A comprehensive solution for plant information management, analytics, and data modelling can help faster troubleshooting and informed decision-making. BTG’s dataPARC also aggregates operational data as well as predefined time periods.
Importance and Challenges with Process Information Management System
Most data visualisation, lab, or analysis software comes with its respective storage systems, but cannot connect to other systems, and is often localised to limited points of use. This is referred to as a data silo and is a big problem in all industries, especially pulp and paper. With multiple distributed control systems, programmable logic controllers, quality control systems, and laboratory systems (to name a few) present in many mills, all of which use different programs and terminals that are often accessible by a select few people, how does one correlate all this invaluable data?
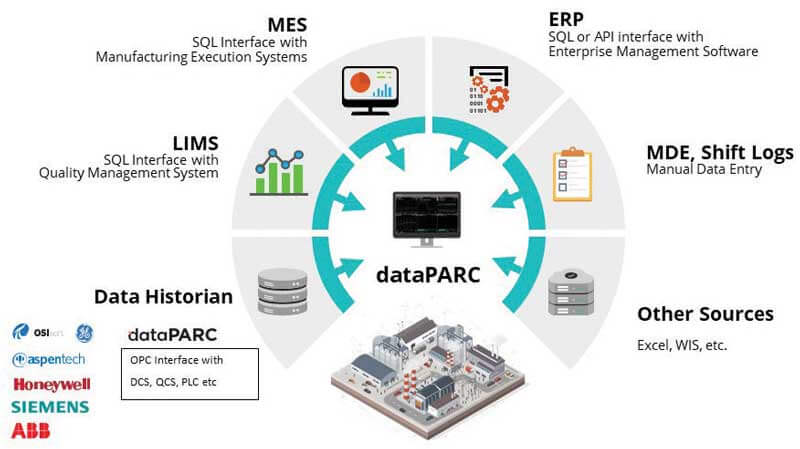
Handling Data from Multiple Sources
The solution is an application that can connect to multiple different data sources and make them available all in one system which is able to be deployed company-wide. BTG’s dataPARC software suite, which is a historian and data visualisation solution designed to connect data across a mill or even a group of mills and make it available in one application is the solution. With all this data available in one place, trends, reports, graphics, centerlines, and other displays that can be used by people at all levels in the mill to make production, optimisation, and troubleshooting decisions becomes simple to produce.
Most importantly, such software creates a data standard so you can rely on the fact that everyone is looking at the same analysis. This is pivotal for digitalisation – to integrate data across multiple sources and mill areas, there must be trust in the data itself. Software like dataPARC helps create this trust through standardising access to data.
Watch: Evolution of Paper Based Packaging
What’s Next after Storing Data?
Having the collective data readily available in a common, accessible location is important for effective usage, but just the ability to see the data is not enough. You need a strong visualisation and analysis tool to support good decisions with all the newfound data. This functionality is also an integral piece of the dataPARC software.
dataPARC has the ability to provide process reports and graphics to enable managers and supervisors to stay current on process conditions and reports. Other management benefits are realised by operations use of the data. Having fast & easy advanced analysis of data from multiple data systems enables a reduction in process and product variability, the ability to proactively make changes, and improved transfer of information between shifts and to management.
dataPARC also aggregates operational data based on the above-monitored conditions and time periods, as well as predefined time periods. Daily, hourly, and minutely aggregations make data retrieval speeds for large time periods among the best in the industry, even when using a slower third-party historian.
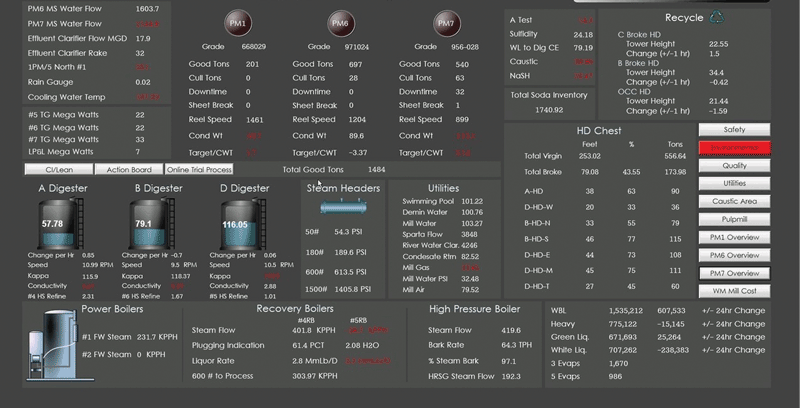
dataPARC’s Unique Value Proposition – Information to Intelligence
- Enabling data acquisition and retrieval for quicker and precise decision-making at the speed of thought in the format that you need. Real-time insight into the mill performance and KPIs.
- Provides a single source of truth for all your manufacturing data. It Aggregates disparate data from machines and manufacturing systems such as DCS, ERP, MES, LAB & Quality systems, to develop the insights that drive continuous improvement. BTG helps it happen irrespective of the make, model, supplier of the data source.
- Gives your operators, engineers & senior management the power to develop data-driven solutions to your most challenging process issues. BTG helps to create real-time insight into the process connecting high data volume, which is beyond human dimensional thinking.
- When process issues begin causing downtime or downgraded products, there’s no time to waste. BTG’s high-performance archive engine returns hours, days, months or years of high-resolution data within seconds to help you to troubleshoot and make decisions faster.
- Give operators, engineers, and the management the insight into current operating conditions using real-time dashboards & displays to monitor equipment status, site-level process flows, or enterprise-wide production KPIs.
- Inbuilt modeling capability utilising historical information (static data) to predict difficult process parameters such as Bulk, Tear, Tensile, Freeness, Kappa, Brightness, viscosity; which is delayed or complex in the LAB. You don’t need third-party software to perform this task.
- Economic benefits are achieved by decreasing costs through operational efficiencies enabled with data-driven insights, decision making, and troubleshooting.
Data-Driven Operational Intelligence – Areas of Opportunity in an Organisation
If you lack high-performing data acquisition, visualisation, and analytics across your plant or enterprise, achieving it in your manufacturing facility is relatively simple when you employ the right resources and have a plan that allows for gradual changes that add up to significant results. Small changes such as combining existing historian systems, effective software tools, and a mindset of proactive digital awareness for your team can significantly impact the overall success of your operations. Newfound ease in your daily tasks and reporting are results of effective IT/OT convergence and will be experienced by everyone. From the operator to the engineer all the way to corporate management, small changes become major impacts when completed strategically and as part of an effective plan for positive digital progress.
Also Read: BTG brings FiberMAX for profitability by focusing on mass flow variations in Paper Industry
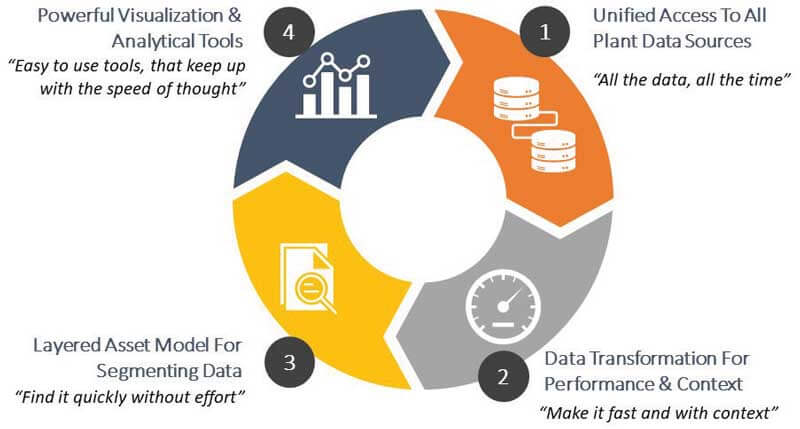
Benefits Summary – BTG’s dataPARC Data Management Solutions
Senior Leadership Team
- View on Profitability
- Help to decide Asset and Resource allocation
- Unbiased Production / Process Information
- Key Cost Driver details
- Enterprise-wide view, not limited to unit operation view
- Overall Equipment Effectiveness (OEE)
- On the Go Plant Information access (Mobile)
- Capable to view process Inventory and interface with other systems like SAP & MIS for order intake
- Quality Deviation statistics
Manager / Process Engineers
- Faster Troubleshooting
- Root Cause Analysis
- Departmental Efficiency information
- Inventory view of Pulp / Water / Utility
- Smart Alarms / Situational awareness
- Crew Efficiency report
- Grade / Batch / Reel Analyses
- Automated Reports
Operators
- Live Process Adherence status
- Smart Alarms
- Center lining
- Ontime LAB Inputs