The bigger the better? Why bigger roll diameters for calenders are not necessarily an advantage.
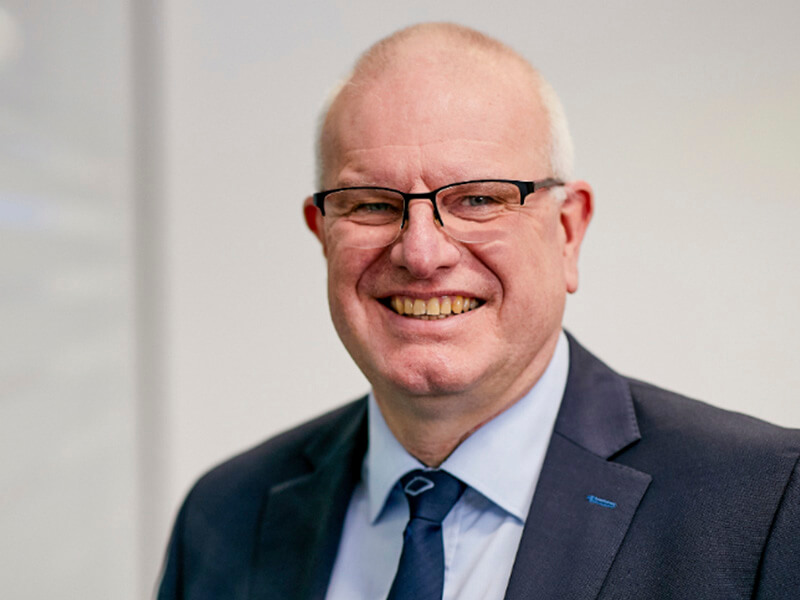
Mr. Hans-Josef Reiners, Sales Director-Paper and Board at ANDRITZ Küsters
Our calenders enable reliable soft calendering for a wide range of applications. The outcome – the excellent surface finish – is often created by a simple pair of rolls.
When running a sheet through a calender, we merely talk physics. Some of the effects a sheet experiences when running through a nip (which is generated by two rolls) are contradictory.
However, everybody knows that the technology works, and here is some background knowledge that hopefully helps explain the effect of the roll diameter.
Mr. Hans-Josef Reiners, Sales Director-Paper and Board at ANDRITZ Küsters, provides some insights into this effect.
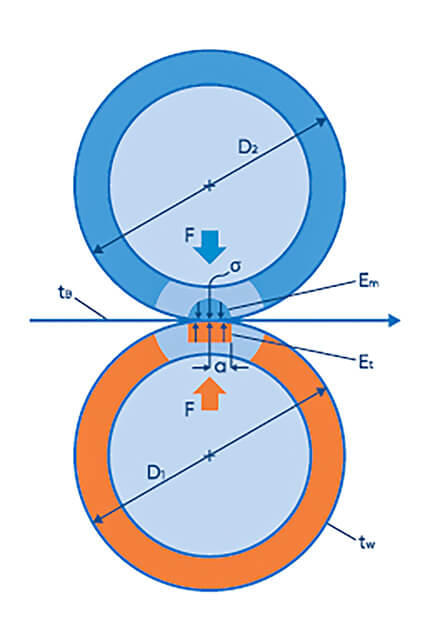
ROLL ARRANGEMENT
The sketch below shows a crown-compensated roll in the top position (blue) and a heated roll in the bottom position (orange). The sheet running through the nip passes from left to right.
Calendering is an effect in which surface properties are transferred from the rolls to the sheet. This is subject to several parameters like
- Nip Load
- Temperature
- Moisture
- Dwell Time
There are other parameters, but let’s stick to these four as the most prominent ones.
NIP LOAD
We will start with the nip load – represented by the letter F in the sketch. In an ideal approach, there is just one point of contact between the two rolls. Accordingly, the nip load is sometimes referred to as the linear nip load.
In practice, the rolls have a certain elasticity and are flattened by the nip load (following the laws of Hertzian pressure). That means that the nip load is distributed over an area in a practical way and becomes a specific nip load.
The area is dependent on the elasticity modulus – represented by Em and Et – of the rolls, but it is also subject to the physical properties of the sheet. As a matter of fact, we use the specific nip load for our internal calculation of the rolls.
TEMPERATURE
The fibers in the sheet show resistance to deformation. Higher temperature lowers this resistance and makes the sheet more flexible. The base temperature at which the sheet enters the nip is the starting point – represented in the sketch by tB. The increase in temperature may only be noted on the surface and not pass through the entire web. For this reason, and in order to reduce two-sidedness, a second calender stack may be installed. For this purpose, the roll pair is arranged in an alternate manner. In one calender stack, the heated roll is in the top position, whereas in the other calender stack the heated roll is in the bottom position.
MOISTURE
The next prominent parameter is moisture. Water softens the fibres, hence a certain sheet humidity is helpful. In some special applications with high quality demands, water is added (by steam or water spraying) before the calender. Here, it is worth considering moisture profiling to keep the moisture in CD direction constant.
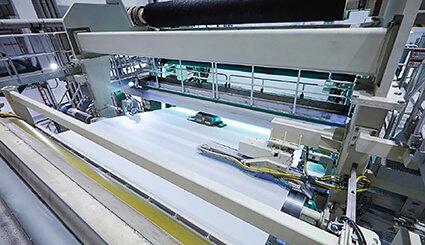
DWELL TIME
Dwell time, as the last prominent parameter, means the time period over which the sheet experiences the change in its environment (i.e. higher nip load and temperature). The first idea may be to reduce the line speed to increase this parameter. However, this will lower production and is the wrong approach.
A workable solution is to add nips because the time of exposure in each nip would thus accumulate. This idea led to the development of multi-nip technology, like the ANDRITZ PrimeCal ProSoft calender. In other applications, two calender stacks were installed in a double arrangement in which the heated rolls are arranged on the same side to drastically improve the smoothness there.
CONCLUSION
Based on this background knowledge, an increase in the roll diameter would increase the parameter dwell time only to a very minor extent.
However, the contact area would increase as well and the specific nip load would be reduced accordingly.
Although a larger diameter may allow a higher linear load, there are also severe negative consequences. Besides space considerations, the disadvantage of increasing the roll diameter may be that this approach sometimes does not pay off.
ANDRITZ PrimeCal calenders provide full control of the nip and a finish that creates paper and board qualities with optimum printability. These calenders are well suited to final calendering of newsprint, fine papers, and various types of board. By making use of the single element-controlled PrimeRoll MHV technology, all PrimeCal calenders are able to create state-of-the-art CD caliper profiles.