…………………………………………………………………………………………………………………………………
The Indian pulp and paper sector is one of the energy & water intensive sectors. The sector offers tremendous scope for improvement in environmental performance. Hence, the pulp & paper manufacturers are increasingly on the look-out for technologies and best practices for improving their performance and reduce the ecological footprint. Below are the views of the panel where the main objective is to facilitate continuous improvement of energy, water and environmental performance in Indian paper industry and help them in achieving the world class standards.
……………………………………………………………………………………………………………………………………………
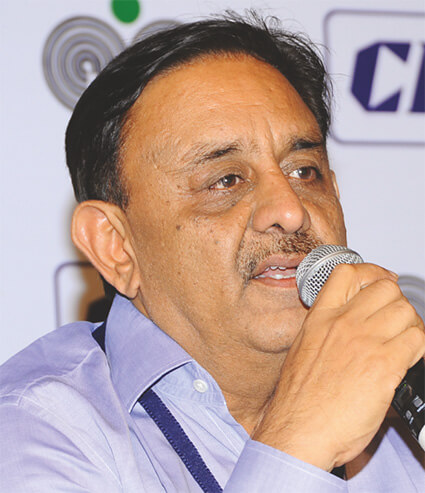
Connecting to the theme of “making the Indian paper industry world class” he said, “I would like to share what ITC is doing on this front. The average water consumption in Indian paper industry is about 100 cubic meters. On my visit to Aurangabad sometime back I observed that smaller mills there are achieving water consumption of 3-4 cubic meters. That area has acute water shortage this year and still they are running their mills on tankers. This is where we need to share each other’s competencies whether you are a small mill or big mill. At ITC we have a target of achieving 40 cubic meters of water per ton of paper this year. Then, next year we will make another target of achieving 35 cubic meters.
We took an initiative in the area of effluent called condensate stripping. The foul condensate that you get in your evaporator becomes nuisance for effluent treatment plant by adding the load and smell. We identified a technology available, it was expensive but we spent money on that. As a result we save 1000 cubic meter of water through this route and it was better than processed water. Moreover, the gases that came out were burnt in limekiln having saved on furnace oil. The payback of the technology has been attractive. It also benefits in reducing the load on the effluent treatment plant thereby saving lot of energy. Initially it looked that these technologies are available for the western world only but in Indian conditions the mill of average size can look out for these technology. With this you are reducing the load on the environment pollution by 25-30%. Load doesn’t happen because of process but it’s due to leakages from the systems. When we put up a project we buy best technologies but we try to save on money by putting second grade pumps and valves, which results in inefficiencies. So, we at ITC took the decision to go for best pumps and the result was straight the color in the effluent came down drastically due to those pumps in the pulp mill. These are the small thing that we need to do and will help in making the good image of the industry.”
……………………………………………………………………………………………………………………………………………
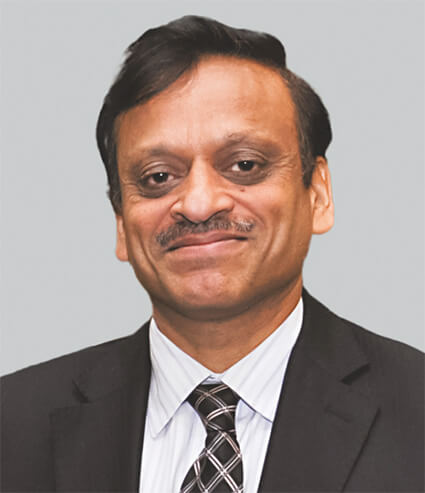
Ballarpur International Graphic Paper Holdings BV
Giving his views on the macro level he said,“There are 5 aspects to sustainability – first and foremost is fibre followed by energy, water, environment and then demand & supply which effect the profitability of the company. In fibre there are two things of concern first is the productivity & efficiency by which we are using the fibre in our mills and secondly its availability & cost. As far as usage of fibre is concerned in the last 1 year most of the mills, be it large or small have invested in new technologies. The subsequent result was that they came up to the ash level of 19-20% as earlier it used to be 9-10%. But, here the challenge is to emulate the ash level of countries like China, US, Indonesia etc. There ash levels still are in excess of 24-25%.
The second aspect to the sustainability is energy, which is very important. I think the paper industry is the sixth largest energy consumer in the country. Moreover, out of total the paper production cost 25% cost goes into energy. On this front paper industry again has evolved over the years. We used to talk about 1200-1500 units per ton and now we have come down to the level of 600-700 units per ton. So, the issue faced here by the industry is obsolescing of technology and the scale.
The scale of operations in India actually does not support the level of power and steam consumption achieved by larger global players. For example, today in China the minimum size of machines being put for uncoated paper is 200,000 tons and coated paper is 300,000 tons per annum. In India in comparison to this the machines, which are being put up has an average size of 75,000 tons per annum. And between these machines there is a difference of at least 20% in the energy consumption. So, we have to go to this scale with the better technology keeping our basics right.
Water again is a very important aspect of the environment. We are dependent on the monsoon for our water supplies. Indian paper industry generally consumes 80-90 cubic meters of water and ITC has taken a tough challenge to make it to 35 cubic meters, which is achievable. Today the norm in India is 100 cubic meters and going to be 80 cubic meters in near future. But, in European Union the standard is only 35 cubic meters, which is for both integrated and non-integrated mills. There is a long way that industry has to travel and a long change which industry has to go through.
Apart from this the cost of production will come down as we reduce our water and energy consumption. So, in one way we are reducing our carbon footprints and on the other hand we are improving the profitability of the company. On the fibre front another important challenge is how to improve the productivity of our farmlands. In India, the average yield of wood is 18 meter cube per annum per hectare whereas in countries like Brazil and Indonesia, it is about 40 meter cube per hectare per annum. The growth of trees in India is just the half as compared to other countries. So, there is a need to have some R&D/genetics program to educate the farmers and work with the farmers on this front.”
……………………………………………………………………………………………………………………………………………
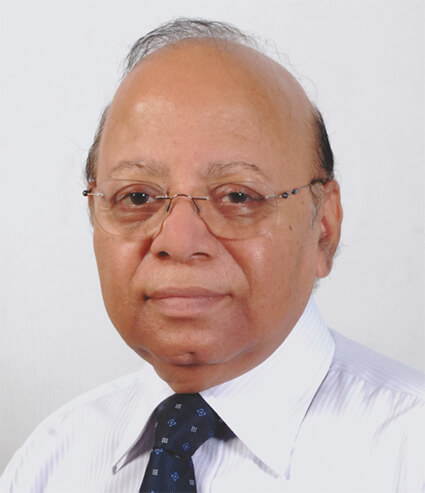
Highlighting the importance of fibre and productivity he said, “We cannot run away from the fact that societies demands are the most important for running an industry. The question of paper production, its demand and requirements for the country will not come down as compared to western world. And whatever projections have been made, they require doubling the use of the wood fibre for paper industry alone in the next 5-10 years. But, where it is going to come from? This is the area where large integrated firms have to strive pretty hard. They have to somehow or the other make farmer interested in growing more and more fibrous wood. Fortunately, the climatic conditions are best suited for the tree plantations as compared to western countries. We need to constantly drive to improve the quality of the plantation and also adopt the right kind of practices for which mills have to undertake lot of work at the field. Therefore, this is the only way the industry can support itself and can hope to meet the demand. Otherwise, we don’t have any option but to import the paper, which will be very unaffordable with the kind of foreign exchange going worse and worse.
In my tenure at APPM we were working on the farm forestry for a long time though we were on the primitive stage of having the productivity from the farmland. We were able to persuade the farmers to sow the clones with buyback guarantee. And, that has prompted us to increase the pulp capacity from 80,000 tons to 170,000 tons. We reached to the farthest place possible to secure our plantations talking to farmers explaining them the process. So, while we have to fight on the front of water, energy, environment along with that we have to economize on them because fittest will survive in the long run. Fibre is the biggest thing standing tall among these things so that is where particularly large integrated mills have to do lot of work. It is just a question of will that’s all is required.”
……………………………………………………………………………………………………………………………………………
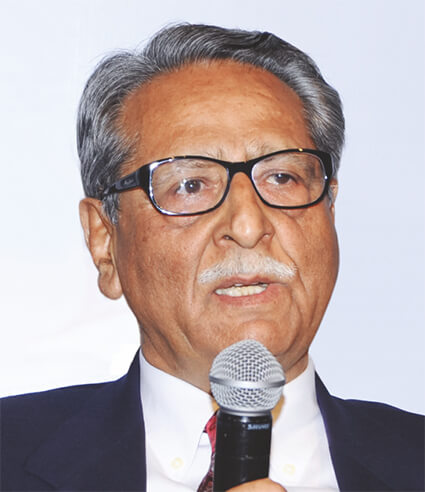
Focusing on importance of adopting the right technology he said, “There is no doubt that the availability of the good technology and the size of operation will always be the winner. If there are possibilities to go in that direction we certainly should choose but most of us in this room have to manage relatively smaller units. So, there are issues we need to address espe-cially when it comes to any equipment purchases. But, more often we are tempted to go for low cost equipments. All of us have suffered time to time by getting into the temptations and regretted later. We strictly have to work on the concept of ownership – cost of purchasing is one time but cost of maintaining is recurring.
And the subject matter to water, energy, and environment there is one saying that what can be measured can be managed. Please emphasize in your operations the need of measurement at every level. Split the measurement of energy in the respective operations and specially the cost of downtime, the cost of shutdown. You will be surprised that the substantial part of our cost comes from such experiences. When it comes to water it should be reused to that extent to a primary application of water, the output of primary application of water can be used for secondary application. Going futher we will reach a stage where we have to look at the process technology. The process like wet-end chemistry plays most important role here, the retention improvements, minimizing COD etc will lead to successful reuse of water to a very large extent.”