At Valmet, everything starts from customer-benefits. Automation and industrial internet applications increase process reliability and performance. Building technology and know-how with customer benefits in mind has been at the core of Valmet’s automation system development from the start. Combining automation and the industrial internet seamlessly is paving the road toward autonomous factories.

Valmet’s automation business is known for its innovative process industry automation systems, but perhaps surprisingly the roots of the company’s operations are in aviation.
In the 1940s, a production plant that had served as Valmet’s instrument factory began to manufacture equipment for the Finnish Air Force. In Tampere, the company’s engineers designed devices such as a black box for recording flight information to improve aviation safety, one of the first-of-its-kind. In addition to measurement technology, the company set out to develop various controllers needed in industrial processes. They could be used for functions such as adjusting valve positions with pressurized air. From there, the development work moved on to digital automation systems, at the forefront of which Valmet has been for five decades now. The company had launched its first decentralized control system, Damatic, in 1979 as the second company in the world.
“Valmet moved over to fully digital process control very early on. It helped customers do things more efficiently,” says President of the Automation Business Line, Sami Riekkola from Valmet.
Solutions to production development challenges are increasingly often services
The global megatrend of sustainability is increasingly often at the core of customers’ operations. Therefore, improving performance is often motivated by a need to decrease emissions and use raw materials more effectively. Changing customer needs increase the demand for automation and digitalization, as new technologies can improve performance in several different areas.
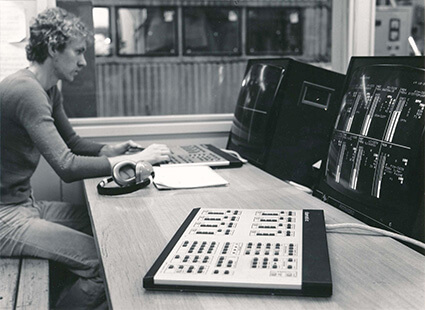
Kari Huovila, Automation Services Business Unit head at Valmet, says that the majority of automation projects start with charting the problems that need solutions together with the customer. After that, work can start to outline what kind of technology is needed.
In addition to distributed control systems and industry-specific automation applications, Valmet’s automation offering includes quality management systems as well as analyzers and measurements, various industrial internet applications and automation services.
“Instead of just technology, we are providing more and more services that are tied to performance and benefits to the customers. For example, a paper mill will no longer purchase just a device for measuring fiber properties. Instead, the customer will acquire a service for achieving the desired level of quality,” Huovila comments.
The heart of Valmet’s automation offering, the Valmet DNA Automation System, was introduced to the market at the beginning of the millennium and is constantly being developed further.
“Our technology is developed in a manner that allows for maintaining and updating the customer’s systems even decades later. The customer can trust that new applications can always be connected to the existing system,” Huovila says.
A good example of this is the Valmet DNA User Interface, which is one of the first web-based user interfaces on the market. The application makes it possible to use the automation system also outside the control room, and previously supplied systems can be upgraded with it, bringing the benefits of browser-based operation to the customer quickly.
The industrial internet connects systems and creates value beyond the value chain
In the conventional scheme, automation has consisted of independent islands that only have limited connections outside. Today, the industrial internet can easily connect systems with one another. “We are witnessing a technological breakthrough in which the internal network of systems extends securely across the internet into IoT solutions that connect different systems and devices. This requires actions such as responding to all information security threats, which is a key area of our constant development work,” says Vice President of R&D Jukka Ylijoki.
Valmet is one of the few operators that are able to supply key customer industries with systems in which data-based production plant performance development is made possible by seamlessly combining the same company’s digital process technology, measurement devices and process automation. “For example, we are currently carrying out quality optimization across the customer’s entire value chain – from fiber to the end product,” says Vice President of Industrial Internet Jari Almi from Valmet.
Toward autonomous factories through digitalization
Industrial internet (IoT) based applications and services with which Valmet improves the reliability and performance of customers’ processes are among the company’s significant growth areas. Customers can use Valmet’s customer portal for purposes such as co-operating with Valmet’s remote service center experts, using industrial internet applications and reading performance reports.
“Our services include aspects such as data analyses, online monitoring, anticipatory diagnostics and timely maintenance planning,” says Vice President of Industrial Internet, Jari Almi from Valmet.
Jari Almi says that IoT solutions are paving the road to further automated and autonomous mills and plants. This enables customers to achieve more efficient production processes at plants such as pulp mills.
“In simplified terms, an autonomous mill means that the process is started with a push of one button. After that, the production is monitored and controlled automatically by means such as the industrial internet and artificial intelligence,” Almi explains.
Performance optimization requires multidisciplinary know-how
When the performance of a mill or a plant is being optimized, there is a multitude of factors to be taken into account. High availability, energy efficiency, optimizing the amount of raw materials used, quality control – each requires specific know-how. Optimizing daily maintenance and long-term lifecycle management in a manner that also takes the changing and developing business needs into account is often a challenging puzzle.
Kari Huovila says that customers in different industries share a wish: that expertise is available quickly and nearby when needed. “Our service network covers the most important market areas. Our local experts are near, and they know the customer’s business well.”
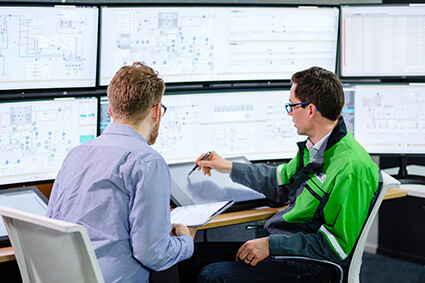
Valmet has supplied almost 5,000 automation systems and more than 100,000 analyzers and measurements across the globe. The equipment and services have a strong market position, especially in the pulp, paper and energy industry, but the company has customers in other areas of the process industry as well. Furthermore, the company’s automation technology is utilized in hundreds of cruise and cargo ships. “We are able to provide our customers with additional value in many industries. Our system is easy to adapt to different customer applications, from pulp mills to cruise ships,” says President of the Automation Business Line Sami Riekkola. “We also provide customers with access to the know-how of the entire Valmet Group, creating significant synergy,” Riekkola continues. “It is a great advantage that in addition to automation we have thorough industrial process know-how and knowledge in-house.”
“The starting point for everything is that our staff are very committed to solving the customers’ problems,” Riekkola comments. “We are quick when it comes to developing new things, but in product development our focus is always locked on helping the customer. A close relationship with the customer also clarifies the goals of product development.”
“Additionally, a key aspect of our competitiveness is high-quality project implementation. That means that the customer receives what they want – and preferably a little more – within the agreed upon schedule,” Riekkola says. He states that Valmet’s ambitious goal is to find growth outside its current strong industries as well.
“Lately, we have been automating sites such as battery chemical plants with the latest technology.”