Mondi Štětí’s PM7 rebuild increased winder capacity and improved safety
When Mondi Štětí was looking to free the finishing area of PM7 from bottlenecks, the solution was found in a fast parent roll change solution with a butt-joint splicer and automatic parent roll transfer. While increasing winder capacity, the rebuild also improved safety.
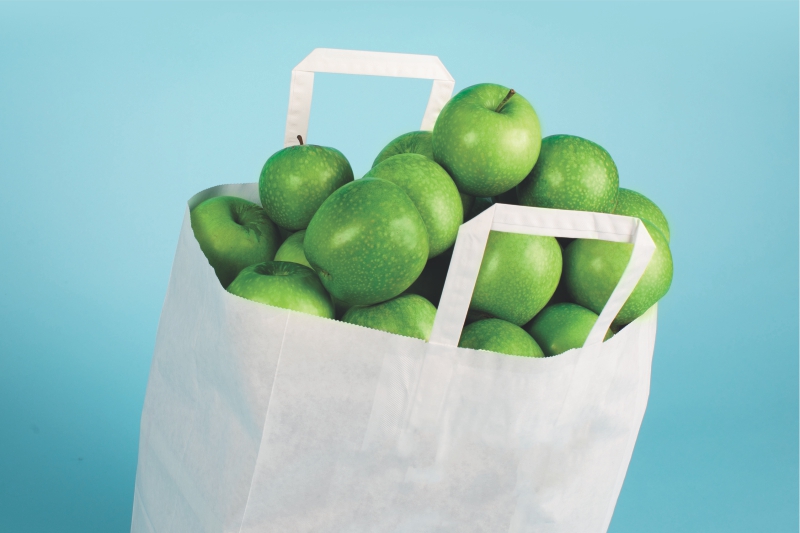
The bottleneck between reel and winder was evident. It was also the starting point for the rebuild project of Mondi Štětí’s PM7, which produces calendered specialty kraft papers. To further increase the production reliability of its paper machine, Mondi decided to take action. The challenges were posed mainly by the winder’s lack of capacity to cope with increased production targets and the non-optimal interaction between it and the reel. Valmet’s task was to find a safe and efficient solution to free the finishing area from bottlenecks.
Finding a solution to increase winder capacity
Mondi’s Senior Project Director Helmut Riesenberger’s team planned to increase the diameter of the parent roll, targeting the minimizing of manual work like sample taking and parent roll transfer. This would have required a major rebuild, with modifications to the dry end foundations, overhead lifting crane and drives, without affording the targeted efficiency increase.
Mondi Štětí mill in the Czech Republic is one of the leading European suppliers of high-quality sack kraft and specialty kraft papers. The PM7 produces calendered specialty kraft papers with high strength and outstanding printability, which serve as shopping and food bags, cement bags, pet food bags and packaging for products in the chemical industry.
Valmet came up with a cost-effective technical solution that fulfilled all the requirements for capacity and increased safety. There was no need for expensive foundation work, or drive or overhead lifting crane rebuilds. Valmet’s solution was tailored to seamlessly fit into an environment that had no existing Valmet technology. During the purchasing process, the Mondi Štětí team had intensive discussions with the Mondi Świecie mill in Poland, where a similar project had been executed a few years earlier. Feedback and experiences from Świecie were positive and encouraging.
Valmet offered a unique and proven solution called Dual Unwind, which changes parent rolls very fast and offers automatic butt-joint splicing. The parent roll change and splicing take place during the winder set change. The solution provided the required capacity for the existing winder. Full parent roll transport was also fully automated with automatic transfer rails, and now connects the reel and winder more safely and efficiently.
Professional project handling
The upgrade was successful, with short shutdown times. Riesenberger underlines the good cooperation with Valmet: “Everything was well organized. There were no delays, and the delivery was on time.” In addition, communication was always open and good. “Problems were solved immediately”, Riesenberger continues. He was also happy with the cooperation with Valmet’s project team: “The cooperation was excellent.”
Parent roll change time massively reduced
The results of the rebuild were extremely good: The winding capacity increased by 62 percent. This was due to Dual Unwind, because the winder parent roll change time was decreased as planned, and the winder downtime during the parent roll change was close to nothing. Riesenberger emphasizes the importance of Dual Unwind: “The fast parent roll change was the key in this project. The parent roll change time has been massively reduced.”
Minimized bottom waste at the reel
Very good results were also achieved with the reel’s Water Jet Turn-up Device and an optimized nip loading solution. Reel bottom waste was minimized, and highly efficient turn-ups were achieved. And on top of everything, the parent reel diameter increased.
The results of the rebuild were extremely good: The winding capacity increased by 62 percent.
Safer for operators
For Mondi, safety has always been the highest priority. Valmet provided a solution that meets all the latest EU safety regulations. Operator safety was improved significantly by installing a fully automatic parent roll transferring system, with transfer rails from reel to winder. All the delivered equipment was designed for safe operation and to meet safety regulations. New safety mats, fences and gates were also added.
“Our concern to build a system compatible with the existing one has been dealt with to our complete satisfaction. Reliability and efficiency are optimal”, says Riesenberger.
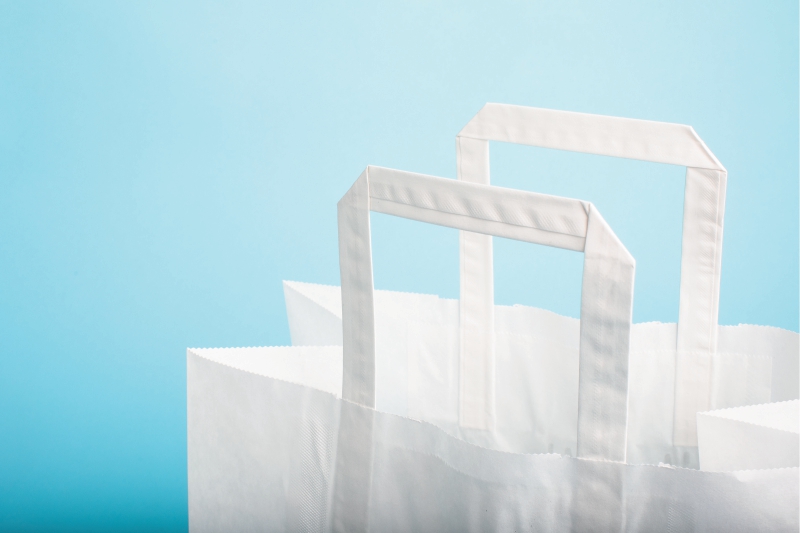
— The article was originally published in Valmet’s Case Study
— Text: Angela Paganini, Pauliina Purola and Photos Topi Saari