Rajiv Kumar Agarwal, Chief Executive Officer, Amar Elastomers, talks about the company’s suction rolls indigenously developed for the first time under the ‘Make in India’ initiative in an interview given to Paper Mart India.
Paper Mart: Can you tell us about Amar Elastomers’ indigenously developed suction rolls?
Rajiv Kumar Agarwal: Amar Elastomers launched India’s first indigenously manufactured suction roll in 2018. It is basically a vacuum roll used for dewatering of the web in the paper section, improving dewatering in a press nip and stabilizing the sheet in the press section. The suction roll has components like a roll shell with drilled holes, vacuum internal unit, rubber covering, bearings and bearing housings.
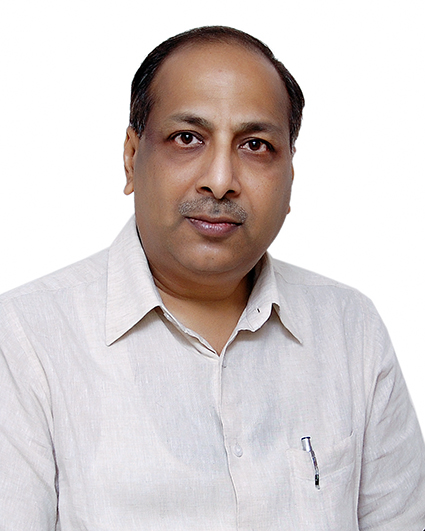
Amar Elastomers
The engineering and designing aspects of the suction roll are quite critical. The suction roll shell, for example, is centrifugally casted for perfect metallurgical components by VOD Ladle Refining process. The shell is machined and honed on CNC Lathe & Grinders for dimensional accuracy and stability. It should be understood that the machined and grinded shell is then drilled for various patterns on CNC Gun Drilling Machine, depending on the quality of paper and the open area required. During the manufacturing of complete suction roll the engineering and design of internal vacuum unit influences the drainage outflow from the roll and is supported by stability of the grade and dimensional requirement of the stainless steel hardware used. The next generation Coldwater Sealing Accessories supports the roll with better vacuum optimization and hardware.
PM: How has been the market demand for your suction rolls?
RKA: Amar Elastomers has supplied its suction rolls to various paper mills. We have successfully installed our suction rolls in various capacities, speeds and parameters adhering to the requirements of different paper mills. We have been supplying suction rolls with speed up to 850 MPM and the basis weight varying from 45 to 90 GSM. We design our suction rolls after thoroughly studying the working parameters of the paper machine. We have a team of experienced engineers who have an in-depth knowledge of how to design and manufacture quality suction rolls.
PM: How are your centrifugally casted pipes for jumbo press rolls a cut above the rest?
RKA: It is the quality that matters. The compactness and strength of a centrifugally casted jumbo roll are much higher than those of the traditional static casted roll shells. The centrifugally casted roll has a better granular structure, molecular strength and tough bonding of alloying elements.
PM: What is the ratio of centrifugally casted rolls to traditional rolls?
RKA: Most of the mills in India use static casted rolls. Earlier, there was only one company in Europe that manufactured centrifugally casted pipes. Also, there happened to be less awareness of centrifugally casted pipes in the Indian Paper Industry. We are working hard to make the domestic industry aware of the availability of centrifugally casted pipes. Of late, industry players have started realizing that centrifugally casted shells are a better option and would give them better runnability of the rolls and thus machine. In one of the paper mills in India, the runnability of a bi-nip press section, drastically improved because of the installed rolls manufactured from the centrifugally casted shells. This affected on other sections of that paper machine with better service life as well.
PM: What are the key factors that determine the lifespan of your rolls?
RKA: The casting process and metallurgy of a shell are of paramount importance, and we maintain the best metallurgical solutions and follow the best casting procedures as far as casting machines are concerned. Metallurgy and operations for casting jumbo roll shells or suction roll shells involve a considerable amount of related equipment and procedures for steel melting. We recently installed a spectrometer that provides online metallurgical tests of the bath during the steel-melting process. This helps us in achieving accurate and on-the-spot check of the metallurgies we are delivering to the end product and customers.
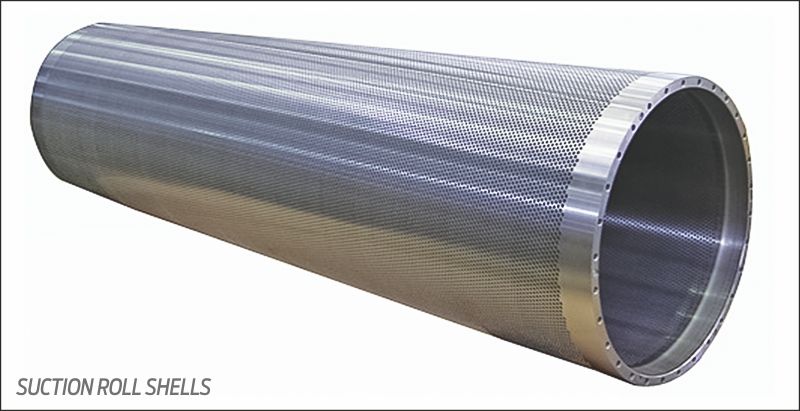
We are also in the process of installing a new INERT GAS DECARBURISING LADLE for better steel making. To be carried out accurately, the process depends on the ability to measure the composition of the stream or gas leaving the furnace throughout the process. With the inclusion of IGD Ladle, we would be able to refine and play more precisely with non ferrous alloying elements in the melt. When we talk about melt, it can be of stainless steel or of carbon steel, or of any cast iron grade. IGD will be used for focusing more on the steel refining process and on delivering the best metallurgical options to the Indian paper industry.
PM: What are the advantages of the ceramic covering on wire return rolls? Please elaborate.
RKA: The inclusion of ceramic covering increases the life cycle of the roll to around ten times. It also helps in quality control and in enhancing the lifespan of other parts of the machine that are in contact with the rolls. Amar Elastomers is currently engaged in the marketing of ceramic covered wire return rolls. We have installed these rolls at Satia Paper Mills. For the last one-and-a-half years, the rolls at Satia Paper Mills have been in good working condition. We are now in the process of delivering more and more wire rolls to the paper industry. The operational cost difference is huge, but it pays off well as far as machine downtime and runnability are concerned.
PM: What are your future targets, especially for suction rolls?
RKA: The indigenous technology for suction roll was developed under the ‘Make in India’ initiative. But marketing and promotional activities for suction roll shells and vacuum internals started much before the ‘Make in India’ initiative was launched. Amar Elastomers has already installed suction rolls at two to three paper mills. Our target is to deliver around three suction rolls per month. Let me take this opportunity to urge the Indian paper mills to invest in our purely indigenous technology, by installing and equipping their paper machines with our efficient suction rolls, meeting the global quality parameters.