Peter Bräuer, Johann Großalber, Heinrich Münster, Xiuli Zhang, Rao Narayana Nagalla
Over the past 5-6 years, China has doubled its paper production to almost 100 million t/a and is now the world’s leading producer. In the same period, however, the production of mechanical pulp has more than trippled, despite of a chronic shortage of wood and energy prices at world market level. The main grades are chemi-mechanical high-yield pulps for printing and writing papers, board, and tissue, produced primarily using the P-RC APMP process with excellent energy efficiency. A range of state-of-the-art equipment and comprehensive consumption and operating data are presented, including information on the latest waste water technology, such as integrated evaporation or anaerobic treatment.
1. Production of paper, board & pulp in China
Production of paper and board in China has risen enormously over the past 10 years, from around 34 million t/a in 2000, to around 96 million t/a in 2010 (average annual increase: 11%). China is thus the largest producer in the world, ahead of the United States and the EU (27)1. This also means that most of the production facilities are no more than 5-6 years old, so they are extremely modern.
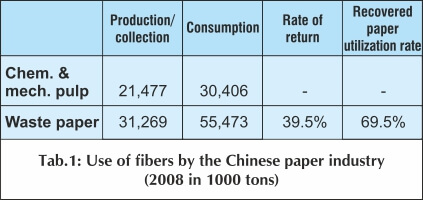
The environment for this growth was not particularly favorable: Supply of raw materials is limited because of the relatively small amount of forest area available, the energy supply is inadequate and based on coal, and the country’s own supply industry is not properly equipped. Thus, China was and still is dependent on imported pulp and waste paper in order to safeguard a reliable supply of fibers.
The Chinese paper industry uses the following fiber composition: (2008 in 1000 tons)
Strong dependence on external sources is evident, particularly for waste paper. But there has been a sensational development in the supply of virgin fibers that has almost gone unnoticed. Unlike the traditional paper producing countries in Europe and North America, the increase in mechanical pulp production in China is above average, also compared to paper production, rising from approximately 500,000 t/a in 2000 to around 4.5 million t/a in 2010 (annual increase of 25%, Fig. 1).
China is thus the largest producer of modern high-yield hardwood pulp (mechanical pulp) using the BCTMP and the P-RC APMP processes. In the classic BCTMP process, the wood chips are impregnated with sodium sulfite and caustic soda, refined, and then post -bleached with peroxide.
The more recent P-RC APMP process differs from this largely in that the chips are impregnated with alkaline peroxide solutions (but without sodium sulfite), and post-bleaching is only needed to achieve the very high final brightness required in market pulp lines.
With this pulping process, the energy requirement for subsequent fiberizing and refining is reduced considerably and the plant configuration becomes more rational. Around 30 new production lines have been installed in China in the past 15 years, and over 75% of them use the P-RC APMP process.
Reasons for the mechanical pulp boom in China
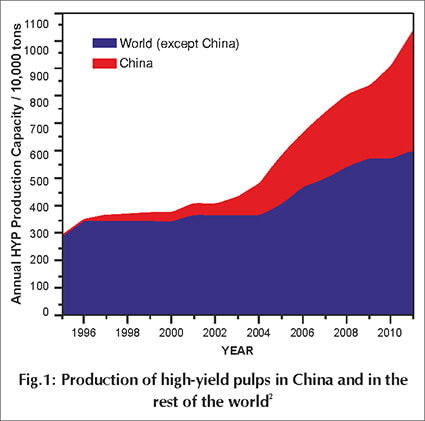
There are many reasons for China pushing mechanical pulps in particular. An important factor is the limited wood resources, so a yield of 85-90% is obviously a considerable advantage. In addition fast-growing species are most suitable for this process. The ambitious forestation program is also geared specially to the needs of the paper industry3.
In addition to poplar, the most common species in China are eucalyptus and massonian pine. Some 40% of the forest area is protected forest and 40% is timber forest, with a high proportion of plantations and short rotation forestry. At the moment, China has poplar plantations covering an area of over 7 million hectares. Large eucalyptus plantations have and still are being established in southern China. The energy-efficient P-RC APMP process is particularly suitable for these fast-growing hardwoods. Another striking factor is that almost all Chinese plants are integrated into paper or board mills, while there is not a single integrated plant in the EU (27) that processes hardwood.
The main advantages of integrated production of high-yield pulps are, of course, the fact that there is no energy-intensive pulp drying and processing needed, no transport and no re pulping, and there is also efficient use of waste heat (steam recovery for paper drying) and a much lower investment and personnel requirement – some plants are operated as a stock preparation plant combined with a paper machine. Another major factor is the possibility to optimize raw materials, chemical dosing, and pulp properties to suit the mill’s own particular paper or board program. By eliminating the need for drying, there are also quality advantages, particularly in terms of brightness and strength properties. This type of mechanical pulp is used in virtually all paper grades. (Table 1)
Advantages of mechanical pulps
The special advantages of modern mechanical pulps compared to chemical pulp are the higher volume and the correspondingly better stiffness, allowing a lower basis weight and lower fiber input. The higher light scattering coefficient and greater opacity can also contribute towards reducing the basis weight. Furthermore, the cost advantage is not to be underestimated.
The disadvantages of mechanical pulps are the lower strength properties in some cases, especially tear strength, but also the lower brightness compared to chemical pulp. (Table 2)
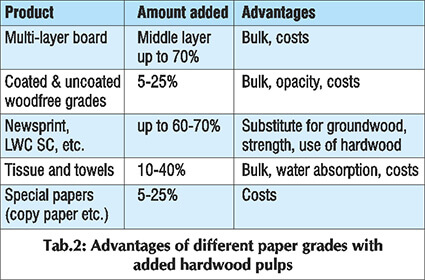
The lower strength can be compensated to a certain extent in hardwood pulps, for example by adding softwood -pulp/ long fiber pulp. In addition, a clear positive synergy effect – in the form of improved strength properties in the paper – can be achieved by mixing P-RC APMP and softwood pulp, as is used in fine papers for example.
This effect is explained by the fines in the high-yield pulp filling the pores between the long pulp fibers, thus increasing formation and bonding ability4.
2. Yellowing – brightness stability of wood-containing papers
An undesirable side effect of adding mechanical pulps is the increased yellowing tendency in the paper. Wood-containing papers yellow due to the effect of UV light on the lignin. However, the lignin content in hardwood is considerably lower than in softwood. Poplar, for example, has an average lignin content of just 18-19%. The yield loss of 5-10% in high-yield pulping is due almost entirely to the lignin content.
Mineral filling materials and optical brightening agents also improve brightness stability: Optical brightening agents act as a UV filter and protect the high-yield fibers against yellowing. Fillers help stabilize the brightness because of the large surface area and their high light scattering coefficient.
With coated papers, yellowing is not really an issue. On the one hand, the raw paper is made with fillers and optical brightening agents, and on the other hand, the pigments in the coating act as a barrier against the effect of light.
3. Using P-RC APMP in wood free grade papers
Use of high-yield pulps in fine papers is limited by definition in many countries because of the high lignin content and the Kappa number. It is becoming more and more evident, however, that this is hardly a functional necessity.
In China, the use of mechanical pulps in fine papers has risen drastically. Pulps with a brightness of 83-86% ISO and a freeness of 250-350 ml CSF are used in wood-free printing papers in amounts of up to 25% as a substitute for short-fiber kraft pulp. Particularly in China, the functionality of the paper is the primary consideration, not a traditional standard.
As far as the ageing resistance of wood-containing papers is concerned, more recent research has shown that the strength of lignin-containing papers is just as stable as that of lignin-free papers if the paper machine is kept in the slightly alkaline range.
The use of energy-efficient mechanical pulps is of remarkable relevance to the sustainability criteria: Higher yield (low wood requirement) than chemical pulp, mainly use of wood material content, lower energy consumption than conventional mechanical pulps, use of fast-growing species also in regions with less favorable climates, higher wood yield per hectare under cultivation, also smaller, decentralized, integrated units that are economically feasible – to mention only some of the main advantages.
4. Plants in China
P-RC APMP technology underwent intensive development before achieving the current level of energy and chemical efficiency. Figure 2 shows the flow diagram of a comparatively simple, highly efficient plant for a final brightness of 75–80% ISO with single-stage impregnation and single-stage high-consistency refining, followed by low-consistency refining. The pulp properties and specific energy consumption of a typical plant are summarized in Table 3.

P-RC APMP pulp made from poplar or aspen with a freeness of 250-350 ml CSF for writing and printing papers requires approximately 700-900 kWh/t for refining. Around two-thirds of this is recovered in the form of low-pressure steam and used in paper drying. In addition, a further 150-200kWh/t are required for auxiliary equipment in this integrated production system. The advantages of these pulps are striking, both economically and ecologically.
The process diagram of the largest P-RC APMP lines in China is shown in Fig. 3. Up to 900 t/d of eucalyptus mechanical pulp with a brightness of > 83% ISO and a freeness of 325 ml CSF are produced in one line.
The mill has one of the most modern zero-effluent waste water treatment technologies worldwide. The waste water from the P-RC APMP plant is evaporated, the resulting concentrate is incinerated in a recovery boiler, and the caustic is recovered in a causticizing plant for reuse in the process. The clean condensate from the evaporation plant is re-used for pulp washing, reducing the fresh water requirement of the mill considerably.
Several Chinese P-RC APMP plants also use particularly efficient 2-stage biological anaerobic/aerobic processes for waste water treatment. As no sodium sulfite is needed for chip impregnation, the APMP technology is also particularly suitable for anaerobic waste water purification
5. High-yield pulps for graphic papers and board in Europe (EU 27)
In Europe and North America, softwood – primarily spruce – is used traditionally for TMP and groundwood. In Sweden and Finland, there are three integrated spruce BCTMP plants for production of board. In total, there are only seven market BCTMP/P-RC APMP plants using hardwood in the EU (27), with a total capacity of approximately 0.9 million t/a.
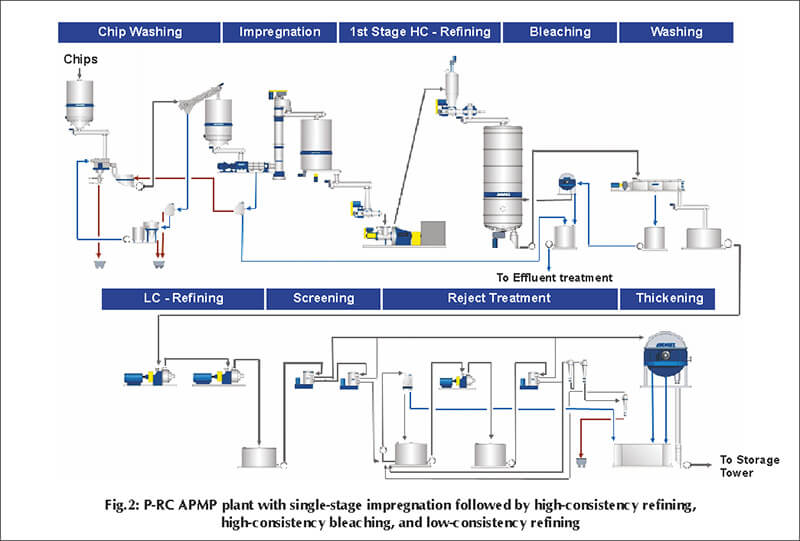
The advantages of hardwoods, such as Eucalyptus, poplar, aspen, birch, and so on, are the substantially higher cellulose content, the comparatively thin and short fibers – resulting in a much higher number of fibers per unit of weight, less fiber shortening in pulping and refining, particular suitability for chemi-mechanical pulping with low electricity consumption, higher initial brightness, and lower costs because of the high wood yield per hectare per year and less competition from the sawmill industry.
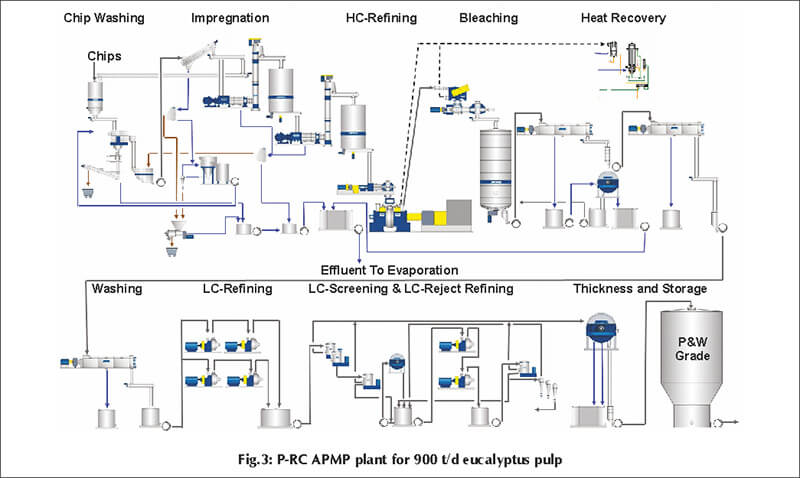
One of the most modern plants for production of market BCTMP in Europe is Estonian Cell (Kunda, Estonia), which produces approximately 150,000 t/a of aspen mechanical pulps for writing and printing papers, as well as for board, using the P-RC APMP process.
The substantial progress achieved in the past few years in mechanical pulping in terms of energy efficiency is explained in Fig. 5.
In spruce TMP for newsprint, for example, the specific energy requirement was reduced by approximately 25 to 30% to around 1600 kWh/t. Essential development stages in achieving today’s ATMP (Advanced Thermo-mechanical Pulping) were the optimized combination of chip pre-treatment and pre-pulping, as well as high-speed refining at higher temperature and post-refining at low pulp consistency.
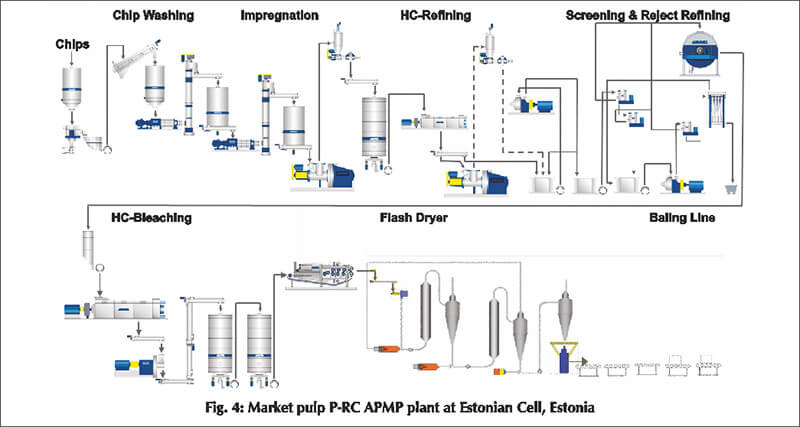
However, hardwood-based CTMP bleached to high brightness certainly enjoys a special status because it has the potential to replace hardwood pulp to a large extent and, at the same time, it provides some of the quality advantages mentioned.
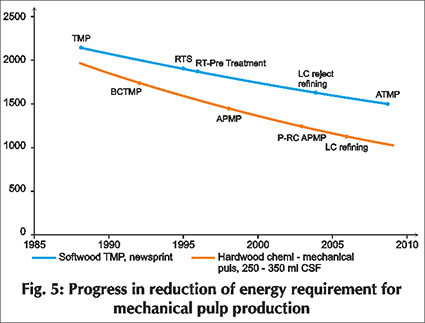
6. Progress in developing the Efficiency in virgin Fiber Generation
Chemi-mechanical pulping not only has the advantage of higher yield over Chemical pulping, but the development of modern base technology and the optimization of each process step such as efficient Impregnation, Screening at higher consistency while maintaining screening efficiency and shifting more and more refining steps towards low consistency refining has reduced the consumption of electrical energy significantly over the past years as can be seen in the example below, which for Hardwood shows a typical Printing and Writing fiber requirement. Systematic development in research, pilot plant and optimization of refining segments has pushed the refining energy down to earlier believed to be unreachable levels of 0.5 to 0.75 MWh/t while keeping the yield between 85 and 88%.
Reference:
1. Austropapier 2009 Annual Report
2. Chemimechanical Pulping in China, Fang Guigan, Shen Kuizhong IMPC 2011
3. Silviculture of poplar plantation in China, Ying Yong Sheng, Tai Xue Bao, 2008
4. Overview of HYP Processes, Development, Pulp Quality and End Uses; Yajun Zhou, IMPC 2011
5. Final report: Real potential for changes in growth and use of EU forests; EUwood.