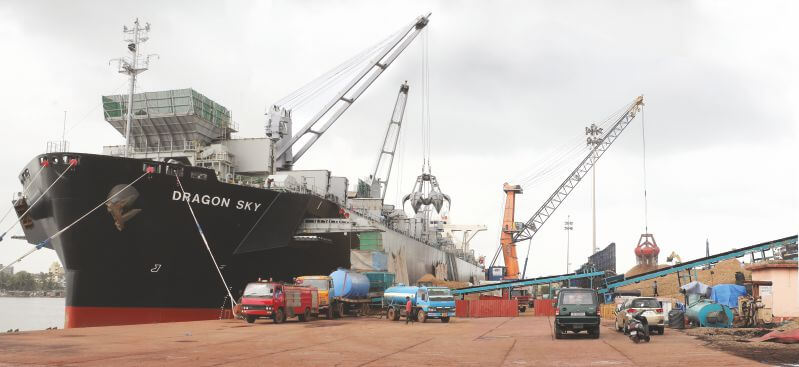
The West Coast Paper Mill has successfully completed over three years of importing chips with around forty shipments till date by setting up a sound ecosystem of infrastructure and manpower, dedicated only to import, handling and transportation of chips. Paper Mart recently visited WCPM and its chip handling facility at Goa port to compile a full-length feature on wood chip import.
Clocking a stable double-digit growth has been a tricky thing for the Indian paper industry, even when other industries have been scaling high on double-digit trajectory. The equation of growth, capacity expansion, huge investments, and raw material scenario often puts up a situation like catch-22 for the Indian paper industry, coming out of which requires a fine balance of great many things. Among the variables, raw material has been the most critical of all for breaking the growth shackles. For brisk growth to happen, capacity expansion is a must, but not without finding a comfort with raw material availability.
A strong resolve, an acute strategy, and a fool-proof plan are needed to catapult the industry on fast growth path in above mentioned scenario. The Indian paper industry exhibited this kind of determined will for growth during and after the second-half of this century’s first decade with major paper mills undergoing huge capacity expansions. The industry increased its production to more than 13 million tonnes by 2015 from 7 million tonnes in 2007, an expansion by more than 100 percent!
India saw rapid growth in the consumption of paper and paper products during 2006-11. During this period, annual consumption of paper and paper products grew at a CAGR of 9.3 percent, much higher than the average global growth rate of around 3 percent. The country experienced strong growth in production of paper and paper products during 2007-11, growing at a CAGR of 13 percent and yet it was not enough to meet demand.
Four major mills, viz. BILT, ITC, JK Paper, and West Coast added around 7-8 lakh tonnes of capacity among themselves during 2009-13, largely based on wood. While the overall period of 2006-2015 has been a great growth story in terms of both consumption and production with demand peaking in 2011, the huge pressure on raw material, especially wood-based fiber, is another grim story running parallel and sending the industry into a tizzy. The same period saw the industry scrambling for various raw material sourcing options to feed now their copiously enlarged capacities. Various permutations and combinations of raw material procurement strategies, viz. social farm forestry, import of wood pulp/wood logs/wood chips, conventional sourcing from forests, etc. were adopted by various mills. This story however is about the West Coast Paper Mill (WCPM) and its fiber strategy banking significantly, as of now, on the import of wood chips.
WCPM & Decision to Import Chips: A Background
In May 2010, WCPM expanded paper manufacturing capacities from 180,000 tonnes per annum to 3,20,000 tonnes per annum along with thermal power generation capacity from 40.5 MW to 74.8 MW. Post expansion, the company has become the fifth largest paper manufacturer in India. The company also has the flexibility to produce pulp sheet in its new enhanced fibreline capacity (capacity increased from 300 tonnes per day to 725 tonnes per day) and sell it in the domestic market. However, with the expansion, the raw material requirement also grew manifold precipitating into acute raw material crunch from 2012-13 onwards.
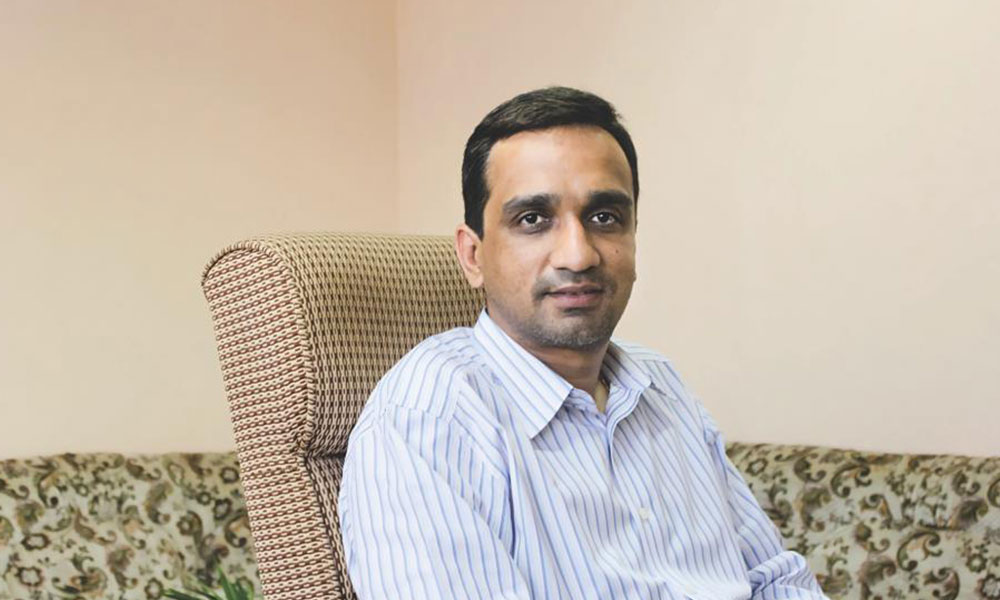
The gloomy domestic fiber sourcing scenario got the company into serious thinking mode to find out and try the option of import or sourcing wood/chips from foreign soils. “In FY 09/10/2011, approximately 8-12 lakh tonne of capacity was commissioned in the country for which raw material consumption was extra. This surplus fiber requirement coupled with less plantation in previous years led to approximately 45 percent increase in wood purchase price for WCPM for the period FY 11/12/2013. That was the time when management thought of wood/chips import. In FY 14, raw material rate further shot up by 40 percent from the previous year, abetting our decision to go for the import,” says Mr. Saurabh Bangur, Vice Chairman, the West Coast Paper Mills Ltd.
Sustained availability of low cost and good quality of cellulosic raw material, i.e. wood-based fiber, is one of the major factors inhibiting the growth of paper industry. This is the key reason of declining proportion of paper production from forest resources – which now stands at around only 36 percent. The forest resources have been diminishing at fast pace without their proper replenishment guided by multidimensional forestry strategies. And, when in such scenario, huge expansion of wood-based capacities takes place, crisis would surely have to precipitate to unprecedented level. That’s what happened during 2009-13 and still has not mitigated to much desired level.
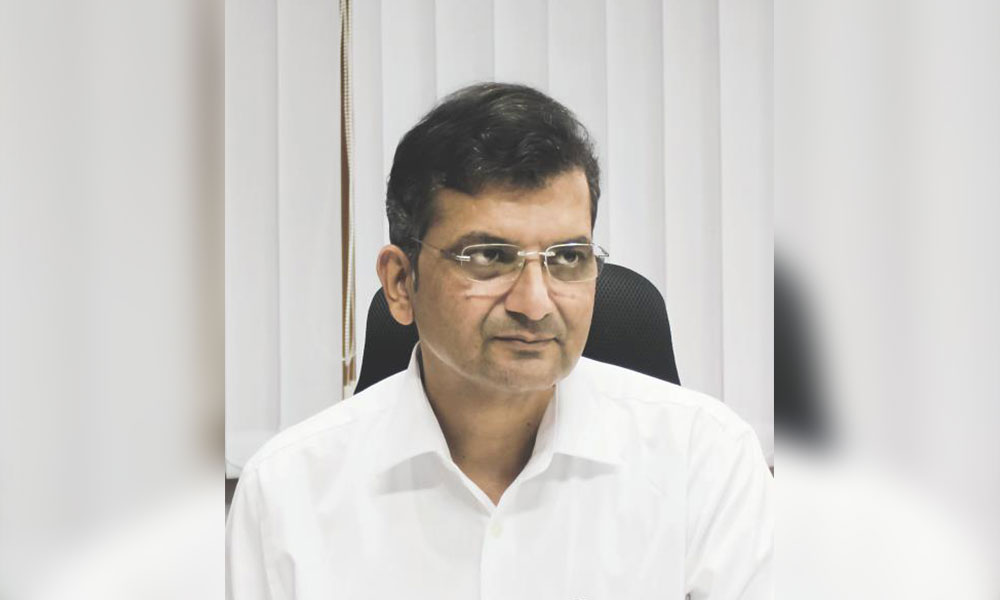
“Wood requirement doubled in 2010 after commissioning of the new plant, and availability of wood was big question mark as other companies also started expanding. I agree that expansion was much needed if the industry had to race past the growth barrier, however this is also true that a well laid out fiber strategy was not put in place such as planting more trees of better species. Hence, the crisis started lurking over our head around 2012-13, making us look for alternatives. One of such alternatives was to import wood chips,” says Mr. Rajendra Jain, Executive Director, WCPM.
WCPM management decided for import option not in a hurry, but the realization on the contrary took quite some time to settle after they had exhausted all the option to procure wood domestically in desired quantities to feed its extra requirement due to recent expansion. The company is now maintaining roughly a 50-50 ratio between its domestic procurement and import.
“We require around 9 lakh tonnes of raw material per annum to feed our enlarged paper production capacity, completely procured from the current market. Around 50 percent of our raw material requirement is met from the domestic procurement – both through social farm forestry route and buying from govt. forests. We have already identified fallow/waste land belonging to marginal farmers within a 250 km radius from our manufacturing unit. We provided clonal seedlings to these farmers, encouraging them to raise plantations from a long-term perspective with the safety net of an assured buyback. Farmers are planting, eucalyptus, subabul or casuarina in their plantation; and after a certain time period, we are buying at market rate. However, we were increasingly falling short of our raw material need after the expansion. Thereafter, we decided to go for the import to balance the surplus needs. It was not because of convenience, rather a necessity to arrange the feed for our machines,” reasons out Mr. Jain.
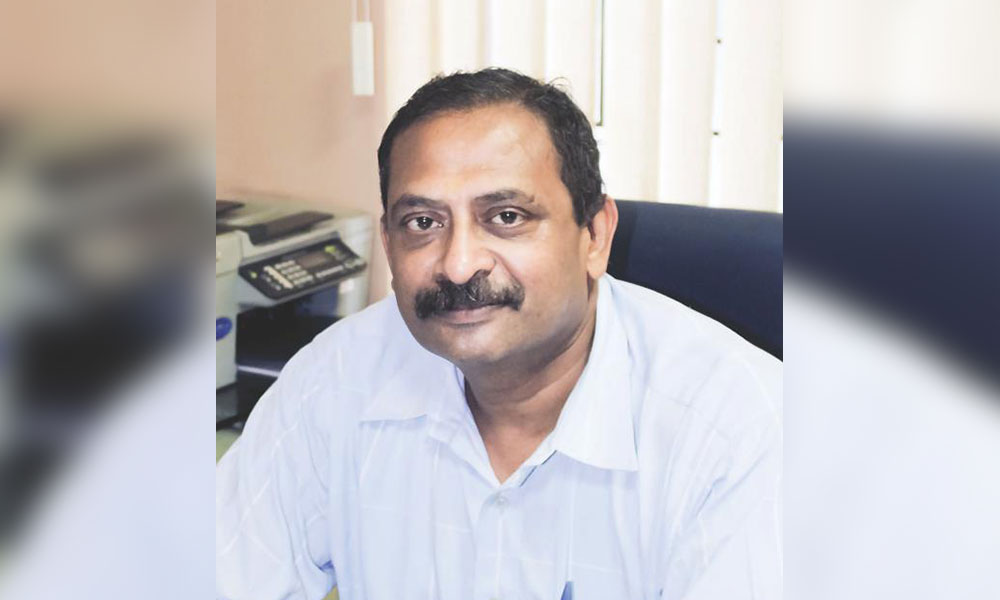
Echoing the same view, Mr. S. Venugopal, General Manager-Raw Material, WCPM says, “See, the decision to import was not instant; it was gradual and a logical thing to do at that point of time. Basically, during 2010-11, we were slightly comfortable. But from 2012-13 onwards, we started facing acuteness of the raw material crunch. Various domestic procurement options were tried out to survive this crisis; one was getting woods from Andhra Pradesh, 1000-1200 kms away from the mill. Quality and quantity both were dwindling with prices soaring at the same time. Wood was immature leading to less pulp outcome and our requirement was huge. We even went as far-off as Kerala, Andhra Pradesh, and Maharashtra, but the situation was practically worsening. We therefore came to realize that why not go overseas instead of competing in the domestic market and thus the decision to import chips.”
Exploring Favorable Foreign Soils
Deciding is easier than executing and WCPM realized it soon after the management gave green signals for the import of wood. Importing wood was not an established thing in India and hence no blueprint as to how to do it on sufficiently long-term basis. The Indian pulp and paper companies have been sporadically bringing wood/logs/chips/pulp from outside whenever the need be and abandoning it soon after. WCPM’s raw material team started moving on a path hitherto less treaded and began developing its own scheme of things based on exhaustive survey and reconnaissance of various nations and their offerings.
“Our raw material team did lots of survey, correspondence and communication along with field visits to many suppliers and travelled many countries like Brazil, Australia, Thailand, Malaysia, Vietnam and South Africa. We practically procured one ship from each country comprising of different species and took lab trials; after that plant trials were done,” informs Mr. Bangur.
After lengthy initial correspondence over mail and phone to fix the most suitable vendor or source, the raw material team visited various countries to confirm the quality, quantity and accessibility of wood being available there. As said by Mr. Bangur, the company even got vessels containing chips from at least five countries and ran suitability trials confirming the machine requirements. Testing the feasibility of various species of wattle, eucalyptus, etc. from those countries, the company eventually zeroed in on Tasmanian Blue Gum, i.e. eucalyptus globulus from Australia, having better yield and consistent fiber quality.
“Let me tell you very candidly that finalizing a specific source or vendor was not at all an easy task. In this case, the theory of ‘one size fits all’ does not apply. Yield variation, moisture quantum, size variation, age of wood, different contents of wood specifications, viscosity, chemical consumption, bulk, etc. have to be observed; and, all vary from plant to plant, location to location and process to process. It was a big challenge for our raw material and pulp mill technical team to standardize our wood import specification,” clarifies Mr. Bangur.
Nearby locations like Malaysia and Thailand could not make it to becoming the final fiber destination for WPCM because of one other reason besides fiber quality. In these countries, an overseas supplier has to sign an agreement with the actual plantations resulting into unnecessary delays. Countries like Brazil and Spain were ruled out, though having good quality fiber in the form of globulus, because of disadvantages in terms of distance.
“After seeing the trial results from initial few shipments, we decided to go for globulus from Australia both because of yield quality gains by at least 5-6 percent and shipment convenience. However, that was not the end of blues. In Australia, there was a condition forbidding the direct import of wood logs; so we settled for wood chips. That’s how we ultimately started importing wood chips with all the difficulties which was to be continued for some time until the chip handling facility at Goa port was stabilized. But, that’s another story!” says Mr. Venugopal.
Apart from external obstructions in meeting the raw material requirements through imports, a lot of internal adjustments were also required to handle the quality of chips. “Pulp mill operations had to be fine tuned to practically every different species supply from different sources. Sometimes the yield was not good at all. At other times, though yield was fine, bulk density of chips was lower and as a result output from the digester was below than desired. So, to have a right balance was the biggest challenge for the team,” told Mr. Bangur.
Eliminating Bottlenecks: One Step at a Time
Wood quality, vendor selection, shipment, handling and transportation were few conspicuous obstacles initially when WCPM decided to go for chip import – to be removed sequentially. Finalizing a vendor was not without much vacillation and brooding, taking in view a relatively longer period of constant wood chips supply. One of the Japanese trading houses became the final choice because it offered a number of solutions to issues such as freight cost, empty haulage charges, quality of chips, etc.
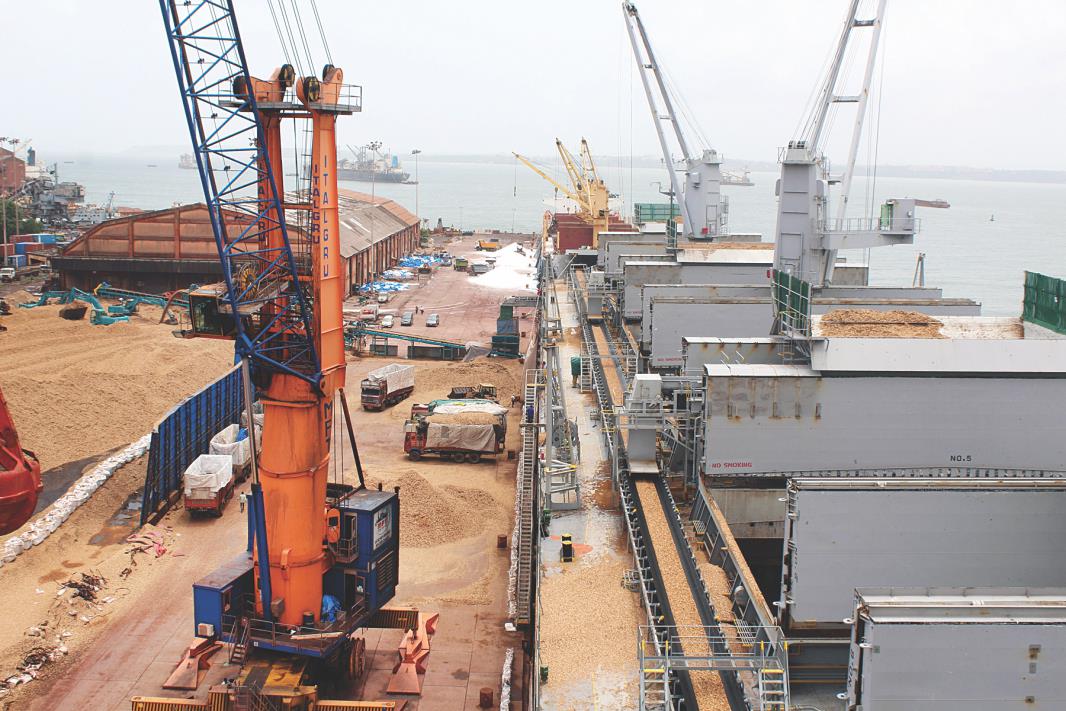
“The company finally decided to go for globulus from Australia also because of the trading house as the chip size supplied by it was rather consistent. It means that the quality of chippers they use is very good or as good as what we have in our factories,” says Mr. Venugopal.
WCPM’s decision on eucalyptus globulus (EG) having better yield was arrived at also because of the help provided by the vendor. “Eucalyptus globulus (EG) species is high pulp yield wood and considered as the one of the best for paper pulp making. At the time of very first wood chip contract discussion with WCPM, it was suggested/ recommended WCPM to consider import of ‘EG’ chips as trial shipment, although cost wise EG chips are expensive. The purpose of offering EG chip to WCPM was that the very first ever wood chip import trial should be beneficial for customer and they should feel visible benefits from EG chips compared with domestic wood chips,” says one Indian official of the trading house.
The trading house offered EG chips from own subsidiaries in Australia and shipped two consecutive shipments of EG chips to WCPM per vessel ANDALUCIA. WCPM achieved higher pulp yield from EG chips and other related benefits from trial shipments.
The availability of bulk carrier or vessel was also a headache as there always was a scarcity of such carriers dedicated to wood chips shipment in the absence of regular/steady demand or import of wood. A mismatch exited between the timing of availability of chips and that of availability of ships. Size of the ships was also of great concern as it must match the volume specifications agreed upon by vendor and client. Even if a ship agrees for the shipment and is not available at the port where it has to load from, it will surely charge for empty haulage, resulting in the escalation of freight cost. These were some of the problems WCPM raw material team had to resolve before they began getting wood chips supply at consistent basis. However, it would be quite interesting to see how these hold-ups were done away with.
“It all looked like a mess. However, a practical and long-term solution was reached with the help of our team. A long term contract was entered, which says that a ship will be solely loading from vendor’s designated port and unloading at client’s port and return back. So, problem of empty haulage charges, size, and availability of ship was all done away with single stroke. So, ships now go to that same destination, and then carry the same commodity and the void is now fixed,” informs Mr. Venugopal.
When the question of choosing the right chip source, vendor, and shipment impediments was settled, handling of chips at the Goa port emerged as another riddle staring in the face, and then there was transportation issue from the port to the mill, 160 km away. Apparently this distance was one of the facilitating factors for the import of the chips for WCPM, yet it was not such a less distance to not cause worry when the question was to organize a systematic large fleet of vehicles to ferry chips from the port to the mill.
“Lots of documentation was needed to be done at port level. Apart from documentation, unloading of huge quantity along with storage at port was also an issue; so the timely dispatch of vessel and timely unloading were important, or else demurrage would be levied on per day basis. Transporting chips in trucks from port to our plant, which is 160 km away, was a mammoth task. All trucks were covered with tarpaulin so that chips’ dust would not fall in transit,” informs Mr. Bangur.
The transportation of chips from the port to the mill was a massive operation to be organized at regular basis. Since the quantity was voluminous, a large fleet of truck was needed to transport over a distance of 160 km. Owing to the ban on the iron ore export effective at the time, a number of truckers were left idle and were easily convinced to offer dedicated services to WCPM for chip carrying purpose. So, in that way transportation also clicked. One by one pieces of puzzle were falling in place. Even the truck customized to the purpose and raised their body to carry larger load. There is a fleet of approx 250 trucks dedicated to WCPM to carry chips to and fro the mill. Moreover, the transportation arrangement is also fine tuned to the daily consumption of chips at the factory.
Handling Troubles at Port: What It Took to Find an Enduring Solution
Chip handling at Mormugao Port, Goa was another stand-alone problem which elicited a dedicated attention in order to get solved and put in place a system which was not only robust, but was to serve WCPM in long-term as the import of chips was envisaged for relatively long period until the cellulose-based raw material scenario changed here in India. A makeshift system meant for one time or two times wouldn’t do.
As there was no previous record of wood chip import into India, there were many administrative and operational problems such as no clear understanding of quarantine regulations on imported wood chips; coal and iron ore contamination at Goa port; no dedicated berth for wood chip vessel at Goa for cargo discharging operation etc.
Wood chips are quite bulky cargo with one shipment carrying somewhere around 45,000-50,000 tonnes of chips. One not only needs a copious space on wharf to unload, but unloading has to take place quick within set time limit to escape from heavy demurrage. However, it was not so, absolutely! This kind of cargo handling was not known to India and the kind of customization it needed required a great amount of work and expertise. This fact may be borne in upon by the mess and troubles experienced at the arrival of the first ship on June 12, 2013, and how the team had a nightmare of time while unloading it!
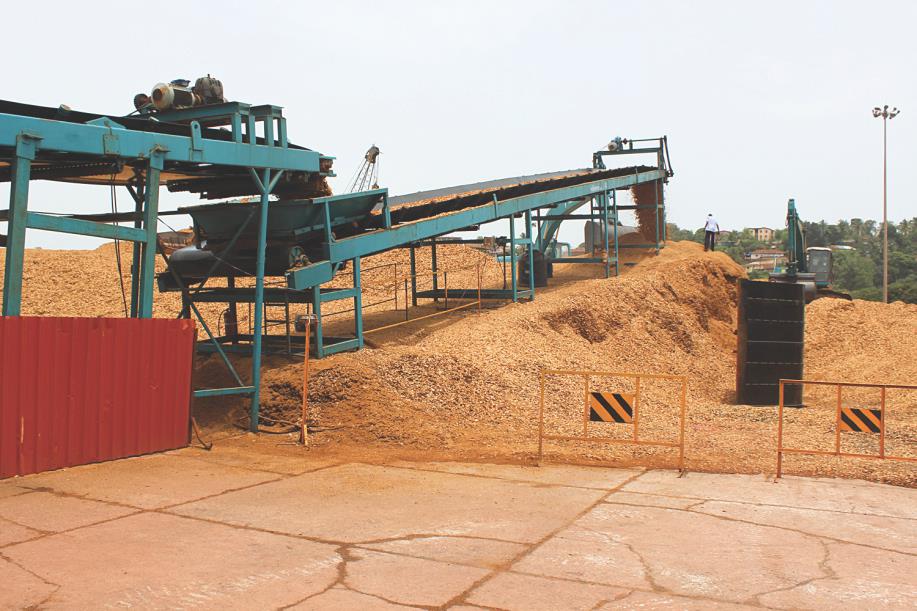
“Handling chips at the port was a big problem and we did not have the know-how as in India nobody has done it on a regular basis. Mainly this kind of operations is done by overseas companies such as China, Japan, Brazil, etc. and there is a big gap between their and our infrastructure. The basic problem was in discharging, because chips are actually voluminous commodity and very difficult to handle. Moreover, finding a suitable berth at the port was also an issue. The speed of on-ship conveyor belt and the one we installed outside did not match while discharging the first ship. And, other issues like limited hauling capacity of the cranes we employed made the discharge rate too tardy. However some of these bottlenecks were overcome by the 3rd or 4th ship with the help of cargo handling companies with a lot of customization,” explains Mr. Venugopal.
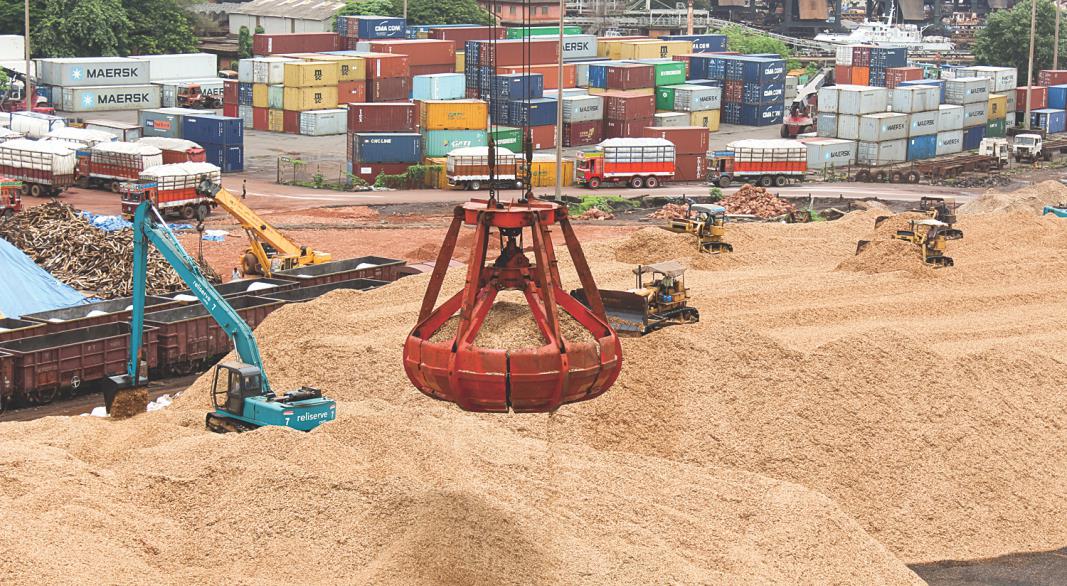
“WCPM team visited relevant authorities many times for understanding the quarantine related queries. A team from Australia visited a number of times to Goa port prior to vessel arrival and shared the knowledge and experience of ‘how to avoid port contamination to wood chips’. In addition, they shared extensive material, experience, knowledge in cargo discharging from ship, stock pile management (storage of much cargo in less space), etc.,” informs the official from the trading house.
The story of blues and crises faced at the arrival of first ship and what it all took to put in place a well-serving system is quite interesting as shared by two energetic youths hailing from two different companies responsible for on-the-ship and off-the-ship cargo handling. “My responsibility is on the ship as in to unload the ship and to deal with the customs, port authorities, plant quarantine and forest department; the whole operation on vessel is mine,” informs an official from the shipping agency.
After the chips are discharged off the vessel, it gets off the wharf to storage plot fast and safe with the help of conveyor belts and cranes. After that chips are transported from port to mill.
Explaining the fix they were in when the first shipment reached the Goa port, says one official, “When the FIRST wood chips carrier in India “M V Andalucia” arrived, we never knew what it was and we took 11 days to unload it! We could not discharge even 4,000 tonne a day, which was very bad and spirit dampening. There were many obstacles as this was not a general cargo like coal or iron ore. I mean it was not a free falling cargo, so we had to devise much equipment which we haven’t used before.”
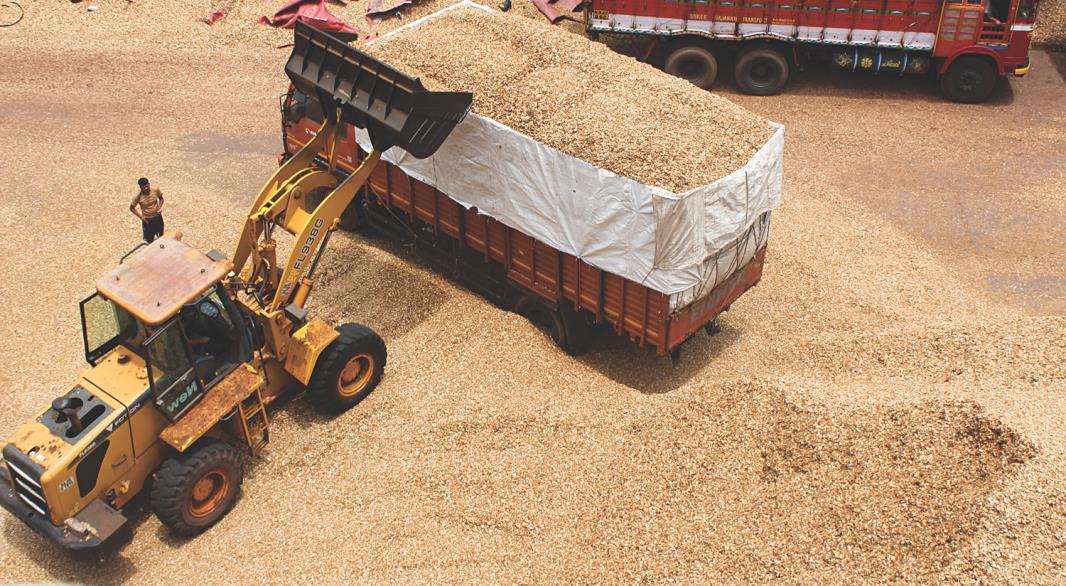
Sharing his experience on the same, other adds, “See, it was critical for us to match and coordinate our operations to discharge the ship within required time frame. But, we were hardly aware of how this ship worked as to what the discharge rate was, type of conveyor there, how big the conveyor was and how we can manage the speed of the conveyor or speed of discharge, etc. As per our best estimate of what it would be (since it was not handled anywhere else), we made the conveyors. However, those conveyors failed because the speed was much lesser, the width was small, and the pulling capacity was very low. In the first shipment we could hardly use them. But once we saw what was there onboard and how it operates, we tried to build all these systems here that were equivalent to take the capacity.”
The system they had put in place was not makeshift and was completely dedicated to handle only this kind of cargo, i.e. wood chips. It took around 7 to 8 ships to get everything in place. Their effort was genuine and many things they did was sort of for-the-first-time. Equipment they contrived, systems they evolved and practices they put in place was not standard or generic, but was meant for just wood chips handling. “The system you see here is not standard; you will not get this anywhere else. Though they look normal once put in place, they are absolutely unique if you look closely,” quips the first official.
“Normally, after few initial ships, we caught our stipulated timeline of 10-11 days during which we used to be on the allotted berth. However, we used to face a lot of hassles from time-to-time such as the vessel had to be taken out as there was some govt. priority vessel. From there on, we thought of increasing the discharge rate. The port already had a HMC and we thought of using it. From there, we touched the discharge rate of 7,000 tonne a day, reducing significantly the total discharge time. Now, it takes approx. 8-9 days to unload a ship with cargo load of about 45,000 tonnes,” explains the official.
The extremely favorable outcome achieved in handling chips at Goa port is also attested by the vendor. “The very first shipment of EG wood chip from Australia per vessel ‘ANDALUCIA’, the cargo discharging operation was completed in almost 13-14 days. However, at the time of 2nd shipment, all required equipment for discharging wood chips was in place. WCPM and their associates at Goa port did wonders and the cargo was discharged much within allocated free time. Ever since there is much further improvement in wood chip discharge and have achieved the highest record of wood chip discharge. Now we can proudly say WCPM and their associates are very much experienced in wood chip discharge operation” says the Indian official of the vendor.
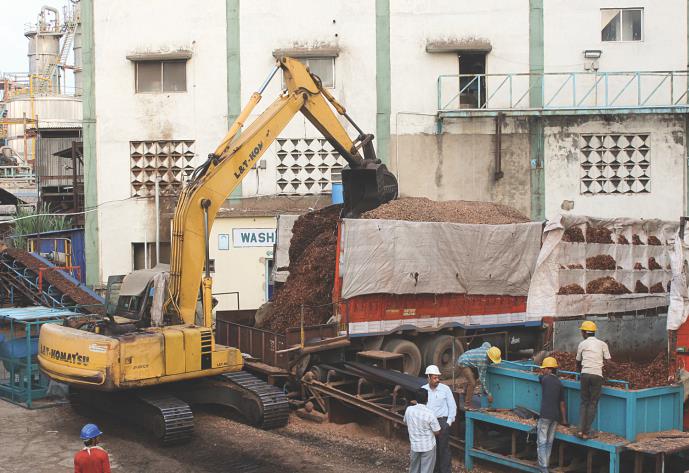
WCPM’s chip importing endeavor thus makes a fine story dotted with many troughs and crests, eventually ending happily with the creation of credible and robust ecosystem right from choosing vendors overseas and managing the port to tweaking internal processes at the factory. They have instilled a system which is not makeshift or temporary, and would serve as a pointer to others who in future like to tread the same course. When we look back and see how things turned out, we feel a fine balance of many visible and invisible factors struck out by virtue of hard work and timing. This would be wrong to assume that only a distance of 160 km from a port made this entire thing possible. This would also be wrong to assess or question the viability of importing chips in long or short run, especially when your machines are going dry and hungry in the want of raw material.
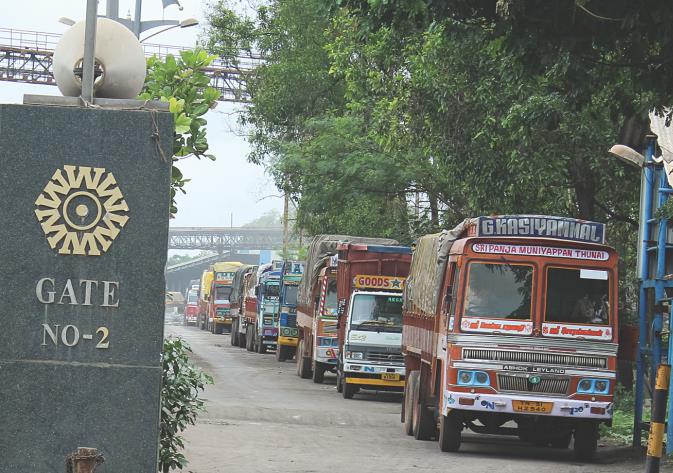
.