“The investment was in line with Södra sustainability and decarbonization goals,” said Mr. Anders Wiman, Power and Recovery Manager, SCV.
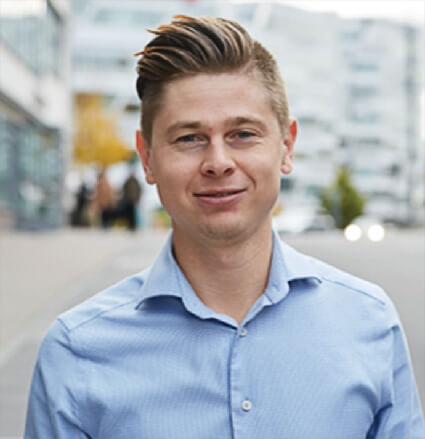
Heat Management’s HISS™ was installed as part of the Södra expansion 2.0 project, resulting in production records (+9 percent), and increased boiler load by 12 percent. With higher production comes more output of renewable energy to the grid, resulting in 20 MWe of locally generated and sustainable power for the Swedish SE3 region. This effectively offsets power generation from fossil power stations, reducing emissions by 21 000 tons CO2eq annually.
Södra Cell Värö is a prosperous NBSK pulp mill with ambitious sustainability goals. As part of the Expansion 2.0 project, Södra increased its NBSK pulp production capacity from 710 000 ADMT/year to 780 000 ADMT/year. The recovery boiler was identified as the bottleneck.
Heat Management’s HISS™ is an optimised soot blowing system that can be customised to meet the needs of each customer. Users of HISS™ can increase the soot blowing capacity by 100 percent without consuming more steam or maintaining the same cleaning effect with 30-45 percent reduced soot blowing steam consumption. The system was used in Södra’s case to maximise cleaning capacity, resulting in production records, while producing more renewable power to the grid.
“We entered into a sustainability partnership with Heat Management to reduce our production costs and increase the generation of renewable power from our pulp mill. The investment in HISS™, allowed us to safely explore the process limits and take it beyond technical specifications, to reach our production goal of 850 000 tonnes/year. The recovery boiler is now operating on a 12 percent higher liquor throughput compared to before. The investment was in line with Södra sustainability and decarbonization goals,” said Mr. Anders Wiman, Power and Recovery Manager, SCV.
Watch: IVAX Paper Chemicals Interview
Partnering with Heat Management to make pulp mill efficiency improvements involves a continuous dialogue for validation and verification. Heat Management studies process data every week to ensure the highest possible amount of steam savings with desirable boiler availability. A good relationship with the pulp mill is in focus, supporting operations, maintenance, production, and process experts with unique knowledge and holistic data analysis for both the measurable and the non-measurable process conditions.
Also Read: Cheema Boilers Supplies One-of-its-kind Boilers to 2nd Generation (2G) Ethanol Plant
This approach renders the biggest advantage: combining improved availability from dynamic operational and strategic soot-blowing capacity with millions of EUR in potential savings generated from increased and safe mill production levels. Energy and water savings per ADMT play straight into the mill sustainability goals and circular operations. All in all, renewable heat and power generation are increased while CO2 emissions are decreased, contributing to the pulp mill’s sustainability goals.
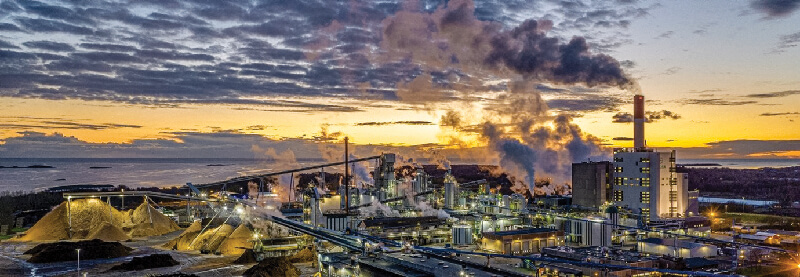