Silverton Pulp & Papers is a part of a highly growing group of paper industries. The group has a diversified business portfolio in manufacturing high-grade writing & printing paper and packaging grades. In each product category, the groups’ manufacturing facilities enjoy the optimum operating efficiencies that result in a more competitive cost structure. The surpluses so generated by the group are reinvested in the business thereby ensuring continuous growth and rising market share. In this perspective, Silverton Pulp & Papers has identified a significant investment opportunity to promote Make in India, Made in India, through various new product launches, planned to kick start in the first quarter of 2025. Currently, the group is making approximately 1100-1150 TPD of paper and targets to manufacture 1500 TPD by 2025.
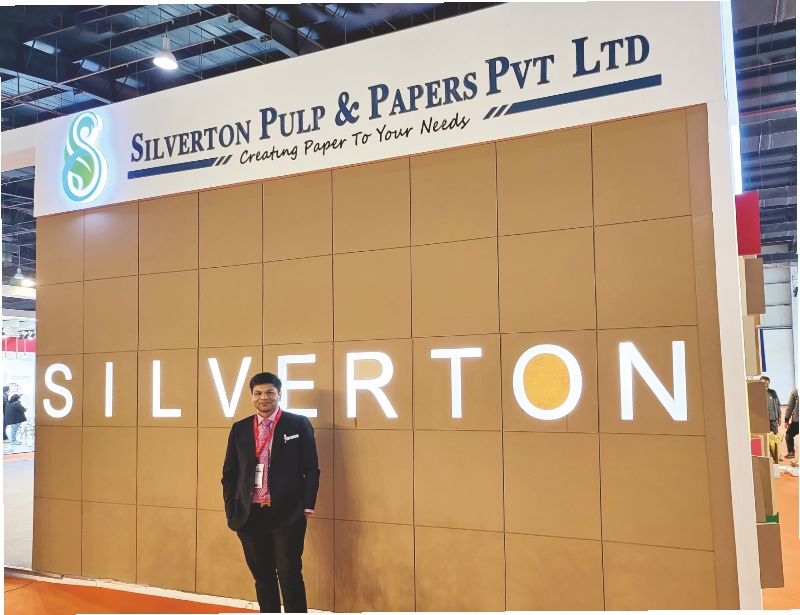
History, Journey & Growth Story
We have been in the paper industry since 1990. We forayed into the paper industry with Garg Duplex & Paper Mill Private Limited with a capacity of just 15 TPD. Since then we have not looked back. Silverton Pulp & Paper Mill was established in 2004 and it has been a part of a highly growing group of paper industries. The group includes four companies that are
- Silverton Pulp & Papers
- Garg Duplex & Paper Mill
- Aroma Krafts & Tissues
- Accurate Multilayers Papers LLP
Today we as a group are making approximately 1100-1150 TPD of paper. We target to manufacture 1500 TPD by 2025.
Journey of Silverton Pulp & Papers started as a small player with a capacity of around 40 TPD of low-quality recycled grade writing paper. Over the years we made mistakes and learned from the mistakes and experiences and I felt we needed a strategy to grow Silverton as a brand.
In 2010-11, there was a boom in the packaging sector. So we decided to convert our existing machine to a multi-layer kraft paper machine and entered into the packaging segment which proved to be the right decision for us. At that time, high BF was made by only 2-3 mills and we decided to diversify towards high BF which increased our capacity from 40 TPD to 250 TPD of kraft paper in the BF range of 18-35, one of the best qualities in North India and well appreciated by the customers. We had made good money in the kraft paper business.
In 2015, we analyzed that there was an opportunity in the multi-layer board market but due to a lack of resources and we did not want to take risks, we did not enter into the segment. But towards the end of 2015, we got the opportunity to buy an Italian second-hand machine and we seized the opportunity but instead of a multi-layer board, we used it for writing and printing paper. We adopted the best technology of that time. It turned out to be a game-changer for us. Those days, very few people who had the latest technology in India and those who had it, did not want to share it.
In 2018, the Italian machine was installed in our new paper plant which was a Greenfield project. It increased our capacity to 182,000 TPA.
We are now entering into the coating market which was dominated by BILT & JK Paper, sharing almost the whole of the domestic production between them. We are coming up with a second-hand machine from Germany, which is an online coating machine with a capacity of around 100,000 TPA. With the new machine, we are targeting the highest value-added products with prices of above INR 100.
With all the expansion, today, I believe, in the recycled grade, we are included in the top 3 paper mills in India in terms of quality.
Watch: Starkraft to Offer Capacity of 350,000 tons from May 2024
Getting into High Value Added Products
Our short-term goal is to establish ourselves in the highest-level category of products within the next 3-4 years. Establishing ourselves in the highest-level category of products has many benefits. The competition that comes from the lower level of the market is eliminated because the highest level of products has an entry barrier. For instance, in the packaging sector, there is no entry barrier. When the packaging boom came in India, during covid, at least 200 new mills were set up. And today what is happening is that out of those 200, 100 mills have already closed. And the ones that are currently running, are on the verge of closing. So, keeping this in mind, we decided to go for such products where the entry barrier was not easy. Only good players can enter the market. There are two types of barriers. One is the capex barrier and the other is the technological barrier. Not all the players in the industry have the correct knowledge or expertise to sustain themselves with the demand in the market. But today, in our company, we have so much experience and such a good team, that we have been able to sustain and grow ourselves rapidly. Today, we know how to make good quality products. So this is our modus operandi and we are taking the same target that after 2025 whatever product we make, we make it above 100 rupees per kilo.
Product Portfolio
We are currently making paper between 200 to 300 tons depending on the grammage. We are making all grades of Maplitho, mainly the recycled grades and the virgin grades by using purchased pulp. Additionally, we are making products like bleached kraft and copiers. Furthermore, we have made a new change in our system. We have rebuilt our small machine completely with DCS and QCS technology which was getting obsolete in the kraft. Now we are making cup stock on it.
Our current capacity for writing grades is more than 10,000 tons which we are targeting above 20,000 tons by 2025. We are making new systems. Today, our group is making 1100-1150 TPD of paper which we are targeting 1500 TPD by 2025.
New Developments
Recently, we have developed a new product for high-strength lamination which is used in pouch packing. It is a high-strength paper and has a BF of about 40. I have always believed that we have to search for growth opportunities. When we installed the writing & printing machine, there was space left in the coating section and we were looking for a similar-grade machine. I learnt that a same width machine was available in Europe and it was the best-suited machine for us. It was also saving us a lot of money. So we purchased the machine for our plant.
In addition to this, we have also installed a waste-to-energy boiler. The boiler can burn all unconventional raw materials from MSW to waste plastic. It is a government-approved technology. So now we have 7 to 8 megawatts power free and we have 200-ton pulp free. We have also put in a new DIP of 150 tons.
Future Plans
Going ahead, we want to focus on flexible packaging, the laminated one. Our main focus is now on biodegradability. We have big plans for the coming years. We will soon start making lighter grams of paper, for example C1S. We will start manufacturing wet strength labels which are used for beer bottles, and liquor bottles for example CCK (coated clay-coated kraft), and SCK (super calender kraft) which is a product that is attached to the release liner in the label. Additionally, we will start producing Maplithos from 45 GSM to 52 GSM, which is not our range today. One of the products is bible paper which is produced only by 2-3 mills in India. We would like to start manufacturing the bible paper. We will start manufacturing medical insert paper. So all these products will add value and will be beneficial for the customers as currently they are imported from all around the world. The slogan that is being used in our country, Make in India, Made in India, we are trying to promote through these products and we are planning to start working on them in the first quarter of 2025.
Also Read: Orient Paper Mills Focuses on Specialty Products in Health and Hygiene, Plastic Substitution Sectors
Industry Scenario and Challenges
In India, according to me, the growth is in the packaging sector. Three types of packaging grades are bound to grow. One is the packaging grade which includes the kraft paper and duplex board. The second is the writing grades. Third, the packaging grades in white paper like bleached kraft and carrybags which includes products like wraps or C1S or C2S which is coated paper.
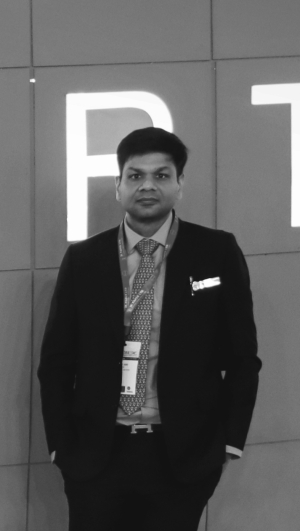
If we talk about kraft and duplex, in India, overproduction is a major threat. There is growth but the mills are in trouble. There are no margins, they are bleeding because of overproduction. If we talk about writing, there is growth in writing too. Maplitho is sustaining because there is no new production. In Maplitho, growth will be 2-3 percent maximum. But production is not that good because everything is going digital, people prefer digital, but packaging grades in writing & printing are not manufactured in India. Only 1-2 mills make it and it is mostly imported. So we are foraying into this sector. So growth is in this market and it is a market where not everyone can sustain. So, in the future, if demand is made, then it will not be the same as the kraft scenario where overproduction is happening. Only those players who can invest in technology and will upgrade with time can sustain and grow.
The challenge for our group is mainly in the kraft industry which is highly reliant on imports. India is self-sufficient in paper manufacturing. But we are still allowing import. If you look at the import data of the last year and this year’s import data, it has increased more than three times. People who are not getting any market, are dumping paper in India. If they sell paper worth 100 rupees in their country, then they dump it in India for 70 rupees. They say that if they dump the money in 20 percent of the market, then they are maintaining their rate. The Indian Paper industry is very vast. Many people are connected directly and indirectly as well. If the dumping continues it will contribute towards national loss. The government should make plans to curb the imports so that the domestic players can sustain and grow. And if the government cannot curb the imports, they should make plans to restrict the price at which the paper is being dumped to maintain competitiveness in the market.
Another challenge is the lack of skilled manpower. Although the literacy rate is increasing in India, if you compare urban cities with the villages, the people are still lacking basic skills. An educated person in the village still lacks the skills which are necessary for any industry. Maybe after 5-10 years, we will have skilled manpower in India. But currently, we are still behind as compared to other nations. I would like to conclude by stating that even with so many challenges in our day-to-day lives, we are surviving in our business. So, we need support and safeguards from the government which will help us to boost our growth.