The paper industry in India is growing by leaps and bounds. Despite the challenges that it faces, the industry has been growing at an average growth rate of 7 percent against the global average 2 to 3 percent. The industry contributes around 4 percent of global paper production accounting to around 20 million tonnes annually. However, the industry is highly fragmented, mainly dominated by small to medium enterprises (SMEs) unlike the global paper industry, as a majority of Indian paper mills have sizes as low as below 50 TPD against around 1000 TPD.
The industry is among the seventeen heavily-polluting industries as identified by the Ministry of Environment, Forests and Climate Change, Government of India. In addition, paper production is a highly water-intensive process. The Indian paper industry is therefore required to comply with increasingly stringent Charter norms pertaining to water usage and waste water discharge.
As a large water consumer, the Indian paper industry has been progressively improving its water usage while achieving the stipulated benchmarks. One of the major challenges before the industry is on the environmental front, which the industry has been able to address gradually by way of adopting various measures, such as closing water circuits, segregation of waste water streams and its use as process water in identified unit operations and adoption of cleaner production technologies and processes coupled with treatment of effluents streams employing available waste-treatment technologies.
The paper industry uses a variety of effluent treatment systems. The preferred process combination for individual case depends on the grade-specific quality of the effluent that is going to be treated. These include primary treatment (screening, coagulation, sedimentation and clarification) followed by secondary treatment (biological treatment involving anaerobic and/or in combination with aerobic process followed by secondary clarification). Few of the paper mills have adopted the tertiary treatment to remove specific waste-water contaminants, such as additional suspended solids and refractory organic or dissolved solids responsible for higher TDS and color that cannot be removed by secondary treatment.
Internal Process Water
Pertaining to the quality of the process water being recycled, one of the major challenges before a majority of paper mills in India has been the poor and inferior quality of the internal process water. This is due to the build-up of organic and inorganic contents coupled with issues related to stickies and slimes because of closed water circuit. This can result a negative impact on product quality, productivity and overall process efficiency thus adversely reflecting the sustainability and competitiveness of the industry. Moreover, the tolerance limits for water quality in different mills of different categories are not clear. Must the reused water really be potable? Or could the reused water contain “something” without harming the product or the viability of the process? Does that something differ from mill to mill? On the basis of the knowledge available today, it seems that no measured value commensurately describes the papermaking process in such a way that a common conclusion could be drawn.
Water in a paper mill carries significant quantities of fibers (losses with effluent 0.5-5 percent of the total fiber amount), filler, fines and other wet-end additives that contribute to Total Suspended Solids (TSS), Chemical Oxygen Demand (COD), Biological Oxygen Demand (BOD) and color. TSS varies significantly from mill to mill based on the type of internal clarification equipment used and equipment design and its arrangement. COD depends on the amount of TSS and other chemically oxidizable wet-end additives, such as starch. A higher amount of BOD in the process water is due to the presence of a large amount of biologically oxidizable material including the abovementioned and others, such as dry strength and wet strength resins, drainage aids, sizing chemicals and other dissolved organics.
Waste Water Treatment/Management Practices in the Paper Industry
Globally, waste water treatment practices involve the application of advanced technologies that enable significant improvement in the quality of the final treated waste water and facilitate its reuse in the processes, thus reducing freshwater consumption. The need for the adoption of such advanced technologies in the Indian paper industry has been strongly felt, especially in the context of the Ganga River Basin/National Charter-Water Consumption and waste-water discharge for paper mills.
The United Nations Industrial Development Organization (UNIDO) implemented a project for the Indian paper industry titled, “Development and adoption of appropriate technologies for enhancing the productivity of the pulp and paper sector in India (2015-2018)”. Under the project, a technology assessment of the industry was undertaken that identified the “Membrane filtration” technology as the best available technology (BAT) option for Indian paper mills. Globally, membrane filtration is used for water treatment for boiler feed water, machine clear filtrate for fresh water replacement at various showers, final effluent for reuse in RCF mills, coating chemicals recovery, evaporator clean condensate for reuse and for environmental compliances vis-à-vis colour removal from extraction stage bleaching effluent and treating effluent before and/or after biological treatment. The UNIDO project subsequently facilitated a bench-level demonstration study of membrane filtration technology at Central Pulp and Paper Research Institute (CPPRI) and sent the findings to the Indian paper industry. Encouraging findings of the study invited interest from the industry in establishing the techno-economic feasibility of the technology in the Indian context.
Various Effluent Streams Before and After Membrane Filtration
Potential for Membrane Filtration Process in the Indian Paper Industry – UNIDO’s Paper Project (Phase 2)
EOP bleach effluent and Nano
filtration PermeateTertiary treated effluent
NF PermeateSecondary Clarifier O/F and
Nanofiltration Permeate
(Source: Bench level demonstration conducted at CPPRI under UNIDO's phase 1 project)
Following the successful completion of the capacity-building and encouraging results of the bench-level demonstration interventions under the project, UNIDO is now undertaking the second phase of the project. Supported by the Government of India, UNIDO’s phase 2 project titled, “Firm level demonstration of technologies and productivity enhancement for the pulp and paper industry (2019-2022)”, comprises two types of interventions at the firm level:
1. Process optimization and productivity enhancement measures
2. Pilot demonstration of identified technologies with high potential for improvement in environment, energy and productivity and replication across the sector, such as membrane filtration technology.
One of the focus areas of the project is pilot demonstration of the membrane filtration technology in an operational environment, including trials, optimization of the process parameters, continuous operations under stabilized conditions and validation of the results, at four paper mills in four paper clusters across the country. The proposed project activity pilot aims to illustrate the potential of membrane filtration to treat paper mill effluents to reduce color, TDS, COD, Fresh Water Consumption and Waste Water Discharge in different segments of the paper industry representing wood, agro residues and waste paper-based category and to achieve the prescribed pollution norms.
Proposed Approach for Membrane Filtration Pilot Plant
Looking at the characteristics of the effluents being discharged from Indian paper industries, the pilot demonstration unit will consist of an integrated membrane system with appropriate configuration of the membranes consisting of a rigorous pre-treatment system combined with ultra filtration and Nano filtration modules of appropriate pore size, an option for multiple stage separation having both series and parallel configuration and adequate automation to run for an extended period. The proposed process flow diagram is given below. The pilot unit will be capable of treating different waste water streams, such as:
Paper mill final effluent after ETP : Ultrafiltration membrane for color removal for regulatory compliance; permeate to discharge while concentrate back to ETP; Nano filtration membrane after ultrafiltration membrane for water reuse in the mill to enable water use reduction as well as regulatory compliance.
Bleached/unbleached recycled paper mill effluent before ETP : Ultrafiltration membrane to reduce the load on ETP for compliances; permeate to ETP and Tconcentrate to boiler.
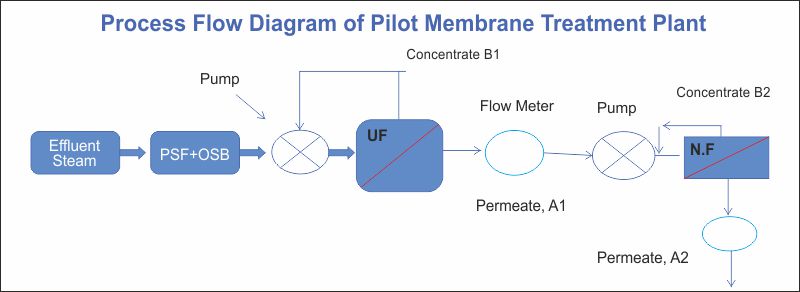
Bleached extraction stage effluent : Ultrafiltration membranes for removing color; permeate to ETP and concentrate to recovery boiler; NF membrane for ultrafiltration permeate for water reuse and concentrate to EPT (due to chloride ions); this is considered more cost-effective due to volume lower than that of the entire effluent.
The project will, therefore, contribute towards the adaptation of this technology to the Indian context and establishment of its techno-economic feasibility for adoption by Indian paper mills.
This article has been written by Rakesh Kumar Jain, United Nations Industrial Development Organization, Delhi (UNIDO); Vikas Kumar, UNIDO, India Office ; Shraddha Srikant, UNIDO, India office; and Farrukh Alimdjanov, UNIDO, Vienna, Austria.