The leading process chemical maker is steadily growing in terms of its production capacity and range of chemicals. With its new plant in Greater Noida, it has expanded its product portfolio to include the sugar and textile process chemicals as well. The new plant with current capacity of 300 MT/month is to reach 600 MT/month by mid-2019 with the addition of two more reactors.
Excerpts from the interview with Mr. Sanjeev Jain, Director, Maxim Specialty Chemicals Pvt. Ltd.
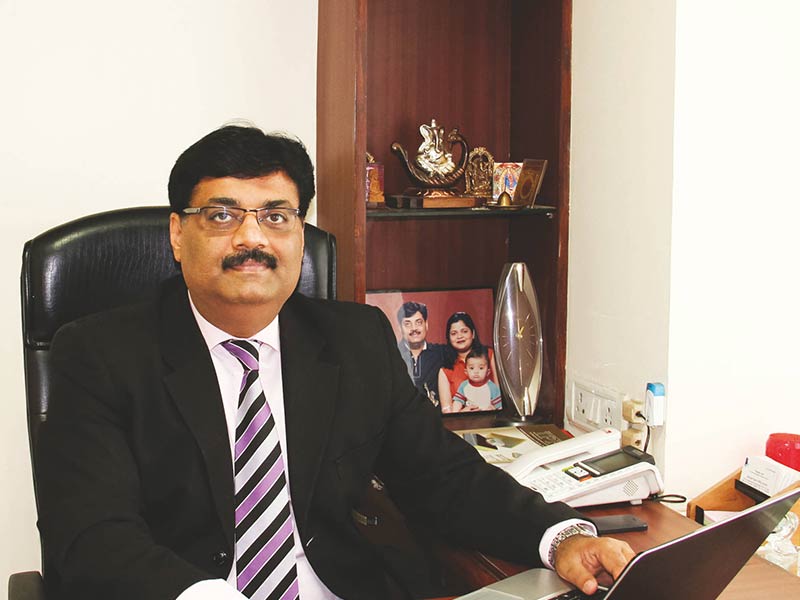
Paper Mart: Tell us something about the new facility in place for the pulp and paper vertical in particular. Kindly let us know some project details and the key areas of focus of the facility?
Sanjeev Jain: If you recall my previous interview in Paper Mart given in October 2016, I mentioned Maxim’s plans to set up a manufacturing plant in the next 2-3 years in Delhi-NCR. The idea was to meet the growing demands for local products in India, to increase our export footprint, and to expand the product portfolio. Well, I am very pleased to inform you that we have finally commissioned our new manufacturing plant at Greater Noida in June 2018 quite successfully. We produced our first chemical batch in August 2018, just within 3 months of commissioning, a huge achievement by our production team.
Our new plant is located in Greater Noida industrial zone and is an environmentally compatible plant with zero liquid discharge (ZLD). At present, we have three reactors with an existing capacity of 300 MT/month but with a provision of two more reactors to achieve our target of 600 MT/month by mid 2019. We have a fully equipped laboratory with all the latest facilities and lab equipment to ensure best possible quality checks on both our incoming raw materials and finished goods. Our plant is well located with an excellent road and port connectivity because both Eastern Peripheral Expressway (EPE), which was recently inaugurated, and Dadri ICD port are within 10 Km distance from our plant.
Maxim Specialty Chemicals has been dealing with paper process and waste water treatment chemicals for many years. Now with the addition of this new production facility, we have expanded our product portfolio to include sugar and textile process chemicals as well. Further, we have also started catering to OEMs, mainly for waste water treatment (WWT) chemicals through our sister concern Spectrum International. This was done mainly to expand our footprints in WWT across industries due to the increasing focus on ETP, especially in view of ongoing CPCB guidelines including ZLD norms.
PM: Give us a brief outlook of your new product portfolio and key areas of their usage and the advantages that can be reaped by the recipient industry over a period of time?
SJ: We are currently producing approximately 200 MT per month of paper process chemicals and 100 MT per month of coagulants only for waste water treatment such as polyamine, Poly DADMAC, DCDA, PAC Blends, ACH Blends, etc. Therefore, our total current production is 300 MT per month which we hope to increase to 600 MT per month by mid-2019 by doubling the production of both paper process and WWT chemicals.
PM: Given the increasing regulatory pressure on the environment side, the pulp and paper industry may be keen in knowing what Maxim Specialty Chemicals can do to help them through its complete package of products and services for pulp and paper environment monitoring?
SJ: Yes, the regulatory pressure by CPCB on the environmental side has been increasing for the last few years on all the process industries, especially the ones which are more water centric such as the paper industry. And therefore, the discharge norms for BOD, COD, color, etc are also being made stricter year after year especially in view of “Namami Gange” project undertaken by the current government.
Further, CPCB’s guideline for ZLD is also posing greater challenges to paper industry because of higher water usages as compared to most other industries. All of these factors have certainly made the paper industry to look at their ETP more seriously than ever. The industry is now looking for solutions to keep its fresh water usage at the lowest possible level by optimizing processes and treating its waste water for maximum reuse. This is the area where Maxim Specialty Chemicals can pitch in to help the industry with its “cost effective solutions” given our broad product range of WWT chemicals. That coupled with our vast experience in ETP area across India and many other countries give us an advantage in addressing ETP related issues effectively. We have a full range of products for TSS/BOD/COD reduction, color removal and sludge dewatering to meet the discharge norms as specified by CPCB time to time.
PM: How do you maintain the constancy in the quality of chemicals? Please explain about your in-house R&D facilities and procedures therein, in brief?
SJ: We have fully equipped QA, QC and R&D departments at our new plant. While our QA assures the quality of incoming raw material, QC checks quality of our finished products. Maxim Specialty Chemicals has always been very proactive in coming up with new and innovative solutions through extensive in-house R&D activities to help the paper industry to address some of their ongoing issues such as odor/smell in paper, cracking in kraft paper, requirement of BF/RCT/CMT enhancement in packaging grades and color removal in discharge, etc.
PM: This is a buoyant phase for the Indian pulp and paper industry, full of Greenfield projects, expansions, rebuilds, and other project activities. How is Maxim Specialty Chemicals doing or will do in terms of growth in supply of its products and services? Kindly give some details?
SJ: I agree this is one of the best times we are witnessing in paper industry especially in packaging and tissue grades. I am sure this trend will continue further given our growing economy, consumer movement towards packaged goods, and booming online business etc. That obviously is a good sign for all the allied industries associated with the paper industry such as chemical industry like ours. I certainly see that contributing to our good business growth over the last few years both in India and internationally.
PM: You may add something, which we might have left untapped by above questions?
SJ: We started with trading business back in the year 2010 with help of our business associations with some global brands. We finally launched our own brand “Maxim Specialty Chemicals” in the year 2012 to build our own product portfolio. We initially started with blending facility which was followed by a small manufacturing plant at Mumbai and then a bigger manufacturing facility at Delhi-NCR. We were initially selling only in India. Our first export assignment was undertaken in the year 2013 to Indonesia and then many more countries followed. Now export constitutes over 30 percent of our total business revenue which we intend increasing to 50 percent. We are currently exporting to Indonesia, Malaysia, Thailand, Vietnam, Egypt, Bangladesh, South Africa, Dubai and Abu Dhabi and looking forward to add three more countries– Turkey, USA and Australia in the year 2019. We have our offices in India and Singapore and plan to open one in Dubai soon.
We have a pan-India presence with our technical sales people located across the country. We have two verticals: paper and WWT. We have recently started sugar and textile verticals to expand our foot prints across industries. Our sister concern Spectrum International will solely focus on OEM business across India and will have no conflict of interest with our direct business done by Maxim Specialty Chemicals because the product range offered by Spectrum Chemicals will be entirely different. The objective of this business is to expand foot prints in WWT chemicals through OEMs.
Maxim has indeed come a long way since its start up in the year 2010 and I have enjoyed seeing it become the company that it is today. However we still are a long way off from the milestone we have set for ourselves. We will continue to help our customers through our innovative and cost-effective solutions and always strive hard to become better than what we are.