment?
RGK: Ruchira Papers is producing paper from agro-waste with sustainability of environment as its main motto. We are helping the environment by using agro-residues as our raw material, which were otherwise burnt causing immense pollution. Now, the farmers are motivated to sell this residue on a commercial basis, which in turn is also helpful in their economic growth.
Environment, as it is now, can’t be ignored any further. The paper industry, including other manufacturing industries, must make their CSR beyond paperwork and lip-syncing. We as paper industry need to reform our process and practices by investing adequately in technology and earth-friendly actions in order to maximize the output with the least input, and making it sustainable too. Ruchira has been doing it and would continue doing as mandated by standards and self-will.
PM: Import has been a consistent issue in the Indian market. Tell me exactly about the threats from imports. Do you really think that these imports will really hamper the Indian production scenario?
RGK: As per Directorate General of Commercial Intelligence and Statistics (DGCIS) data, total imports in FY17 were up 36 percent over FY16. Far as ASEAN imports were concerned, there was a surge of 67 percent in FY17 numbers over FY16. Imports reached 1.1 million tonnes in the first half of 2017-18 as against 650 thousand tonnes imported in the first half of 2016-17, indicating an increase of approximately 69 percent. The increase in imports is mainly because of nil duty for ASEAN countries. Of course, this is bad for domestic players if they can’t sell their products in the market because of price competition. However, I don’t see Indian players struggling to sell their products. The import is only filling the gap which our capacities can’t as the consumption is much beyond what we produce today, especially in W&P & newsprint.
Moreover, the prices of imported paper have really shot up. That’s why the Indian paper is becoming more economical for people to buy. The import this year has not increased. The import demand has not increased as much as Indian paper demand has increased. Thus, the pricing of the Indian paper is going to become better because the demand for it is increasing. The imported papers are not cheap anymore. This is resulting in less dumping. Also, the quality of the Indian paper is improving day-by-day.
PM: Tell us about the performance of Ruchira in the past few years.
RGK: Ruchira has been performing very well in the last few years. The profitability of the company has been growing. When you improve your product, the market remains there for you already. We have no problem in selling our products. At any point in time, we have sufficient orders. We are very comfortable with our market. In coming times, there should be a good future for the industry as well as for us because there is going to be a huge shortage of paper.
PM: Which segment do you think is going to grow in India?
RGK: The duplex is going to grow because of e-commerce. There of course would be growth in the W&P segment & copier segment. The reason for that is vast untapped market in India, where education still has to make inroads.
The newsprint demand is expected to reach 2.7 million tonnes in FY19. The demand for packaging paper and board segment is expected to grow at a CAGR of 8.9 percent and reach 9.7 million tonnes in FY19. India’s share in global paper demand is gradually growing as domestic demand is increasing at a steady pace while demand in the western nations is contracting. The demand in India grew from 9.3 million tonnes in FY08 to 15.03 million tonnes in FY16 at a CAGR of 6.4 percent.