ABB, one of the world’s foremost technology leaders, is working with customers, partners and suppliers towards a more sustainable and resource-efficient future.Through automation, electrification and digital solutions, the company makes a difference to industrial operations globally. It believes that India is prepared for technological advancement and that there can be a bright future for the pulp and paper industry in terms of digitalization. ABB’s Pulp and Paper team members Paul Goss, Global Sales Manager and Lweendo Ahnlund, Global Sales and Marketing Manager, spoke with Paper Mart during Paperex 2023.
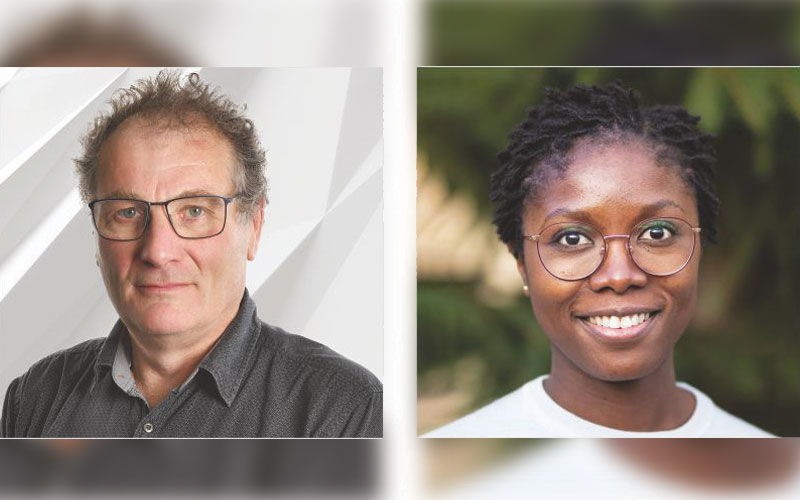
Paper Mart: Tell us something about ABB, how it came into being, major milestones and achievements.
Paul Goss: ABB was formed in 1988 when Sweden’s Allmänna Svenska Elektriska Aktiebolaget (Asea) and Switzerland’s Brown, Boveri & Cie merged to create Asea Brown Boveri (ABB). Headquartered in Zurich, Switzerland, the company today employs over 105,000 people globally and has over 30 million USD in revenues. ABB has a history of innovation excellence stretching back more than 130 years, built on a strong set of legacy brands. Innovation has been in our DNA since we were founded to take advantage of a new technology called electricity. Since then, we have continued to push the boundaries of technology to drive performance to new levels. Our automation and digital solutions have also helped to transform society and industries. Today, we are working towards a productive and sustainable future.
PM: How quickly is the Indian paper industry adopting digitalization and how do you foresee the future? How can the paper industry be benefited by implementing digitalization in their manufacturing setups?
PG: When we talk about digitalization, I don’t see India behind the world or leading the world. I see them in the world. There’s a lot of interest in digital advancements. ABB has large R&D centers in India, where we develop our software and supply digital solutions to Indian customers. There are many Indian customers on board. Some are leading, while some are lagging. Whether you take Europe, Asia, or America, it’s all the same. India is as well prepared for the digital future as others.
The paper industry around the world can be conservative when it comes to adopting new technologies, digital solutions are treated the same. If we look across to digitalization in the automotive industry or manufacturing industries, it’s much more prevalent. ABB considers this as an advantage because we work in many sectors. The paper industry is clearly not an early adopter of digitization, however, it can have a bright future.
If you take the data and data analysis you get in a car, such as location, mileage, fuel levels, maintenance alerts, and compare it with the pulp and paper industry, there is a gap to bridge. Digital solutions can make possibilities reality, and quickly.
Paper mill management and operations must make sure the technologies that they purchase today are digitally enabled. It could be a step too far to fully deploy automation and digital layers, but making a start and being ready supports high productivity, availability and energy efficiencies in the short-term. The data is there for use in the future. We look after some paper mills where each motor is connected and provides data directly to ABB. If a motor there shows an alert or a data anomaly, we take care of it.
Lweendo Ahnlund: More and more of the paper and pulp producers are starting to analyze the value and the benefit of applying digital solutions to capture energy savings, improving runnability, and increasing the life cycle of their investments. It’s the same worldwide, everybody is starting to see more clearly the tangible benefits of moving to adopting more digital technologies.
Watch: Top Paper Companies 2023
PM: Please elaborate on your services and solutions for the pulp and paper sector.
PG: We have a full portfolio for the industry. We go from single products such as measurement scanners, paper machine actuators, all the way up to complete solutions, ABB Ability™ Quality Management System and testing & industry specific instruments. where we take the full responsibility for equipping a paper mill with anything that has a plug on it. We are currently the only independent full scope electrical supplier in the paper industry. By independent, we mean that our focus is solely on automation, electrification and digitalization.
We help the paper manufacturers make good quality paper at the lowest possible cost in a sustainable way. Delivering products and providing solutions is one thing, but providing services and maintaining continuous partnership with customers on how to elaborate on those assets is becoming more and more important.
LA: Our focus is on quality. We want to help our customers in producing high quality paper and reducing waste by using less input and raw materials. We focus on finding ways to be more efficient and tightening the tolerances in the paper machine, so that they use less input materials and still produce high quality paper within specification every single time.
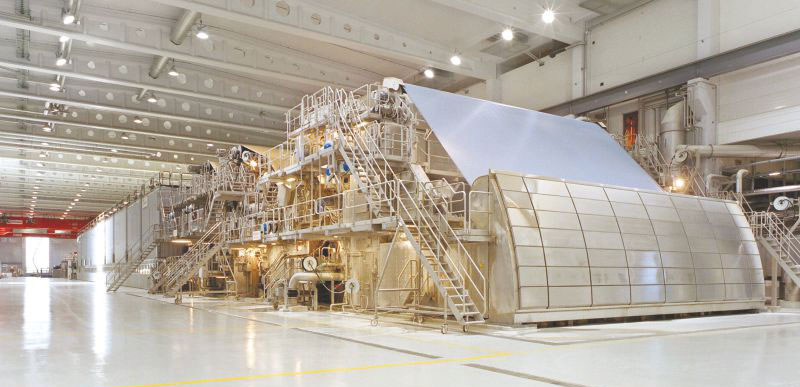
PM: What kind of offerings does ABB have with regard to digitalization? How do you help industries in general and specifically the paper industry?
PG: If you don’t have digital solutions in your package nowadays, you’re not a competitive player in this industry. Digitalization is what we operate on all our products and solutions, and also across our solutions, from one solution to another, extending the services, which matters.
We often look at digitalization from the point of view of a product or solution, but digitalization goes much further. It enables much more advanced services, much deeper insight into the process. We provide the expertise to collect, build solutions with and to analyze the data, advising and assisting the customers on how to improve their processes based on the data available.
Whether it’s pulp consistency, felt wear, or any of the many properties that customers care about, ABB’s L&W (formerly Lorentzen &Wettre) product line delivers the accuracy, reliability and speed needed to both determine and ensure specifications are being met. The benefit is that L&W can see exactly how many measurements were on the outer line. You need to do a service; we can see your measurement is drifting. So that connectivity will be coming. L&W is collecting data for the process. We are using lots of inputs from lab measurements to create online measurements now, so not just a specific hardware center, but a combination of what we have on the paper machine and what we have in the lab, combining the data together and coming up with something new. You see our connection with the L&W laboratory. We have the ABB Quality Control System (QCS) for pulp and paper on the machines, measuring and controlling the manufacturing process to deliver paper that’s on-specification, with equipment to ensure consistency, energy savings, reduced costs.
ABB has been leading the digital arena in pulp and paper and, together with new innovations, already has an extensive digital installed base. Our Manufacturing Execution System (MES) solutions automate the entire process and are currently running with many of the major paper makers. We have successful applications in condition monitoring on electrification equipment. So, it’s not what we don’t have, it’s where to apply what we do have because principally, we cover the full digital scope and we have many such examples all over the world. We enable the industries to progress and evolve by making the most of existing technologies.
PM: How do you collaborate with your customers? How do you go about customizing solutions for your customers, especially for the paper industry?
PG: ABB has around 3,000 people purely focused on the global paper industry. Everything from our lab equipment from L&W to the digital and drive, electrification and automation solutions. One company cannot take on the challenges alone. We are collaborating with all major paper companies around the world, continuously listening to what they need and offering them expertise and solutions. Service is extremely important to our offering – the skills and advice, and is why most of our customers keep coming back to us. When you’re doing service in a proper way with customers, it meansworking with the customers continuously on optimizing their process and making their process better.That’s where you learn from the customers, their requirements, and what they need.
We often say that we don’t sell lab equipment or QCS, we sell the customer the ability to make better paper faster, and in a sustainable way. That’s what we do. The hardware and software is only a small part of the story. You need the equipment, the solution, and then the services.
Also Read: Nalaka Group: First-Ever Tissue Paper Manufacturing Company in Sri Lanka
PM: Do you have any new or future developments regarding your integrated solutions, digitalization or process improvement domains?
PG: We wouldn’t have been here if we were not continuously developing, and if we did not have a roadmap for the future. ABB has been in this business for more than 70 years, and we’re here to stay. Our focus is to move forward. As examples we are looking at how to manage sheet breaks, machine learning and connected engineering. In connecting engineering, we’re connecting the data to the engineers and helping, moving service into the digital arena. As the world changes and people change, it’s much more difficult to get people on site nowadays, to get people willing to travel. Getting the data to the people is probably easier than getting the people to the data.
We are continuously devising new products, digital solutions, developments and directions. Many of them are about how to optimize the existing process. For instance, we have recently introduced the new Autoline automated paper and board testing system, which is continuously being developed by our L&W team. A lot of instruments have already been developed in the past, but we are always looking at how we can reinvent them, make them digital enabled.
Developments are a double-edged sword. Though we continue new developments, as a company that has been around for so many years, we also have a long connection to history. We also work on how to maintain and manage our installed base, and to move it forward. The installed base is continuously evolving for our customers, it’s important we assist them in managing these assets protecting their investments.
PM: ABB is striving to make the customers, the businesses and manufacturing processes more efficient, sustainable. Please share your vision.
PG: Well, our vision is clear. We must look at the past and bring it to the future. The future is around the digital world, where we are using the data that is readily available to create more sustainable processes. At this moment in the paper industry, we’re roughly using 20-30 percent of the data that is available for us to improve the process.
ABB is investing a lot of time, effort and money, to help customers move forward. Our developments are focused on the new opportunities technology brings enabling proven solutions to provide higher value using the new technologies available. In addition we are continuously working on our service portfolio, how we can perform the services in a way that will help the customers make paper in the most optimal way to the best quality at the lowest cost, and in sustainable ways. We put a lot of time into developing ways on how we can use and work with customers in a sustainable way from our side, as well as how we can help customers do that.
PM: Any major development you would like to highlight?
PG: New products are being developed and their applications are being worked upon. Our main developments are taking care of our installed base, expanding our services and digitalization offerings.
Talking about digital capabilities,we are monitoring all electrification in a plant in Finland. We know exactly how many times something has been switched on and off. We can tell the customer that it has now been switched one million times. We have a dashboard that gives us an alarm. We can notify the customer that they will need maintenance soon. It saves the customer waiting for the switch to break and then have a shutdown. It saves production loss. This is just one very basic example of where our industry is heading.
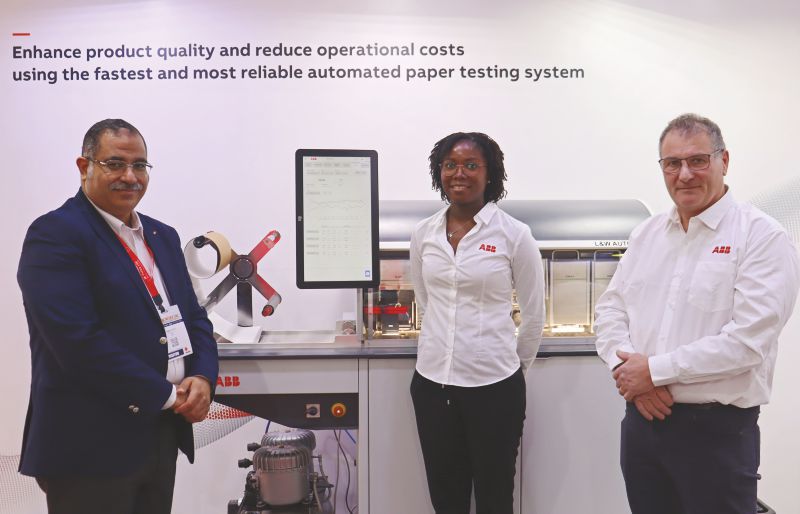